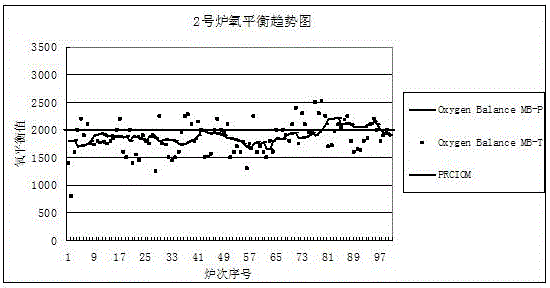
本發明涉及一種解決轉爐自動化煉鋼氧槍工作氧壓不穩定的方法,特別是采用模擬量控制的方式解決轉爐自動化煉鋼吹煉工作氧壓不穩定的問題,屬冶金自動化,屬于轉爐煉鋼自動化控制
技術領域:
。
背景技術:
::轉爐煉鋼的目的是對兌入轉爐的鐵水和廢鋼等原料,通過氧槍連續吹氧的方式,不斷降低原料中的碳含量和提升溫度的過程。在轉爐出鋼前的冶煉終點,能否直接出鋼的判斷依據,是鋼水碳含量和溫度能否滿足目標要求;因此,能準確判斷冶煉過程和終點鋼水碳含量是轉爐煉鋼的關鍵,冶煉終點命中率高的控制技術能減少補吹和倒爐取樣的次數,可有效地縮短冶煉時間,提高轉爐產量,降低生產成本,是轉爐煉鋼的關鍵技術。例如:某廠轉爐氧槍供氧管道受場地空間限制,孔板流量計的布置不能滿足計量的準確性,總管氧壓的波動造成流量計量發生大的偏差,而且很不穩定,供氧壓力受氧氣管網壓力波動影響,總管氧壓波動較大,波動范圍在1.3-2.5Mpa,每天均不同程度大范圍波動,給轉爐自動化煉鋼的順利進行造成極大影響。現有的轉爐自動化煉鋼模型,大都采用達涅利自動化煉鋼模型,是按氧氣流量及累計氧氣消耗量及初始輸入物料參數、終點目標參數按照模型來進行自動計算,按計算結果對整個吹煉過程中加料量、吹氧量、加料時機、氧槍槍位變化時機、副槍動作時機、吹煉終點確定等過程進行自動控制,實現自動化煉鋼的目標;所以氧流量的計量穩定及準確性是所有工作的基礎。不同轉爐,不同總管氧壓情況下,要達到相同的工作氧壓,需要的氧氣流量值均不相同,而當設定同一流量值時,氧槍工作氧壓會發生大的波動,造成吹煉無法進行。因此,
背景技術:
的轉爐自動化煉鋼模型難以適應這樣的供氧條件,自動學習的結果常常偏離真實值,轉爐自動化煉鋼模型很難指導生產操作。技術實現要素:本發明的目的是提供一種解決轉爐自動化煉鋼氧槍工作氧壓不穩定的方法,采用模擬計算量替代實際測量值參與自動化煉鋼模型控制,與自動化煉鋼系統實現無縫對接,改善自動化煉鋼效果,提高自動化煉鋼率;在供氧不穩情況下轉爐自動化煉鋼率可實現100%,終點命中率可通過軟件原有的自學習功能不斷得到提高,解決
背景技術:
存在的上述問題。本發明的技術方案是:一種解決轉爐自動化煉鋼氧槍工作氧壓不穩定的方法,通過建立轉爐煉鋼工作氧壓與供氧流量關系的數學模型,根據實際工作氧壓計算供氧流量,并用該計算供氧流量替代儀表測量流量值,參與自動化煉鋼模型控制,實現自動化煉鋼過程的準確控制和穩定操作。包括以下幾個步驟:①計算供氧流量模型的確定基于在供氧管路固定、氧槍參數已確定的情況下,氧槍的流量與噴頭參數及出口氧壓相關的原理,按照流體力學及氣體方程可推導出通過氧槍噴孔的氣體流量公式如下:F0:氧氣流量,m3/minP工作:工作氧壓,MpaT環:氧氣環境溫度,℃Cd:氧槍噴孔流量系數,通常取0.96-0.99N:氧槍噴孔個數A喉:氧槍噴孔喉口面積,mm2通過上述公式計算結果,確定計算供氧流量與工作氧壓的關系;驗證:通過物料平衡計算,與上述計算供氧流量的模擬計算值相比,驗證后基本符合實際,因此,用此計算供氧流量替代流量計測量值,參與自動化冶煉過程控制,能夠準確反應實際氧氣消耗與入爐料條件及終點目標之間的關系;②模型實現采用氧槍工作氧壓及氧氣工作環境溫度按理想氣體方程及噴頭設計流量壓力特性計算供氧流量,用計算供氧流量替代孔板流量計流量,參與轉爐吹煉過程的流量控制,并把計算供氧流量應用到已有的轉爐自動化煉鋼模型上,同時保留孔板流量計流量做為參考,不參與控制。把計算供氧流量應用到已有的轉爐自動化煉鋼模型上,通過修改已有轉爐自動化煉鋼模型的程序實現。依據氧壓與氧流量的關系,經過嵌入程序進行計算,實時產生工作氧壓與供氧流量的對應值,并將計算供氧流量顯示的操作界面上,與副槍自動化煉鋼氧流量控制模型無縫對接,為自動化煉鋼順利進行提供了保障。