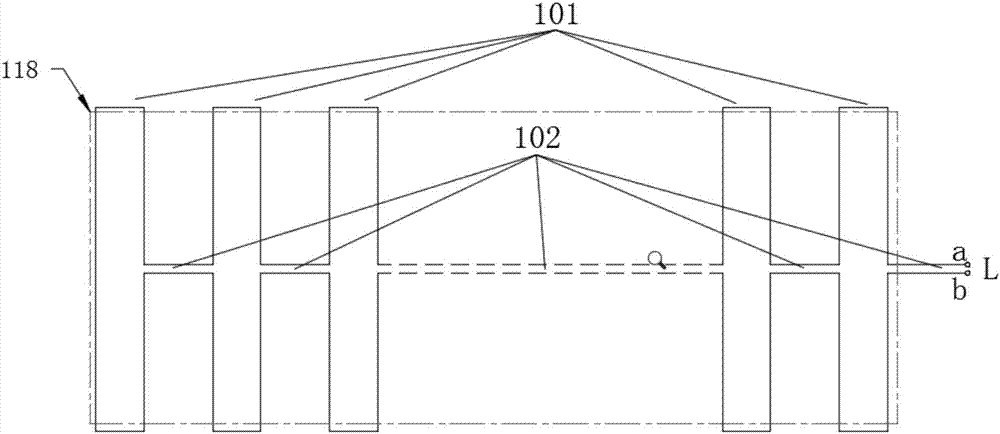
本實用新型涉及磁感應領域,特別涉及一種陣列編碼磁信號定位感應裝置。
背景技術:
:隨著電子產品和各類數控機床的進步與發展,對距離和二維面的位置傳感感應器的應用和需求越來越廣泛。專利號為CN201320756682.X的中國實用新型專利“電磁天線的單層布線系統”公布了一種在二維面兩個方向設置若干獨立電磁感應通道線圈來構成磁信號定位感應器,可用來掃描檢測定位電磁筆以實現手寫輸入觸控裝置,這種磁信號定位感應器每個通道位置的設置一獨立的電磁感應通道線圈,要區域掃描檢測這樣的磁信號定位感應器需要很長的時間,反映速度慢,這樣的磁信號定位感應器十分復雜,不適合大尺寸磁信號定位感應器的設計運用。技術實現要素:本實用新型旨在至少在一定程度上解決相關技術中的技術問題之一。為此,本實用新型的主要目的在于提供一種陣列編碼磁信號定位感應裝置,旨在解決現有技術的磁感應裝置檢測時間長、反應速度慢、裝置復雜的問題。為實現上述目的,本實用新型提供一種陣列編碼磁信號定位感應裝置,包括感應組件和連接所述感應組件的控制電路,其特征在于,所述感應組件包括:水平編碼陣列、與所述水平編碼陣列垂直設置的垂直編碼陣列,所述水平編碼陣列與所述垂直編碼陣列均由磁信號感應線圈單元組成;其中,所述水平編碼陣列由一個以上的磁信號感應線圈單元組成;所述垂直編碼陣列由一個以上的磁信號感應線圈單元組成;其中,所述磁信號感應線圈單元由至少兩個磁感應線圈通過差分線串聯而成;其中,所述磁感應線圈由1圈到10圈的連續環形導線構成。所述磁信號感應線圈單元中串聯磁感應線圈的差分線在磁感應定位有效區內,或在磁感應定位有效區外。所述磁信號感應線圈單元中串聯磁感應線圈的差分線在磁感應定位有效區外。設置在所述水平編碼陣列中的磁信號感應線圈與所述垂直編碼陣列中的磁信號感應線圈相互交叉排列組合設置。所述控制電路包括多選一陣列開關、前級信號放大器、可控增益放大器、帶通放大器、交直流變換器、積分電路、直流放大器、充放電開關和處理器;其中,所述多選一陣列開關一側分別與所述水平磁感應線圈和所述垂直磁感應線圈連接,所述多選一陣列開關另一側與所述前級放大器連接,所述前級放大器與所述可控增益放大器連接;所述可控增益放大器一端通向所述處理器,所述可控增益放大器另一端通向所述帶通放大器,所述帶通放大器通過所述交直流變換器與所述積分電路連接;所述積分電路一端通過直流放大器通向所述處理器,所述積分電路另一端通向所述充放電開關,所述處理器分別通向所述多選一陣列開關和所述充放電開關。排列組合設置為:水平編碼陣列和垂直編碼陣列中任意磁信號感應線圈單元上任意磁信號感應圈與相鄰前或相鄰后其它的磁信號感應線圈單元上的磁感應線圈的兩兩排列組合不與其它位置上的兩兩排列組合重復;并同時遵循同一所述磁信號感應線圈單元上的磁感應線圈在任意位置不連續出現參與兩兩排列組合。所述水平編碼陣列和垂直編碼陣列中任意位置相鄰的兩個磁感應線圈的兩兩排列組合是唯一的。有益效果如下:這種磁信號定位感應器的磁信號線圈單元由多個磁感應通道線圈串聯而成,每一個串聯磁信號感應線圈單元可以同時檢測多個位置的交變磁信號源,這樣電磁感應通道線圈的引出線的布線就更加簡單,磁信號定位感應器對交變磁信號源的掃描檢測鎖定時間短,速度快。附圖說明為了更清楚地說明本實用新型實施例或現有技術中的技術方案,下面將對實施例或現有技術描述中所需要使用的附圖作簡單地介紹,顯而易見地,下面描述中的附圖僅僅是本實用新型的一些實施例,對于本領域普通技術人員來講,在不付出創造性勞動的前提下,還可以根據這些附圖示出的結構獲得其他的附圖。圖1為本實用新型整體結構示意圖。圖2為本實用新型差分線設置在有效區內的磁感應單元結構示意圖。圖3為本實用新型差分線設置在有效區外的磁感應單元結構示意圖。圖4為本實用新型差分線設置在有效區內的水平陣列編碼結構示意圖。圖5為本實用新型差分線設置在有效區內的垂直陣列編碼結構示意圖。圖6為本實用新型差分線設置在有效區內的感應元件示意圖。圖7為本實用新型差分線設置在有效區外的水平陣列編碼結構示意圖。圖8為本實用新型差分線設置在有效區外的垂直陣列編碼結構示意圖。圖9為本實用新型差分線設置在有效區外的感應元件示意圖。具體實施方式下面將結合本實用新型實施例中的附圖,對本實用新型實施例中的技術方案進行清楚、完整地描述,顯然,所描述的實施例僅僅是本實用新型的一部分實施例,而不是全部的實施例?;诒緦嵱眯滦椭械膶嵤├?,本領域普通技術人員在沒有作出創造性勞動前提下所獲得的所有其他實施例,都屬于本實用新型保護的范圍。需要說明,本實用新型實施例中所有方向性指示(諸如上、下、左、右、前、后……)僅用于解釋在某一特定姿態(如附圖所示)下各部件之間的相對位置關系、運動情況等,如果該特定姿態發生改變時,則該方向性指示也相應地隨之改變。在本實用新型中如涉及“第一”、“第二”等的描述僅用于描述目的,而不能理解為指示或暗示其相對重要性或者隱含指明所指示的技術特征的數量。