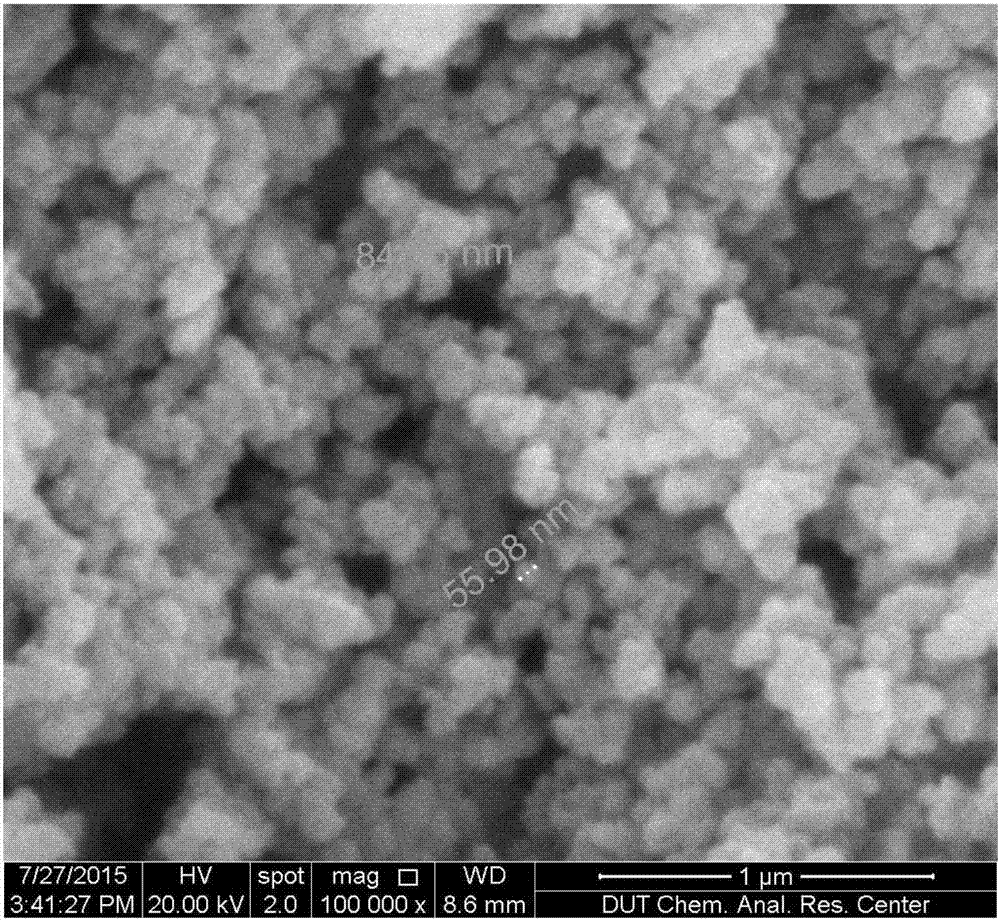
本發明屬于濕法冶金和資源回收的領域,具體涉及一種利用鉻礦、含鉻中間產物和含鉻廢棄物來生產具有多種用途的鉻化合物的處理方法。
背景技術:鉻具有熔、沸點高、硬度大、抗腐蝕性強等特點,三氧化二鉻是一種廣泛應用的多用產品,在化工、耐火材料和金屬材料等領域應用廣泛。但目前世界上鉻資源大部分品質較低,而各種廢棄的含鉻有害廢渣。尤其是六價鉻的廢渣不僅造成水體污染,土壤污染導致糧食和整個食物鏈的污染危害極大。目前我國有大約20加生產紅礬鈉的廠家,由于產生大量的廢棄物處理不當,造成了相當大的浪費。含有的六價鉻是嚴重危害人體健康的一種元素,而且其水溶性較好,固體廢渣大量堆放時,由于雨水沖刷的原因,會造成大量的環境污染。但三價鉻卻是毒性相對較小的一種元素,而且還是人體所必須的一種微量元素,如果將含大量六價鉻的廢渣轉化為三價鉻,用于相應的方面,則會有很大前景。為此,如何在低品位的鉻礦和中間產物綠色提取鉻減少有害廢棄物,以及從含鉻廢渣綜合回收鉻資源具有實際意義。目前,對于鉻鐵礦有磁選法和電選法兩種,前者要求其中的鐵有強磁性,但實際生活中很難滿足這個條件,電選能滿足弱磁性分離,但處理量小,成本高,因此規模難以擴大(唐曉玲,朱霞麗.一種通過磁化焙燒使鉻鐵礦中鉻鐵分離,中國,ZL.201310475068.0)。用酸處理鉻鐵礦和鉻鐵渣時,浸出液中會有大量的鐵離子,影響回收、富集鉻的質量,因此,在鉻回收之前必須除去其中的鐵。2005年,Dahnke等人在《IronControlinHydrometallurgy》提出采用磷酸沉淀法從酸性水溶液中除鐵的方法,研究指出在25~57℃范圍內,溫度對磷酸沉鐵影響不明顯,在室溫下形成的沉淀為無定型,而在50℃以上溫度條件下所得沉淀物則具有類似磷硅酸鐵天然礦物的晶型。2006年李雪飛釆用膦酸類萃取劑(如P204)在溶液pH值為1.5及一定相比萃取時間條件下,鐵萃取率可達99%以上但同時鉻的萃取率也高達25%。2007年胡國榮發表專利提出將針鐵礦法應用于酸性溶液除鐵并回收鉻,雖然鐵的去除率高達99%,但鉻損率也較高15%,而且還很有可能造成鉻的二次污染。2011年王親猛根據草酸亞鐵溶度積較低(Ksp=2.1×10-7,25℃)的性質,使溶液中的鐵以草酸亞鐵形式沉淀析出。對草酸沉鐵而言,除溫度和pH值外,草酸加入量是本方法的另一個關鍵因素。若草酸加入量過低,則亞鐵離子難以沉淀完全,若添加量過多,則過量的草酸根將與草酸亞鐵發生配合反應,沉淀下來的鐵離子重新溶解并返回溶液,使鐵的去除率不升反降。雖然草酸亞鐵沉淀法可以實現鉻、鐵有效分離,工藝過程簡單且易于操作,產品為草酸亞鐵和三氧化二鉻粉體,但該工藝需嚴格控制草酸加入量,而且限于pH值條件,溶液中和負荷較重。2015年徐志峰等在《有色金屬科學與工程》中指出,對溶液中的鉻、鐵離子可用磷酸沉淀法加以分離,最終可使沉淀后溶液中鉻的濃度降至0.04g/L左右,沉鉻渣中鐵含量降至0.4%。