在轉爐自動化煉鋼模型中設定目標流量,通過自動化煉鋼程序來實時自動調整流量,實現對流量的控制,進而穩定了供氧壓力,避開了總管氧壓大范圍波動對流量表測量值精確度的干擾;副槍系統,通過在每爐吹煉前中期采用靜態模型進行過程控制,利用副槍TSC探頭在不終斷吹煉的情況下直接插入鋼水中進行定C、定溫并取樣分析,利用TSC測量結果和設定終點目標差值在后續的吹煉過程中采用動態控制模式,重新計算后續吹煉用氧量及輔料用量,自動控制吹煉終點,實現轉爐吹煉終點碳、溫度的自動命中。本發明采用吹煉過程氧氣模擬計算供氧流量直接替代儀表測量值,參與轉爐吹煉過程自動化控制,實時根據氧槍工作氧壓計算吹煉過程供氧流量,實現了穩定吹煉過程供氧壓力的目的。本發明的主要創新特點有:(1)不需要增加儀表及穩壓閥組或改造氧氣管道,而是通過模擬計算供氧流量替代測量值實現自動控制氧流量及工作氧壓,因此無需投入,不占空間;(2)計算時間響應快速,可忽略不計;(3)計算供氧流量與實際流量值偏差小,能夠保證自動化煉鋼模型的正確運算;(4)能與現有的達涅利自動化煉鋼模型無縫對接,實現自動化煉鋼。本發明的實用性在于:(1)適用于國內煉鋼轉爐供氧管路設計缺陷或供氧系統壓力波動大,同時配備轉爐副槍自動化煉鋼系統的所有煉鋼廠,采用本方法可快速解決問題,免去巨額改造投資及時間;(2)無額外設備維護費用,全部功能通過現有裝備實現;(3)本方法軟件程序簡單,可自主開發和優化。本發明適用于現有煉鋼廠煉鋼系統供氧氣條件不穩定、自動化煉鋼不能正常進行且無改造空間或無資金改造的情況下使用。本發明積極效果:轉爐自動化煉鋼需要對吹煉過程氧氣流量及工作氧壓進行準確控制,并對數據進行收集、分析,以不斷通過軟件自學習功能自動調整模型參數適應吹煉過程,達到準確控制轉爐煉鋼鋼水終點成份、溫度的目的。當各種因素造成總管供氧壓力波動時,造成吹煉氧氣流量檢測的準確性受到較大的影響,從而影響到自動化煉鋼過程吹氧工作氧壓的巨大波動,被迫使自動化煉鋼不能進行而改用手動控制,自動化煉鋼模型無法應用,大大影響轉爐煉鋼的命中率。本專利申請是不進行任何投資的情況下,采用模擬量參與自動化煉鋼的流量控制,使自動化煉鋼模型脫離總管氧壓波動對其的干擾,實現100%自動化煉鋼,模型不斷得到優化完善,煉鋼終點命中率得到有效提高。附圖說明圖1為本發明實施例計算供氧流量與工作氧壓關系圖;圖2為本發明實施例修改達涅利自動化煉鋼模型程序說明示意圖;圖3為本發明實施例1號爐使用本發明后氧平衡值情況(100爐數據);圖4為本發明實施例2號爐使用本發明后氧平衡值情況(100爐數據)。具體實施方式以下結合附圖,通過實施例對本發明做進一步說明。一種解決轉爐自動化煉鋼氧槍工作氧壓不穩定的方法,通過建立轉爐煉鋼工作氧壓與供氧流量關系的數學模型,根據實際工作氧壓計算供氧流量,并用該計算供氧流量替代儀表測量流量值,參與自動化煉鋼模型控制,實現自動化煉鋼過程的準確控制和穩定操作。包括以下步驟:①計算供氧流量模型的確定基于在供氧管路固定、氧槍參數已確定的情況下,氧槍的流量與噴頭參數及出口氧壓相關的原理,按照流體力學及氣體方程可推導出通過氧槍噴孔的氣體流量公式如下:F0:氧氣流量,m3/minP工作:工作氧壓,MpaT環:氧氣環境溫度,℃Cd:氧槍噴孔流量系數,通常取0.96-0.99N:氧槍噴孔個數A喉:氧槍噴孔喉口面積,mm2通過上述公式計算結果,確定計算供氧流量與工作氧壓的關系;②模型實現采用氧槍工作氧壓及氧氣工作環境溫度按理想氣體方程及噴頭設計流量壓力特性計算供氧流量,用計算供氧流量替代孔板流量計流量,參與轉爐吹煉過程的流量控制,并把計算供氧流量應用到已有的轉爐自動化煉鋼模型上,同時保留孔板流量計流量作為參考,不參與控制。把計算供氧流量應用到已有的轉爐自動化煉鋼模型上,通過修改已有轉爐自動化煉鋼模型的程序實現。