由此,限定有“第一”、“第二”的特征可以明示或者隱含地包括至少一個該特征。在本實用新型的描述中,“多個”的含義是至少兩個,例如兩個,三個等,除非另有明確具體的限定。在本實用新型中,除非另有明確的規定和限定,術語“連接”、“固定”等應做廣義理解,例如,“固定”可以是固定連接,也可以是可拆卸連接,或成一體;可以是機械連接,也可以是電連接;可以是直接相連,也可以通過中間媒介間接相連,可以是兩個元件內部的連通或兩個元件的相互作用關系,除非另有明確的限定。對于本領域的普通技術人員而言,可以根據具體情況理解上述術語在本實用新型中的具體含義。另外,本實用新型各個實施例之間的技術方案可以相互結合,但是必須是以本領域普通技術人員能夠實現為基礎,當技術方案的結合出現相互矛盾或無法實現時應當認為這種技術方案的結合不存在,也不在本實用新型要求的保護范圍之內。一種陣列編碼磁信號定位感應裝置,包括感應組件和連接所述感應組件的控制電路,其特征在于,所述感應組件包括:水平編碼陣列、與所述水平編碼陣列垂直設置的垂直編碼陣列,所述水平編碼陣列與所述垂直編碼陣列均由磁信號感應線圈單元組成;其中,所述水平編碼陣列由一個以上的磁信號感應線圈單元組成;所述垂直編碼陣列由一個以上的磁信號感應線圈單元組成;其中,所述磁信號感應線圈單元由至少兩個磁感應線圈通過差分線串聯而成;其中,所述磁感應線圈由1圈到10圈的連續環形導線構成。所述磁信號感應線圈單元中串聯磁感應線圈的差分線在磁感應定位有效區內,或在磁感應定位有效區外。所述磁信號感應線圈單元中串聯磁感應線圈的差分線在磁感應定位有效區外。設置在所述水平編碼陣列中的磁信號感應線圈與所述垂直編碼陣列中的磁信號感應線圈相互交叉排列組合設置。所述控制電路包括多選一陣列開關、前級信號放大器、可控增益放大器、帶通放大器、交直流變換器、積分電路、直流放大器、充放電開關和處理器;其中,所述多選一陣列開關一側分別與所述水平磁感應線圈和所述垂直磁感應線圈連接,所述多選一陣列開關另一側與所述前級放大器連接,所述前級放大器與所述可控增益放大器連接;所述可控增益放大器一端通向所述處理器,所述可控增益放大器另一端通向所述帶通放大器,所述帶通放大器通過所述交直流變換器與所述積分電路連接;所述積分電路一端通過直流放大器通向所述處理器,所述積分電路另一端通向所述充放電開關,所述處理器分別通向所述多選一陣列開關和所述充放電開關。排列組合設置為:水平編碼陣列和垂直編碼陣列中任意磁信號感應線圈單元上任意磁信號感應圈與相鄰前或相鄰后其它的磁信號感應線圈單元上的磁感應線圈的兩兩排列組合不與其它位置上的兩兩排列組合重復;并同時遵循同一所述磁信號感應線圈單元上的磁感應線圈在任意位置不連續出現參與兩兩排列組合。所述水平編碼陣列和垂直編碼陣列中任意位置相鄰的兩個磁感應線圈的兩兩排列組合是唯一的。所述磁感應線圈的材質為合金材料,該合金材料由以下質量配比的合金制成:(FexCo1-x)a(Ni1-y-zAlyCez)bCucBdSieCrf,其中a=30-60,b=30-55,c=1-5,d=1-8,e=1-5,f=1-5,x=0.1-0.8,y=0.1-0.5,z=0.01-0.08;該合金的制備方法包括以下步驟:步驟一,納米合金粉體的制備:采用鐵粉、鎳粉、鉻粉和銅粉作為基礎粉體;所采用的鐵粉的顆粒度60~100μm,純度≥99%;鎳粉的顆粒度為3~6μm,純度>99%;鉻粉的顆粒度80~120μm,純度≥99.9%;銅粉的顆粒度為50~130μm,純度≥99.9%;所述鐵粉、鎳粉、鉻粉和銅粉的質量比為20-40:15-30:1-6:1-5,配置成混合粉末,加入無水乙醇攪拌均勻,放入密封罐后,在行星式球磨機上于常溫下進行星式球磨,球磨時間為100-190h,獲得顆粒尺寸為1-10nm的Fe-Ni-Cu-Cr納米合金粉末,所述基礎粉體與無水乙醇的質量比為1-2:0.5-3;步驟二,合金粉體基體的制備:按照合金的質量配比將步驟一所得到的納米合金粉體進行干燥后加入粉體Si、Al、Co、Ce和B,將上述原料放入真空感應爐中,在1000-1500℃下進行熔煉,反復熔煉2-4次,每次熔煉30-120min,熔煉完畢后,在氦氣的保護下進行鑄坯,冷卻后得到合金鑄錠,將冷卻后的合金鑄錠,放入密封罐后,在行星式球磨機上于常溫下進行星式球磨,球磨的時間為50-200h,球磨得到粒度為小于15nm的合金粉體基體;所述Si,Al,Co,Ce和B的純度達到99.8%以上,Si粒徑為粒徑為10-100μm,Al的粒徑為10-80μm,Co的粒徑為10-120μm,Ce的粒徑為10-90μm,B的粒徑為10-110μm;步驟三,燒結:將步驟二所制得的合金粉體基體在氬氣氣氛燒結爐中燒結成型,在燒結過程,首先以10-15℃/min的升溫速率在400-500℃預燒1-3h,然后以30-40℃/min的升溫速率在1250-1350℃燒結5-8h得到基礎合金;步驟四,淬火:將步驟三燒結的基礎合金置于淬火爐內進行淬火處理,首先在淬火溫度為1100-1200℃保溫時間15-25min,之后在5-10min內降溫至50-80℃保溫時間30-40min;步驟五,退火處理:將步驟四淬火得到的基礎合金置于氬氣氣氛的退火爐中,首先加熱到450-455℃,保溫1-2h,再次加熱到525-535℃,保溫2-3h,然后加熱到720℃,保溫3-4h,停止加熱,在30-40min內將溫度降至150-170℃,然后自然冷卻至室溫得到合金;步驟六,加工:將步驟五所制得的合金進行切割加工制得所需形狀的線圈。