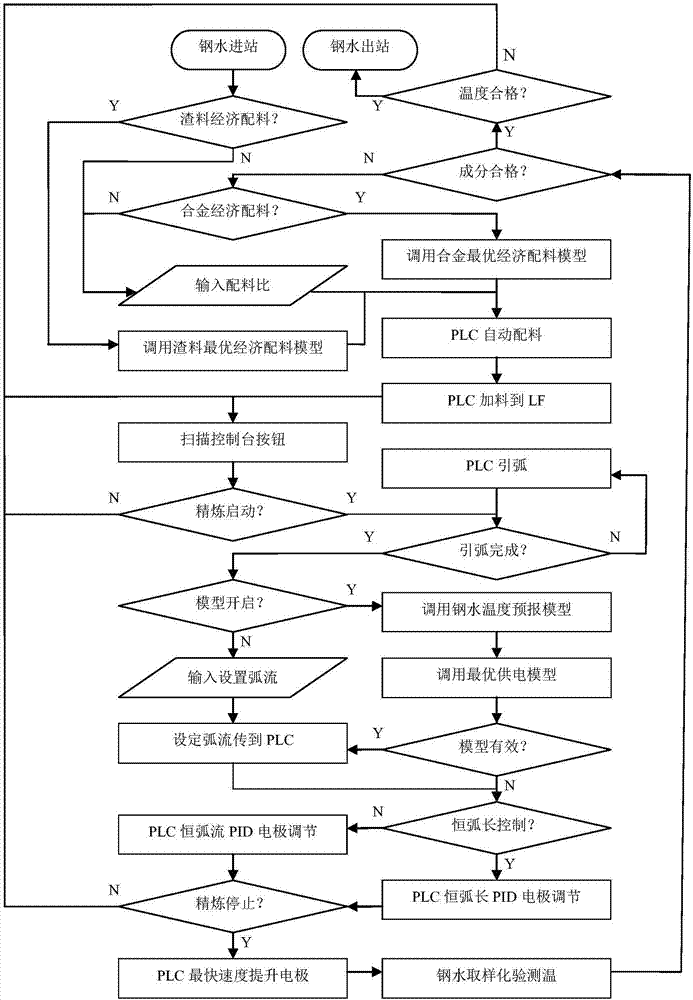
本發明涉及冶金爐外精煉控制
技術領域:
,尤其涉及一種lf精煉爐最優經濟配料和智能控制模型。
背景技術:
:lf鋼包精煉爐用于對轉爐初煉鋼水進行二次精煉處理。即:鋼水加熱、升溫、成份調整、脫硫、去氣、去除夾雜、均勻鋼水成份和溫度。經過鋼包精煉處理,可獲得品質更高的鋼水,品種轉換機動靈活,成份、溫度控制更為準確,并且作為轉爐與板坯連鑄機之間的緩沖環節,均衡協調轉爐與連鑄機的生產節奏,解除了連鑄生產的后顧之憂,是實現多包連澆高效生產的關鍵設備。lf鋼包精煉爐自動控制系統的控制品質直接影響最終鋼水產品質量,特別是電極升降調節模式,不僅決定鋼水的加熱、升溫品質,還關系到噸鋼電耗。目前已有的lf爐控制系統只針對鋼水的加熱、升溫加以考慮,僅滿足工藝要求為目標,而忽略了對lf系統電耗的綜合考慮。現有的lf鋼包精煉爐鋼水測溫都是斷電離線測溫模式,測溫等待期間散熱損失不可避免,從而額外增加了電耗,而且爐前測溫操作人員的勞動強度相應增大。現有lf鋼包精煉爐配料(渣料和鐵合金及喂絲)都采用離線計算模式人工計算渣料和鐵合金及喂絲配比,不僅繁瑣,而且實時性滯后,也會間接導致鋼水品質降低。技術實現要素:針對lf鋼包精煉爐的控制缺陷,發明了一種lf精煉爐最優經濟配料和智能控制模型,克服現有lf控制技術的缺陷和不足。結合lf爐的特點,推導出lf爐最優經濟配料數學模型和鋼水溫度預報數學模型及以電耗最低為目標的電極智能調節數學模型,通過編制vbs腳本程序嵌入到wincc,即可實現lf鋼包精煉爐最優經濟配料和智能控制。用于在線預報鋼水溫度、自動獲得最優經濟配料、在滿足工藝要求的條件下使噸鋼電耗達到最低。為了達到上述目的,本發明采用以下技術方案實現:一種lf精煉爐最優經濟配料和智能控制模型,包括lf爐最優經濟配料模型和lf爐鋼水溫度預報和最優供電模型;一、所述lf爐最優經濟配料模型過程如下:首先,將公式中用到的參數進行說明:lf爐渣料化學成分和價格及加入量見表1;其中渣料化學成分和價格為已知量,加入量為待求未知量;表1渣料化學成分和價格lf爐合金(含喂絲)化學成分和價格及加入量見表2;其中合金(含喂絲)化學成分和價格為已知量,加入量為待求未知量;表2合金化學成分和價格注:合金中含喂絲;合金中化學元素收得率見表3;收得率為已知量;表3合金中化學元素收得率成分1成分2...成分m收得率η1η2...ηm目標鋼水化學成分見表4;化學成分上下限為已知量;表4目標鋼水標準和初始鋼水化學成分鋼包幾何參數:d—鋼包底部外徑,md—鋼包底部內徑,mh--鋼包外部高度,mh—鋼包內部深度,mθ—鋼包側面半錐角,弧度;1.1模型簡化(1)由轉爐來的鋼包,鋼包中的鋼渣渣層厚度忽略不計;(2)合金中元素除標明的收得率外,其它元素均全部進入鋼相中;1.2建模1.2.1約束條件1.2.1.1熔渣堿度(二元堿度)約束為保障爐渣流動性,熔渣堿度(二元堿度cao/sio2)應該控制在一定范圍內;式中:rh、rl--熔渣堿度(二元堿度)上、下限;1.2.1.2熔渣中mgo含量約束熔渣中合適的mgo含量是提高鋼包爐襯耐火材料壽命的保證;式中:am,h、am,l--渣中mgo含量上、下限;1.2.1.3熔渣層厚度約束鋼水重量mg對應的渣線直徑dz則mg--鋼水質量,kgρg--鋼水密度,kg/m3ρg=7138由上式解出dz為保證埋弧操作,熔渣線上部渣層厚度不低于hz式中ρb