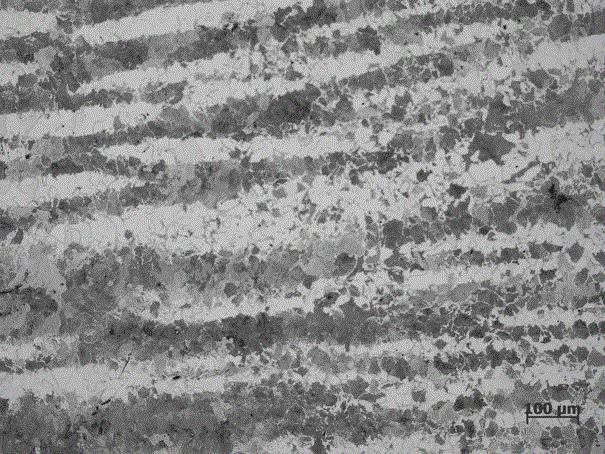
本發明屬于特種鋼板制造領域,具體涉及一種厚度185mm保高溫抗拉強度鋼板及其制造方法,用于鍋爐筒體、封頭的制備。
背景技術:
:SA299GrB鋼板被廣泛用于制造鍋爐筒體、封頭設備。目前我國經濟高速發展,電力需求旺盛,對此,鍋爐用鋼板的需求量較大。這種鋼板需要在高溫、高壓環境中服役,工作條件惡劣,因此要求具有較高的強度,尤其是高溫抗拉強度以及與之匹配的良好的韌性。文獻1(《電焊機》:2010年,40卷第二期,國產SA299特厚板性能試驗研究)涉及到一種國產SA299鋼板,厚度178mm,雖然厚度較大,但該鋼種370℃高溫拉伸不能滿足ASME要求;文獻2(《寬厚板》:2013年,19卷第一期,舞鋼SA299GrA大厚度鍋爐汽包用鋼板的研制開發)研發了一種SA299GrA鋼板,厚度165mm,但鋼中Mo元素含量較高,Mo會導致焊縫熱影響區發生石墨化傾向,惡化性能。目前,根據文獻資料記載,此類鋼種主要存在如下技術難題:1)ASMESA299/SA299M標準對該類鋼板性能強制性要求部分僅為常溫拉伸性能,產品性能指標不高,并不能很好的滿足實際要求;2)目前國產180mm以上厚度規格的該種鋼板SA299GrB尚未見文獻報道,180mm以上規格SA299GrB鋼板現在成為大型鍋爐等裝備制造業發展的限制性環節;3)目前文獻及實物鋼板的高溫(350℃-375℃)抗拉強度,尤其是心部1/2處高溫抗拉強度較低;4)該鋼板,尤其是厚度大于100mm的鋼板,化學成分設計中往往額外添加一定的Mo含量。鍋爐用鋼板是鍋爐制造的核心材料,其厚度直接限制了鍋爐裝備大型化發展的趨勢;鋼板長時間在高溫下使用,較低的高溫抗拉強度或不穩定的高溫抗拉強度,存在一定的安全隱患,且給鍋爐產品設計人員帶來諸多制約;鍋爐在長期高溫使用過程中,Mo鋼在高溫高壓條件下,焊縫熱影響區容易發生石墨化傾向,惡化設備安全性。技術實現要素:本發明基于SA299GrB鋼板使用的特殊性,開發了一種大厚度鋼板,公稱厚度可達185mm;其常溫抗拉強度為550-690MPa;A50延伸率≥19%;0℃橫向沖擊功≥41J;參考《ASME鍋爐及壓力容器規范國際性規范》中SA299鋼種375℃高溫抗拉強度要求517MPa,并在此基礎上提高20MPa,即375℃高溫抗拉強度≥537MPa;鋼板厚度方向Z向性能≥25%;鋼中不另外添加Mo元素,采用Cu等元素進行合金化,保證鋼板強度等性能。本發明解決上述問題所采用的技術方案為:一種大厚度保高溫抗拉強度鋼板SA299GrB,該鋼板厚度可達185mm,化學成分在ASMESA299/299M標準并結合ASMESA20/20M標準的基礎上作進一步改進,按質量百分比計為C:0.23~0.26%,Si:0.15~0.40%,Mn:1.40~1.50%,P:≤0.008%,S:≤0.003%,Ni:0.20~0.30%,Cr:0.20~0.30%,Mo:≤0.06%,Cu:0.20~0.30%,V:≤0.001%,Nb:≤0.020%,Sb:≤0.003%,Sn:≤0.010%,As:≤0.012%,H:≤0.0002%,O:≤0.0020%,N:≤0.0120%,Alt:0.020~0.050%,余量為Fe及不可避免的雜質元素。本發明的185mm厚度鋼板,其常溫抗拉強度550-690MPa,375℃高溫抗拉強度≥537MPa,心部0℃橫向夏比V型缺口沖擊功≥41J,鋼板厚度方向Z向性能≥25%,采用Cu、Cr等元素作為提供鋼板抗拉強度的強化元素,而不額外添加Mo元素。