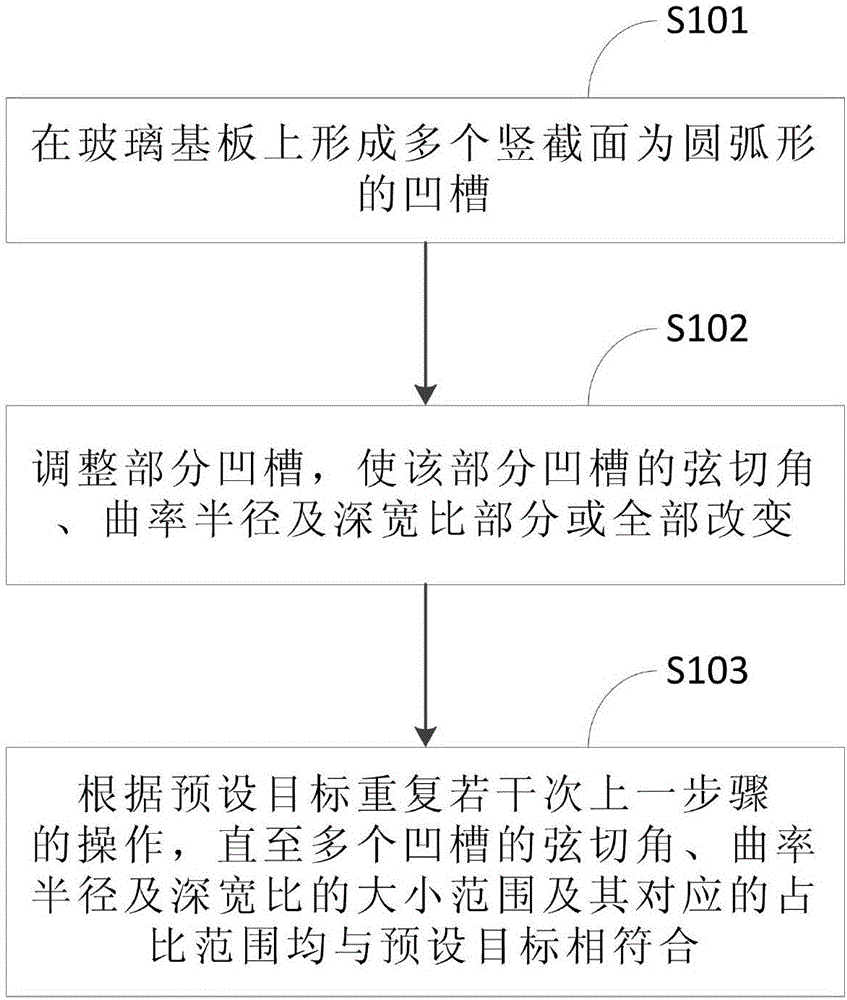
本發明涉及液晶顯示領域,特別涉及一種抗閃光蓋板的制造方法。
背景技術:
:液晶顯示裝置(LCD,LiquidCrystalDisplay)具有機身薄、省電、無輻射等眾多優點,得到了廣泛的應用。TFT-LCD在日常生活中已經很普及,如電視、電腦、手機等顯示屏,該領域技術不斷更新以更好的服務消費者。不斷的產品升級使對TFT-LCD更高的要求,提出了更高的產品品質的要求。車載顯示和小尺寸顯示面板的抗眩功能越來越受到人們的關注,傳統的抗眩結構的加工方法包括濕刻法和涂布法。濕刻法即采用酸液對蓋板玻璃進行表面蝕刻處理,得到粗糙的表面結構。涂布方法即通過在蓋板玻璃表面涂布有機或無機粒子的方式得到粗糙表面結構。然而,濕刻和涂布的方法工藝雖然簡單,但是無法得到形貌可控的粗糙表面結構,無法控制蓋板表面透射光或者反射光的光強空間分布和強度,這就會導致蓋板表面發生閃光的現象,嚴重影響畫面的品質。技術實現要素:本發明的目的在于提供一種抗閃光蓋板的制造方法,以解決現有技術中,無法得到形貌可控的粗糙表面結構的蓋板,無法控制蓋板表面透射光或者反射光的光強空間分布和強度,這就會導致蓋板表面發生閃光的現象,嚴重影響畫面的品質的問題。本發明的技術方案如下:一種抗閃光蓋板的制作方法,包括以下步驟:1)根據預設目標設定玻璃基板表面結構的不同結構參數的目標大小范圍及其對應的目標占比范圍;2)在所述玻璃基板上形成多個微結構,每個所述微結構的不同結構參數的絕對值大小均在其對應的所述目標大小范圍之內,且所述目標大小范圍劃分為若干個設定范圍,參數大小處于該若干個設定范圍內的所述微結構的個數與所述微結構的總數的比例大小均在其對應的所述目標占比范圍之內,以使所述抗閃光蓋板具有抗閃光作用。優選地,在玻璃基板上形成多個微結構,包括以下步驟:1)在玻璃基板上形成多個豎截面為圓弧形的凹槽;2)調整部分所述凹槽,使該部分所述凹槽的弦切角、曲率半徑及深寬比部分或全部改變;3)根據所述預設目標重復若干次所述步驟2)的操作,直至多個所述凹槽的弦切角、曲率半徑及深寬比的大小范圍及其對應的占比范圍均與所述預設目標相符合。優選地,多個所述凹槽的大小相同,其相互連接并均勻分布排列。優選地,步驟1)具體包括:在所述玻璃基板表面的預設位置噴涂包括氫氟酸、磷酸及硫酸在內所組成的混酸溶液,并使所述混酸溶液在所述預設位置停留至預設時間長度,使其蝕刻出多個所述凹槽。優選地,步驟2)具體包括:在所述多個凹槽上涂布正光阻層,所述正光阻層覆蓋多個所述凹槽;準備設定光罩并將其與所述正光阻層相對合,將紫外光線照射所述設定光罩,以得到曝光區小于未曝光區的光阻結構;在所述光阻結構的曝光區再次噴涂所述混酸溶液對所述玻璃基板進行蝕刻,以改變該曝光區部分的所述凹槽的弦切角、曲率半徑及深寬比。優選地,所述預設目標具體為:弦切角大小的絕對值處于30°~40°、20°~30°、10°~20°的所述凹槽的個數占所述凹槽的總數的百分比分別為0~0.5%、0.5%~1.5%、7%~15%及85%~91%,多個所述凹槽的平均曲率半徑范圍為10~30um,且多個所述凹槽的平均深寬比范圍為0.05~0.1。