,j--j=1,2,3,4分別為cao、sio2、mgo、al2o3密度,kg/m3ρa,1=3350,ρa,2=2600,ρa,3=3580,ρa,4=3960;1.2.1.4鋼水合金元素化學成分約束lf目標鋼水成分需滿足國標要求;式中:ch,j、cl,j--合金元素化學成分j國家標準上、下限;1.2.2目標函數總配料成本最低1.3模型求解式(1)~(5)可以分解為2個獨立的線性規劃問題分別求解;1.3.1渣料最優經濟配料模型s.t.xa,i≥0(i=1,2,...,k)變量個數k,約束條件個數5,用兩階段單純形法可求出最優解;1.3.2合金最優經濟配料模型s.t.xb,i≥0(i=1,2,...,n)變量個數n,約束條件個數2m,用兩階段單純形法可求出最優解;目標鋼水化學成分見表4;化學成分上下限為已知量;二、所述lf爐鋼水溫度預報和最優供電模型過程如下:根據lf系統能量平衡,確定鋼水當前溫度與實時輸入的有功電功率的函數關系;2.1模型簡化(1)電極形成電弧無電抗,僅等效為電阻;(2)三相平衡,即變壓器負載側abc三相內阻、內抗相同、空載電壓相同,abc三相短網內阻、內抗相同;(3)冶煉時間僅從電極通電開始計算,中間斷電(取樣、測溫、加料)不計入冶煉時間,忽略斷電期間的lf爐熱損;(4)忽略熔渣化學反應生成熱;(5)忽略合金(含喂絲)熔化潛熱;2.2供電策略(1)輸入lf爐內的三相電功率平衡(相等);(2)滿足供電制度條件下,總電耗最低;rb、xb為變壓器負載側單相電阻(ω)、電抗(ω),隨變壓器電壓檔位變化,rd、xd為lf爐單相短網電阻(ω)、電抗(ω),r為電弧等效電阻(ω),i為單相有效電流(a),ub為變壓器負載側空載電壓(v);ub與lf當前溫度t有關,即不同的升溫階段選擇不同的電壓等級;上式中:r0=rb(ub)+rdx0=xb(ub)+xd2.3建模2.3.1鋼水溫度預報模型2.3.1.1能量收入(1)輸入電能q1,jq1=ni2rdt(7)式中:n—電極根數,交流lf爐,n=3,直流lf爐n=1i—負載側單相電流,ar—單相電弧等效電阻,ωdt—微元時間,s(2)電極燃燒放熱q2,jq2=n[-δhc(t)]dcdt(8)式中:dc—單根電極平均消耗速度,kg/sδhc(t)--石墨燃燒生成co的熱效應,j/kgδhc(t)為溫度t(k)的函數;ac=-9.15×106,bc=-310.8,cc=0.3817,dc=-9.642×1072.3.1.2能量支出(1)鋼水升溫顯熱q1’,j式中:cg--鋼水平均比熱,j/(kgk)cg=1.046×106dt—鋼水微升溫,k(2)渣料升溫顯熱q2’,j式中:cz(t)—熔渣比熱,j/(kgk)cz(t)為溫度t(k)的函數;aa,1=886.0,ba,1=0.0807,ca,1=-1.241×107aa,2=732.0,ba,2=0.6468,ca,2=-1.133×107aa,3=1224.5,ba,2=0.0785,ca,3=-2.860×107aa,4=1125.2,ba,2=0.1255,ca,3=-3.475×107(3)lf爐襯耐火材料升溫顯熱q3’,jq3'=(ccmc+cdmd)dt(11)式中:mc—鋼包襯側面耐火材料質量,kgcc—鋼包襯側面耐火材料比熱,j/(kgk)md—鋼包襯底部耐火材料質量,kgcd—鋼包襯底部耐火材料比熱,j/(kgk)ρc—鋼包襯側面耐火材料密度,kg/m3ρd—鋼