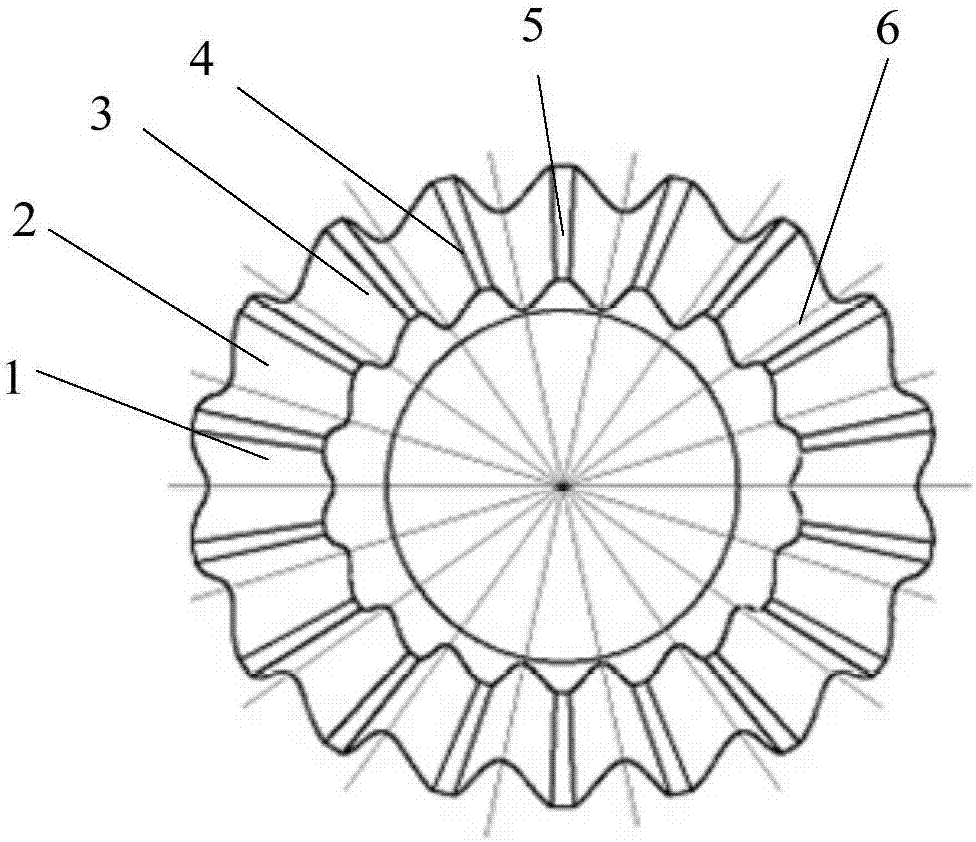
本發(fā)明涉及非圓錐齒輪塑性成形
技術(shù)領(lǐng)域:
,尤其涉及一種用于非圓錐齒輪的熱鍛成形模具及熱鍛成形工藝。
背景技術(shù):
:非圓錐齒輪可以實現(xiàn)兩相交軸或交錯軸之間變傳動比傳動,具有許多圓錐齒輪不能實現(xiàn)的特殊功能,例如采用非圓錐齒輪的汽車防滑差速器不僅具有結(jié)構(gòu)緊湊、傳動平穩(wěn)、效率高、壽命長等優(yōu)點,而且還具有差速防滑功能,在泥濘、濕滑、冰雪等地面的通過性能比傳統(tǒng)的圓錐齒輪差速器有大幅度提高。與具有平面圓節(jié)曲線的圓錐齒輪相比,非圓錐齒輪具有復雜的空間非圓節(jié)曲線,使得其幾何形狀十分復雜,這給非圓錐齒輪制造帶來巨大困難。目前,非圓錐齒輪主要采用五軸聯(lián)動數(shù)控加工中心切削制造,切削加工不能細化齒輪基體晶粒,不能形成沿齒面連續(xù)分布的金屬流線,難以制造出高性能長壽命非圓錐齒輪。因此,多軸聯(lián)動數(shù)控加工無法滿足低成本、高效率、高性能非圓錐齒輪加工制造要求,亟待開發(fā)非圓錐齒輪塑性成形工藝,從而實現(xiàn)非圓錐齒輪高效、優(yōu)質(zhì)、低耗成形制造。技術(shù)實現(xiàn)要素:本發(fā)明的主要目的在于提供一種用于非圓錐齒輪的熱鍛成形模具及熱鍛成形工藝,旨在大幅度提高非圓錐齒輪生產(chǎn)效率,降低制造成本。為實現(xiàn)上述目的,本發(fā)明提供一種用于非圓錐齒輪的熱鍛成形模具設計方法,設計預制坯及預制坯模具時包括以下步驟:將非圓錐齒輪按單個齒分割成多個部分,并將多個分割后的部分轉(zhuǎn)化為多個具有扇形截面且等高的扇形柱體;以多個扇形柱體的圓弧中點為基準點,采用樣條曲線將所有基準點連接成一閉合曲線即為預制坯的徑向截面形狀;根據(jù)扇形柱體的高度、預制坯的徑向截面形狀以及預制坯的最大軸向截面為分模面進行預制坯模具的加工。優(yōu)選地,所述將非圓錐齒輪按單個齒分割成多個部分,并將多個分割后的部分轉(zhuǎn)化為多個具有扇形截面且等高的扇形柱體的步驟具體包括:以非圓錐齒輪軸線和各齒槽頂點為基準建立多個基準面;通過多個基準面將非圓錐齒輪鍛件分割成多個部分;將所分割的各部分按照等體積原則轉(zhuǎn)換為具有扇形截面且等高的扇形柱體,各扇形柱體的扇形截面中心角與非圓錐齒輪中兩相鄰基準面夾角相等。優(yōu)選地,進行終鍛模的型腔設計時,將非圓半軸錐齒輪大端齒形的齒頂曲線沿徑向延伸所得曲面和非圓半軸錐齒輪大端齒形所在球面共同構(gòu)成的分模面進行終鍛模的型腔設計,其中,包含背部軸桿型腔的凹模為上模,包含齒形型腔的齒形模為下模。