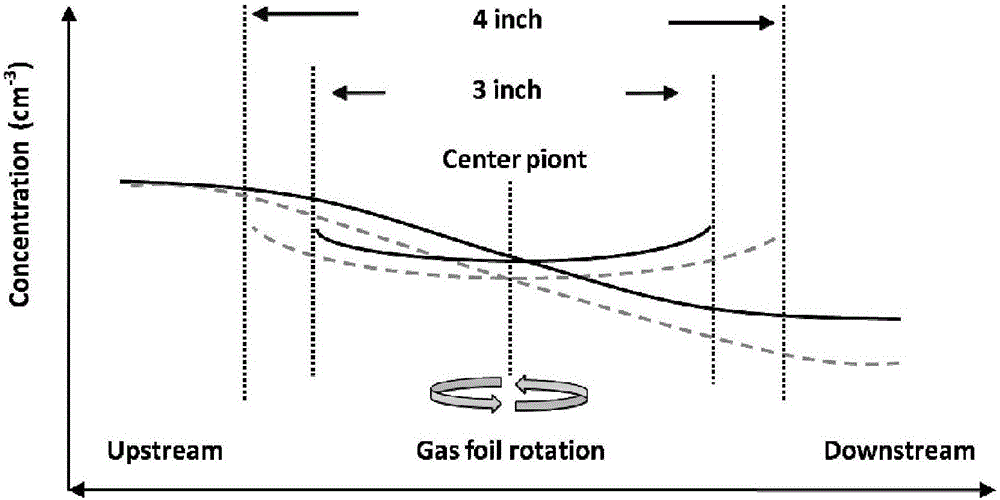
本發明涉及一種碳化硅外延片的生長方法,尤其涉及一種提高碳化硅外延兼容性的方法。
背景技術:
:SiC是繼Si和GaAs等材料之后發展起來的第三代新型半導體材料,室溫下SiC禁帶寬度達3.0eV,擊穿電場強度達3×106V/cm,熱導率達4.9W/cm·℃,電子飽和漂移速度達2×107cm/s。優越的材料特性使得SiC成為高性能電子器件的理想材料。經過十幾年的發展,SiC外延晶片尺寸、晶體質量、均勻性等指標有了大幅的提升,目前商業化的SiC襯底尺寸已經上升至6英寸,但是大部分的SiC器件研制流水線依舊為3英寸或4英寸,因此SiC外延材料要求覆蓋3-6英寸。目前商用SiC外延爐大部分為水平式外延爐,源在進氣方向的耗盡導致源在襯底上方分布不均勻,通常采用氣浮旋轉的方式來降低由于源耗盡引起的不均勻性。源在反應室基座和襯底上的耗盡速率不同,通常源在基座上的耗盡速率小于在襯底上的耗盡速率,因此襯底邊緣存在源濃度變化不連續的點,形成邊緣效應。對比不同外延尺寸的襯底,由于基座區域和襯底區域的比例不同,造成外延片中心點性能參數不同。如圖1所示,長實線和長虛線分別對應3英寸和4英寸外延片的源耗盡曲線。由于3英寸基座區域的比例較大,3英寸襯底上方的源濃度要高于4英寸襯底上方相同位置的源濃度。因此即使采用相同的工藝條件,采用氣浮旋轉的3英寸襯底和4英寸襯底生長出來的外延片性能參數也是不同的,如圖1中短實線和短虛線所示。同時由于源耗盡速率在基座和襯底邊緣的不連續性,襯底邊緣存在很強的邊緣效應。技術實現要素:發明目的:針對以上問題,本發明提出一種提高碳化硅外延兼容性的方法。技術方案:為實現本發明的目的,本發明所采用的技術方案是:一種提高碳化硅外延兼容性的方法,包含以下步驟:(1)選用外延爐支持的最大尺寸的石墨基座;(2)基座中放入碳化硅襯底,根據襯底尺寸在石墨基座的襯底坑中放入合適尺寸的填充片,用于固定襯底;襯底尺寸與石墨基座尺寸相同時,不需要放入填充片;(3)將石墨基座放入反應室大盤內,將反應室中的空氣置換為氬氣,再將反應室抽至真空后通入氫氣,保持氫氣流量為60-120L/min;等系統升溫至1300-1450℃時,將反應室的壓力設置為100-200mbar,繼續向反應室通入氯化氫氣體,保持HCl/H2的流量比范圍為0.01%-0.25%;(4)等系統繼續升溫至1500-1550℃時,關閉氯化氫氣體,同時保持氫氣流量和反應室壓力不變;(5)系統繼續升溫,達到生長溫度1570-1680℃后,維持生長溫度2~10分鐘;(6)向反應室通入硅源和碳源,控制硅源和氫氣的流量比小于0.025%;調節碳源流量,控制進氣端C/Si比小于等于1,通入氯化氫氣體,控制Cl/Si比為2-6,通入氮氣,生長n型緩沖層;(7)采用線性緩變的方式改變生長源和摻雜源的流量,至生長外延結構所需的設定值,生長外延結構;(8)完成外延結構的生長后,關閉生長源和摻雜源,在氫氣氛圍中將反應室溫度降至室溫,反應室溫度達到室溫后將反應室抽至真空,再向反應室中充入氬氣,將反應室充至大氣壓,然后打開反應室,取出外延片。