優選地,在玻璃基板上形成多個微結構,包括以下步驟:1)在玻璃基板上涂覆一透明有機層,所述透明有機層具有所述玻璃基板的光學性質;2)在所述透明有機層上涂覆一負光阻層,準備設定光罩并將紫外光線照射所述設定光罩,以對所述負光阻層進行曝光顯影,得到所述負光阻層的光阻預設結構;3)對所述光阻預設結構及所述透明有機層進行蝕刻,以去除所述光阻預設結構,并得到所述透明有機層的透明有機結構,且所述透明有機結構的外型與所述光阻預設結構的外型相同,所述透明有機結構包括多個所述微結構;其中,所述設定光罩設有全曝光區、半曝光區及無曝光區,所述半曝光區位于所述全曝光區的兩側,所述無曝光區位于所述半曝光區的中部,多個所述透明微結構具有抗閃光作用。優選地,每個所述微結構的外型為中間厚兩側薄的底面橫截面為圓弧形的凸包,所述凸包的中部對應所述無曝光區,所述凸包的兩側對應所述半曝光區。優選地,各個所述微結構的大小不完全相同,且相鄰兩個所述微結構之間設有間距,該間距區對應所述全曝光區。優選地,所述凸包的曲率半徑范圍為2~100um,相鄰兩個所述凸包之間的間隔范圍為0.2~30um,所述凸包的高度范圍為1~100um。本發明的有益效果:本發明的一種抗閃光蓋板的制作方法,包括兩種制作方式,其一是通過多次濕蝕刻,并輔助光罩的工藝方式在玻璃基板上制備多個微結構,通過對微結構的相關結構參數進行設計并優化,有效改善微結構在高解析度蓋板上產生的閃光現象,使微結構蓋板在增強面板戶外可讀性的同時也避免閃光現象,對于抗眩蓋板在小尺寸顯示面板上的實際應用起到很好的推動作用。其二是采用光刻的方式制備從圓弧狀到球狀的抗閃光結構,通過光罩工藝精確控制微結構周期大小、間距和高度,當微結構粒徑大小為2~100um范圍內,微結構間距為0.2~30um的范圍內(間距為粒徑大小的0.1~0.3倍),微結構高度為1~100um的范圍內(高度為粒徑大小的0.5~2倍),通過光學軟件模擬進行驗證,改善蓋板表面的抗閃光效果。【附圖說明】圖1為本發明實施例一的抗閃光蓋板的制造方法實施步驟流程圖;圖2為本發明實施例一的抗閃光蓋板的制造方法實施步驟中,將玻璃基板清洗并烘干后的示意圖;圖3為本發明實施例一的抗閃光蓋板的制造方法實施步驟中,在玻璃基板上形成多個豎截面為圓弧形的凹槽的示意圖;圖4為本發明實施例一的抗閃光蓋板的制造方法實施步驟中,在透明有機層上涂覆一正光阻層的示意圖;圖5為本發明實施例一的抗閃光蓋板的制造方法實施步驟中,將紫外光線照射所述設定光罩的示意圖;圖6為本發明實施例一的抗閃光蓋板的制造方法實施步驟中,得到曝光區小于未曝光區的光阻結構的示意圖;圖7為本發明實施例一的抗閃光蓋板的制造方法實施步驟中,改變該曝光區部分的所述凹槽的弦切角、曲率半徑及深寬比的示意圖;圖8為本發明實施例一的凹槽的弦切角、曲率半徑和深度的結構參數表達示意圖;圖9為本發明實施例二的抗閃光蓋板的制造方法實施步驟流程圖;圖10為本發明實施例二的抗閃光蓋板的制造方法實施步驟中,將玻璃基板清洗并烘干后的示意圖;圖11為本發明實施例二的抗閃光蓋板的制造方法實施步驟中,在玻璃基板上涂覆一透明有機層的示意圖;圖12為本發明實施例二的抗閃光蓋板的制造方法實施步驟中,在透明有機層上涂覆一負光阻層的示意圖;圖13為本發明實施例二的抗閃光蓋板的制造方法實施步驟中,將紫外光線照射所述設定光罩,對所述負光阻層進行曝光顯影的示意圖;圖14為本發明實施例二的抗閃光蓋板的制造方法實施步驟中,得到負光阻層的光阻預設結構的示意圖;圖15為本發明實施例二的抗閃光蓋板的制造方法實施步驟中,去除光阻預設結構,并得到透明有機層的透明有機結構的示意圖;圖16為本發明實施例二的抗閃光蓋板的制造方法實施步驟中,得到的透明有機材料層形成的多個所述微結構的豎截面近似于圓弧狀的示意圖;圖17為本發明實施例二的凸包的弦切角、曲率半徑和深度的結構參數表達示意圖。