優(yōu)選地,進行預鍛模的型腔設計時,預鍛模型腔是在終鍛模型腔的基礎上,齒形型腔沿齒面法向增大0.2mm~0.3mm,背部軸桿型腔沿軸向增大0.8~1.2mm,并以非圓半軸錐齒輪大端齒形的齒頂曲線沿徑向延伸所得延伸曲面和非圓半軸錐齒輪大端齒形所在球面共同構(gòu)成的分模面進行分模設計,其中,包含齒形型腔的齒形模為上模,包含背部軸桿型腔的凹模為下模。優(yōu)選地,預鍛模下模型腔底部根據(jù)預制坯徑向截面形狀設計用于預制坯定位的定位槽。優(yōu)選地,最大扇形柱體半徑等于非圓錐齒輪鍛件背部軸桿的半徑。本發(fā)明進一步提出一種基于上述的用于非圓錐齒輪的熱鍛成形模具設計方法的熱鍛成形工藝,包括以下步驟:將圓棒料進行下料以及少無氧化加熱處理;將經(jīng)少無氧化加熱處理后的圓棒料經(jīng)過鐓粗或者拔長,獲得直徑滿足2rmin≤d≤2rmax的圓柱坯料,其中rmin、rmax分別為預制坯徑向截面的最大內(nèi)切圓半徑和和最小外接圓半徑;將經(jīng)過鐓粗或者拔長后的圓棒料在預制坯模具進行預制坯成形獲得預制坯;將預制坯置入預鍛模的下模型腔內(nèi),在壓力機的作用下完成預鍛成形獲得預鍛件;將預鍛件置入終鍛模的下模型腔內(nèi),在壓力機的作用下完成終鍛成形。本發(fā)明提出的用于非圓錐齒輪的預制坯設計方法,能夠有效提高非圓錐齒輪成形過程中金屬流動的合理性和齒形填充效果,并且有利于提高溫度場和塑性變形的均勻性,提高非圓錐齒輪的機械性能。同時,本熱鍛成形預鍛和終鍛模具設計方法相比常規(guī)的平面分模設計方法能夠有效改善模具應力分布,提高模具壽命。附圖說明圖1為本發(fā)明用于非圓錐齒輪的熱鍛成形模具設計方法在設計預制坯模具時的流程示意圖;圖2為非圓錐齒輪的結(jié)構(gòu)示意圖;圖3為預制坯的徑向截面形狀結(jié)構(gòu)示意圖;圖4為預制坯的側(cè)面結(jié)構(gòu)示意圖;圖5為預制坯模具與圓棒料的結(jié)構(gòu)示意圖;圖6為非圓錐齒輪的主視結(jié)構(gòu)示意圖;圖7為非圓錐齒輪的俯視結(jié)構(gòu)示意圖;圖8為非圓錐齒輪的左視結(jié)構(gòu)示意圖;圖9為終鍛模和預鍛模的上模的剖視結(jié)構(gòu)示意圖;圖10為終鍛模和預鍛模的上模的俯視結(jié)構(gòu)示意圖;圖11為圖10所示的a處細節(jié)放大結(jié)構(gòu)示意圖;圖12為終鍛模和預鍛模的下模的剖視結(jié)構(gòu)示意圖;圖13為終鍛模和預鍛模的下模的俯視結(jié)構(gòu)示意圖;圖14為圖12所示的b處細節(jié)放大結(jié)構(gòu)示意圖;圖15為本發(fā)明用于非圓半軸錐齒輪的熱鍛成形工藝優(yōu)選實施例的流程示意圖。圖中,1-齒1,2-齒2,3-齒3,4-齒4,5-齒5,6-基準面,7-預制坯徑向截面,8-預制坯上模,9-圓棒料,10-預制坯下模,11-預制坯分模面,12-大端齒形所在球面,13-大端齒形齒頂曲線,14-徑向延伸曲面,15-終鍛模齒面,16-預鍛模齒面,17-定位槽,18-終鍛模型腔,19-預鍛模型腔。