該實施例的優選合金的配比為:(Fe0.6Co0.4)50(Ni0.65Al0.3Ce0.05)35Cu3B6Si3Cr3;更加優選該合金的結構為:該合金形成了α-Fe相、摻雜Co的α-Fe相和非晶相組成,其中α-Fe相和摻雜Co的α-Fe相組成第一相,第一相中α-Fe相和摻雜Co的α-Fe相的顆粒尺寸在1-15nm之間,第一相與非晶相之間形成了一個界面相,其中第一相的飽和磁化強度約為1.52T,相界面為一個厚度為1-1.5nm的界面,其中Ni在第一相中的含量為在非晶相中的含量的1.5倍。步驟一中,優選的球磨時間為152h。步驟五中更加優選,將步驟四淬火得到的基礎合金置于氬氣氣氛的退火爐中,首先加熱至455℃,保溫1.5h,之后再次加熱至530℃,保溫2.5h,然后加熱到720℃,保溫3.5h,停止加熱,在30-40min內將溫度降至150-170℃,然后自然冷卻至室溫得到合金。實施例1如圖1、圖2和圖4~圖6所示,一種陣列編碼磁信號定位感應裝置,包括感應組件100和檢測控制電路10,感應元件100透過連接器插接或直接熱壓焊接到檢測控制電路,感應元件100包括:水平編碼陣列1010與水平編碼陣列1010垂直設置的垂直編碼陣列1011,水平編碼陣列1010與垂直編碼陣列1011均由磁信號感應線圈單元組成;其中,水平編碼陣列1010由一個以上的磁信號感應線圈單元組成;垂直編碼陣列1011由一個以上的磁信號感應線圈單元組成;其中,磁信號感應線圈單元由至少兩個磁感應線圈101通過差分線102串聯而成。其中,磁感應線圈由1圈到10圈的連續環形導線構成。差分線102設置在磁信號定位有效區118內,磁感應線圈為透明導電材質或者非透明導電材質,垂直編碼陣列1011與水平編碼陣列1010設置在同一個裝置內。優選地,設置在水平編碼陣列1010中的磁信號感應線圈101與垂直編碼陣列1011中的磁信號感應線圈101相互交叉排列組合設置。優選地,檢測控制電路10包括多選一陣列開關103、前級信號放大器104、可控增益放大器105、帶通放大器106、交直流變換器107、積分電路108、直流放大器109、充放電開關112和處理器110;其中,多選一陣列開關103一側分別與水平編碼陣列1010和垂直編碼陣列1011的磁感應線圈101連接,多選一陣列開關103另一側與前級放大器104連接,前級放大器104與可控增益放大器105連接;可控增益放大器105一端通向處理器110,可控增益放大器105另一端通向帶通放大器106,帶通放大器106通過交直流變換器107與積分電路108連接;積分電路108一端通過直流放大器109通向處理器110,積分電路108另一端通向充放電開關112,處理器110通過掃描總線114通向多選一陣列開關103,處理器110另一側通向充放電開關112。優選地,排列組合設置為:水平編碼陣列1010和垂直編碼陣列1011中任意磁信號感應線圈單元上任意磁信號感應圈101與相鄰前或相鄰后其它的磁信號感應線圈單元上的磁感應線圈101的兩兩排列組合不與其它位置上的兩兩排列組合重復;并同時遵循同一磁信號感應線圈單元上的磁感應線圈101在任意位置不連續出現參與兩兩排列組合;優選地,水平編碼陣列1010和垂直編碼陣列1011中任意位置相鄰的兩個磁感應線圈101的兩兩排列組合是唯一的;差分線102設置在磁信號定位有效區118內。所述磁感應線圈的材質為合金材料,該合金材料由以下質量配比的合金制成:(FexCo1-x)a(Ni1-y-zAlyCez)bCucBdSieCrf,其中a=30-60,b=30-55,c=1-5,d=1-8,e=1-5,f=1-5,x=0.1-0.8,y=0.1-0.5,z=0.01-0.08;該合金的制備方法包括以下步驟:步驟一,納米合金粉體的制備:采用鐵粉、鎳粉、鉻粉和銅粉作為基礎粉體;所采用的鐵粉的顆粒度60~100μm,純度≥99%;鎳粉的顆粒度為3~6μm,純度>99%;鉻粉的顆粒度80~120μm,純度≥99.9%;銅粉的顆粒度為50~130μm,純度≥99.9%;所述鐵粉、鎳粉、鉻粉和銅粉的質量比為20-40:15-30:1-6:1-5,配置成混合粉末,加入無水乙醇攪拌均勻,放入密封罐后,在行星式球磨機上于常溫下進行星式球磨,球磨時間為100-190h,獲得顆粒尺