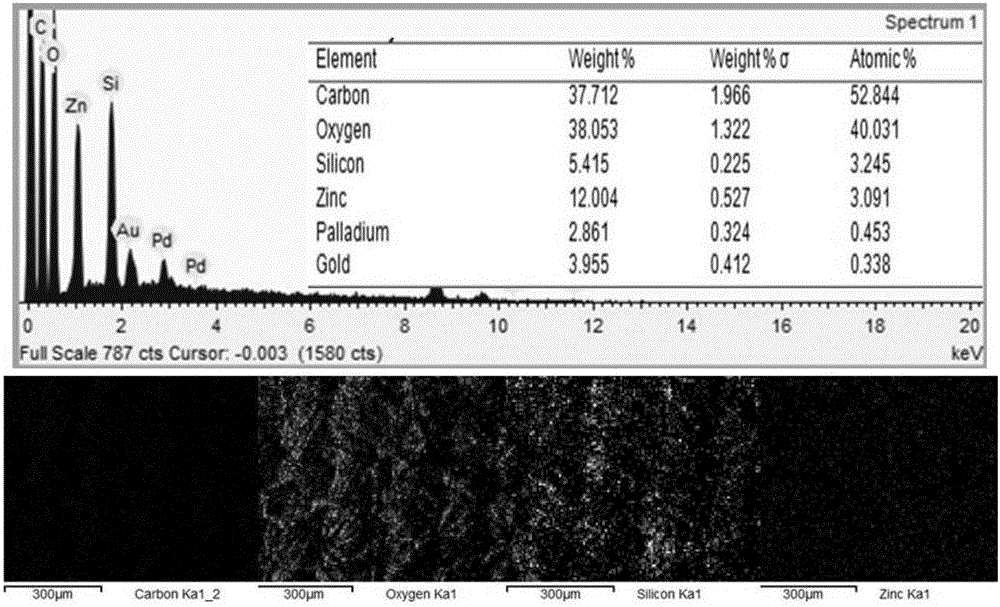
本發(fā)明涉及納米材料領(lǐng)域,尤其涉及ZnO納米材料織物的生產(chǎn)方法及ZnO納米材料織物。
背景技術(shù):
:紫外線(簡稱UV)按輻射波長可分為長波紫外線UVA(320~400nm)、中波紫外線UVB(280~320nm)和短波紫外線UVC(200~280nm),其中,容易對人體造成傷害的紫外線波長段為290~400nm。如果紫外光線在織物上吸收率和反射率越高,那么紫外線透過率越低,產(chǎn)品的防護(hù)性能越好。目前紡織品紫外線防護(hù)的機(jī)理主要來源于纖維織物本身對紫外線的吸收屏蔽作用,或利用屏蔽劑對紫外線進(jìn)行吸收和反射。利用屏蔽劑的處理可獲得優(yōu)良的抗紫外線性能,主要的處理方法有2種:一是在纖維成形時加入無機(jī)或有機(jī)屏蔽劑,制作成抗紫外線纖維;二是選用紫外線屏蔽劑將織物經(jīng)浸軋或涂層整理賦予織物抗紫外線功能。然而前者的處理技術(shù)要求高、成本大,多以聚酯和聚丙烯為基材,難以應(yīng)用于天然纖維,且在混紡時效果難以控制;后者的產(chǎn)品功能耐洗滌程度差,織物風(fēng)格受到影響,均不大適合用于以輕薄、透氣、吸濕等性能為主的夏季服裝面料。自1997年德國植物學(xué)家Barthlott發(fā)現(xiàn)荷葉表面的自清潔效應(yīng)和超疏水現(xiàn)象以來,超疏水表面已經(jīng)引起了科研人員極大的興趣和廣泛的關(guān)注。所謂超疏水表面是指與水滴的接觸角大于150°且滾動角小于10°的表面。研究發(fā)現(xiàn),這些超疏水表面的微納米結(jié)構(gòu)對超疏水性起著至關(guān)重要的作用。納米ZnO具有抗紫外性,抗菌性,化學(xué)穩(wěn)定性,熱穩(wěn)定性,無毒性等,近年來被廣泛用在抗紫外材料,紡織領(lǐng)域。目前,最主要的是兩步生長法ZnO表面,然而這種方法操作難度較大,成品率低,織物上的納米ZnO層分布不均。技術(shù)實(shí)現(xiàn)要素:本發(fā)明解決的技術(shù)問題是提供一種操作簡便的ZnO納米材料織物的生產(chǎn)方法。本發(fā)明解決其技術(shù)問題所采用的技術(shù)方案是:ZnO納米材料織物的生產(chǎn)方法,包括以下步驟:(1)將織物浸泡在PDMS溶液中,然后取出烘干;(2)將醋酸鋅和維生素C溶解在水中并攪拌均勻,制成第一溶液,接著向第一溶液中加入氫氧化鈉的水溶液,形成第二溶液,將步驟(1)的織物放入第二溶液內(nèi)進(jìn)行反應(yīng),然后取出清洗并烘干,制得具有納米ZnO層的織物;(3)將所述具有納米ZnO顆粒層的織物再浸泡在PDMS溶液中,然后取出烘干。上述PDMS是聚二甲基硅氧烷。上述步驟3是為了使納米ZnO層與織物接合的更加牢固。上述織物的種類可應(yīng)用現(xiàn)有種類的織物,尤其適合耐堿類織物。進(jìn)一步的是:步驟(1)中,浸泡時間為1-10分鐘,烘干溫度為80-150℃;步驟(2)中,反應(yīng)溫度控制在50-200℃,反應(yīng)時間控制為1-10h,烘干溫度為80-150℃。步驟(3)中,浸泡時間為1-10分鐘,取出后烘干溫度為80-150℃。進(jìn)一步的是:步驟(1)中,PDMS溶液的配比為:每100ml四氫呋喃中溶解1-2mlPDMS;步驟(2)中,第一溶液的配比為:每100ml去離子水中溶解1-5g醋酸鋅和1-5g維生素C,氫氧化鈉的水溶液的配比為:每100ml去離子水中溶解1-5g氫氧化鈉;步驟(3)中,PDMS溶液的配比為:每100ml四氫呋喃中溶解1-2mlPDMS。