本發(fā)明目的的實現(xiàn)、功能特點及優(yōu)點將結(jié)合實施例,參照附圖做進一步說明。具體實施方式應當理解,此處所描述的具體實施例僅僅用以解釋本發(fā)明,并不用于限定本發(fā)明。本發(fā)明提出一種用于非圓錐齒輪的熱鍛成形模具設計方法。參照圖1至圖14(圖7中虛線為分模面輪廓線,實線為鍛件輪廓線),本優(yōu)選實施例中,一種用于非圓錐齒輪的熱鍛成形模具設計方法,設計預制坯及預制坯模具時包括以下步驟:步驟s10,將非圓錐齒輪按單個齒分割成多個部分,并將多個分割后的部分轉(zhuǎn)化為多個具有扇形截面且等高的扇形柱體;步驟s20,以多個扇形柱體的圓弧中點為基準點,采用樣條曲線將所有基準點連接成一閉合曲線即為預制坯的徑向截面形狀;步驟s30,根據(jù)扇形柱體的高度、預制坯的徑向截面形狀以及預制坯的最大軸向截面為分模面進行預制坯模具的加工(如圖5所示)。具體地,步驟s10具體包括:步驟s101,以非圓錐齒輪軸線和各齒槽頂點為基準建立多個基準面(如圖2所示);步驟s102,通過多個基準面將非圓錐齒輪鍛件分割成多個部分(如圖2所示);步驟s103,將所分割的各部分按照等體積原則轉(zhuǎn)換為具有扇形截面且等高的扇形柱體,各扇形柱體的扇形截面中心角與非圓錐齒輪中兩相鄰基準面夾角相等(如圖3和圖4所示)。為保證預制坯在預鍛型腔中的可靠定位,最大扇形柱體半徑等于非圓半軸錐齒輪背部軸桿的半徑。本實施例中,具有最大體積的扇形柱體的扇形半徑r=25mm。根據(jù)公式計算扇形柱體高度h=29.60mm。根據(jù)各扇形柱體等高的條件,計算出其余扇形半徑ri。各齒形部分的體積vi、扇形截面半徑ri,扇形截面夾角θi和預制坯高度h如表1所示。表1預制坯設計參數(shù)齒1齒2齒3齒4齒5體積vi(mm3)2465.882435.272472.162642.592789.05角度θi(°)25.2322.8919.4717.7517.28高度h(mm)29.6029.6029.6029.6029.60半徑ri(mm)19.4520.3022.1724.0125.00具體地,結(jié)合參照圖6至圖14,進行終鍛模的型腔設計時,將非圓半軸錐齒輪大端齒形的齒頂曲線沿徑向延伸所得曲面和非圓半軸錐齒輪大端齒形所在球面共同構(gòu)成的分模面進行終鍛模的型腔設計,其中,包含背部軸桿型腔的凹模為上模,包含齒形型腔的齒形模為下模。具體地,結(jié)合參照圖6至圖14,進行預鍛模的型腔設計時,預鍛模型腔是在終鍛模型腔的基礎上,齒形型腔沿齒面法向增大0.2mm~0.3mm(圖11中以0.2mm為例說明),背部軸桿型腔沿軸向增大0.8~1.2mm(圖14中以1mm為例說明),并以非圓半軸錐齒輪大端齒形的齒頂曲線沿徑向延伸所得延伸曲面和非圓半軸錐齒輪大端齒形所在球面共同構(gòu)成的分模面進行分模設計,其中,包含齒形型腔的齒形模為上模,包含背部軸桿型腔的凹模為下模。