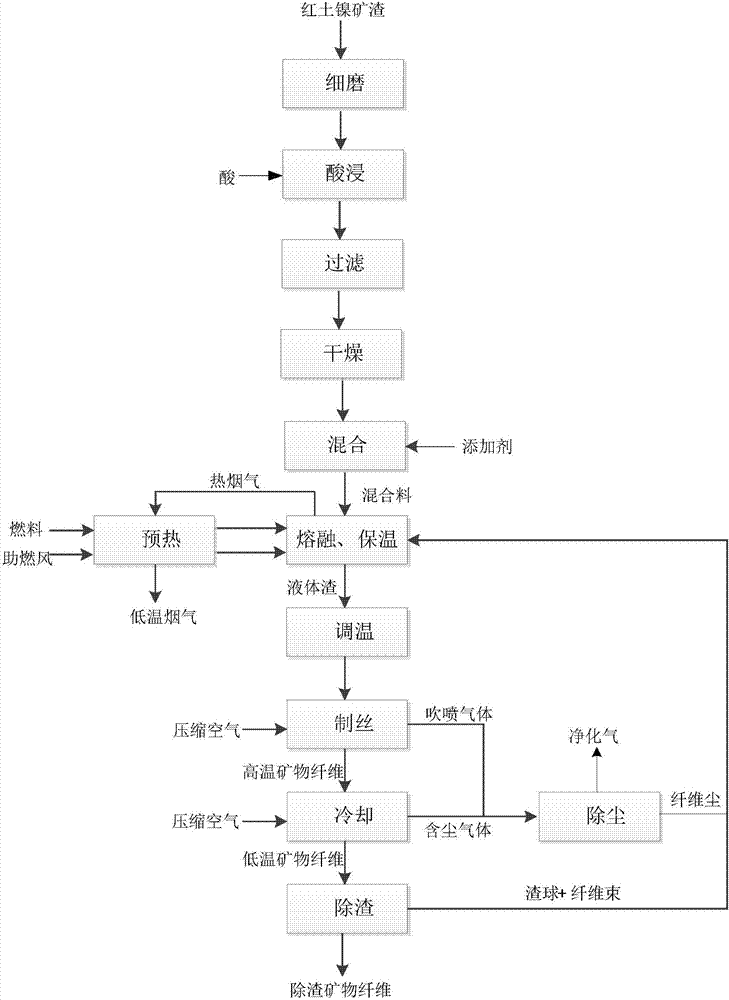
本發(fā)明屬于廢棄物資源領(lǐng)域,具體地,涉及一種由紅土鎳礦渣制備礦物纖維的系統(tǒng)及方法。
背景技術(shù):
:礦物纖維是一種無(wú)機(jī)纖維,具有保溫、隔熱、阻燃等特點(diǎn),是一種優(yōu)良的建筑材料。天然的礦物纖維儲(chǔ)量極少,目前絕大多數(shù)的礦物纖維是采用不同的天然礦物通過(guò)配比調(diào)整化學(xué)成分生產(chǎn)的。開(kāi)采天然礦物需要付出開(kāi)采成本和環(huán)境破壞等代價(jià)。紅土鎳礦渣是當(dāng)下一種大宗的廢棄物資源,目前由于技術(shù)所限,絕大部分的紅土鎳礦渣堆棄在尾渣壩內(nèi)而未得到利用。紅土鎳礦的主要成分為mgo、sio2、cao和al2o3,紅土鎳礦渣為紅土鎳礦提取fe、ni、co后得到的廢渣,其mgo含量較高。礦物纖維生產(chǎn)中要求酸度系數(shù)(sio2+al2o3)/(cao+mgo)=1.3-1.5,同時(shí)保證酸度系數(shù)(sio2+al2o3)/mgo≥1.5。紅土鎳礦渣的化學(xué)成分中mgo含量過(guò)高,需要進(jìn)行除鎂操作,除去mgo后的紅土鎳礦渣才可以用來(lái)來(lái)代替天然礦物生產(chǎn)礦物纖維。纖維塵、渣球和纖維束是在制備礦物纖維過(guò)程中產(chǎn)生的廢渣,現(xiàn)有工藝并未考慮回收纖維塵、渣球和纖維束的問(wèn)題,不僅造成了浪費(fèi),還對(duì)環(huán)境造成了污染。技術(shù)實(shí)現(xiàn)要素:針對(duì)現(xiàn)有技術(shù)的不足,本發(fā)明首先提供了一種由紅土鎳礦渣制備礦物纖維的系統(tǒng),包括:酸浸設(shè)備,具有紅土鎳礦渣入口、酸入口和除鎂礦渣出口;過(guò)濾設(shè)備,具有除鎂礦渣入口和過(guò)濾礦渣出口,所述除鎂礦渣入口與所述酸浸設(shè)備的除鎂礦渣出口相連;烘干設(shè)備,具有過(guò)濾礦渣入口和烘干礦渣出口,所述過(guò)濾礦渣入口與所述過(guò)濾設(shè)備的過(guò)濾礦渣出口相連;混合設(shè)備,具有烘干礦渣入口、添加劑入口和混合料出口,所述烘干礦渣入口與所述烘干設(shè)備的烘干礦渣出口相連,蓄熱式熔化爐,包括熔化爐和蓄熱爐,所述熔化爐具有混合料入口、渣料入口、高溫液態(tài)渣出口和高溫?zé)煔獬隹冢鲂顭釥t具有燃料入口和助燃風(fēng)入口,所述混合料入口與所述混合設(shè)備的混合料出口相連;中間罐,具有高溫液態(tài)渣入口和調(diào)溫液態(tài)渣出口,所述高溫液態(tài)渣入口與所述蓄熱式熔化爐的高溫液態(tài)渣出口相連;制絲設(shè)備,具有調(diào)溫液態(tài)渣入口和高溫礦物纖維出口,所述調(diào)溫液態(tài)渣入口與所述中間罐的調(diào)溫液態(tài)渣出口相連;冷卻設(shè)備,具有高溫礦物纖維入口、壓縮空氣入口、低溫礦物纖維出口和含塵氣體出口,所述高溫礦物纖維入口與所述制絲設(shè)備的高溫礦物纖維出口相連;除塵設(shè)備,具有含塵氣體入口、凈化氣出口和纖維塵出口,所述含塵氣體入口與所述冷卻設(shè)備的含塵氣體出口相連,所述纖維塵出口與所述蓄熱式熔化爐的渣料入口相連。