包襯底部耐火材料密度,kg/m3(4)氬氣帶走顯熱q4’,jq4'=farcar(t-t0)dt(12)式中:ca—氬氣比熱,j/(m3k)car=928.1far—氬氣流量,m3/st0—環境溫度,k(5)冷卻水帶走顯熱q5’,jq5'=fh2och2o(th2o1-th2o0)dt(13)式中:ch2o—水比熱,j/(kgk)ch2o=4962fh2o—lf爐(爐蓋)冷卻水流量,kg/sth2o0—冷卻水入口溫度,kth2o1—冷卻水出口溫度,k(6)lf爐表面輻射和對流熱損q6’,jq6'=qrdt(14)式中:qr—單位時間表面輻射和對流熱損,wqr通常為一常數,通過歷史數據統計得到;3.2.3能量平衡lf爐能量收入=lf爐能量支出lf爐能量收入=輸入電能+電極燃燒放熱lf爐能量支出=鋼水升溫顯熱+渣料升溫顯熱+lf爐襯耐火材料升溫顯熱+氬氣帶走顯熱+冷卻水帶走顯熱+lf表面輻射和對流熱損式(7)~(14)代入式(15):fh2och2o(th2o1-th2o0)dt+qrdt整理上式得到:式中:q(t)=nδhc(t)dc+farcar(t-t0)+fh2och2o(th2o1-th2o0)+qrq(t)為各項與時間無關的熱損失速度(熱收入為負)之和,是溫度t的函數;c(t)為各項與質量有關的熱容之和,是溫度t的函數;式(16)為鋼水升溫速度與供電功率和鋼水溫度的函數關系式;如果考慮三相不平衡(變壓器內阻抗不平衡、短網阻抗不平衡、電流不平衡),根據式(16)的意義,并用式(6)的r代入得到:式中:tt—t時刻的鋼水溫度,ktt+δt—t+δt時刻的鋼水溫度,k式(17)即為鋼水溫度預報數學模型,只要給定初始鋼水溫度,經過迭代計算即可達到當前時刻鋼水溫度;其中ii為實測得到的各單相電流值,r0,i、x0,i分別為變壓器內阻與短網電阻之和、變壓器內抗與短網電抗之和;2.3.2最優供電模型根據供電策略,輸入lf爐三相功率相同,lf爐總電耗為:式(16)代入上式中,并用式(6)的i代入得到:式中:t1—加熱開始溫度,kt2—加熱結束溫度,k當時,式(18)取得極值;求出極值點等效電阻r*:式(19)代入式(6)中,求出極值點單相電流i*:在極值點:由式(21)可知,在極值點處,說明式(18)恒存在極小值;式(20)即為lf爐最優供電模型,最佳設定電流是鋼水溫度t單調函數,按照設定的最佳電流冶煉,可以得到最低的電耗;但lf精煉過程必須按照供電制度u(t)滿足工藝升溫要求,即鋼水升溫速度不低于工藝設定值;由式(16)可知,鋼水升溫速度要求滿足:式中:δ(t)—由精煉工藝確定的升溫速度,不同溫度區間升溫速度不同,k/simin—滿足精煉工藝要求的單相最小電流,a式(6)中的r代入上式,解出關于imin的方程:式中:為單相電弧最小功率;由式(20)、(22),得到lf爐最佳設定電流為:i0=min[imax,max(i*,imin)]i0=min(imax,max(i*,imin))其中:imax--為變壓器相應電壓ub(t)下的額定電流,a功率因數:式(19)代入上式中,求出最優功率因數:上述lf爐最優供電模型是針對三相交流lf爐導出的,導出的結果也適用于直流lf爐,用于直流lf爐時,只需令n=1(電極根數),并且r0=3rb+rd,x0=3xb;2.4控制策略電弧電壓與電弧長度關系:u=α+βl(24)式中:u—電弧電壓,vα—陰極區和陽極區電壓降之和,vβ—弧柱中的電位梯度,v