【具體實施方式】以下各實施例的說明是參考附加的圖式,用以例示本發明可用以實施的特定實施例。本發明所提到的方向用語,例如「上」、「下」、「前」、「后」、「左」、「右」、「內」、「外」、「側面」等,僅是參考附加圖式的方向。因此,使用的方向用語是用以說明及理解本發明,而非用以限制本發明。在圖中,結構相似的單元是以相同標號表示。實施例一總的來說,本發明的一種抗閃光蓋板的制造方法包括以下兩個步驟:第一,根據預設目標設定玻璃基板1表面結構的不同結構參數的目標大小范圍及其對應的目標占比范圍。第二,在所述玻璃基板1上形成多個微結構,每個所述微結構的不同結構參數的絕對值大小均在其對應的所述目標大小范圍之內,且所述目標大小范圍劃分為若干個設定范圍,參數大小處于該若干個設定范圍內的所述微結構的個數與所述微結構的總數的比例大小均在其對應的所述目標占比范圍之內,以使所述抗閃光蓋板具有抗閃光作用。以下多本發明進行具體的說明。請參考圖1,圖1為本實施例的一種抗閃光蓋板的制造方法實施步驟流程圖。從圖1可以看到,本發明的一種抗閃光蓋板的制造方法包括以下步驟:步驟S101:在玻璃基板1上形成多個豎截面為圓弧形的凹槽2。本步驟優選多個所述凹槽2的大小相同,其相互連接并均勻分布排列。步驟S102:調整部分所述凹槽2,使該部分所述凹槽2的弦切角、曲率半徑及深寬比部分或全部改變。步驟S103:根據所述預設目標重復若干次所述步驟S102的操作,直至多個所述凹槽2的弦切角、曲率半徑及深寬比的大小范圍及其對應的占比范圍均與所述預設目標相符合。其中,相鄰的兩次重復步驟S102的操作中,后一次部分被調整的所述凹槽2與前一次不完全相同。在本實施例中,步驟S101具體包括:在所述玻璃基板1表面的預設位置噴涂包括氫氟酸、磷酸及硫酸在內所組成的混酸溶液,并使所述混酸溶液在所述預設位置停留至預設時間長度,使其蝕刻出多個所述凹槽2。在本實施例中,步驟S102具體包括:第一,在所述多個凹槽2上涂布正光阻層3,所述正光阻層3覆蓋多個所述凹槽2。第二,準備設定光罩4并將其與所述正光阻層3相對合,將紫外光線5照射所述設定光罩4,以得到曝光區小于未曝光區的光阻結構。第三,在所述光阻結構的曝光區再次噴涂所述混酸溶液對所述玻璃基板1進行蝕刻,以改變該曝光區部分的所述凹槽2的弦切角、曲率半徑及深寬比。在本實施例中,所述預設目標具體為:弦切角大小的絕對值處于30°~40°、20°~30°、10°~20°的所述凹槽2的個數占所述凹槽2的總數的百分比分別為0~0.5%、0.5%~1.5%、7%~15%及85%~91%,多個所述凹槽2的平均曲率半徑范圍為10~30um,且多個所述凹槽2的平均深寬比范圍為0.05~0.1。請參考圖2至圖8,圖2為本發明實施例一的抗閃光蓋板的制造方法實施步驟中,將玻璃基板1清洗并烘干后的示意圖。圖3為本發明實施例一的抗閃光蓋板的制造方法實施步驟中,在玻璃基板1上形成多個豎截面為圓弧形的凹槽2的示意圖。