進(jìn)一步地,所述系統(tǒng)還包括除渣設(shè)備,所述除渣設(shè)備具有低溫礦物纖維入口、除渣礦物纖維出口和渣料出口,所述低溫礦物纖維入口與所述冷卻設(shè)備的低溫礦物纖維出口相連,所述渣料出口與所述蓄熱式熔化爐的渣料入口相連。進(jìn)一步地,所述制絲設(shè)備還具有壓縮空氣入口和吹噴氣體出口,所述吹噴氣體出口與所述除塵設(shè)備的含塵氣體入口相連。進(jìn)一步地,所述蓄熱式熔化爐的蓄熱爐還具有高溫?zé)煔馊肟诤偷蜏責(zé)煔獬隹冢龈邷責(zé)煔馊肟谂c所述熔化爐的高溫?zé)煔獬隹谙噙B。進(jìn)一步地,所述系統(tǒng)還包括細(xì)磨機(jī),所述細(xì)磨機(jī)具有進(jìn)料口和出料口,所述出料口與所述酸浸設(shè)備的紅土鎳礦渣入口相連。本發(fā)明還提供了一種利用上述系統(tǒng)制備礦物纖維的方法,包括如下步驟:準(zhǔn)備紅土鎳礦渣和添加劑,所述添加劑包括粉煤灰和/或生石灰;將所述紅土鎳礦渣送入所述酸浸設(shè)備中脫鎂,獲得除鎂礦渣;將所述除鎂礦渣依次送入所述過(guò)濾設(shè)備和所述烘干設(shè)備進(jìn)行過(guò)濾和烘干,獲得烘干礦渣;將所述烘干礦渣送入所述混合設(shè)備與所述添加劑混合均勻,獲得混合料;將所述混合料送入所述蓄熱式熔化爐內(nèi)熔融,并保溫,得到內(nèi)部成分均一的液態(tài)渣;將所述液態(tài)渣送入所述中間罐調(diào)節(jié)溫度;將調(diào)溫后的液態(tài)渣送入所述制絲設(shè)備中制絲,得到高溫礦物纖維;將所述高溫礦物纖維送入所述冷卻設(shè)備,用壓縮空氣進(jìn)行冷卻,獲得低溫礦物纖維和含塵氣體;將所述含塵氣體送入所述除塵設(shè)備除塵,獲得凈化氣和纖維塵;將所述纖維塵送入所述蓄熱式熔化爐,與所述混合料一起制備所述液態(tài)渣。進(jìn)一步地,除去所述低溫礦物纖維中的渣球和纖維束,將所述渣球和所述纖維束送入所述蓄熱式熔化爐,與所述混合料一起制備所述液態(tài)渣。進(jìn)一步地,采用噴吹制絲法將調(diào)溫后的液體渣制成所述高溫礦物纖維,所述吹噴制絲法采用壓縮空氣進(jìn)行吹噴,將排出的吹噴氣體送入所述除塵設(shè)備中除塵。進(jìn)一步地,所述蓄熱式熔化爐的加熱溫度為1400℃-1800℃。進(jìn)一步地,調(diào)溫后的液態(tài)渣的溫度為1200℃-1500℃。本發(fā)明回收了纖維塵、渣球和纖維束,提高了能源利用率,又解決了環(huán)境污染問(wèn)題。本發(fā)明使用的紅土鎳礦渣成本低廉,而且蓄熱式熔化爐燃料消耗少、節(jié)約能源,因此本發(fā)明制得的礦物纖維的生產(chǎn)成本低。本發(fā)明制得的礦物纖維質(zhì)量好,是一種優(yōu)良的建筑材料。附圖說(shuō)明圖1為本發(fā)明實(shí)施例中的一種由紅土鎳礦渣制備礦物纖維的系統(tǒng)的結(jié)構(gòu)示意圖。圖2為本發(fā)明實(shí)施例中的一由紅土鎳礦渣制備礦物纖維的工藝流程圖。具體實(shí)施方式以下結(jié)合附圖和實(shí)施例,對(duì)本發(fā)明的具體實(shí)施方式進(jìn)行更加詳細(xì)的說(shuō)明,以便能夠更好地理解本發(fā)明的方案以及其各個(gè)方面的優(yōu)點(diǎn)。然而,以下描述的具體實(shí)施方式和實(shí)施例僅是說(shuō)明的目的,而不是對(duì)本發(fā)明的限制。