/ml—電弧長度,m由于電弧等效電阻:r帶入式(6),得到:由式(24)和式(25),得到:由式(26)可見,在特定電壓下,電弧長度l只是單相電流i的單調函數,最佳電流i0對應的電弧長度l(i0);電極的升降運動是通過比例閥控制液壓傳動系統實現的,比例閥通過控制液壓介質的流量改變電極升降速度,與電極升降直接關聯的被控參數是電弧長度,而電弧電壓又與電弧長度成線性關系,因而通過電極升降即可直接控制電弧電壓,給定電流最佳設定值i0,最佳電弧電壓設定值u0由式(25)得到;采用pid控制電極升降,以u0作為被控參數,通過適當選取比例值、積分時間、微分時間,可以達到快速達到穩態。與現有技術相比,本發明的有益效果是:1、lf渣料、鐵合金(含喂絲)配料在滿足工藝要求最終鋼水質量的前提下,達到最經濟配料;2、實現lf爐鋼水在線溫度預報,免除人工測溫帶來測溫元件消耗和額外勞動強度;3、在供電制度給定的條件下,按照最優供電智能模型得到的最佳電流進行電極控制,可以獲得最低噸鋼電耗。附圖說明圖1為本發明的交流lf爐的單相等效電路圖;圖2為本發明的plc控制系統上位機vbs腳本語言編程邏輯程序框圖。具體實施方式以下結合附圖對本發明提供的具體實施方式進行詳細說明。一種lf精煉爐最優經濟配料和智能控制模型,包括lf爐最優經濟配料模型和lf爐鋼水溫度預報和最優供電模型;一、所述lf爐最優經濟配料模型過程如下:首先,將公式中用到的參數進行說明:lf爐渣料化學成分和價格及加入量見表1;其中渣料化學成分和價格為已知量,加入量為待求未知量;表1渣料化學成分和價格lf爐合金(含喂絲)化學成分和價格及加入量見表2;其中合金(含喂絲)化學成分和價格為已知量,加入量為待求未知量;表2合金化學成分和價格注:合金中含喂絲;合金中化學元素收得率見表3;收得率為已知量;表3合金中化學元素收得率成分1成分2...成分m收得率η1η2...ηm目標鋼水化學成分見表4;化學成分上下限為已知量;表4目標鋼水標準和初始鋼水化學成分鋼包幾何參數:d—鋼包底部外徑,md—鋼包底部內徑,mh--鋼包外部高度,mh—鋼包內部深度,mθ—鋼包側面半錐角,弧度;1.1模型簡化(1)由轉爐來的鋼包,鋼包中的鋼渣渣層厚度忽略不計;(2)合金中元素除標明的收得率外,其它元素均全部進入鋼相中;1.2建模1.2.1約束條件1.2.1.1熔渣堿度(二元堿度)約束為保障爐渣流動性,熔渣堿度(二元堿度cao/sio2)應該控制在一定范圍內;式中:rh、rl--熔渣堿度(二元堿度)上、下限;1.2.1.2熔渣中mgo含量約束熔渣中合適的mgo含量是提高鋼包爐襯耐火材料壽命的保證;式中:am,h、am,l--渣中mgo含量上、下限;1.2.1.3熔渣層厚度約束鋼水重量mg對應的渣線直徑dz則mg--鋼水質量,kgρg--鋼水密度,kg/m3ρg=7138由上式解出dz為保證埋弧操作,熔渣線上部渣層厚度不低于hz式中ρb,j--j=1,2,3,4分別為cao、sio2、mgo、al2o3密度,kg/m3ρa,1=3350,ρa,2=2600,ρa,3=3580,ρa,4=3960;1.2.1.4鋼水合金元素化學成分約束lf目標鋼水成分需滿足國標要求;式中:ch,j、cl,j--合金元素化學成分j國家標準上、下限;1.2.2目標函數總配料成本最低1.3模型求解式(1)~(5)可以分解為2個獨立的線性規劃問題分別求解;1.3.1渣料最優經濟配料模型s.t.xa,i≥0(i=1,2,