寸為1-10nm的Fe-Ni-Cu-Cr納米合金粉末,所述基礎粉體與無水乙醇的質量比為1-2:0.5-3;步驟二,合金粉體基體的制備:按照合金的質量配比將步驟一所得到的納米合金粉體進行干燥后加入粉體Si、Al、Co、Ce和B,將上述原料放入真空感應爐中,在1000-1500℃下進行熔煉,反復熔煉2-4次,每次熔煉30-120min,熔煉完畢后,在氦氣的保護下進行鑄坯,冷卻后得到合金鑄錠,將冷卻后的合金鑄錠,放入密封罐后,在行星式球磨機上于常溫下進行星式球磨,球磨的時間為50-200h,球磨得到粒度為小于15nm的合金粉體基體;所述Si,Al,Co,Ce和B的純度達到99.8%以上,Si粒徑為粒徑為10-100μm,Al的粒徑為10-80μm,Co的粒徑為10-120μm,Ce的粒徑為10-90μm,B的粒徑為10-110μm;步驟三,燒結:將步驟二所制得的合金粉體基體在氬氣氣氛燒結爐中燒結成型,在燒結過程,首先以10-15℃/min的升溫速率在400-500℃預燒1-3h,然后以30-40℃/min的升溫速率在1250-1350℃燒結5-8h得到基礎合金;步驟四,淬火:將步驟三燒結的基礎合金置于淬火爐內進行淬火處理,首先在淬火溫度為1100-1200℃保溫時間15-25min,之后在5-10min內降溫至50-80℃保溫時間30-40min;步驟五,退火處理:將步驟四淬火得到的基礎合金置于氬氣氣氛的退火爐中,首先加熱到450-455℃,保溫1-2h,再次加熱到525-535℃,保溫2-3h,然后加熱到720℃,保溫3-4h,停止加熱,在30-40min內將溫度降至150-170℃,然后自然冷卻至室溫得到合金;步驟六,加工:將步驟五所制得的合金進行切割加工制得所需形狀的線圈。該實施例的優選合金的配比為:(Fe0.6Co0.4)50(Ni0.65Al0.3Ce0.05)35Cu3B6Si3Cr3;更加優選該合金的結構為:該合金形成了α-Fe相、摻雜Co的α-Fe相和非晶相組成,其中α-Fe相和摻雜Co的α-Fe相組成第一相,第一相中α-Fe相和摻雜Co的α-Fe相的顆粒尺寸在1-15nm之間,第一相與非晶相之間形成了一個界面相,其中第一相的飽和磁化強度約為1.52T,相界面為一個厚度為1-1.5nm的界面,其中Ni在第一相中的含量為在非晶相中的含量的1.5倍。步驟一中,優選的球磨時間為152h。步驟五中更加優選,將步驟四淬火得到的基礎合金置于氬氣氣氛的退火爐中,首先加熱至455℃,保溫1.5h,之后再次加熱至530℃,保溫2.5h,然后加熱到720℃,保溫3.5h,停止加熱,在30-40min內將溫度降至150-170℃,然后自然冷卻至室溫得到合金?!拘阅軠y試】(一)步驟一所制得的納米合金粉體:采用日本RikenDenshi公司ModeIBHV-525型振動樣品磁強計(VSM)測量樣品的磁性能。1、通過研究球磨后的XRD譜線發現,在球磨至一段時間后Ni、Cr和Cu的衍射峰將出現基本消失的情形,這是由于隨著球磨時間的增加,Fe形成過飽和固溶體,晶體的完整性受到破壞,使得參與衍射的晶粒減少而導致峰高逐漸降低,Ni、Cr和Cu的衍射峰降低直至基本消失,說明Ni、Cr和Cu固溶于Fe中,形成Fe的過飽和固溶體,研究還發現這種情形的出現,對于Cr含量和球磨時間是成反比的;但是球磨后期的顆粒硬化,內應力增大,當達到彈性極限時,顆粒開始碎化,在粉末不斷細化的同時,伴隨著粉末團聚現象的產生,這是由于球磨過程中,形成了很多納米級粉末,而尺寸達到納米級的粉末的表面能和吸附能增加,從而造成團聚現象,因此該在該配比下最佳的球磨時間為152h;2、如表1所述隨著Cr含量的上升Fe-Ni-Cu-Cr的合金的飽和磁化強度先上升后下降,在Cr含量為3-6%時達到最大值,5%時達到最大值172(σs/A·m2·kg-1);這是因為,當Cr含量增加,會導致合金中長程有序鐵磁性相增加,但是Cr元素不具有磁矩,所以比飽和磁化強度隨著Cr含量的增加先上升后下降的情形;隨著Cr含量的上升該合金的磁導率變化量實現先上升后下降的趨勢,得到含量為5%時為飽和磁化強度與磁導率最優的配比。表1納米合金粉體的性能測試:Cr含量飽和磁化強度(σs/A·m2·kg-1)磁導率增長量0%1240%1%1471%3%1512%5%1723%7%1501.5%9%131-1%(二)(1)制備過程中加入了鈰,使得合金中含有Ce元素對Ni進行了摻雜,研究發現由于合金中同時含有Cr、Ni等大原子,當大原子與小原子組合形成合金時候,則能夠生成一種金屬間化合物Laves相,它的不同尺寸原子以最致密的方式堆垛在晶胞中,其硬度較高,有顯著的強化作用,隨著Ce元素的增加,合金中硬質相增加,促使合金中的固溶體組織均勻細化,導致合金在外力的作用下不易折斷和剝落,研究發現含有Ce的合金經過摩擦后合金表面顯得光滑平整,說明摩擦基體對硬質相的支持保護作用加大,硬相不易剝離和脫落,因而提高了抗磨損的能力,磨損量減少,耐磨性比未加Ce的合金提高20%~30%以上,并且增加Ce的含量引起合金體中的奧氏體含量降低,能夠有效改善合金表面的微觀結構,從而提高合金的耐腐蝕性能;但是還發現隨著Ce含量的增加至一定程度后,合金中的耐摩擦性能和耐腐蝕性能增強,但是磁導率呈現下降的趨勢,這是由于Ce增加到一定程度后對于合金的晶粒大小的細化作用減小達到瓶頸,因此隨著Ce含量的增加對于耐摩擦性能增長變緩,如表2所述當Ce含量為1.75%時候為最佳配比,其中合金的配比為(Fe0.6Co0.4)50(Ni0.65Al0.3Ce0.05)35Cu3B6Si3Cr3。