預鍛模下模型腔底部根據(jù)預制坯徑向截面形狀設計用于預制坯定位的定位槽。通過設置定位槽,從而對預鍛件進行有效定位,保證了加工精度。本發(fā)明提出的用于非圓錐齒輪的預制坯設計方法,能夠有效提高非圓錐齒輪成形過程中金屬流動的合理性和齒形填充效果,并且有利于提高溫度場和塑性變形‘的均勻性,提高非圓錐齒輪的機械性能。同時,本熱鍛成形預鍛和終鍛模具設計方法相比常規(guī)的平面分模設計方法能夠有效改善模具應力分布,提高模具壽命。本發(fā)明進一步提出一種用于非圓半軸錐齒輪的熱鍛成形工藝。參照圖15,本優(yōu)選實施例中,一種基于上述熱鍛成形模具設計方法的熱鍛成形工藝,包括以下步驟:步驟s100,將圓棒料進行下料以及少無氧化加熱處理;步驟s200,將經(jīng)少無氧化加熱處理后的圓棒料經(jīng)過鐓粗或者拔長,獲得直徑滿足2rmin≤d≤2rmax的圓柱坯料,其中rmin、rmax分別為預制坯徑向截面的最大內(nèi)切圓半徑和和最小外接圓半徑;步驟s300,將經(jīng)過鐓粗或者拔長后的圓棒料在預制坯模具進行預制坯成形獲得預制坯;步驟s400,將預制坯置入預鍛模的下模型腔內(nèi),在壓力機的作用下完成預鍛成形獲得預鍛件;步驟s500,將預鍛件置入終鍛模的下模型腔內(nèi),在壓力機的作用下完成終鍛成形。具體地,當圓棒料初始直徑大于2rmax時采用拔長工藝獲得圓柱坯料,當圓棒料初始直徑小于2rmin時采用鐓粗工藝獲得圓柱坯料。將圓棒料進行少無氧化加熱處理時,采用中頻感應加熱爐進行圓棒料加熱,加熱溫度為950℃±20℃,并在圓棒料表面噴涂水基石墨乳溶液,噴涂石墨層厚度為1mm~2mm。由于非圓錐齒輪各個齒形幾何形狀都不相同,預鍛件置入下模時,必須嚴格根據(jù)非圓錐齒輪各齒形與終鍛模各齒形型腔對應關(guān)系進行定位。本實施例中,圓棒料先鐓粗至φ47mm×23.5mm的圓柱坯料后,迅速置入預制坯模腔中,通過壓力機加載,完成預制坯成形,獲得合格預制坯鍛件。其中鐓粗圓柱坯料的直徑滿足38.9mm≤d≤50mm。本實施例提出的非圓錐齒輪的熱鍛成形工藝,通過熱鍛的方法成型非圓錐齒輪,能夠取代多軸聯(lián)動數(shù)控切削加工工藝,大幅度提高非圓錐齒輪生產(chǎn)效率,降低制造成本,同時顯著提高非圓錐齒輪的機械力學性能。另外,將圓棒料在預制坯模具進行預制坯成形獲得預制坯,有效提高非圓錐齒輪成形過程中金屬流動的合理性和齒形填充效果,并且有利于提高溫度場和塑性變形的均勻性,提高非圓錐齒輪的機械性能。以上僅為本發(fā)明的優(yōu)選實施例,并非因此限制本發(fā)明的專利范圍,凡是利用本發(fā)明說明書及附圖內(nèi)容所作的等效結(jié)構(gòu)變換,或直接或間接運用在其他相關(guān)的
技術(shù)領(lǐng)域:
,均同理包括在本發(fā)明的專利保護范圍內(nèi)。當前第1頁12