...,k)變量個數k,約束條件個數5,用兩階段單純形法可求出最優解;1.3.2合金最優經濟配料模型s.t.xb,i≥0(i=1,2,...,n)變量個數n,約束條件個數2m,用兩階段單純形法可求出最優解;目標鋼水化學成分見表4;化學成分上下限為已知量;二、所述lf爐鋼水溫度預報和最優供電模型過程如下:根據lf系統能量平衡,確定鋼水當前溫度與實時輸入的有功電功率的函數關系;lf爐冶煉不同鋼種,有不同的供電制度,即在某一溫度區間,送電電壓等級不同,在給定的供電制度和最低升溫速度下,鋼水升溫速度對冶煉電耗影響很大,為了減少熱損失項(lf爐體表面散熱、冷卻水帶走的熱、氬氣攪拌帶走的熱),應盡可能加大電流,縮短冶煉時間。但加大電流的同時,lf爐短網和變壓器電能損耗急劇增加(電能損耗與電流平方成正比),因此存在一個使得總電耗最低的平衡點,這個平衡點是動態的,隨著供電電壓等級和鋼水溫度而改變,在平衡點的電流即為最佳電流。lf最優供電模型就是要找到最佳電流設定值。2.1模型簡化(1)電極形成電弧無電抗,僅等效為電阻;(2)三相平衡,即變壓器負載側abc三相內阻、內抗相同、空載電壓相同,abc三相短網內阻、內抗相同;(3)冶煉時間僅從電極通電開始計算,中間斷電(取樣、測溫、加料)不計入冶煉時間,忽略斷電期間的lf爐熱損;(4)忽略熔渣化學反應生成熱;(5)忽略合金(含喂絲)熔化潛熱;2.2供電策略(1)輸入lf爐內的三相電功率平衡(相等);(2)滿足供電制度條件下,總電耗最低;如圖1所示,為交流lf爐的單相等效電路圖;圖1中,rb、xb為變壓器負載側單相電阻(ω)、電抗(ω),隨變壓器電壓檔位變化,rd、xd為lf爐單相短網電阻(ω)、電抗(ω),r為電弧等效電阻(ω),i為單相有效電流(a),ub為變壓器負載側空載電壓(v);ub與lf當前溫度t有關,即不同的升溫階段選擇不同的電壓等級;上式中:r0=rb(ub)+rdx0=xb(ub)+xd2.3建模2.3.1鋼水溫度預報模型2.3.1.1能量收入(1)輸入電能q1,jq1=ni2rdt(7)式中:n—電極根數,交流lf爐,n=3,直流lf爐n=1i—負載側單相電流,ar—單相電弧等效電阻,ωdt—微元時間,s(2)電極燃燒放熱q2,jq2=n[-δhc(t)]dcdt(8)式中:dc—單根電極平均消耗速度,kg/sδhc(t)--石墨燃燒生成co的熱效應,j/kgδhc(t)為溫度t(k)的函數;ac=-9.15×106,bc=-310.8,cc=0.3817,dc=-9.642×1072.3.1.2能量支出(1)鋼水升溫顯熱q1’,j式中:cg--鋼水平均比熱,j/(kgk)cg=1.046×106dt—鋼水微升溫,k(2)渣料升溫顯熱q2’,j式中:cz(t)—熔渣比熱,j/(kgk)cz(t)為溫度t(k)的函數;aa,1=886.0,ba,1=0.0807,ca,1=-1.241×107aa,2=732.0,ba,2=0.6468,ca,2=-1.133×107aa,3=1224.5,ba,2=0.0785,ca,3=-2.860×107aa,4=1125.2,ba,2=0.1255,ca,3=-3.475×107(3)lf爐襯耐火材料升溫顯熱q3’,jq3'=(ccmc+cdmd)dt(11)式中:mc—鋼包襯側面耐火材料質量,kgcc—鋼包襯側面耐火材料比熱,j/(kgk)md—鋼包襯底部耐火材料質量,kgcd—鋼包襯底部耐火