需要說(shuō)明的是,本發(fā)明涉及的所有百分?jǐn)?shù)均為質(zhì)量百分?jǐn)?shù)。本發(fā)明提供的由紅土鎳礦渣制備礦物纖維的系統(tǒng)包括:酸浸設(shè)備,具有紅土鎳礦渣入口、酸入口和除鎂礦渣出口;過(guò)濾設(shè)備,具有除鎂礦渣入口和過(guò)濾礦渣出口,除鎂礦渣入口與酸浸設(shè)備的除鎂礦渣出口相連;烘干設(shè)備,具有過(guò)濾礦渣入口和烘干礦渣出口,過(guò)濾礦渣入口與過(guò)濾設(shè)備的過(guò)濾礦渣出口相連;混合設(shè)備,具有烘干礦渣入口、添加劑入口和混合料出口,烘干礦渣入口與烘干設(shè)備的烘干礦渣出口相連;蓄熱式熔化爐,包括熔化爐和蓄熱爐,熔化爐具有混合料入口、渣料入口、高溫液態(tài)渣出口和高溫?zé)煔獬隹冢顭釥t具有燃料入口和助燃風(fēng)入口,混合料入口與混合設(shè)備的混合料出口相連;中間罐,具有高溫液態(tài)渣入口和調(diào)溫液態(tài)渣出口,高溫液態(tài)渣入口與蓄熱式熔化爐的高溫液態(tài)渣出口相連;制絲設(shè)備,具有調(diào)溫液態(tài)渣入口和高溫礦物纖維出口,調(diào)溫液態(tài)渣入口與中間罐的調(diào)溫液態(tài)渣出口相連;冷卻設(shè)備,具有高溫礦物纖維入口、壓縮空氣入口、低溫礦物纖維出口和含塵氣體出口,高溫礦物纖維入口與制絲設(shè)備的高溫礦物纖維出口相連;除塵設(shè)備,具有含塵氣體入口、凈化氣出口和纖維塵出口,含塵氣體入口與冷卻設(shè)備的含塵氣體出口相連,纖維塵出口與蓄熱式熔化爐的渣料入口相連。本發(fā)明回收了纖維塵,提高了能源利用率,又解決了環(huán)境污染問(wèn)題。本發(fā)明將紅土鎳礦渣脫鎂后,采用蓄熱式熔化爐進(jìn)行熔融,蓄熱式熔化爐采用燃?xì)饧訜帷<t土鎳礦渣中含有金屬氧化物,若采用電爐熔化,由于電爐中的石墨電極的作用,電爐內(nèi)的氣氛是還原性氣氛,會(huì)造成紅土鎳礦渣中的金屬氧化物被還原為單質(zhì)金屬,致使難以獲得礦物纖維或獲得的礦物纖維過(guò)短。而蓄熱式熔化爐的內(nèi)部氣氛為氧化性氣氛,不會(huì)導(dǎo)致金屬氧化物被還原。此外,電爐熔化時(shí)會(huì)預(yù)先形成金屬熔池,靠石墨電極與金屬熔池間起弧發(fā)熱,金屬熔池的存在會(huì)導(dǎo)致在制絲過(guò)程中形成金屬夾雜,影響礦物纖維的生成,而燃?xì)鉅t則不會(huì)產(chǎn)生這些問(wèn)題。在本發(fā)明優(yōu)選的實(shí)施例中,上述系統(tǒng)還可包括除渣設(shè)備,除渣設(shè)備具有低溫礦物纖維入口、除渣礦物纖維出口和渣料出口,低溫礦物纖維入口與冷卻設(shè)備的低溫礦物纖維出口相連,渣料出口與蓄熱式熔化爐的渣料入口相連。除渣設(shè)備排出的渣球和纖維束被送回蓄熱式熔化爐中,與紅土鎳礦渣和添加劑一起制備液態(tài)渣,提高了能源利用率,又解決了環(huán)境污染問(wèn)題。在本發(fā)明優(yōu)選的實(shí)施例中,制絲設(shè)備還具有壓縮空氣入口和吹噴氣體出口,吹噴氣體出口與除塵設(shè)備的含塵氣體入口相連。吹噴氣體里也含有纖維塵,將其送入除塵設(shè)備中回收纖維塵后再排出,能提高能源利用率,減少環(huán)境污染。