本發明鋼板化學成分的設計原理是C能夠顯著提高鋼板的常溫強度和高溫強度,但是對塑性和韌性有不利影響;Si主要作為煉鋼時的還原劑和脫氧劑使用,有一定的固溶強化作用,但含量過高會導致鋼的低溫韌性降低,且影響鋼板涂覆性能,所以Si控制在0.15~0.4%;Mn通過固溶強化提高鋼的強度,對鋼板韌性也是有利的元素;Cr能提高鋼的強度和回火穩定性,強烈抑制鋼板石墨化趨勢,但同時會降低鋼的韌性和塑性;大厚度鋼板連續空冷階段,鋼板心部冷卻速率較慢,Cu在鋼板中連續析出和轉變,相界面處析出,強化鐵素體,從而提高鋼板強度。Cr+Cu復合強化,提高了鋼板,尤其是心部的高溫穩定性,彌補了Mo元素缺失導致的不足。Ni能夠提高鋼的韌性和塑性,同時也增加強度,本發明的Ni控制在0.20~0.30%之間;Mo存在于固溶體和碳化物中,可提高回火穩定性,但鍋爐在長期高溫使用過程中,Mo鋼焊縫熱影響區容易發生石墨化傾向,雖然Mo能夠顯著提高大厚度鋼板的性能,但是作為鍋爐材料時,容易導致鍋爐設備惡化。本申請中的Mo是作為殘余元素存在,不添加Mo元素;P、S是有害元素,P增加鋼的脆性,降低鋼的焊接性能,降低塑性和冷加工性能,S降低鋼的延展性和韌性,在熱加工過程中造成裂紋,故盡量減少P、S含量;Nb形成Nb(N,C)析出相提高再結晶溫度,細化奧氏體晶粒,能有效提高鋼的強度和韌性;Sb、Sn、As、Pb、Bi等是有害元素,容易在晶界偏析,降低鋼的抗回火脆化性能,應盡量去除,控制在較低含量。O,N氣體元素應盡量降低,提高鋼的純凈度,降低夾雜物含量;H增加鋼的氫脆傾向,應盡量降低其含量;Alt與氧有很強的親和力主要作為脫氧劑加入,Alt與N形成的AlN可細化奧氏體晶粒。本發明的另一目的是提供上述大厚度保高溫抗拉強度鋼板SA299GrB的制造方法,主要步驟如下(1)冶煉:采用優質廢鋼,經電爐EAF冶煉:出鋼溫度1610~1650℃,轉爐出鋼P≤0.0050%;LF精煉:白渣保持時間不小于25min,總精煉時間不小于80min,鋼水S≤0.003%時扒渣;VD真空脫氣精煉:真空度≤67Pa,真空保持時間在20min以上后破空;模鑄,制造出滿足化學成分要求鋼錠,鋼錠大頭厚度978mm,小頭厚度780mm,確保軋成鋼板后滿足3倍壓縮比;對鑄坯加罩緩冷72小時以上,加罩是為了進一步降低鋼坯中的H含量,緩冷結束后對鑄坯表面帶溫清理;確保鋼錠坯料表面無裂紋等影響鋼板表面質量的缺陷存在。(2)軋制:創新性的采用雙維度軋制開坯-全縱向軋制成材的兩火生產工藝,該工藝主要特點為開坯階段展寬與縱向軋制交替進行;成材階段初始采用大壓下量軋制,前3道次壓下量≥30%,使軋制力滲透鋼板心部,提高鋼板心部性能,具體工藝如下:A開坯:鋼錠開坯軋制加熱在均熱爐中進行,利用溫控系統采用分段加熱方式:總加熱時間34h以上;預熱段溫度為室溫~800℃,預熱段升溫時間不低于7h;悶爐保溫5h±30min;再緩慢加熱至1250℃,升溫時間6h±30min,均熱溫度1150~1250℃,均熱時間不低于16h,采用長時間加熱的目的促進鋼中化學成分的均勻性,減輕心部偏析情況,提高鋼板心部性能;開軋溫度為1050~1100℃,首道次展寬軋制壓下量10%以上,隨后采用縱軋方式,再接著展寬軋制,如此循環。