材料比熱,j/(kgk)ρc—鋼包襯側面耐火材料密度,kg/m3ρd—鋼包襯底部耐火材料密度,kg/m3(4)氬氣帶走顯熱q4’,jq4'=farcar(t-t0)dt(12)式中:ca—氬氣比熱,j/(m3k)car=928.1far—氬氣流量,m3/st0—環境溫度,k(5)冷卻水帶走顯熱q5’,jq5'=fh2och2o(th2o1-th2o0)dt(13)式中:ch2o—水比熱,j/(kgk)ch2o=4962fh2o—lf爐(爐蓋)冷卻水流量,kg/sth2o0—冷卻水入口溫度,kth2o1—冷卻水出口溫度,k(6)lf爐表面輻射和對流熱損q6’,jq6'=qrdt(14)式中:qr—單位時間表面輻射和對流熱損,wqr通常為一常數,通過歷史數據統計得到;3.2.3能量平衡lf爐能量收入=lf爐能量支出lf爐能量收入=輸入電能+電極燃燒放熱lf爐能量支出=鋼水升溫顯熱+渣料升溫顯熱+lf爐襯耐火材料升溫顯熱+氬氣帶走顯熱+冷卻水帶走顯熱+lf表面輻射和對流熱損式(7)~(14)代入式(15):fh2och2o(th2o1-th2o0)dt+qrdt整理上式得到:式中:q(t)=nδhc(t)dc+farcar(t-t0)+fh2och2o(th2o1-th2o0)+qrq(t)為各項與時間無關的熱損失速度(熱收入為負)之和,是溫度t的函數;c(t)為各項與質量有關的熱容之和,是溫度t的函數;式(16)為鋼水升溫速度與供電功率和鋼水溫度的函數關系式;如果考慮三相不平衡(變壓器內阻抗不平衡、短網阻抗不平衡、電流不平衡),根據式(16)的意義,并用式(6)的r代入得到:式中:tt—t時刻的鋼水溫度,ktt+δt—t+δt時刻的鋼水溫度,k式(17)即為鋼水溫度預報數學模型,只要給定初始鋼水溫度,經過迭代計算即可達到當前時刻鋼水溫度;其中ii為實測得到的各單相電流值,r0,i、x0,i分別為變壓器內阻與短網電阻之和、變壓器內抗與短網電抗之和;2.3.2最優供電模型根據供電策略,輸入lf爐三相功率相同,lf爐總電耗為:式(16)代入上式中,并用式(6)的i代入得到:式中:t1—加熱開始溫度,kt2—加熱結束溫度,k當時,式(18)取得極值;求出極值點等效電阻r*:式(19)代入式(6)中,求出極值點單相電流i*:在極值點:由式(21)可知,在極值點處,說明式(18)恒存在極小值;式(20)即為lf爐最優供電模型,最佳設定電流是鋼水溫度t單調函數,按照設定的最佳電流冶煉,可以得到最低的電耗;但lf精煉過程必須按照供電制度u(t)滿足工藝升溫要求,即鋼水升溫速度不低于工藝設定值;由式(16)可知,鋼水升溫速度要求滿足:式中:δ(t)—由精煉工藝確定的升溫速度,不同溫度區間升溫速度不同,k/simin—滿足精煉工藝要求的單相最小電流,a式(6)中的r代入上式,解出關于imin的方程:式中:為單相電弧最小功率;由式(20)、(22),得到lf爐最佳設定電流為:i0=min[imax,max(i*,imin)]i0=min(imax,max(i*,imin))其中:imax--為變壓器相應電壓ub(t)下的額定電流,a功率因數:式(19)代入上式中,求出最優功率因數:上述lf爐最優供電模型是針對三相交流lf爐導出的,導出的結果也適用于直流lf爐,用于直流lf爐時,只需令n=1(電極根數),并且r0=3rb+rd,x0=3xb;2.4控制策略電弧電壓與電弧長度關系:u=α+βl(24)式中:u