磨損試驗:在RRT2III型往復式摩擦磨損機上進行,磨損試驗試樣的對偶件為70mm×1317mm×10mm白剛玉砂條,粒度為200目,試樣表面粗糙度在018~014μm之間。測試速度150r/s,測試壓力28MPa,測試時間10min,每個試樣測試次數1600-1800次,測試行程75m,室溫20-25℃,濕度23-26%,無潤滑干摩擦試驗,磨損量用萬用電子分析天平測試。未添加Ce的合金磨損量為0.019/mg;腐蝕試驗:腐蝕介質選取H2SO4(5%)、HCl(5%)和NaOH(5%),試樣均在微沸狀態下腐蝕24h,采用失重法進行腐蝕試驗,試樣先要打磨拋光,在腐蝕前后用丙酮浸泡、酒精清洗、吹風機吹干后用萬分之一天平稱腐蝕前后的重量,腐蝕率。表2合金性能測試:(三)步驟三中經過二次加熱處理進行燒結,首先進行預熱之后升溫進行正式燒結。經過研究發現二次加熱處理后的初始磁導率要比一次預熱處理后的初始磁導率要好,其磁導率要高于單次加熱的合金5-10%,隨溫度的升高,合金發生結構馳豫,向穩定的低內能狀態轉變。并且二次加熱工藝的加熱速率也需要遠遠高于第一次預熱工藝的加熱速率:“首先以10-15℃/min的升溫速率在400-500℃預燒1-3h,然后以30-40℃/min的升溫速率在1250-1350℃燒結5-8h”優選“首先以12℃/min的升溫速率在400-500℃預燒2h,然后以35℃/min的升溫速率在1250-1350℃燒結7h”,第二次加熱速率幾乎三倍于第一次的加熱速率,通過研究發現由于之前的預熱已經使得合金體具有一定的適應能力,通過快速升溫,使得材料的合金迅速且結晶更加充分,晶粒間的耦合作用更強,從而材料的有效各向異性常數更低,初始磁導率更高。經過實驗得知,采用二次加熱處理進行燒結后的合金初始磁導率要高于單次加熱處理進行燒結后的合金初始磁導率3-7%,采用第二次加熱速率三倍于第一次的加熱速率后得到的合金的初始磁導率相較于普通二次加熱處理進行燒結后的合金初始磁導率提高4-8%;(四)本實用新型中的淬火步驟中的第二階段采用了快速的淬火步驟,通過研究發現,采用了快速的淬火步驟能夠使得合金的性能更加優質,能提高合金的沖擊韌性值及硬度值,且對于磁性能并無影響,該合金在急冷過程中,其材料的內部結構發生相變增韌,Ce元素能夠部分熔解,使得在粘結相中的Ce在急冷情況下來不及析出,起到了固熔強化的作用,能大幅度提高了該合金的沖擊韌性及硬度值。沖擊韌性能夠達到0.72-0.89MJ/m2,其中經過綜合考慮當合金材料的配比為:其中合金的配比為(Fe0.6Co0.4)50(Ni0.65Al0.3Ce0.05)35Cu3B6Si3Cr3,時Ce含量約為1.75%時的沖擊韌性以及各項性能達到最佳,沖擊韌性為0.85MJ/m2,洛氏硬度值為38HRC。(五)經過退火步驟后該合金形成了α-Fe相、摻雜Co的α-Fe相和非晶相組成,其中α-Fe相和摻雜Co的α-Fe相組成第一相,第一相中α-Fe相和摻雜Co的α-Fe相的顆粒尺寸在1-15nm之間,第一相與非晶相之間形成了一個界面相,其中第一相的飽和磁化強度約為1.52T,相界面為一個厚度為1-1.5nm的界面,其中Ni在第一相中的含量為在非晶相中的含量的1.5倍;本實用新型創造性的首先制備納米合金粉體,之后加入金屬進行熔煉,這樣使得Ni能夠進入至由α-Fe相和摻雜Co的α-Fe相組成的第一相中,經過研究發現當Ni在第一相中的含量為在非晶相中的含量的1.5倍時該合金的飽和磁化強度最大,其合金的飽和磁化強度約為1.57T。(1)步驟五中的退火溫度對于合金的晶粒直徑有一定影響。在合金加熱過程中,由于存在不同的金屬元素,經過研究發現首先加熱至455℃,保溫1.5h,先使得第一相中的元素優先成核,之后再次加熱至530℃,保溫2.5h,然后加熱到720℃,保溫3.5h,使得非晶相此時能夠得到均勻細小納米結構。如果再次升溫后發現當溫度升高到750℃時,晶粒尺寸急劇長大,其使磁各向異性增加,同時大晶粒對疇壁的位移、磁矩轉動起阻礙作用。因此本實用新型采用最佳的退火溫度為“首先加熱至455℃,保溫1.5h,先使得第一相中的元素優先成核,之后再次加熱至530℃,保溫2.5h,然后加熱到720℃,保溫3.5h”。