依據氧壓與氧流量的關系,經過嵌入程序進行計算,實時產生工作氧壓與供氧流量的對應值,并將計算供氧流量顯示的操作界面上,與副槍自動化煉鋼氧流量控制模型無縫對接,為自動化煉鋼順利進行提供了保障。在轉爐自動化煉鋼模型中設定目標流量,通過自動化煉鋼程序來實時自動調整流量,實現對流量的控制,進而穩定了供氧壓力,避開了總管氧壓大范圍波動對流量表測量值精確度的干擾;副槍系統,通過在每爐吹煉前中期采用靜態模型進行過程控制,利用副槍TSC探頭在不終斷吹煉的情況下直接插入鋼水中進行定C、定溫并取樣分析,利用TSC測量結果和設定終點目標差值在后續的吹煉過程中采用動態控制模式,重新計算后續吹煉用氧量及輔料用量,自動控制吹煉終點,實現轉爐吹煉終點碳、溫度的自動命中。在實施例中,參照附圖1,確定計算供氧流量與工作氧壓的關系圖。實施例的計算模型驗證,參照表1、表2。表1:轉爐裝入物料情況表鐵水裝入量廢鋼裝入量鐵水比%廢鋼比%成鋼量比%噸鋼返礦加入比%135100.930.0680.9240.020表2:氧平衡計算表由以上物料平衡計算,與(1)項中流量模擬計算值相比,基本符合實際,驗證:通過物料平衡計算,與上述計算供氧流量的模擬計算值相比,驗證后基本符合實際,因此,用此計算供氧流量替代流量計測量值,參與自動化冶煉過程控制,能夠準確反應實際氧氣消耗與入爐料條件及終點目標之間的關系;實施例中模型實現:現經過分析,采用氧槍工作氧壓及氧氣工作環境溫度按理想氣體方程及噴頭設計流量壓力特性計算氧槍流量,用此流量替代孔板流量計流量參與轉爐吹煉過程的流量控制,并把此參數應用到達涅利自動化煉鋼模型L1及L2,同時保留原孔板流量計流量做為參考(不參與控制),具體修改要求如下:流量計算程序修改程序說明,參照附圖2.附圖2中:F計算:氧氣流量,m3/min;P:氧槍工作氧壓,Mpa;T1、T2:供氧管路支路末端截止閥狀態(1:表示閥關限位觸發;0:表示閥關限位未觸發);P1、P2:1號、2號氧槍工作氧壓,Mpa;T環:氧氣工作環境溫度,℃。應用范圍:本實施例對3座轉爐進行改造,3座轉爐L1東、西氧槍氧流量調節閥控制;3座轉爐副槍L1單爐實際氧耗累積量計量;3座轉爐副槍自動化煉鋼L2模型單爐氧耗累積量計量、氧流量計量;其它需更改的點(現場確定)。在沒有任何資金投入的情況下,成功解決了氧壓波動及氧量計量波動對轉爐自動化煉鋼供氧模型影響的問題,統一了3座轉爐供氧模型參數,使轉爐供氧模型全面實現自動化。主要效果如下:(1)總氧耗的穩定性根據投入應用后300爐數據分析,單爐氧耗量波動在5900-6400m3/t(與鐵水成份、溫度、廢鋼量、是否留渣、返礦加入量等因素的影響具有較強的對應性),噸鋼氧耗波動在49-52m3/t,與理論計算相符,也與實際轉爐冶煉工藝經驗值相符。(2)、總管氧壓對工作氧壓及氧流量的影響使用該發明后三座轉爐過程控制參數如下,在總管氧壓波動時,氧流量及工作氧壓基本不受影響,轉爐自動化煉鋼模型實現了參數統一,100%支持自動化煉鋼,具體見表3。表3:典型供氧參數實際情況表120t轉爐1號爐煉鋼生產,鐵水140t,廢鋼5t,吹煉過程總管氧壓波動在1.3~2.5MPa,調節閥后氧壓波動在1.3~1.5MPa,氧槍吹煉流量設定在400M3/min,吹煉工作氧壓穩定在0.6MPa左右,氧平衡值設定為2000,模型單爐實際氧平衡值穩定在2250±200,波動范圍1990~2500。1號爐使用本發明后氧平衡值情況(100爐數據)參照附圖3。120t轉爐2號爐煉鋼生產,鐵水140t,廢鋼5t,吹煉過程總管氧壓波動在1.3~2.5MPa,調節閥后氧壓波動在1.3~1.5MPa,氧槍吹煉流量設定在400M3/min,吹煉工作氧壓穩定在0.6MPa左右,氧平衡值設定為2000,模型實際單爐氧平衡值穩定在1850±200。2號爐使用本發明后氧平衡值情況(100爐數據)參照附圖4。當前第1頁1 2 3