在本發(fā)明優(yōu)選的實(shí)施例中,蓄熱式熔化爐的蓄熱爐還具有高溫?zé)煔馊肟诤偷蜏責(zé)煔獬隹冢邷責(zé)煔馊肟谂c熔化爐的高溫?zé)煔獬隹谙噙B。將熔化爐排出的高溫?zé)煔庾鳛樾顭釥t的熱源,回收高溫?zé)煔獾臒崃浚軠p小系統(tǒng)的能耗,降低礦物纖維的生產(chǎn)成本。在本發(fā)明優(yōu)選的實(shí)施例中,上述系統(tǒng)還包括細(xì)磨機(jī)。細(xì)磨機(jī)具有進(jìn)料口和出料口,出料口與酸浸設(shè)備的紅土鎳礦渣入口相連。細(xì)磨機(jī)用于將紅土鎳礦渣磨成粉料。紅土鎳礦渣粉料可以直接購(gòu)買(mǎi),也可以自行制備,降低礦物纖維的生產(chǎn)成本。本發(fā)明還提供了一種利用上述系統(tǒng)制備礦物纖維的方法,包括如下步驟:準(zhǔn)備紅土鎳礦渣和添加劑;將所述紅土鎳礦渣送入所述酸浸設(shè)備中脫鎂,獲得除鎂礦渣;將所述除鎂礦渣依次送入所述過(guò)濾設(shè)備和所述烘干設(shè)備進(jìn)行過(guò)濾和烘干,獲得烘干礦渣;將所述烘干礦渣送入所述混合設(shè)備與所述添加劑混合均勻,獲得混合料;將混合料送入蓄熱式熔化爐內(nèi)熔融,并保溫,得到內(nèi)部成分均一的液態(tài)渣;將液態(tài)渣送入中間罐調(diào)節(jié)溫度;將調(diào)溫后的液態(tài)渣送入制絲設(shè)備中制絲,得到高溫礦物纖維;將高溫礦物纖維送入冷卻設(shè)備,用壓縮空氣進(jìn)行冷卻,獲得低溫礦物纖維和含塵氣體;將含塵氣體送入除塵設(shè)備除塵,獲得凈化氣和纖維塵;將纖維塵送入蓄熱式熔化爐,與混合料一起制備液態(tài)渣。本發(fā)明使用紅土鎳礦渣內(nèi)mgo含量過(guò)高,需要進(jìn)行酸浸除鎂操作后才能制備礦物纖維。本發(fā)明采用酸浸法除鎂,使用的酸包括:稀鹽酸或稀硫酸等強(qiáng)酸中的一種,酸浸采用常壓酸浸,酸浸時(shí)間為1-12h,酸浸溫度為30-60℃。除鎂后的紅土鎳礦渣經(jīng)過(guò)過(guò)濾和烘干后與添加劑混合均勻后制備液態(tài)渣。在本發(fā)明優(yōu)選的實(shí)施例中,酸浸除鎂后的紅土鎳礦渣烘干的溫度為105-120℃,時(shí)間為12-24h。本發(fā)明使用的添加劑包括粉煤灰和/或生石灰。往除鎂后的紅土鎳礦渣中加入添加劑的目的是為了使液體渣中的sio2、cao、al2o3和mgo的成分含量處于合理的范圍,提高制得的礦物纖維的質(zhì)量。在本發(fā)明優(yōu)選的實(shí)施例中,液體渣中的sio2的含量為10-70wt%。在本發(fā)明優(yōu)選的實(shí)施例中,液體渣中的cao的含量為0-50wt%。在本發(fā)明優(yōu)選的實(shí)施例中,液體渣中的al2o3的含量為10-60wt%。在本發(fā)明優(yōu)選的實(shí)施例中,液體渣中的mgo的含量為10-50wt%。在本發(fā)明優(yōu)選的實(shí)施例中,液體渣中的na2o、k2o等堿金屬氧化物的總量不大于10wt%。同前所述,可除去低溫礦物纖維中的渣球和纖維束,將渣球和所述纖維束送入蓄熱式熔化爐,與混合料一起制備所述液態(tài)渣。同前所述,可采用噴吹制絲法將調(diào)溫后的液體渣制成高溫礦物纖維,吹噴制絲法采用壓縮空氣進(jìn)行吹噴,將排出的吹噴氣體送入除塵設(shè)備中除塵。