—電弧電壓,vα—陰極區和陽極區電壓降之和,vβ—弧柱中的電位梯度,v/ml—電弧長度,m由于電弧等效電阻:r帶入式(6),得到:由式(24)和式(25),得到:由式(26)可見,在特定電壓下,電弧長度l只是單相電流i的單調函數,最佳電流i0對應的電弧長度l(i0);電極的升降運動是通過比例閥控制液壓傳動系統實現的,比例閥通過控制液壓介質的流量改變電極升降速度,與電極升降直接關聯的被控參數是電弧長度,而電弧電壓又與電弧長度成線性關系,因而通過電極升降即可直接控制電弧電壓,給定電流最佳設定值i0,最佳電弧電壓設定值u0由式(25)得到;采用pid控制電極升降,以u0作為被控參數,通過適當選取比例值、積分時間、微分時間,可以達到快速達到穩態。本發明所述的模型方法利用plc控制系統實現,具體實現方法如下:一、將現場儀表檢測到各參量信號送至plc,并經由tcp/ip網絡總線送至上位計算機監控系統,鋼水重量、化學成分通過通過tcp/ip網絡總線傳送至上位計算機系統。儀表系統涉及的檢測參量有:(1)加料系統稱量倉重量;(2)氬氣系統流量;(3)設備冷卻水系統流量、進出口溫度;(4)鋼水檢測溫度;(5)變壓器二次側電壓、電流。儀表系統涉及的控制參量有:電極升降調節比例閥輸信號出(-10~+10v)。電氣系統涉及控制參量有:(1)變壓器二次側有載調壓開關輸出信號(脈沖);(2)渣料倉、合金倉振動給料器輸出信號(開關量);(3)渣料稱量倉、合金稱量倉振料器輸出信號(開關量);(4)下料和上料皮帶運行輸出信號(開關量)。二、上位機用vbs腳本語言編程,邏輯程序框圖見附圖2,采用本發明列出的各數學模型算法,通過時間周期(10秒)事件調用腳本語言。本發明的優選實現方式是選用simatic的plc,上位機平臺軟件wincc,下位機平臺軟件step7。電極調節模式提供恒弧長或恒電流可選模式,建議實施過程采用恒弧長控制模式,用pid算法實現電極跟隨調節,pid參數現場整定。上位機設置一pid參數整定畫面,設置pid參數時以便實時觀察pid整定后的效果。上位機設置一lf爐自動配料畫面,內嵌一按鈕單擊事件,當按下該按鈕時,調用最優配料程序,得到當前最佳配比,按確認按鈕后,自動按照最佳配比加料到指定的lf爐內(預先儲存在緩沖倉)。采用一個獨立的plc可編程控制器組成電極升降自動調節系統,通過信號變換電路及輸入模塊采集系統各相電弧電壓、電弧電流、變壓器電壓等級以及其它相關的給定信號,先將弧流、弧壓、變壓器阻抗、短網阻抗進行運算處理,并將運算結果與給定值進行比較,將輸出信號送至液壓系統電極升降比例閥,實現電極位置自動調節,從而控制輸入到爐內的功率,按照最佳功率曲線運行,滿足精煉工藝要求。在電極自動調節過程中,隨時可以手動干預。采用另一個獨立的plc可編程控制器組成自動加料系統,通過信號變換電路及輸入模塊采集系統各振動給料器、各稱量倉振料器、下料和上料皮帶開關量狀態信號,從上位機獲取最佳經濟配料各料倉的加料量,plc下位程序按順序稱量各料倉渣料和鐵合金(不同稱量倉可以同時稱量操作),同時在上位機顯示各料倉稱量進度。一旦遇有料倉下料堵料情況(一定時間內不下料),自動標記堵料,進行后續料倉配料,配料完畢plc把實際配料量傳送到上位機顯示和記錄。以上實施例在以本發明技術方案為前提下進行實施,給出了詳細的實施方式和具體的操作過程,但本發明的保護范圍不限于上述的實施例。上述實施例中所用方法如無特別說明均為常規方法。當前第1頁12