圖4為本發明實施例一的抗閃光蓋板的制造方法實施步驟中,在透明有機層上涂覆一正光阻層3的示意圖。圖5為本發明實施例一的抗閃光蓋板的制造方法實施步驟中,將紫外光線5照射所述設定光罩4的示意圖。圖6為本發明實施例一的抗閃光蓋板的制造方法實施步驟中,得到曝光區小于未曝光區的光阻結構的示意圖。圖7為本發明實施例一的抗閃光蓋板的制造方法實施步驟中,改變該曝光區部分的所述凹槽2的弦切角、曲率半徑及深寬比的示意圖。圖8為本發明實施例一的凹槽2的弦切角、曲率半徑和深度的結構參數表達示意圖。本發明在所述玻璃基板1上形成多個微結構,使每個所述微結構的不同結構參數大小均符合其對應的所述目標大小范圍,及使符合各種結構參數要求的所述微結構的個數占全部所述微結構的比例均符合其對應的所述目標占比范圍,以使所述抗閃光蓋板具有抗閃光作用。本發明的制作方法的具體實施步驟如下所述:本發明采用多次濕刻的工藝方式進行蓋板表面微結構的制備,微結構主要的濕刻工藝結構參數如圖8所示,其中r為曲率半徑,h為凹槽2深度,β為弦切角,h/r為深寬比。具體工藝操作流程如圖2至圖7所示。首先將玻璃基板1清洗干凈并烘干,如圖2所示,在玻璃基板1表面第一次噴涂較低濃度的氫氟酸、磷酸及硫酸等組成的混酸溶液,并使混酸溶液在玻璃基板1表面停留一段時間,使得混酸溶液蝕刻出如圖3所示的微結構,即多個豎截面為圓弧形的凹槽2。其中微結構的弦切角β的絕對值控制在0°~10°,平均曲率半徑r的大小控制在30~50um,平均深寬比h/r控制在0.02~0.025,并再次將玻璃基板1洗凈并烘干。其次在玻璃基板1的凹槽2上即濕刻表面涂布一層正光阻,采用曝光的方式將微結構表面留下少量曝光區,其中曝光區的面積大小遠小于未曝光區,形成曝光區小于未曝光區的光阻結構。接著如上所述,在所述光阻結構的曝光區再次噴涂所述混酸溶液對所述玻璃基板1進行蝕刻,以改變該曝光區部分的所述凹槽2的弦切角、曲率半徑及深寬比,即在玻璃基板1表面再次噴涂濃度稍高的氫氟酸、磷酸及硫酸的混酸溶液,使混酸溶液在基板表面暫留一段時間,濕刻出所需圖案,以上工藝流程如圖4~圖7所示。其中每個凹槽2的弦切角β的絕對值在10°~20°之間的角度占比在2%~5%,平均曲率半徑r控制在20~40um,平均深寬比h/r控制在0.03~0.04。接下來重復若干次圖4~圖7所示的操作過程,其中每次曝光顯影區均與前幾次不完全相同,最終在玻璃基板1的表面濕刻出多個不同弦切角、曲率半徑和深寬比的凹槽2,其中弦切角呈現高斯分布的特性,滿足絕對值在30°~40°占比0~0.5%,20°~30°占比0.5%~1.5%,10°~20°占比7%~15%,0°~10°占比85%~91%,平均曲率半徑R控制在10~30um,平均深寬比h/R控制在0.05~0.1。表一和表二顯示了不同濕刻工藝制備的抗閃光蓋板的具體工藝參數情況。從表中數據可知,4#樣品采用多次濕刻的工藝進行微結構制備,其弦切角分布呈現出一定分散的特性,絕對值在30°~40°的占比為0.1%,20°~30°的占比為0.7%,10°~20°的占比為8.8%,0°~10°的占比90.4%,平均曲率半徑r為29um,平均深寬比h/r為0.05,其參數規格符合上述事實方案要求。