填充片是選用與放置在基座上的碳化硅襯底具有相同的摻雜類型、晶面晶向、表面形貌和厚度以及與基座具有相同尺寸的碳化硅襯底,在中心位置加工出與基座上的碳化硅襯底尺寸相同的圓形空位,圓形空位的直徑為基座上的碳化硅襯底直徑的1.05-1.1倍。填充片可以重復使用,重復使用過程中,當填充片的外延厚度達到200-500微米,進行機械拋光或化學機械拋光,去除填充片上的外延層。有益效果:本發明的方法通過引入和襯底具有相同摻雜類型、晶面晶向以及表面形貌的填充片的方式,使襯底區域得以延伸,從而使不同尺寸襯底對應的基座以及襯底區域比例接近,使源在實際襯底上的耗盡速率連續變化,避免邊緣效應。同時通過填充片的引入,使得源在不同尺寸襯底上方相同位置的濃度相似,從而提高了不同尺寸基座的兼容性,減少不同尺寸外延爐間的濃度以及厚度標定頻率;同時也可在多片式外延爐中實現不同尺寸襯底的同時生長,極大程度的減少了片間偏差。該發明簡單可行,不需要對外延系統做改變,適用于現有單片以及多片式外延爐。附圖說明圖1是未加填充片的襯底上方的源耗盡曲線;圖2是填充片的示意圖;圖3是增加填充片前后襯底上方的源耗盡曲線的對比圖。具體實施方式下面結合附圖和實施例對本發明的技術方案作進一步的說明。本發明所述的提高碳化硅外延兼容性的方法,是在使用時選擇外延爐支持的最大尺寸的石墨基座。當放入小尺寸襯底時,放入合適尺寸的填充片,當襯底尺寸和基座尺寸相同時,則不需要加入填充片。如圖2所示,選用系統配套的6英寸石墨基座,放入3英寸或者4英寸襯底時,需要加入相應尺寸的填充片。放入6英寸襯底時,則不需要加入填充片。加入填充片可以解決不同尺寸SiC襯底外延性質不同的問題,也可以降低外延過程中的邊緣效應。填充片的加工方法是選用6英寸碳化硅襯底,利用激光切割或者金剛石劃片的方法在6英寸碳化硅襯底的中心位置加工出小尺寸襯底的空位,該空位的圓心位置和6英寸碳化硅襯底的圓心位置重疊。加工填充片所選用的6英寸碳化硅襯底與放置在基座上的小尺寸襯底具有相同的摻雜類型、晶面晶向、表面形貌和厚度。通過引入和襯底具有相同摻雜類型、晶面晶向以及表面形貌的填充片,使襯底區域得以延伸,從而使不同尺寸襯底對應的基座以及襯底區域比例接近,使源在實際襯底上的耗盡速率連續變化,避免邊緣效應。同時填充片的引入,使得源在不同尺寸襯底上方相同位置的濃度相似,可以很好的提高基座的兼容性。