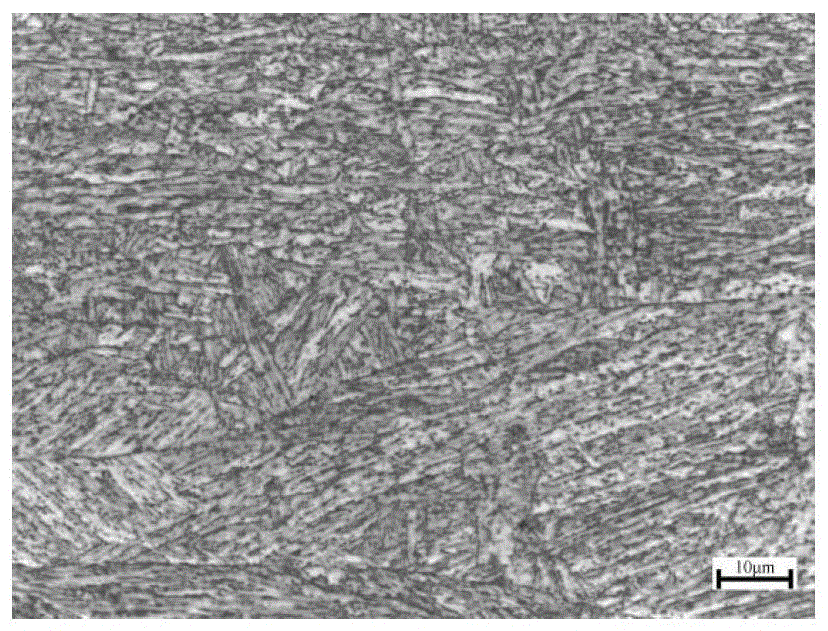
本發(fā)明屬于金屬材料領(lǐng)域,尤其涉及一種屈服強度為800MPa級且具有良好韌性和焊接性能的熱軋高強度鋼及其生產(chǎn)方法。
背景技術(shù):隨著世界經(jīng)濟的發(fā)展,資源、環(huán)境和能源的壓力日益加大,環(huán)保和節(jié)能越來越受到鋼鐵行業(yè)的重視。開發(fā)具有節(jié)能、高效、長壽及性能優(yōu)異的高強度鋼,滿足石油、煤炭、化工、電力、交通等國民經(jīng)濟關(guān)鍵行業(yè)發(fā)展的需要也是鋼鐵工業(yè)實現(xiàn)可持續(xù)發(fā)展的重要途徑。目前用于造船、壓力容器、海洋石油平臺、石油和天然氣輸送管線、鐵路運輸及工程機械等行業(yè)的高強度鋼,不僅需要具有較高的抗拉強度和屈服強度,而且需要良好的韌性和焊接性能,另外也希望在較低的制造成本條件下獲得此類高強度鋼。目前世界上很多鋼鐵研究人員已經(jīng)進行了大量的高強度鋼的開發(fā)工作,這些工作的主要思路是通過適宜的合金設(shè)計和軋制工藝(以及軋后熱處理),來獲得理想的組織形態(tài)和組織匹配,以達到高強度鋼優(yōu)良的綜合性能。公開號為CN101928873A所公開的專利《一種高強度和超高強度鋼板的加工方法》,采用C-Mn-Cr-Ni-Nb-B的合金設(shè)計,在熱軋后通過感應(yīng)加熱方法進行預(yù)熱、淬火和回火的方法生產(chǎn)屈服強度為710~1550MPa的高強度鋼板。公開號為CN1390972A所公開的專利《低合金超高強度鋼種》,采用C-Mn-Cr-Mo-V的合金設(shè)計,在熱軋后通過調(diào)質(zhì)處理(淬火+高溫回火)處理來生產(chǎn)屈服強度為797~1260MPa的高強度鋼板。上述專利雖然可以生產(chǎn)屈服強度為800MPa級鋼板,但都是利用了熱軋+離線熱處理(調(diào)質(zhì)、回火等)的方法,因此生產(chǎn)成本較高。為了能夠降低生產(chǎn)成本,公開號為CN101932745A所公開的專利《高強度鋼板及其制造方法》,通過熱軋和軋后自回火處理得到屈服強度為817MPa的汽車用高強度鋼,但其采用了較高的碳含量(0.33%)、較高的硅含量(1.52%)和較高的錳含量(2.3%),其延伸率為7.5%,強塑積(TS×EL)為11408MPa.%。該鋼的碳當量較高(Ceq=0.713),焊接性能較差。另外該專利沒有提供低溫韌性,但其較高的碳含量和硅含量表明其低溫韌性也較差。公開號為CN101041879A所公開的專利《熱軋超高強度馬氏體鋼及其制造方法》,提供了一種利用熱軋生產(chǎn)屈服強度為860MPa熱軋卷板的方法,但這種高強度鋼是通過大功率的卷取機在熱軋后采用超低溫卷取來生產(chǎn)的,且只能生產(chǎn)厚度為1—4mm的熱軋卷板??梢钥闯觯屑夹g(shù)中利用熱軋及軋后離線熱處理的方法生產(chǎn)800MPa高強度鋼,生產(chǎn)成本較高;采用較高碳、高硅和高錳的合金設(shè)計獲得的800MPa級鋼板,韌性和焊接性能較差;而利用超低溫卷取的方法來生產(chǎn)或薄規(guī)格熱軋卷板,則需要大功率卷取機且只能生產(chǎn)薄規(guī)格卷板。因此需要一種利用熱軋方法生產(chǎn)具有良好韌性和焊接性能的800MPa級高強度鋼板的方法。