在本發(fā)明優(yōu)選的實(shí)施例中,蓄熱式熔化爐的加熱溫度為1400℃-1800℃。此溫度可以處理不同條件的紅土鎳礦渣,且不會(huì)造成熱能浪費(fèi)。在進(jìn)一步優(yōu)選的實(shí)施例中,蓄熱式熔化爐的加熱溫度為1500℃-1600℃。混合料在蓄熱式熔化爐內(nèi)熔融后還需保溫一段時(shí)間,使得熔融后的液體渣內(nèi)部均一。在本發(fā)明優(yōu)選的實(shí)施例中,在上述加熱溫度下,保溫的時(shí)間為20-40min。紅土鎳礦渣混的粒徑越小,熔融的效果越好。在本發(fā)明優(yōu)選的實(shí)施例中,紅土鎳礦渣的粒徑≤60μm。制絲前液態(tài)渣的溫度直接影響制得的礦物纖維的質(zhì)量。在本發(fā)明優(yōu)選的實(shí)施例中,調(diào)整液態(tài)渣的溫度至1200℃-1500℃。本發(fā)明使用的紅土鎳礦渣來(lái)源廣泛、成本低廉,而且蓄熱式熔化爐燃料消耗少、節(jié)約能源,因此本發(fā)明制得的礦物纖維的生產(chǎn)成本低。本發(fā)明制得的礦物纖維的質(zhì)量好。下面參考具體實(shí)施例,對(duì)本發(fā)明進(jìn)行說(shuō)明。下述實(shí)施例中所取工藝條件數(shù)值均為示例性的,其可取數(shù)值范圍如前述
發(fā)明內(nèi)容中所示。下述實(shí)施例所用的檢測(cè)方法均為本行業(yè)常規(guī)的檢測(cè)方法。實(shí)施例1本實(shí)施例采用圖1所示的系統(tǒng)及圖2所示的工藝流程生產(chǎn)礦物纖維板,具體如下:準(zhǔn)備3000kgrkef紅土鎳礦渣、300kg粉煤灰和600kg生石灰。所用紅土鎳礦渣化學(xué)成分如表1所示:表1rkef紅土鎳礦渣主要化學(xué)成分成分feosio2mgocaoal2o3含量11.5148.4220.1712.059.52在細(xì)磨機(jī)1中將紅土鎳礦渣中細(xì)磨至粒徑≤60μm。粉料在酸浸設(shè)備2中經(jīng)過(guò)酸浸后得到脫鎂礦渣,其化學(xué)成分如表2所示:表2脫鎂rkef紅土鎳礦渣主要化學(xué)成分成分feosio2mgocaoal2o3含量6.4163.223.596.2215.52所用酸為10%的稀鹽酸,用量為20噸。采用常壓酸浸的方法,酸浸時(shí)間為10h,酸浸溫度為50℃。將脫鎂后的rkef紅土鎳礦渣依次送入過(guò)濾設(shè)備3和烘干設(shè)備4中,經(jīng)過(guò)過(guò)濾和烘干后獲得烘干礦渣。烘干溫度為120℃,時(shí)間為12h。將烘干礦渣送入混合設(shè)備5與粉煤灰和生石灰混合均勻,獲得混合料。將混合料送入蓄熱式熔化爐6內(nèi),在1500℃的溫度下熔融,然后保溫40min,得到內(nèi)部成分均一的液態(tài)渣。蓄熱式熔化爐6包括熔化爐601和蓄熱爐602。熔化爐601會(huì)排出熱煙氣,將熱煙氣送入蓄熱爐602中預(yù)熱燃料和助燃風(fēng)。將液態(tài)渣引流至中間罐7,在中間罐中降溫至1200℃。將調(diào)溫后的液態(tài)渣送入制絲設(shè)備8,通過(guò)噴吹制絲工藝將液態(tài)渣吹成礦物纖維。采用壓縮空氣噴吹。將制絲設(shè)備8排出的高溫礦物纖維送入集棉箱9中,并往集棉箱9中通入壓縮空氣冷卻礦物纖維。