該軋制模式有利于打斷原始模鑄形成的粗大的柱狀晶,提高鋼板心部的致密性,細化心部晶粒度;軋制完成后,加罩堆緩冷,緩冷48小時以上,鋼板軋后緩冷的目的是進一步降低鋼板中殘留的H含量,減弱H的危害;B軋制成材:坯料采用常規加熱方式,加熱總時間400±20min,控制加熱時間,防止晶粒異常長大;出爐后對鋼坯進行粗軋與精軋的兩階段軋制,充分利用微合金元素的釘扎作用;粗軋開軋溫度為1050~1100℃,前3道次單道次壓下量≥30%,采用大壓下量的目的是使軋制力滲透至鋼板心部,提高鋼板心部的致密性,細化心部晶粒度;終軋溫度850~900℃,軋制完成后,采用水冷加速冷卻至600±20℃,細化鐵素體晶粒;鋼板在表面溫度100~200℃時下線;(3)熱處理:鋼板在臺車爐中正火熱處理,隨爐升溫,正火保溫溫度為860~890℃,保溫時間為1.5~3min/mm,采用隨爐升溫方式,采用LQL加熱曲線:第一階段室溫-650℃,升溫速率70±5℃/h,第二階段650℃-830℃,升溫速率100±5℃/h;第三階段850℃-目標溫度,升溫速率50±5℃/h,進入保溫階段。保證①在最合理的時間鋼板完全奧氏體化②鋼板整體溫度均勻。隨后空冷。采用LQL加熱曲線能避免鋼板表面產生熱應力(鋼板內外膨脹系數不一致),因為該熱應力有可能導致鋼板內部產生微裂紋缺陷,降低鋼板性能。該熱處理工藝目的是通過正火消除在控冷過程中產生的少量貝氏體與馬氏體,獲得理想的鐵素體+珠光體的組織與均勻的性能,從而提高了沖擊韌性,即獲得鋼板成品。與現有技術相比,本發明的特點在于:本發明SA299GrB鋼板,厚度規格達到了185mm;不添加Mo,其含量屬于殘留;通過Cu-Cr復合強化,提高鋼板常溫強度;而且心部375℃高溫抗拉強度≥537MPa;0℃橫向夏比V型缺口沖擊功≥41J;鋼板全厚度方向Z向性能≥25%。與現有鋼板制造工藝相比,本發明鋼板的制造方法具有如下特點:1)利用LF+VD精煉工藝,采用鋼錠生產鑄坯,鋼錠大頭厚度978mm,小頭厚度780mm,保證軋成鋼板后有3倍以上壓縮比;2)采用多級加熱方式,盡量消除鋼錠表面和心部之間的溫差;采用雙維度軋制開坯-全縱向軋制成材的兩火生產工藝,提高鋼板心部的致密性;3)利用臺車爐加熱,隨爐加熱,采用獨特的LQL加熱曲線。為了本申請描述的鋼板,本發明優化了鋼板的化學組分,精選廢鋼,嚴控澆鑄工藝參數,所生產的鋼錠具有低的中心偏析和中心疏松,內部質量良好。鋼板軋制前對鋼錠再加熱,且采用多階段加熱方式,對于大厚度的鋼錠而言,表面和心部的溫差較大,溫度隨厚度呈梯度式變化,這也導致鋼錠的晶相組織在厚度上存在差異,難以保證后期金屬材料表里性能的均一,尤其是心部性能難以控制。采用多級加熱方式,根據鋼材的成分設計特點設置相應各階段的加熱溫度和保溫時間,盡量消除鋼錠表面和心部之間的溫差,保證最終鋼板整體的性能穩定。另外,上述階段加熱方式是隨之進行的高溫大壓下軋制的前提,都是為了消除表里差異、獲得組織均勻的鋼板,高溫大壓下充分保證軋制力能夠滲透到坯料心部,確保厚鋼板心部組織的細化,提高心部性能。本發明鋼板的熱處理工藝采用采用獨特的LQL加熱曲線;鋼板以正火+空冷工藝熱處理,而非采用噴霧冷卻或水冷等加速冷卻方式,可以保證鋼板為鐵素體+珠光體組織,有利于后續使用的焊接性能;另外,鋼板表面硬度更均勻,在彎曲成筒或制作封頭熱成形過程中不容易產生加工裂紋。附圖說明圖1為本發明實施例1的鋼板1/4厚度的金相組織;圖2為本發明實施例1的鋼板1/2厚度的金相組織。具體實施方式以下結合附圖實施例對本發明作進一步詳細描述。