(2)研究發現在進行退火的過程中需要進行保溫程序,但是保溫的時間與本實用新型合金的磁性能具有很大的關系,隨著保溫時間的延長,磁性能下降。由于在合金的內部存在很大的內應力,且不同部位固化推進方式不同而形成區域應力場,在720℃保溫3-4h后(最佳保溫時間為3.5h),合金的內應力可以達到充分的釋放,磁晶各相異性能降低,合金內部的亞穩定結構趨于穩定,而使合金表現出優良的軟磁性能。但在720℃保溫超過4h后,由于出現了惡化磁性能的析出相,導致合金磁性能下降。實施例2參照圖1,圖3和圖7~圖9,與實施例的不同之處在于,差分線102設置在磁信號定位有效區118外,磁感應線圈101為不透明導電材質,垂直編碼陣列1011與水平編碼陣列1010設置在同一個裝置內,磁感應線圈的材質與實施例1一致。工作原理如下:參照圖6和圖9,交變磁信號源117的靠近水平編碼陣列1010,水平編碼陣列1010中靠近交變磁信號源117的幾個相鄰水平磁感應線圈單元(圖3),例如:x1、x5、x7與交變磁信號源117互感產生磁互感信號。產生此磁互感信號的幾個相鄰水平磁感應線圈101,如x1、x5、x7的組合編碼為x5x1、x5x7、x7x5、x1x5x7或x7x5x1,該組合編碼為當前交變磁信號源117在水平編碼陣列1010核磁信號定位有效區118中的水平坐標編碼,產生磁互感信號越強的磁感應線圈101判定越靠近交變磁信號源117。同理,交變磁信號源117靠近垂直編碼陣列1011,垂直垂直編碼陣列1011中靠近交變磁信號源117的幾個相鄰的磁感應線圈單元(圖3),例如y6、y2、y4與交變磁信號源117互感產生磁互感信號。產生此磁互感信號的幾個相鄰的磁感應線圈101如y6、y2、y4的組合編碼為y6y2,y2y6,y2y4,y4y2,y6y2y4或y4y2y6,該組合編碼為當前交變磁信號源117在垂直編碼陣列1011和磁信號定位有效區118中的垂直坐標編碼,產生磁互感信號越強的磁感應線圈101判定越靠近交變磁信號源117。靠近交變磁信號源117的幾個相鄰磁感應線圈101的x1、x5、x7或y6、y2、y4的組合編碼x1x5,x5x1,x5x7,x7x5,x1x5x7或x7x5x1和y6y2,y2y6,y2y4,y4y2,y6y2y4或y4y2y6,代表交變磁信號源117在感應元件100的檢測磁信號定位有效區118水平方向和垂直方向的大致絕對坐標位置。交變磁信號源117判定在大致絕對坐標位置處磁互感信號最強那個磁感應線圈101,如x1x5x7的x5和y6y2y4的y2位置,再根據最強磁感應線圈兩側的磁感應線圈的感應磁互感信號強度的比值判定交變磁信號源117在最強磁感應線圈x1x5x7的x5和y6y2y4的y2通道所在區域內相對兩側磁感應線圈2的精細相對位置。最強磁感應線圈x5和y2兩側的磁感應線圈x1,x7和y6,y4磁互感信號強度的比值為1:1代表交變磁信號源117在最強磁感應線圈x5和y2通道的中心位置,大于1:1則判定交變磁信號源117在最強磁感應線圈x5和y2通道所在區域內并偏向一側的次強磁感應線圈,偏移的距離跟這個比值成正比,小于1:1則判定交變磁信號源117在最強磁感應線圈x5和y2通道所在區域內并偏向另一側的次強磁感應線圈單元,偏移的距離跟這個比值成反比。所述磁感應線圈的材質為合金材料,該合金材料由以下質量配比的合金制成:(FexCo1-x)a(Ni1-y-zAlyCez)bCucBdSieCrf,其中a=30-60,b=30-55,c=1-5,d=1-8,e=1-5,f=1-5,x=0.1-0.8,y=0.1-0.5,z=0.01-0.08;該合金的制備方法包括以下步驟:步驟一,納米合金粉體的制備:采用鐵粉、鎳粉、鉻粉和銅粉作為基礎粉體;所采用的鐵粉的顆粒度60~100μm,純度≥99%;鎳粉的顆粒度為3~6μm,純度>99%;鉻粉的顆粒度80~120μm,純度≥99.9%;銅粉的顆粒度為50~130μm,純度≥99.9%;所述鐵粉、鎳粉、鉻粉和銅粉的質量比為20-40:15-30:1-6:1-5,配置成混合粉末,加入無水乙醇攪拌均勻,放入密封罐后,在行星式球磨機上于常溫下進行星式球磨,球磨時間為100-190h,獲得顆粒尺寸為1-10nm的Fe-Ni-Cu-Cr納米合金粉末,所述基礎粉體與無水乙醇的質量比為1-2:0.5-3;步驟二,合金粉體基體的制備:按照合金的質量配比將步驟一所得到的納米合金粉體進行干燥后加入粉體Si、Al、Co、Ce和B,將上述原料放入真空感應爐中,在1000-1500℃下進行熔煉,反復熔煉2-4次,每次熔煉30-120min,熔煉完畢后,在氦氣的保護下進行鑄坯,冷卻后得到合金鑄錠,將冷卻后的合金鑄錠,放入密封罐后,在行星式球磨機上于常溫下進行星式球磨,球磨的時間為50-200h,球磨得到粒度為小于15nm的合金粉體基體;所述Si,Al,Co,Ce和B的純度達到99.8%以上,Si粒徑為粒徑為10-100μm,Al的粒徑為10-80μm,Co的粒徑