固體廢棄物中,鉻鋁渣是一種重要冶金過程的污染物。鄧祥義等在1995年《湖北化工》第3期“廢料鋁泥中鉻的回收”一文中處理含鉻鋁泥過程利用聚丙烯酰胺高分子沉淀鋁,六價鉻可進入溶液達到分離鉻鋁的目的;該方法目前已經廣泛用于鉻冶金過程,由于沉淀的氫氧化鋁膠體吸附性很強,含鉻高,分離系數低,尤其是隨著環境標準的提高和新材料雜質控制精度的提高難以滿足目前的要求。李莉等人于2010年第4期在《過程工程學報》“熔鹽法活化處理含鉻紅土鎳礦浸出液的鉻鋁分離及堿液循環”一文中提出了改進的方法,利用熱水進行洗滌,提高鉻鋁分離系數;此方法實施過程中,由于要用到大量的水洗操作,會產生不必要的含六價鉻的廢水,造成二次污染,環境污染嚴重,且在堿溶鉻鋁時,會消耗大量的強堿,造成一部分浪費。還有一種分離方法是向鉻鋁渣中加入強堿,使鉻、鋁都以離子形式存在于溶液中,再加入H2O2攪拌,煮沸,將三價鉻全部氧化為六價鉻,然后加入十二烷基硫酸鈉等表面活性劑,并加酸調節溶液pH至充分形成Al(OH)3沉淀,過濾、洗滌、干燥得到高純氫氧化鋁固體,六價鉻在收集的濾液和洗液中(中國專利:201310294122.1,2013,07~12.)。林盛等在2014年第5期《礦冶工程》“從鋁熱法制備金屬鉻所得鉻渣中回收鉻、鋁工藝研究”一文中提出了熔融堿中焙燒-水浸-碳酸化分解-濃縮結晶工藝從鋁熱法生產金屬鉻所得爐渣中回收氧化鋁和鉻酸鈉的方法,探討了鉻渣粒度、堿渣比、焙燒時間以及溫度等因素對鉻和鋁浸出率的影響。鉻和鋁的浸出率隨堿渣比、焙燒時間以及焙燒溫度增加而增加,隨鉻渣粒度減少而增加,最佳浸出工藝條件為:焙燒溫度700℃,焙燒時間4h,粒度0.045mm和堿礦比6∶1。所得鉻鹽(以重鉻酸鈉計)和氧化鋁的純度分別為88.5%和95.4%,總回收率分別達到85.6%和96.4%,鈉以碳酸鈉和碳酸氫鈉的形式得到回收。李小斌等人2008年在《TransactionsofNonferrousMetalsSocietyofChina》第18期上的“Newtechnologyforcomprehensiveutilizationofaluminum-chromiumresiduefromchromiumsaltsproduction”一文中提到,將鉻鋁渣、水、添加劑等準確稱重,加入到高壓釜中,在70~80℃下重結晶反應1~2小時,然后取出冷卻到室溫,過濾、洗滌,得到無鉻鋁渣,實現鉻鋁的分離。C.Capdevila等人2008年在《JournalofMaterialsScience》上發表的“AluminumpartitioningduringphaseseparationinFe-20%Cr-6%AlODSalloy”一文中提到,用相分離的方法將鉻鋁分開。綜上其主要問題提取和回收鉻過程是一直存在六價鉻,分離效率不高導致渣中滯留等不足之處。無論在提取過程還是固廢鉻回收過程如何將六價鉻轉化為三價鉻,再以簡單的方法制備三氧化鉻實現二者分離的方法則會有很大前景,目前還未見報道。