技術(shù)實現(xiàn)要素:本發(fā)明的目的在于克服上述問題和不足而提供一種屈服強度為800MPa級熱軋高強度鋼及其生產(chǎn)方法,該高強度鋼不僅具有較高的屈服強度,而且具有較高的塑性、韌性和較好的焊接性能;采用軋后快冷至250~150℃并緩慢冷卻至室溫的工藝,取消了軋后離線熱處理,降低了生產(chǎn)成本。本發(fā)明是這樣實現(xiàn)的:該屈服強度800MPa級熱軋高強度鋼板的成分按重量百分比計如下:C:0.04%~0.07%,Si:0.20%~0.30%,Mn:1.65%~1.85%,P:0~0.015%,S:0~0.003%,Ni:0.25%~0.35%,Cr:0.20%~0.30%,Cu:0.20%~0.30%,Mo:0.20%~0.30%,Nb:0.05%~0.07%,Ti:0.010%~0.020%,Als:0.03%~0.06%其余為Fe和不可避免的雜質(zhì)。本發(fā)明采用低C和低Si并添加Ni、Cr、Mo、Cu、Nb、Ti的合金設(shè)計,顯著地降低了鋼的碳當量,不僅有利于低溫韌性,并保證鋼板具有較好的焊接性能和低溫韌性。本發(fā)明成分設(shè)計理由如下:C:在鋼中形成間隙固溶體,起固溶強化作用,能顯著地提高鋼的強度且成本低廉。但碳含量過高,對低溫韌性和焊接性能不利。本發(fā)明中碳含量為0.04%~0.07%。Si:在煉鋼時為脫氧元素,在鋼中起固溶強化作用,能顯著地提高鋼的強度,但加入過多會損害鋼的延伸率、韌性和焊接性能,本發(fā)明的硅含量為0.20%~0.30%。Mn:提高鋼的淬透性,降低鋼的轉(zhuǎn)變溫度,同時具有固溶強化作用。但錳含量過多時一方面會在鑄坯心部產(chǎn)生偏析,影響熱軋后組織的均勻性,對低溫韌性不利,另一方面會使馬氏體轉(zhuǎn)變溫度下降,導致室溫組織中有一定的殘余奧氏體,影響鋼的強度。由于鋼中錳含量較高時,會加重鑄坯心部的偏析和疏松。本發(fā)明中的錳含量為1.65%~1.85%。P:作為鋼中的有害元素,對鋼的延伸率、低溫沖擊韌性和焊接性能均有損害,其含量應(yīng)盡可能控制在較低水平。因此本發(fā)明中P的含量為≤0.015%。S:作為鋼中的有害元素,對鋼的低溫韌性有很大的損害。硫在鋼中與錳形成硫化錳夾雜,不僅影響鋼的韌性、延伸率、Z向性能、焊接性能,而且還會影響石油天然氣管線用鋼的抗氫致裂紋(HIC)性能。其含量應(yīng)盡可能控制在較低水平。因此本發(fā)明中S的含量為≤0.003%。Cr:增加鋼的淬透性,提高鋼的強度,但Cr含量過高,鋼中容易形成多種含Cr的碳化物,雖然鋼的強度和硬度提高,卻使鋼的韌性下降。因此本發(fā)明中Cr的含量為0.20%~0.30%。Ni:提高淬透性和降低冷脆轉(zhuǎn)變溫度。但Ni含量過高,不僅使合金成本增加,而且會降低馬氏體轉(zhuǎn)變溫度、增加孿晶馬氏體的比例而不利于鋼的韌性。因此本發(fā)明中Ni的含量為0.25%~0.35%。Cu:是鋼中的一種耐蝕元素,并且在鋼中能起到固溶強化作用。但為防止其在鋼中引起熱脆,其含量不應(yīng)太高,并加入一定的鎳。本發(fā)明中Cu的含量為0.20%~0.30%。Mo:在鋼中推遲先共析鐵素體轉(zhuǎn)變,增加鋼的淬透性,細化晶粒,提高鋼的強度和韌性。本發(fā)明中Mo的含量為0.20%~0.30%。