為10-120μm,Ce的粒徑為10-90μm,B的粒徑為10-110μm;步驟三,燒結:將步驟二所制得的合金粉體基體在氬氣氣氛燒結爐中燒結成型,在燒結過程,首先以10-15℃/min的升溫速率在400-500℃預燒1-3h,然后以30-40℃/min的升溫速率在1250-1350℃燒結5-8h得到基礎合金;步驟四,淬火:將步驟三燒結的基礎合金置于淬火爐內進行淬火處理,首先在淬火溫度為1100-1200℃保溫時間15-25min,之后在5-10min內降溫至50-80℃保溫時間30-40min;步驟五,退火處理:將步驟四淬火得到的基礎合金置于氬氣氣氛的退火爐中,首先加熱到450-455℃,保溫1-2h,再次加熱到525-535℃,保溫2-3h,然后加熱到720℃,保溫3-4h,停止加熱,在30-40min內將溫度降至150-170℃,然后自然冷卻至室溫得到合金;步驟六,加工:將步驟五所制得的合金進行切割加工制得所需形狀的線圈。該實施例的優選合金的配比為:(Fe0.6Co0.4)50(Ni0.65Al0.3Ce0.05)35Cu3B6Si3Cr3;更加優選該合金的結構為:該合金形成了α-Fe相、摻雜Co的α-Fe相和非晶相組成,其中α-Fe相和摻雜Co的α-Fe相組成第一相,第一相中α-Fe相和摻雜Co的α-Fe相的顆粒尺寸在1-15nm之間,第一相與非晶相之間形成了一個界面相,其中第一相的飽和磁化強度約為1.52T,相界面為一個厚度為1-1.5nm的界面,其中Ni在第一相中的含量為在非晶相中的含量的1.5倍。步驟一中,優選的球磨時間為152h。步驟五中更加優選,將步驟四淬火得到的基礎合金置于氬氣氣氛的退火爐中,首先加熱至455℃,保溫1.5h,之后再次加熱至530℃,保溫2.5h,然后加熱到720℃,保溫3.5h,停止加熱,在30-40min內將溫度降至150-170℃,然后自然冷卻至室溫得到合金。【性能測試】(一)步驟一所制得的納米合金粉體:采用日本RikenDenshi公司ModeIBHV-525型振動樣品磁強計(VSM)測量樣品的磁性能。1、通過研究球磨后的XRD譜線發現,在球磨至一段時間后Ni、Cr和Cu的衍射峰將出現基本消失的情形,這是由于隨著球磨時間的增加,Fe形成過飽和固溶體,晶體的完整性受到破壞,使得參與衍射的晶粒減少而導致峰高逐漸降低,Ni、Cr和Cu的衍射峰降低直至基本消失,說明Ni、Cr和Cu固溶于Fe中,形成Fe的過飽和固溶體,研究還發現這種情形的出現,對于Cr含量和球磨時間是成反比的;但是球磨后期的顆粒硬化,內應力增大,當達到彈性極限時,顆粒開始碎化,在粉末不斷細化的同時,伴隨著粉末團聚現象的產生,這是由于球磨過程中,形成了很多納米級粉末,而尺寸達到納米級的粉末的表面能和吸附能增加,從而造成團聚現象,因此該在該配比下最佳的球磨時間為152h;2、如表1所述隨著Cr含量的上升Fe-Ni-Cu-Cr的合金的飽和磁化強度先上升后下降,在Cr含量為3-6%時達到最大值,5%時達到最大值172(σs/A·m2·kg-1);這是因為,當Cr含量增加,會導致合金中長程有序鐵磁性相增加,但是Cr元素不具有磁矩,所以比飽和磁化強度隨著Cr含量的增加先上升后下降的情形;隨著Cr含量的上升該合金的磁導率變化量實現先上升后下降的趨勢,得到含量為5%時為飽和磁化強度與磁導率最優的配比。表1納米合金粉體的性能測試:Cr含量飽和磁化強度(σs/A·m2·kg-1)磁導率增長量0%1240%1%1471%3%1512%5%1723%7%1501.5%9%131-1%(二)(1)制備過程中加入了鈰,使得合金中含有Ce元素對Ni進行了摻雜,研究發現由于合金中同時含有Cr、Ni等大原子,當大原子與小原子組合形成合金時候,則能夠生成一種金屬間化合物Laves相,它的不同尺寸原子以最致密的方式堆垛在晶胞中,其硬度較高,有顯著的強化作用,隨著Ce元素的增加,合金中硬質相增加,促使合金中的固溶體組織均勻細化,導致合金在外力的作用下不易折斷和剝落,研究發現含有Ce的合金經過摩擦后合金表面顯得光滑平整,說明摩擦基體對硬質相的支持保護作用加大,硬相不易剝離和脫落,因而提高了抗磨損的能力,磨損量減少,耐磨性比未加Ce的合金提高20%~30%以上,并且增加Ce的含量引起合金體中的奧氏體含量降低,能夠有效改善合金表面的微觀結構,從而提高合金的耐腐蝕性能;但是還發現隨著Ce含量的增加至一定程度后,合金中的耐摩擦性能和耐腐蝕性能增強,但是磁導率呈現下降的趨勢,這是由于Ce增加到一定程度后對于合金的晶粒大小的細化作用減小達到瓶頸,因此隨著Ce含量的增加對于耐摩擦性能增長變緩,如表2所述當Ce含量為1.75%時候為最佳配比,其中合金的配比為(Fe0.6Co0.4)50(Ni0.65Al0.3Ce0.05)35Cu3B6Si3Cr3。磨損試驗:在RRT2III型往復式摩擦磨損機上進行,磨損試驗試樣的對偶件為70mm×1317mm×10mm白剛玉砂條,粒度為200目,試樣表面粗糙度在018~014μm之間。