填充片中間的空位可以是正圓形也可以是帶參考邊的圓形,帶參考邊的空位直徑為對應襯底直徑的1.05-1.1倍,預留空隙,方便填充片的放置,避免因為熱脹冷縮發生擠壓。實際生長外延層時,使用單片式外延爐或者行星式多片式外延爐,選用外延爐支持的最大尺寸的石墨基座,將碳化硅襯底置于石墨基座內,在石墨基座內放入合適尺寸的填充片,利用填充片固定襯底,可以選取偏向<11-20>方向4°或者8°的碳化硅襯底。然后將石墨基座放入反應室大盤內,將反應室大盤內的空氣置換為氬氣,再將反應室抽至真空后向反應室內通入氫氣,保持H2的流量為60~120L/min,等系統升溫至1300-1450℃時,將反應室的壓力設置為100-200mbar,繼續向反應室通入少量氯化氫(HCl)氣體,保持HCl/H2的流量比范圍為0.01%-0.25%。等系統繼續升溫至1500-1550℃時,關閉氯化氫氣體,同時保持氫氣和反應室壓力不變,讓系統繼續升溫,當系統達到生長溫度1570-1680℃后,維持生長溫度2~10分鐘。之后向反應室通入小流量硅源和碳源,可以是硅烷和乙烯,控制硅源和氫氣的流量比小于0.025%,調節碳源流量,控制進氣端C/Si比小于等于1,通入氯化氫(HCl)氣體,控制Cl/Si比為2~6,通入高純氮氣(N2),生長出厚度為0.5-2μm,摻雜濃度為~1E18cm-3的n型緩沖層。采用線性緩變的方式改變生長源和摻雜源的流量,至生長外延結構所需的設定值,控制SiH4/H2流量比為0.2%,設定進氣端C/Si比為1.05,并通入氯化氫(HCl)氣體,設定進氣端Cl/Si比為2.5,通入5sccm的氮氣,外延時間設定為60分鐘,生長外延結構。完成外延結構的生長后,關閉生長源和摻雜源,在氫氣氛圍中將反應室溫度降至室溫,反應室溫度達到室溫后將氫氣排出反應室,將反應室抽至真空,維持3-10分鐘,再向反應室中充入氬氣,最終用氬氣將反應室充至大氣壓,然后打開反應室,取出外延片。填充片可以重復使用,重復使用過程中,當填充片的外延厚度累計達到200-500微米,一般200微米左右就要進行處理,不能超過500微米,一般進行機械拋光或化學機械拋光,去除填充片上的外延層,達到和襯底相同的表面現象。如圖3所示,其中點狀虛線表示加入填充片后3英寸和4英寸襯底上方相同位置的源耗盡分布曲線;實線和線狀虛線和圖1中一樣,長實線和長虛線分別對應3英寸和4英寸外延片的源耗盡曲線,短實線和短虛線表示采用氣浮旋轉的3英寸襯底和4英寸襯底上方相同位置的源耗盡分布曲線。對同一個外延爐生長3英寸、4英寸和6英寸外延片的中心點進行濃度和厚度測試,如表1所示。表1樣品3英寸4英寸6英寸厚度(μm)29.3528.9628.06濃度(×1015cm-3)4.1E154.03E153.98E15結合圖3和表1中的數據可以看出,采用本發明的方法,可以有效提高不同尺寸碳化硅外延的兼容性。當前第1頁1 2 3