將制絲設(shè)備8排出的吹噴氣體和集棉箱9排出的含塵氣體送入除塵設(shè)備10除塵,獲得凈化氣和纖維塵。將纖維塵送入蓄熱式熔化爐6,與混合料一起制備液態(tài)渣。將集棉箱9排出的低溫礦物纖維送入除渣設(shè)備11中除渣,獲得除渣礦物纖維(即成品)、渣球和纖維束。將渣球和纖維束送入蓄熱式熔化爐6,與混合料一起制備液態(tài)渣。本實(shí)施中的液態(tài)渣中的sio2的含量為10wt%,cao的含量為4wt%,al2o3的含量為60wt%,mgo的含量為10wt%,na2o和k2o等堿金屬氧化物的總量為8wt%。本實(shí)施例制得的礦物纖維的平均長(zhǎng)度為1-200mm,纖維平均直徑為4.4μm,纖維板密度為156kg/m3,渣球含量小于2.8%,抗拉強(qiáng)度為15kpa,壓縮強(qiáng)度為70kpa,防火等級(jí)為a級(jí)。實(shí)施例2本實(shí)施例采用圖1所示的系統(tǒng)及圖2所示的工藝流程生產(chǎn)礦物纖維板,具體如下:準(zhǔn)備3000kgrkef紅土鎳礦渣、400kg粉煤灰。所用rkef紅土鎳礦渣化學(xué)成分如表3所示:表3rkef紅土鎳礦渣主要化學(xué)成分成分feosio2mgocaoal2o3含量6.1637.7417.6514.6514.05在細(xì)磨機(jī)1中將紅土鎳礦渣中細(xì)磨至粒徑≤60μm。粉料在酸浸設(shè)備2中經(jīng)過(guò)酸浸后得到脫鎂礦渣,其化學(xué)成分如表4所示:表4脫鎂rkef紅土鎳礦渣主要化學(xué)成分成分feosio2mgocaoal2o3含量5.2161.224.596.2222.52所用酸為40%的稀硫酸,用量為15噸。采用常壓酸浸的方法,酸浸時(shí)間為5h,酸浸溫度為40℃。將脫鎂后的rkef紅土鎳礦渣依次送入過(guò)濾設(shè)備3和烘干設(shè)備4中,經(jīng)過(guò)過(guò)濾和烘干后獲得烘干礦渣。烘干溫度為105℃,時(shí)間為24h。將烘干礦渣送入混合設(shè)備5與粉煤灰混合均勻,獲得混合料。將混合料送入蓄熱式熔化爐6內(nèi),在1800℃的溫度下熔融,然后保溫20min,得到內(nèi)部成分均一的液態(tài)渣。蓄熱式熔化爐6包括熔化爐601和蓄熱爐602。熔化爐601會(huì)排出熱煙氣,將熱煙氣送入蓄熱爐602中預(yù)熱燃料和助燃風(fēng)。將液態(tài)渣引流至中間罐7,在中間罐中降溫至1500℃。將調(diào)溫后的液態(tài)渣送入制絲設(shè)備8,通過(guò)噴吹制絲工藝將液態(tài)渣吹成礦物纖維。采用壓縮空氣噴吹。將制絲設(shè)備8排出的高溫礦物纖維送入集棉箱9中,并往集棉箱9中通入壓縮空氣冷卻礦物纖維。將制絲設(shè)備8排出的吹噴氣體和集棉箱9排出的含塵氣體送入除塵設(shè)備10除塵,獲得凈化氣和纖維塵。將纖維塵送入蓄熱式熔化爐6,與混合料一起制備液態(tài)渣。將集棉箱9排出的低溫礦物纖維送入除渣設(shè)備11中除渣,獲得除渣礦物纖維(即成品)、渣球和纖維束。將渣球和纖維束送入蓄熱式熔化爐6,與混合料一起制備液態(tài)渣。本實(shí)施中的液態(tài)渣中的sio2的含量為70wt%,cao的含量為1wt%,al2o3的含量為10wt%,mgo的含量為10wt%,na2o和k2o等堿金屬氧化物的總量為6wt%。