測試速度150r/s,測試壓力28MPa,測試時間10min,每個試樣測試次數1600-1800次,測試行程75m,室溫20-25℃,濕度23-26%,無潤滑干摩擦試驗,磨損量用萬用電子分析天平測試。未添加Ce的合金磨損量為0.019/mg;腐蝕試驗:腐蝕介質選取H2SO4(5%)、HCl(5%)和NaOH(5%),試樣均在微沸狀態下腐蝕24h,采用失重法進行腐蝕試驗,試樣先要打磨拋光,在腐蝕前后用丙酮浸泡、酒精清洗、吹風機吹干后用萬分之一天平稱腐蝕前后的重量,腐蝕率。表2合金性能測試:(三)步驟三中經過二次加熱處理進行燒結,首先進行預熱之后升溫進行正式燒結。經過研究發現二次加熱處理后的初始磁導率要比一次預熱處理后的初始磁導率要好,其磁導率要高于單次加熱的合金5-10%,隨溫度的升高,合金發生結構馳豫,向穩定的低內能狀態轉變。并且二次加熱工藝的加熱速率也需要遠遠高于第一次預熱工藝的加熱速率:“首先以10-15℃/min的升溫速率在400-500℃預燒1-3h,然后以30-40℃/min的升溫速率在1250-1350℃燒結5-8h”優選“首先以12℃/min的升溫速率在400-500℃預燒2h,然后以35℃/min的升溫速率在1250-1350℃燒結7h”,第二次加熱速率幾乎三倍于第一次的加熱速率,通過研究發現由于之前的預熱已經使得合金體具有一定的適應能力,通過快速升溫,使得材料的合金迅速且結晶更加充分,晶粒間的耦合作用更強,從而材料的有效各向異性常數更低,初始磁導率更高。經過實驗得知,采用二次加熱處理進行燒結后的合金初始磁導率要高于單次加熱處理進行燒結后的合金初始磁導率3-7%,采用第二次加熱速率三倍于第一次的加熱速率后得到的合金的初始磁導率相較于普通二次加熱處理進行燒結后的合金初始磁導率提高4-8%;(四)本實用新型中的淬火步驟中的第二階段采用了快速的淬火步驟,通過研究發現,采用了快速的淬火步驟能夠使得合金的性能更加優質,能提高合金的沖擊韌性值及硬度值,且對于磁性能并無影響,該合金在急冷過程中,其材料的內部結構發生相變增韌,Ce元素能夠部分熔解,使得在粘結相中的Ce在急冷情況下來不及析出,起到了固熔強化的作用,能大幅度提高了該合金的沖擊韌性及硬度值。沖擊韌性能夠達到0.72-0.89MJ/m2,其中經過綜合考慮當合金材料的配比為:其中合金的配比為(Fe0.6Co0.4)50(Ni0.65Al0.3Ce0.05)35Cu3B6Si3Cr3,時Ce含量約為1.75%時的沖擊韌性以及各項性能達到最佳,沖擊韌性為0.85MJ/m2,洛氏硬度值為38HRC。(五)經過退火步驟后該合金形成了α-Fe相、摻雜Co的α-Fe相和非晶相組成,其中α-Fe相和摻雜Co的α-Fe相組成第一相,第一相中α-Fe相和摻雜Co的α-Fe相的顆粒尺寸在1-15nm之間,第一相與非晶相之間形成了一個界面相,其中第一相的飽和磁化強度約為1.52T,相界面為一個厚度為1-1.5nm的界面,其中Ni在第一相中的含量為在非晶相中的含量的1.5倍;本實用新型創造性的首先制備納米合金粉體,之后加入金屬進行熔煉,這樣使得Ni能夠進入至由α-Fe相和摻雜Co的α-Fe相組成的第一相中,經過研究發現當Ni在第一相中的含量為在非晶相中的含量的1.5倍時該合金的飽和磁化強度最大,其合金的飽和磁化強度約為1.57T。(1)步驟五中的退火溫度對于合金的晶粒直徑有一定影響。在合金加熱過程中,由于存在不同的金屬元素,經過研究發現首先加熱至455℃,保溫1.5h,先使得第一相中的元素優先成核,之后再次加熱至530℃,保溫2.5h,然后加熱到720℃,保溫3.5h,使得非晶相此時能夠得到均勻細小納米結構。如果再次升溫后發現當溫度升高到750℃時,晶粒尺寸急劇長大,其使磁各向異性增加,同時大晶粒對疇壁的位移、磁矩轉動起阻礙作用。因此本實用新型采用最佳的退火溫度為“首先加熱至455℃,保溫1.5h,先使得第一相中的元素優先成核,之后再次加熱至530℃,保溫2.5h,然后加熱到720℃,保溫3.5h”。(2)研究發現在進行退火的過程中需要進行保溫程序,但是保溫的時間與本實用新型合金的磁性能具有很大的關系,隨著保溫時間的延長,磁性能下降。由于在合金的內部存在很大的內應力,且不同部位固化推進方式不同而形成區域應力場,在720℃保溫3-4h后(最佳保溫時間為3.5h),合金的內應力可以達到充分的釋放,磁晶各相異性能降低,合金內部的亞穩定結構趨于穩定,而使合金表現出優良的軟磁性能。但在720℃保溫超過4h后,由于出現了惡化磁性能的析出相,導致合金磁性能下降。以上所述僅為本實用新型的優選實施例,并非因此限制本實用新型的專利范圍,凡是在本實用新型的實用新型構思下,利用本實用新型說明書及附圖內容所作的等效結構變換,或直接/間接運用在其他相關的
技術領域:
均包括在本實用新型的專利保護范圍內。當前第1頁1 2 3