本發(fā)明還提供了ZnO納米材料織物,所述ZnO納米材料織物是通過上述生產(chǎn)方法制得。本發(fā)明的有益效果是:(1)操作簡便,制備的ZnO顆粒層耐久性好,解決了許多傳統(tǒng)方法制備工序復(fù)雜,耗時長,穩(wěn)定性,機(jī)械性能差等問題。(2)PDMS修飾納米ZnO織物在短時間內(nèi)就獲得了超疏水自清潔表面,此外,織物表面表現(xiàn)出良好的油水分離現(xiàn)象,并在外力摩擦下,擁有持久的超疏水性能。(3)本發(fā)明的織物可為多種類型的織物。而棉纖維織物可作為一種選擇,棉纖維素是世界上豐富的資源,成本費(fèi),可生物降解性,耐化學(xué)性好,無毒害,可直接與食物接觸,解決了原料成本高,環(huán)境污染嚴(yán)重等問題,并可在無損失液體運(yùn)輸,微量吸液管,防污染,抗紫外材料,超疏水紡織品,油水分離材料等領(lǐng)域廣泛應(yīng)用。附圖說明為了更清楚地說明本發(fā)明實(shí)施例的技術(shù)方案,下面將對實(shí)施例描述中所需要使用的附圖做簡單的介紹,顯而易見的下面描述中的附圖僅僅是本發(fā)明的一些實(shí)施例,對于本領(lǐng)域普通技術(shù)人員來講,在不付出創(chuàng)造性勞動的前提下,還可以根據(jù)這些附圖獲得其他的附圖。其中,圖1為本發(fā)明所述的ZnO納米材料織物的生產(chǎn)方法的步驟示意圖;圖2為本發(fā)明所述的織物表面Zn元素分布以及EDS能譜圖;圖3為本發(fā)明所述的織物表面紅外測試結(jié)果圖;圖4為本發(fā)明所述的織物表面的形貌及接觸角;圖5為按照本發(fā)明的方法在120℃時,油浴6小時制備的織物表面按照AATCC標(biāo)準(zhǔn)水洗一次至十次的接觸角變化趨勢圖;圖6為按照本發(fā)明的方法在120℃時,油浴6小時制備的織物表面摩擦30次至300次接觸角變化趨勢圖。具體實(shí)施方法為使本發(fā)明的上述目的、特征和優(yōu)點(diǎn)能夠更加明顯易懂,下面結(jié)合具體實(shí)施方式對本發(fā)明作進(jìn)一步詳細(xì)的說明。如圖1所示,本發(fā)明的方法包括:步驟一:PDMS修飾清洗干凈的純棉布在一個實(shí)施例中,該步驟可以具體如下執(zhí)行:先將織物按照3×3cm規(guī)格裁剪數(shù)塊,并置于燒杯中一次經(jīng)過去離子水,無水乙醇超聲5min,超聲完畢后放入烘箱80℃干燥,冷卻備用。將2~10ml的PDMS溶于500ml的四氫呋喃中,在磁力轉(zhuǎn)子的作用下持續(xù)攪拌1h,向溶液中加入依次經(jīng)過水、無水乙醇清洗,并烘干備用的織物,浸泡2min;取出80℃烘干。步驟二:油浴法制得具有納米ZnO顆粒層表面的織物在一個實(shí)施例中,該步驟可以具體如下執(zhí)行:將1~5g醋酸鋅,1~5g維生素C溶解在100ml去離子水中在磁力轉(zhuǎn)子的作用下攪拌均勻,然后向其中加入含1~5gNaOH的100ml水溶液,然后將配置好的溶液裝在圓底燒瓶中,在圓底燒瓶中加入依次經(jīng)過水,無水乙醇清洗以及PDMS修飾的純棉布,80~150℃溫度下反應(yīng)1~6h,然后取出清洗并80℃烘干。步驟三:PDMS修飾制得具有紫外防護(hù)和耐水洗特殊浸潤性功能織物表面的織物。