技術實現要素:本發明的目的是克服上述不足問題,提供了一種利用水熱還原氛圍還原六價鉻或抑制六價鉻產生的方法,來進行沉鉻分離鉻鋁和鉻鐵雜質的方法,主要特點是不經過六價鉻的過程提取鉻或先將廢渣中六價鉻轉為三價鉻后進行分離。然后調節pH加還原劑使六價鉻全轉化為三價鉻,然后調節選擇氧化以達到只將二價鐵氧化為三價鐵的目的,經過水熱反應后,分離出鐵,再調節pH,加入適當水化劑,經水熱沉淀鉻處理,過濾、酸性洗液洗滌后可得到氧化鉻晶體,洗液中含有鋁離子,控制合適的酸度即可得到氫氧化鋁,實現了鉻鋁分離和鉻的提純、回收與廢棄資源的綜合利用的方法,流程簡單,反應速度快,雜質少,廢水廢氣排放少,工藝環保,得到的氧化鉻可做半導體光電材料、供冶煉鉻鐵、或經過提純處理生產度鉻氧化物。本發明的技術方案:一種鉻提取和有害廢物治理回收并制備鉻化合物的方法,步驟如下:首先對含鉻固體破碎,含鉻固體中含有鉻、鐵和鋁三種元素;酸浸溶解其中各元素,達到終點pH為0.5~4.5;過濾上述酸液中的不溶物,將過濾后得到溶液作為原料;對過濾得到的不溶物多次處理至鉻含量符合國家環保標準,在上述過程中所用的酸液重復使用;對上述原料調節pH至0.5~6.0,加入還原劑,使六價鉻全部轉化為三價鉻,再調節pH至1.0~5.0,得到分離鉻鐵合格液;向分離鉻鐵合格液中加入氧化劑,得到三價鐵、三價鉻和三價鋁的混合溶液;低溫水熱:在50~150℃溫度條件下,壓力為0.50MPa~2.5MPa條件下,恒溫水熱反應0.5~10小時,反應時伴隨著不斷攪拌,反應結束后過濾得到濾液與含Fe沉渣,調節濾液pH為0.5~3.5,得到沉鉻合格液;高溫水熱:將沉鉻合格液與水化劑置于密閉反應釜中水熱反應,加溫至150℃~300℃,壓力在0.5MPa~3.5MPa之間,保溫1~5小時,對反應后產物過濾、用微酸性液體洗滌、干燥,得到綠色濾餅,即為含Cr化合物,經500~1200℃焙燒后轉化為氧化鉻固體,作為半導體等光電材料。對高溫水熱中過濾和洗滌后得到的濾液調節pH為7.0~9.5,得到的含Al固體,干燥、焙燒得到氧化鋁。將低溫水熱中得到的含Fe沉渣,經高溫脫水后變為鐵紅即為氧化鐵。所述的還原劑選用亞硫酸鈉、過氧化氫、Fe2+或高COD有機廢水。所述的氧化劑選用氧氣、空氣、過氧化氫、臭氧或硫酸自由基。所述的水化劑選用草酸、纖維素、甲醇、甲醛、甲酸、乙醇或葡萄糖。對高溫水熱過濾后的產物洗滌用的微酸性液體,選用pH在3.0~5.0的稀酸。在以上酸浸含鉻固體及調節溶液的pH過程中,選用有機酸和/或無機酸;在調節溶液pH時,采用陽離子離子膜電解法。以上過程中的洗滌液均重復使用。本發明的有益效果:該方法分別采用選擇還原和選擇氧化法并結合水熱進行鉻的提取、回收,沉鉻的率較高,分離效果好,流程簡單,反應速度快,減少了三廢的排放,綠色環保。附圖說明圖1是鉻提取與回收的基本流程圖。圖2是高溫水熱后得到的含鉻化合物SEM表征圖。圖3是高溫水熱后得到的含鉻化合物TEM表征圖。圖4是含鉻化合物經焙燒后得到的氧化鉻SEM表征圖。圖5是含鉻化合物經焙燒后得到的氧化鉻TEM表征圖。