本實(shí)施例制得的礦物纖維的平均長(zhǎng)度為1-500mm,纖維平均直徑為4.2μm,纖維板密度為145kg/m3,渣球含量小于2.6%,抗拉強(qiáng)度為13kpa,壓縮強(qiáng)度為72kpa,防火等級(jí)為a級(jí)。實(shí)施例3本實(shí)施例采用圖1所示的系統(tǒng)及圖2所示的工藝流程生產(chǎn)礦物纖維板,具體如下:準(zhǔn)備3000kg小高爐紅土鎳礦渣、200kg生石灰。所用小高爐紅土鎳礦渣化學(xué)成分如表5所示:表5小高爐紅土鎳礦渣主要化學(xué)成分成分feosio2mgocaoal2o3含量10.6642.6418.4912.478.62在細(xì)磨機(jī)1中將小高爐紅土鎳礦渣中細(xì)磨至粒徑≤60μm。粉料在酸浸設(shè)備2中經(jīng)過(guò)酸浸后得到脫鎂礦渣,其化學(xué)成分如表6所示:表6脫鎂小高爐紅土鎳礦渣主要化學(xué)成分成分feosio2mgocaoal2o3含量4.1363.753.865.4814.64所用酸為50%稀硫酸,用量為10噸。采用常壓酸浸的方法,酸浸時(shí)間為5h,酸浸溫度為50℃。將脫鎂后的小高爐紅土鎳礦渣依次送入過(guò)濾設(shè)備3和烘干設(shè)備4中,經(jīng)過(guò)過(guò)濾和烘干后獲得烘干礦渣。烘干溫度為110℃,時(shí)間為20h。將烘干礦渣送入混合設(shè)備5與生石灰混合均勻,獲得混合料。將混合料送入蓄熱式熔化爐6內(nèi),在1600℃的溫度下熔融,然后保溫30min,得到內(nèi)部成分均一的液態(tài)渣。蓄熱式熔化爐6包括熔化爐601和蓄熱爐602。熔化爐601會(huì)排出熱煙氣,將熱煙氣送入蓄熱爐602中預(yù)熱燃料和助燃風(fēng)。將液態(tài)渣引流至中間罐7,在中間罐中降溫至1250℃。將調(diào)溫后的液態(tài)渣送入制絲設(shè)備8,通過(guò)噴吹制絲工藝將液態(tài)渣吹成礦物纖維。采用壓縮空氣噴吹。將制絲設(shè)備8排出的高溫礦物纖維送入集棉箱9中,并往集棉箱9中通入壓縮空氣冷卻礦物纖維。將制絲設(shè)備8排出的吹噴氣體和集棉箱9排出的含塵氣體送入除塵設(shè)備10除塵,獲得凈化氣和纖維塵。將纖維塵送入蓄熱式熔化爐6,與混合料一起制備液態(tài)渣。將集棉箱9排出的低溫礦物纖維送入除渣設(shè)備11中除渣,獲得除渣礦物纖維(即成品)、渣球和纖維束。將渣球和纖維束送入蓄熱式熔化爐6,與混合料一起制備液態(tài)渣。本實(shí)施中的液態(tài)渣中的sio2的含量為10wt%,cao的含量為50wt%,al2o3的含量為10wt%,mgo的含量為10wt%,na2o和k2o等堿金屬氧化物的總量為5wt%。本實(shí)施例制得的礦物纖維的平均長(zhǎng)度為20-400mm,纖維平均直徑為4.8μm,纖維板密度為182kg/m3,渣球含量小于1.9%,抗拉強(qiáng)度為16.5kpa,壓縮強(qiáng)度為81kpa,防火等級(jí)為a級(jí)。實(shí)施例4本實(shí)施例采用圖1所示的系統(tǒng)及圖2所示的工藝流程生產(chǎn)礦物纖維板,具體如下:準(zhǔn)備3000kg小高爐紅土鎳礦渣、200kg粉煤灰和150kg生石灰。