在一個實(shí)施例中,該步驟可以具體如下執(zhí)行:將制得的具有ZnO顆粒層表面的織物浸泡在步驟一所得的PDMS的四氫呋喃溶液中2min,取出80℃烘干,并150℃熱處理5h。上述步驟過程可參閱圖1,如圖1所示,棉織物首先經(jīng)過PDMS修飾然后經(jīng)油浴構(gòu)建二階微納米結(jié)構(gòu)ZnO棉織物表面,最后再經(jīng)PDMS修飾獲得超疏水自清潔功能織物表面。上述步驟所得實(shí)驗(yàn)結(jié)果可參閱圖2至圖5。圖2為本發(fā)明所得織物表面的Zn與Si元素分布以及EDS能譜圖。如圖2所示,上方為制備的微納結(jié)構(gòu)ZnO棉織物表面元素含量譜圖;下方為制備的微納結(jié)構(gòu)ZnO棉織物表面元素Zn與Si的分布圖,嵌入的SEM為織物掃描范圍,依次往右為元素C,O分布圖。圖3為本發(fā)明織物表面紅外測試結(jié)果圖。圖4為本發(fā)明織物表面的形貌及接觸角。如圖4所示,制備的特殊浸潤性功能織物表面呈現(xiàn)出小顆粒狀的微納結(jié)構(gòu),獲得超疏水表面,接觸角達(dá)到165°以上。為使本發(fā)明的上述目的,特征和優(yōu)點(diǎn)能夠更加明顯易懂,下面結(jié)合附圖和實(shí)施例進(jìn)一步說明本發(fā)明的技術(shù)方案。但是本發(fā)明不限于所列出的實(shí)施例,還應(yīng)包括在本發(fā)明所要求的權(quán)利范圍內(nèi)其他任何公知的改變。首先,此處所稱的“一個實(shí)施例”或“實(shí)施例”是指可包含于本發(fā)明至少一個實(shí)現(xiàn)方式的特定特征,結(jié)構(gòu)或特性。在本說明書中不同地方出現(xiàn)的“在一個實(shí)例中”并非均指一個實(shí)施例,也不是單獨(dú)的或選擇性的與其他實(shí)施例互相排斥的實(shí)施例。其次,本發(fā)明利用結(jié)構(gòu)示意圖等進(jìn)行詳細(xì)描述,在詳述本發(fā)明實(shí)施例時,為便于說明,示意圖會不依一般作局部放大,而且所述示意圖只是實(shí)例,其再次不應(yīng)限制本發(fā)明保護(hù)的范圍。此外,在實(shí)際制作中應(yīng)包含長度,寬度及深度的三維空間。另外,本發(fā)明中所講的字母簡稱,均為本領(lǐng)域固定簡稱,其中部分字母文解釋如下:PDMS:聚二甲基硅烷;SEM圖:電子掃描顯像圖;EDS圖:能譜圖。實(shí)施例一:步驟一:PDMS修飾清洗干凈的純棉布。在一個實(shí)施例中,該步驟可以具體如下執(zhí)行:先將織物按照3×3cm規(guī)格裁剪數(shù)塊,并置于燒杯中一次經(jīng)過去離子水,無水乙醇超聲5min,超聲完畢后放入烘箱80℃干燥,冷卻備用。將3ml的PDMS溶于500ml的四氫呋喃中,在磁力轉(zhuǎn)子的作用下持續(xù)攪拌1h,向溶液中加入依次經(jīng)過水,無水乙醇清洗,并烘干備用的織物,浸泡2min;取出80℃烘干。步驟二:油浴法制得具有納米ZnO顆粒層表面的織物。在一個實(shí)施例中,該步驟可以具體如下執(zhí)行:將2g醋酸鋅,1.5g維生素C溶解在100ml去離子水中在磁力轉(zhuǎn)子的作用下攪拌均勻,然后向其中加入含2gNaOH的100ml水溶液,然后將配置好的溶液裝在圓底燒瓶中,在圓底燒瓶中加入依次經(jīng)過水,無水乙醇清洗以及PDMS修飾的純棉布,120℃溫度下反應(yīng)3h。然后取出清洗并烘干。步驟三:再次PDMS修飾制得具有紫外防護(hù),抗菌性和耐水洗特殊浸潤性功能織物表面的織物。