Nb:鋼中的Nb(固溶Nb或應(yīng)變誘導析出Nb)會顯著地抑制奧氏體的再結(jié)晶,提高奧氏體的再結(jié)晶溫度,使熱軋在再結(jié)晶溫度區(qū)間和未再結(jié)晶溫度區(qū)間兩個溫度段進行軋制,通過控制軋制細化鋼的顯微組織。本發(fā)明中改為Nb含量為0.05%~0.07%。Ti:與鋼中的C、N形成碳化物、氮化物或碳氮化物,在再加熱和焊接預(yù)熱時抑制奧氏體晶粒的長大,細化晶粒,顯著提高鋼板強度、韌性和焊接性能。由于鈦與鋼中氮的親和力較強,在鋼中容易形成氮化鈦,因此鈦還有固氮的作用,消除鋼中的自由氮。但較高的鈦含量,會在鋼中形成粗大的氮化鈦粒狀,影響鋼的強度和韌性。因此本發(fā)明中Ti的含量為0.010%~0.020%。本發(fā)明屈服強度800MPa級熱軋高強度鋼生產(chǎn)方法包括以下步驟:冶煉→連鑄→再加熱→粗軋→待溫→精軋→冷卻。其特征在于:鑄坯再加熱溫度為1200~1250℃,促進鋼中Nb、V的碳化物的充分溶解,部分溶解的含Ti碳化物能有效抑制奧氏體晶粒的長大。在奧氏體再結(jié)晶的溫度范圍進行粗軋,粗軋終軋溫度為1010~980℃,奧氏體晶粒通過再結(jié)晶逐道次細化;粗軋結(jié)束后待溫至930~950℃溫度區(qū)間內(nèi)進行精軋,精軋的終軋溫度為830~805℃,在奧氏體的未再結(jié)晶溫度~Ar3的溫度范圍進行精軋,奧氏體雖不發(fā)生再結(jié)晶,但其形狀變?yōu)轱灎?,其?nèi)部存在大量的變形帶,促進了相變后組織細化;軋后冷卻分為兩個階段冷卻:1)第一階段以大于20℃/s的冷速淬火冷卻至300~150℃,獲得寬度約為80~240nm的細小的馬氏體板條;2)第二階段以<30℃/h的冷速緩慢冷卻至室溫,在使馬氏體產(chǎn)生的同時對相變后的馬氏體進行自回火。本發(fā)明的基本思路:采用低C和低Si并添加Ni、Cr、Mo、Cu、Nb、Ti的合金設(shè)計,采用奧氏體再結(jié)晶和未再結(jié)晶兩階段軋制、軋后快速冷卻至Ms點以下并緩冷之室溫的工藝,生產(chǎn)出屈服強度為800MPa級并具有良好低溫韌性和焊接性能的高強度鋼。本發(fā)明技術(shù)方案的有益效果在于:采用熱機械軋制+直接淬火+自回火技術(shù),不需要離線淬火和或回火,簡化了生產(chǎn)工藝,降低了鋼的生產(chǎn)成本;采用低C設(shè)計和TMCP工藝,具有較好的低溫韌性;碳當量降低至0.51以下,焊接性能提高。從實施效果看,本發(fā)明的高強度鋼板屈服強度為800~875MPa,抗拉強度為960~1060MPa,延伸率為19~22%,-20℃沖擊功為60~90J。附圖說明圖1為本發(fā)明實施例1鋼板的顯微組織。圖2為本發(fā)明實施例2鋼板的顯微組織。圖3為本發(fā)明實施例3鋼板的顯微組織。圖4為本發(fā)明實施例4鋼板的顯微組織。圖5為本發(fā)明實施例5鋼板的顯微組織。圖6為本發(fā)明實施例6鋼板的顯微組織。具體實施方式下面通過實施例對本發(fā)明作進一步的說明。本發(fā)明實施例根據(jù)技術(shù)方案的組分配比,進行冶煉與軋制。本發(fā)明實施例鋼的化學成分見表1。本發(fā)明實施例鋼的主要工藝參數(shù)見表2。本發(fā)明實施例鋼的力學性能見表3。表1實施例的化學成分(%)表2實施例鋼的主要工藝參數(shù)表3實施例鋼的力學性能