實施例1本實施例的185mm厚度汽包板,其熔煉化學成分按質量百分比計為:C:0.26%,Si:0.30%,Mn:1.45%,P:0.006%,S:0.002%,Ni:0.25%,Cr:0.25%,Cu:0.25%,Mo:0.05%,Nb:0.0156%,Sb:0.0009%,Sn:0.002%,As:0.0042%,H:0.00009%,Alt:0.033%,余量為Fe及不可避免的雜質元素。該鋼板的制造工藝為:1)冶煉:采用優質廢鋼,電爐EAF冶煉;LF精煉;VD真空脫氣精煉;模鑄,制造出滿足化學成分要求鋼錠,鋼錠大頭厚度978mm,小頭厚度780mm,保證軋成鋼板后有3倍壓縮比;對鑄坯加罩緩冷96小時,進一步降低鋼坯的H含量,緩冷結束后對鑄坯表面帶溫清理,確保鋼錠坯料表面無裂紋等影響鋼板表面質量的缺陷存在。2)軋鋼:鋼錠加熱在均熱爐中,利用溫控系統采用分段加熱方式:總加熱時間36h。開坯后的板坯在連續爐加熱,總加熱時間410min;采用雙維度軋制開坯-全縱向軋制成材的兩火生產工藝,軋板厚度187.3mm。軋制完成后,鋼板在表面溫度450℃時下線,加罩堆緩冷,緩冷52小時,鋼板軋后緩冷的目的是充分降低鋼板中殘留的H含量,減弱H的危害。3)熱處理:利用臺車爐加熱,隨爐加熱,采用獨特的LQL加熱曲線;正火加熱溫度為870℃,正火保溫時間為1.7min/mm,出爐后在冷床空冷至180℃下線,即獲得鋼板成品。性能檢驗:性能檢驗包括交貨態鋼板性能、交貨態+回火態鋼板性能、交貨態+模擬焊后熱處理狀態鋼板性能,具體交貨態+回火工藝、交貨態+模擬焊后熱處理工藝如下:交貨態+回火工藝:樣坯從鋼板上取下,試樣大小為555mm(軋制方向)*600mm(寬度方向)*185mm(厚度方向),在小爐子中640℃保溫10小時,即實驗室模擬回火熱處理,然后再進行力學性能檢驗。交貨態+模擬焊后熱處理工藝:樣坯從鋼板上取下,試樣大小為555mm(軋制方向)*600mm(寬度方向)*185mm(厚度方向);在小爐子中585℃保溫14小時,模擬鋼板焊后熱處理過程,然后再進行力學性能檢驗。檢驗證明,本實施例中的鋼板試樣力學性能溫度且均勻,具體力學性能見表1、表2。交貨態鋼板金相組織見圖1。表1鋼板的常溫橫向、Z向拉伸、0℃沖擊性能表2鋼板的高溫拉伸性能實施例2本實施例的185mm厚度汽包板,其化學成分按質量百分比計為:C:0.27%,Si:0.32%,Mn:1.47%,P:0.009%,S:0.002%,Ni:0.27%,Cr:0.25%,Cu:0.26%,Mo:0.04%,Nb:0.0156%,Sb:0.0009%,Sn:0.002%,As:0.0042%,H:0.00010%,Alt:0.033%,余量為Fe及不可避免的雜質元素。該鋼板的制造工藝為:1)冶煉:采用優質廢鋼,電爐EAF冶煉:出鋼溫度1623℃;LF精煉:白渣保持時間30min,總精煉時間90min;VD真空脫氣精煉:真空保持時間在25min;模鑄,制造出滿足化學成分要求鋼錠,鋼錠大頭厚度978mm,小頭厚度780mm,保證軋成鋼板后有3倍壓縮比;對鑄坯加罩緩冷102小時,進一步降低鋼坯的H含量,緩冷結束后對鑄坯表面帶溫清理,確保鋼錠坯料表面無裂紋等影響鋼板表面質量的缺陷存在。2)軋鋼:鋼錠加熱在均熱爐中,利用溫控系統采用分段加熱方式:總加熱時間36h。開坯后的板坯在連續爐加熱,總加熱時間423min;采用雙維度軋制開坯-全縱向軋制成材的兩火生產工藝,軋板厚度187.0mm。軋制完成后,鋼板在表面溫度440℃時下線,加罩堆緩冷,緩冷60小時,鋼板軋后緩冷的目的是充分降低鋼板中殘留的H含量,減弱H的危害。