在一個實(shí)施例中,該步驟可以具體如下執(zhí)行:將制得的ZnO顆粒層的表面的織物浸泡在步驟一所得的PDMS的四氫呋喃溶液中2min,取出80℃烘干,并150℃熱處理2h。實(shí)施例二:步驟一:PDMS修飾清洗干凈的純棉布。在一個實(shí)施例中,該步驟可以具體如下執(zhí)行:先將織物按照3×3cm規(guī)格裁剪數(shù)塊,并置于燒杯中一次經(jīng)過去離子水,無水乙醇超聲5min,超聲完畢后放入烘箱80℃干燥,冷卻備用。將5ml的PDMS溶于500ml的四氫呋喃中,在磁力轉(zhuǎn)子的作用下持續(xù)攪拌1h,向溶液中加入依次經(jīng)過水,無水乙醇清洗,并烘干備用的織物,浸泡2min;取出100℃烘干。步驟二:油浴法制得具有納米ZnO顆粒層表面的織物。在一個實(shí)施例中,該步驟可以具體如下執(zhí)行:將4g醋酸鋅,3g維生素C溶解在100ml去離子水中在磁力轉(zhuǎn)子的作用下攪拌均勻,然后向其中加入含4gNaOH的100ml水溶液,然后將配置好的溶液裝在圓底燒瓶中,在圓底燒瓶中加入依次經(jīng)過水,無水乙醇清洗以及PDMS修飾的純棉布,120℃溫度下反應(yīng)4h。然后取出清洗并烘干。步驟三:再次PDMS修飾制得具有紫外防護(hù)和耐水洗特殊浸潤性功能織物表面的織物。在一個實(shí)施例中,該步驟可以具體如下執(zhí)行:將制得的納米ZnO顆粒層表面的織物浸泡在步驟一所得的PDMS的四氫呋喃溶液中2min,取出80℃烘干,并150℃熱處理4h。實(shí)施例三:步驟一:PDMS修飾清洗干凈的純棉布。在一個實(shí)施例中,該步驟可以具體如下執(zhí)行:先將織物按照3×3cm規(guī)格裁剪數(shù)塊,并置于燒杯中一次經(jīng)過去離子水,無水乙醇超聲5min,超聲完畢后放入烘箱80℃干燥,冷卻備用。將7ml的PDMS溶于500ml的四氫呋喃中,在磁力轉(zhuǎn)子的作用下持續(xù)攪拌1h,向溶液中加入依次經(jīng)過水,無水乙醇清洗,并烘干備用的織物,浸泡2min;取出100℃烘干。步驟二:油浴法制得具有納米ZnO顆粒層表面的織物。在一個實(shí)施例中,該步驟可以具體如下執(zhí)行:將5g醋酸鋅,4g維生素C溶解在100ml去離子水中在磁力轉(zhuǎn)子的作用下攪拌均勻,然后向其中加入含5gNaOH的100ml水溶液,然后將配置好的溶液裝在圓底燒瓶中,在圓底燒瓶中加入依次經(jīng)過水,無水乙醇清洗以及PDMS修飾的純棉布,140℃溫度下反應(yīng)6h。然后取出清洗并烘干。步驟三:再次PDMS修飾制得具有紫外防護(hù)和耐水洗特殊浸潤性功能織物表面的織物。在一個實(shí)施例中,該步驟可以具體如下執(zhí)行:將制得的ZnO顆粒層的表面的織物浸泡在步驟一所得的PDMS的四氫呋喃溶液中2min,取出80℃烘干,并150℃熱處理4h。實(shí)施例四:步驟一:PDMS修飾清洗干凈的純棉布。在一個實(shí)施例中,該步驟可以具體如下執(zhí)行:先將織物按照3×3cm規(guī)格裁剪數(shù)塊,并置于燒杯中一次經(jīng)過去離子水,無水乙醇超聲5min,超聲完畢后放入烘箱80℃干燥,冷卻備用。將10ml的PDMS溶于500ml的四氫呋喃中,在磁力轉(zhuǎn)子的作用下持續(xù)攪拌1h,向溶液中加入依次經(jīng)過水,無水乙醇清洗,并烘干備用的織物,浸泡5min;取出100℃烘干。