將4種不同參數的微結構蓋板放在同一解析度的顯示面板上,通過實物照片結果可知閃光現象的嚴重程度為:4#<1#<2#<3#,3#和2#有明顯的閃光現象,1#的閃光現象較為輕微,4#幾乎看不到閃光現象,從而也進一步驗證了通過多次濕刻工藝制備蓋板表面抗眩微結構可以有效改善高解析度顯示面板表面的閃光現象。表一不同濕刻工藝凹槽2弦切角的統計分布表二不同濕刻工藝凹槽2結構參數對比樣品編號0°-10°占比10°-20°占比20°-30°占比30°-40°占比曲率半徑/um深寬比1#97%2.70%0.20%-490.031#99.10%0.80%0.10%-850.0251#99.40%0.50%0.10%-1140.021#90.40%8.80%0.70%0.10%290.05本發明的一種抗閃光蓋板的制作方法,通過多次濕蝕刻,并輔助光罩的工藝方式在玻璃基板1上制備多個微結構,通過對微結構的相關結構參數進行設計并優化,有效改善微結構在高解析度蓋板上產生的閃光現象,使微結構蓋板在增強面板戶外可讀性的同時也避免閃光現象,對于抗眩蓋板在小尺寸顯示面板上的實際應用起到很好的推動作用。實施例二總的來說,本發明的一種抗閃光蓋板的制造方法包括以下兩個步驟:第一,根據預設目標設定玻璃基板10表面結構的不同結構參數的目標大小范圍及其對應的目標占比范圍。第二,在所述玻璃基板10上形成多個微結構,每個所述微結構的不同結構參數的絕對值大小均在其對應的所述目標大小范圍之內,且所述目標大小范圍劃分為若干個設定范圍,參數大小處于該若干個設定范圍內的所述微結構的個數與所述微結構的總數的比例大小均在其對應的所述目標占比范圍之內,以使所述抗閃光蓋板具有抗閃光作用。以下多本發明進行具體的說明。請參考圖9,圖9為本實施例的抗閃光蓋板的制造方法實施步驟流程圖,從圖9可以看到,本發明的一種抗閃光蓋板的制造方法,包括以下步驟:步驟S101:在玻璃基板10上涂覆一透明有機層20,所述透明有機層20具有所述玻璃基板10的光學性質。步驟S102:在所述透明有機層20上涂覆一負光阻層30,準備設定光罩并將紫外光線70照射所述設定光罩,以對所述負光阻層30進行曝光顯影,得到所述負光阻層30的光阻預設結構。步驟S103:對所述光阻預設結構及所述透明有機層20進行蝕刻,以去除所述光阻預設結構,并得到所述透明有機層20的透明有機結構,且所述透明有機結構的外型與所述光阻預設結構的外型相同,所述透明有機結構包括多個所述微結構。其中,所述設定光罩設有全曝光區40、半曝光區50及無曝光區60,所述半曝光區50位于所述全曝光區40的兩側,所述無曝光區60位于所述半曝光區50的中部,多個所述透明微結構具有抗閃光作用。在本實施例中,每個所述微結構的外型為中間厚兩側薄的底面橫截面為圓弧形的凸包,所述凸包的中部對應所述無曝光區60,所述凸包的兩側對應所述半曝光區50。在本實施例中,各個所述微結構的大小不完全相同,且相鄰兩個所述微結構之間設有間距,該間距區對應所述全曝光區40。在本實施例中,所述凸包的曲率半徑范圍為2~100um,相鄰兩個所述凸包之間的間隔范圍為0.2~30um,所述凸包的高度范圍為1~100um,所述間隔范圍為所述曲率半徑范圍的0.1~0.3倍,所述高度范圍為所述曲率半徑范圍的0.5~2倍。請參考圖10至圖17,圖10為本實施例的抗閃光蓋板的制造方法實施步驟中,將玻璃基板10清洗并烘干后的示意圖。圖11為本實施例的抗閃光蓋板的制造方法實施步驟中,在玻璃基板10上涂覆一透明有機層20的示意圖。