3)熱處理:利用臺車爐加熱,隨爐加熱,采用獨特的LQL加熱曲線;正火加熱溫度為870℃,正火保溫時間為1.7min/mm,出爐后在冷床空冷至170℃下線,即獲得鋼板成品。性能檢驗:性能檢驗包括交貨態鋼板性能、交貨態+模擬熱成型熱處理+模擬熱成型熱處理+模擬焊后熱處理狀態鋼板性能,具體交貨態+模擬熱成型熱處理+模擬熱成型熱處理+模擬焊后熱處理工藝如下:交貨態+模擬熱成型熱處理+模擬熱成型熱處理+模擬焊后熱處理工藝:樣坯從鋼板上取下,試樣大小為555mm(軋制方向)*600mm(寬度方向)*185mm(厚度方向),在實驗室小爐子中做熱處理:1、930±10℃,保溫2.5h,空冷2、930±10℃,保溫2.5h,空冷3、610±5℃,保溫8h,300℃以上升、降溫速度≤78℃/h,300℃以下空冷。具體力學性能見表3、表4。表3鋼板的常溫橫向、Z向拉伸、0℃沖擊性能表4鋼板的高溫拉伸性能取樣位置溫度屈服強度,MPa抗拉強度,MPa375℃≥202≥537正火1/2板厚375℃281548正火+模擬熱成型+模擬熱成型+模擬焊后1/2板厚375℃276538實施例3本實施例公稱厚度185mm厚度汽包板,其化學成分按質量百分比計為:C:0.25%,Si:0.25%,Mn:1.43%,P:0.010%,S:0.002%,Ni:0.29%,Cr:0.28%,Cu:0.20%,Mo:0.03%,Nb:0.0170%,Sb:0.0007%,Sn:0.002%,As:0.0040%,H:0.00009%,Alt:0.030%,余量為Fe及不可避免的雜質元素。該鋼板的制造工藝為:1)冶煉:采用優質廢鋼,電爐EAF冶煉;LF精煉;VD真空脫氣精煉;模鑄,制造出滿足化學成分要求鋼錠,鋼錠大頭厚度978mm,小頭厚度780mm,保證軋成鋼板后有3倍壓縮比;對鑄坯加罩緩冷110小時,進一步降低鋼坯的H含量,緩冷結束后對鑄坯表面帶溫清理,確保鋼錠坯料表面無裂紋等影響鋼板表面質量的缺陷存在。2)軋鋼:鋼錠加熱在均熱爐中,利用溫控系統采用分段加熱方式:總加熱時間36h。開坯后的板坯在連續爐加熱,總加熱時間426min;采用雙維度軋制開坯-全縱向軋制成材的兩火生產工藝,軋板厚度187.8mm。軋制完成后,鋼板在表面溫度400℃時下線,加罩堆緩冷,緩冷60小時,鋼板軋后緩冷的目的是充分降低鋼板中殘留的H含量,減弱H的危害。3)熱處理:利用臺車爐加熱,隨爐加熱,采用獨特的LQL加熱曲線;正火加熱溫度為870℃,正火保溫時間為1.7min/mm,出爐后在冷床空冷至100℃下線,即獲得鋼板成品。性能檢驗:性能檢驗包括交貨態鋼板性能系列溫度沖擊、系列高溫拉伸遷都。具體力學性能見表5、表6。表5鋼板系列溫度沖擊性能表6鋼板的高溫拉伸性能180mm以上規格大厚度鋼板力學性能中拉伸性能、沖擊韌性性能難以平衡,尤其是外加了心部高溫拉伸性能,使得鋼板制造難度相當大。作為鍋爐用鋼板,通過實例,本發明鋼板性能不僅滿足正火交貨狀態的性能,試樣經過回火、模擬熱成型熱處理、模擬焊后熱處理以后的性能也能達到交貨狀態的性能要求,尤其是心部高溫拉伸,完全滿足要求,且有一定富余量。本發明生產的大厚度鍋爐鋼板的Z向性能達到了斷面收縮率35%以上。結果表明本發明中利用鋼錠生產的鑄坯,對應的大厚度鍋爐鋼板不僅具有高的抗層狀撕裂能力而且具有高的致密度,從而保證了鋼板對心部性能的苛刻要求,從側面也呼應了該鋼板高溫拉伸性能的優異性。當前第1頁1 2 3