步驟二:油浴法制得具有納米ZnO顆粒層表面的織物在一個實(shí)施例中,該步驟可以具體如下執(zhí)行:將5g醋酸鋅,4g維生素C溶解在100ml去離子水中在磁力轉(zhuǎn)子的作用下攪拌均勻,然后向其中加入含5gNaOH的100ml水溶液,然后將配置好的溶液裝在圓底燒瓶中,在圓底燒瓶中加入依次經(jīng)過水,無水乙醇清洗以及PDMS修飾的純棉布,150℃溫度下反應(yīng)7h。然后取出并清洗烘干。步驟三:再次PDMS修飾制得具有紫外防護(hù)和耐水洗特殊浸潤性功能織物表面的織物。在一個實(shí)施例中,該步驟可以具體如下執(zhí)行:將制得的ZnO顆粒層的表面的織物浸泡在步驟一所得的PDMS的四氫呋喃溶液中2min,取出80℃烘干,并150℃熱處理5h。下表為本發(fā)明的織物表面的紫外防護(hù)性能數(shù)據(jù):SampleUPFT(UVA)T(UVB)UPFRating純棉布3.8932.24%24.09%0PDMS4.0631.31%23.14%0PDMS+ZnO51.882.23%1.91%50+PDMS+ZnO+PDMS48.812.66%2.01%45表1如表1所示,未做任何處理的空白樣防紫外系數(shù)為0,而修飾PDMS后制得的樣品防紫外能力依然為0,經(jīng)過油浴后制得表面與納米ZnO顆粒層的棉織物獲得極佳的防紫外效果,并且納米ZnO無毒無害,可直接與皮膚接觸,適合在防紫外紡織品、功能性材料等領(lǐng)域推廣和應(yīng)用。在以上實(shí)施例中,制得的紫外防護(hù)和耐水洗特殊浸潤性功能織物表面在外界摩擦以及水洗作用下具有持久的疏水性。如圖5所示,按照AATCC標(biāo)準(zhǔn)的2A方法制備的油浴150℃水洗一次至十次的特殊浸潤性功能織物表面與水的接觸角變化趨勢,從圖5可以看出,十次加強(qiáng)水洗后樣品保持了較好的疏水性,織物表面經(jīng)緯組織點(diǎn)是最易受到摩擦破壞的位置,在這些位置納米ZnO顆粒發(fā)生脫落或破壞,導(dǎo)致棉織物疏水性能有小幅度下降。如圖6所示,制備的樣摩擦30次至300次的特殊浸潤性功能織物表面與水的接觸角變化趨勢,從圖6可以看出,三百次摩擦后樣品保持了較好的疏水性,織物表面經(jīng)緯組織點(diǎn)是最易受到摩擦破壞的位置,在這些位置納米ZnO顆粒在機(jī)械外力的作用下發(fā)生脫落或破壞,表面形貌發(fā)生破壞,導(dǎo)致棉織物疏水性能有小幅度下降。綜上所述,本發(fā)明的方法在現(xiàn)有技術(shù)基礎(chǔ)上充分利用了PDMS修飾與油浴方法構(gòu)建微納級二階ZnO織物粗糙結(jié)構(gòu)表面,獲得超疏水自清潔與油水分離功能表面。其反應(yīng)條件溫和,工藝簡便易操作,制備的納米ZnO形貌可控,摩擦水洗后超疏水性能優(yōu)良,對環(huán)境無污染,具有良好的應(yīng)用前景,能在無損失液體運(yùn)輸,微量吸液管,防紫外產(chǎn)品,功能性材料,自清潔紡織品,油水分離材料等領(lǐng)域得到很好地應(yīng)用。應(yīng)說明的是,以上實(shí)施例僅以說明本發(fā)明的技術(shù)方案而非限制,盡管參照較佳實(shí)施例對本發(fā)明進(jìn)行了詳細(xì)說明,本領(lǐng)域的普通技術(shù)人員應(yīng)當(dāng)理解,可對本發(fā)明的技術(shù)方案進(jìn)行修改或者等同替換,而不脫離本發(fā)明技術(shù)方案的精神和范圍,其均應(yīng)涵蓋在本發(fā)明的權(quán)利要求范圍當(dāng)中。當(dāng)前第1頁1 2 3