所用小高爐紅土鎳礦渣化學(xué)成分如表7所示:表7小高爐紅土鎳礦渣主要化學(xué)成分成分feosio2mgocaoal2o3含量12.6646.5217.6411.8410.23在細(xì)磨機(jī)1中將小高爐紅土鎳礦渣中細(xì)磨至粒徑≤60μm。粉料在酸浸設(shè)備2中經(jīng)過(guò)酸浸后得到脫鎂礦渣,其化學(xué)成分如表8所示:表8脫鎂小高爐紅土鎳礦渣主要化學(xué)成分成分feosio2mgocaoal2o3含量5.8765.484.316.1413.73所用酸為15%稀鹽酸,用量為20噸。采用常壓酸浸的方法,酸浸時(shí)間為3h,酸浸溫度為60℃。將脫鎂后的小高爐紅土鎳礦渣依次送入過(guò)濾設(shè)備3和烘干設(shè)備4中,經(jīng)過(guò)過(guò)濾和烘干后獲得烘干礦渣。烘干溫度為120℃,時(shí)間為12h。將烘干礦渣送入混合設(shè)備5與粉煤灰和生石灰混合均勻,獲得混合料。將混合料送入蓄熱式熔化爐6內(nèi),在1400℃的溫度下熔融,然后保溫25min,得到內(nèi)部成分均一的液態(tài)渣。蓄熱式熔化爐6包括熔化爐601和蓄熱爐602。熔化爐601會(huì)排出熱煙氣,將熱煙氣送入蓄熱爐602中預(yù)熱燃料和助燃風(fēng)。將液態(tài)渣引流至中間罐7,在中間罐中降溫至1350℃。將調(diào)溫后的液態(tài)渣送入制絲設(shè)備8,通過(guò)噴吹制絲工藝將液態(tài)渣吹成礦物纖維。采用壓縮空氣噴吹。將制絲設(shè)備8排出的高溫礦物纖維送入集棉箱9中,并往集棉箱9中通入壓縮空氣冷卻礦物纖維。將制絲設(shè)備8排出的吹噴氣體和集棉箱9排出的含塵氣體送入除塵設(shè)備10除塵,獲得凈化氣和纖維塵。將纖維塵送入蓄熱式熔化爐6,與混合料一起制備液態(tài)渣。將集棉箱9排出的低溫礦物纖維送入除渣設(shè)備11中除渣,獲得除渣礦物纖維(即成品)、渣球和纖維束。將渣球和纖維束送入蓄熱式熔化爐6,與混合料一起制備液態(tài)渣。本實(shí)施中的液態(tài)渣中的sio2的含量為17wt%,cao的含量為5wt%,al2o3的含量為10wt%,mgo的含量為50wt%,na2o和k2o等堿金屬氧化物的總量為7wt%。本實(shí)施例制得的礦物纖維的平均長(zhǎng)度為14-400mm,纖維平均直徑為4.5μm,纖維板密度為178kg/m3,渣球含量小于2.1%,抗拉強(qiáng)度為16kpa,壓縮強(qiáng)度為77kpa,防火等級(jí)為a級(jí)。從上述實(shí)施例可知,本發(fā)明制得的礦物纖維板質(zhì)量好,是一種優(yōu)良的建筑材料。本發(fā)明回收了纖維塵、渣球和纖維束,提高了能源利用率,又解決了環(huán)境污染問(wèn)題。本發(fā)明使用的紅土鎳礦渣成本低廉,而且蓄熱式熔化爐燃料消耗少、節(jié)約能源,因此本發(fā)明制得的礦物纖維的生產(chǎn)成本低。顯然,上述實(shí)施例僅僅是為清楚地說(shuō)明本發(fā)明所作的舉例,而并非對(duì)實(shí)施方式的限定。對(duì)于所屬領(lǐng)域的普通技術(shù)人員來(lái)說(shuō),在上述說(shuō)明的基礎(chǔ)上還可以做出其它不同形式的變化或變動(dòng)。這里無(wú)需也無(wú)法對(duì)所有的實(shí)施方式予以窮舉。而由此所引申出的顯而易見(jiàn)的變化或變動(dòng)仍處于本發(fā)明的保護(hù)范圍之中。當(dāng)前第1頁(yè)12