圖6是含鉻化合物經焙燒后得到的氧化鉻HRTEM表征圖。圖7是含鉻化合物與其焙燒后得到的氧化鉻XRD表征圖。圖8是焙燒后得到的氧化鉻的紫外吸收光譜圖。圖9是焙燒后得到的氧化鉻的熒光特性圖,激發波長λ=246nm。具體實施方式下面結合技術方案和附圖對本發明作進一步詳細說明,但本發明并不局限于具體實施例。實例1:鉻鐵為原料原料成分如下:表1高碳鉻鐵成分取15.0g高碳鉻鐵,溶于35mL體積分數60%為硫酸溶液中,水浴加熱至80℃,恒溫30min,使其充分反應。然后冷卻到室溫,過濾掉少量不溶物,得到含鉻、鐵和其他雜質的混合溶液濾液,將其稀釋10倍,用質量分數為5%的硫酸調節其pH至2.8。取10mL該濾液,加入2mL質量分數為20%的過氧化氫,攪拌30min,然后置于18mL的密閉反應釜中,在90℃條件下恒溫2小時,再冷卻至室溫,過濾,得到含Fe沉渣與綠色濾液。在該濾液中加入甲醇1.5mL,用質量分數5%的硫酸調節pH至2.1,置于18mL的密閉反應釜中,在210℃條件下恒溫1.5小時,冷卻至室溫,過濾,去離子水洗滌,120℃下干燥2小時,600℃下焙燒3.5小時,得到綠色氧化鉻晶體(產物表征如圖2~圖9所示)。含Fe沉渣經500℃焙燒后得到氧化鐵固體,上述過程中濾液及洗滌液重復使用。實例2:含鉻廢棄渣為原料表2鉻鋁渣成分取10.0g鉻鋁渣,溶于20mL體積分數13%為硫酸溶液中,加熱反應35min,使得鉻鋁渣反應完全。過濾反應后的物質,得到濾液,將其稀釋5倍,加入0.5mL的質量分數為20%的過氧化氫,攪拌30min,得到綠色溶液。取該溶液10mL,加入1.5mL甲醇,調節pH至1.9,然后加入到18mL的密閉反應釜,140℃下反應2小時。反應結束后,冷卻至室溫,過濾,用pH為3.5的草酸對固體洗滌三次,得到的固體在110℃下烘干2小時,450℃下焙燒2.5小時,得到氧化鉻晶體。對收集到的濾液及洗滌液,調節其pH到8,得到白色沉淀,過濾,去離子水洗滌,干燥,300℃下焙燒2.5小時,得到氧化鋁固體,上述過程中濾液及洗滌液可以重復使用。實例3:一種鉻礦為原料表3鉻礦成分取15.0g鉻礦,溶于30mL體積分數45%為硫酸溶液中,水浴加熱至80℃,恒溫30min,使鉻礦充分反應。然后冷卻到室溫,過濾掉少量不溶物,得到含鉻、鐵和其他雜質的混合溶液濾液,用陽離子膜電解法調節其pH至2.8。取10mL該濾液,在攪拌的條件下,通入臭氧10min完成選擇性氧化,然后置于18mL的密閉反應釜中,在90℃條件下恒溫1小時,再冷卻至室溫,過濾,得到含Fe沉渣與綠色濾液。在綠色濾液中加入甲醇1.5mL,用陽離子膜電解法調節pH至2.1,置于18mL的密閉反應釜中,在210℃下恒溫1.5小時,冷卻至室溫,過濾,用去離子水洗滌,120℃下干燥2小時,500℃下焙燒3小時,得到氧化鉻晶體。對收集到的濾液及洗滌液,調節其pH到8,得到白色沉淀,過濾,去離子水洗滌,干燥,300℃下焙燒2.5小時,得到氧化鋁固體,上述過程中濾液及洗滌液可以重復使用。