圖12為本實施例的抗閃光蓋板的制造方法實施步驟中,在透明有機層20上涂覆一負光阻層30的示意圖。圖13為本實施例的抗閃光蓋板的制造方法實施步驟中,將紫外光線70照射所述設定光罩,對所述負光阻層30進行曝光顯影的示意圖。圖14為本實施例的抗閃光蓋板的制造方法實施步驟中,得到負光阻層30的光阻預設結構的示意圖。圖15為本實施例的抗閃光蓋板的制造方法實施步驟中,去除光阻預設結構,并得到透明有機層20的透明有機結構的示意圖。圖16為本實施例的抗閃光蓋板的制造方法實施步驟中,得到的透明有機材料層形成的多個所述微結構的豎截面近似于圓弧狀的示意圖。圖17為本實施例的凸包的弦切角、曲率半徑和深度的結構參數表達示意圖。本發明在所述玻璃基板10上形成多個微結構,使每個所述微結構的不同結構參數大小均符合其對應的所述目標大小范圍,及使符合各種結構參數要求的所述微結構的個數占全部所述微結構的比例均符合其對應的所述目標占比范圍,以使所述抗閃光蓋板具有抗閃光作用。本發明的制作方法的具體實施步驟如下所述:本發明采用光刻的方法進行玻璃基板10表面微結構的制備,微結構主要的工藝結構參數如圖17所示,其中r為凸包的曲率半徑,h為凸包的高度,β為凸包的弦切角,h/r為高寬比。具體工藝操作流程如圖10至圖16所示。首先,將玻璃基板10清洗干凈并烘干,如圖10所示。然后在玻璃基板10表面涂布一層與玻璃基板10組分相近的材質以形成涂布層,該涂布層和玻璃基板10有很相近的物理性質,保證涂布層在玻璃基板10表面擁有良好的附著力,如圖11所示。接著在涂布層的上方涂布一層負光阻層30,負光阻層30的涂布需要厚度合適且均勻,如圖12所示。然后用光罩的方式在負光阻層30表面形成相應的圖案,其中該光罩包括無曝光區60、全曝光和半曝光區50,如圖13所示,經過使用紫外光線70曝光之后,負光阻層30無曝光區60的光阻被洗掉,全曝光區40的光阻完全保留,半曝光區50光阻被部分洗掉,如圖14所示。接著利用干刻或濕刻的方式將中間位置的涂布層完全蝕刻掉,再利用光阻清洗劑將兩側光阻中的半曝光區50清洗掉,如圖15所示。最后再次利用干刻或者蝕刻的方式進行將半曝光區50下方的涂布層進行部分蝕刻,并清洗掉涂布層上方的全部光阻,得到如圖16所示的微結構類型。其中,光刻工藝加工產生的凸包的結構特征參數具體包括:凸包呈現出從球狀到圓弧狀的幾何形貌,其曲率半徑r的大小范圍在2~100um之內,凸包之間的間隔大小范圍在0.2~30um之內,其中凸包之間的間隔約為曲率半徑r的0.1~0.3倍,凸包凸起高度h的大小范圍在1~100um之內,其中凸包凸起高度h約為其曲率半徑r的0.5~2倍。本發明采用光刻的方式制備從圓弧狀到球狀的抗閃光凸包結構,通過光罩工藝精確控制凸包周期大小、間距和高度,當凸包的曲率半徑r大小在2~100um范圍內,凸包間距在0.2~30um的范圍內(間距為曲率半徑r大小的0.1~0.3倍),凸包高度在1~100um的范圍內(高度h為曲率半徑r大小的0.5~2倍),通過光學軟件模擬進行驗證,本發明很好地改善了玻璃基板10表面的抗閃光效果。綜上所述,雖然本發明已以優選實施例揭露如上,但上述優選實施例并非用以限制本發明,本領域的普通技術人員,在不脫離本發明的精神和范圍內,均可作各種更動與潤飾,因此本發明的保護范圍以權利要求界定的范圍為準。當前第1頁1 2 3