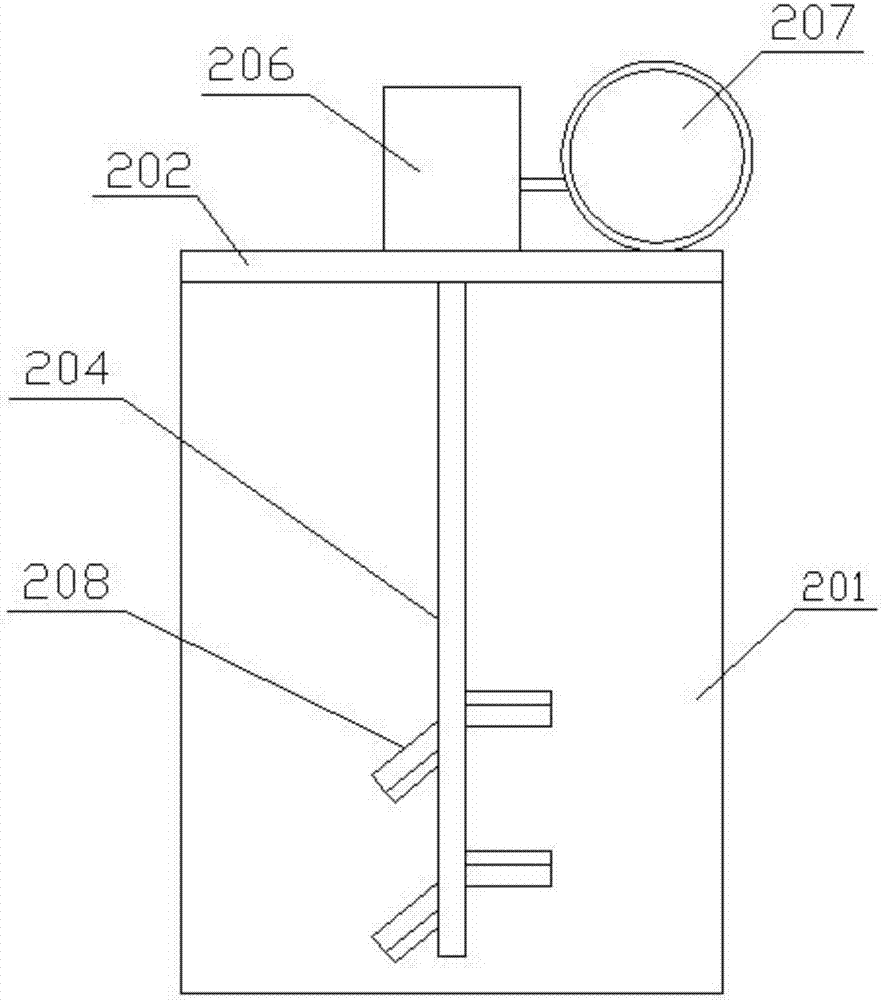
本發明涉及資源再生
技術領域:
,具體涉及一種再生鉛低溫連續熔煉工藝。
背景技術:
:目前,國內再生鉛廠大約有近300家,但上萬噸規模的不多,小廠平均生產能力為1000噸/年左右。國內的再生鉛廠家,生產規模小,技術水平低,絕大部分廠家采用小型反射爐冶煉,一些小企業,個體戶甚至采用原始的土爐土窯冶煉。具體冶煉方法是:將鉛金屬與鉛渣灰混合進入窯爐冶煉,大量的低溫即可熔化的鉛金屬和熔鑄鉛渣一起進行高溫冶煉,冶煉過程中以煙煤為燃料,加入無煙煤和鐵屑作為配料,每爐投料約2-4噸,平均煤耗560千克標煤/噸鉛。這些規模小、產量低、工藝及環保設備簡陋的再生鉛廠,金屬鉛的回收率只有80%,綜合能耗高達600kg標煤/噸鉛,產生大量棄渣中高達8%以上的含鉛無法得到再回收利用,銻等有色金屬50%未回收利用。每年有十萬噸計的鉛流失或排放到環境中,嚴重地浪費了資源,消耗了能源。世界上一些先進國家再生鉛工業在上世紀80年代就已走向生產規模化、工藝清潔無害化的良性發展之路。主要采用的工藝流程是:廢舊電池→破碎分選→鉛膏脫硫→短窯冶煉→精煉→產品。近些年中國大規模引進或自主開發了機械破碎分選廢舊電池工藝和設備。但傳統的熔煉設備能耗較大,熔煉效率較低。技術實現要素:本發明所要解決的技術問題在于提高一種連續性好,熔煉效率高,能耗低的再生鉛低溫連續熔煉工藝。本發明所要解決的技術問題采用以下技術方案來實現:一種再生鉛低溫連續熔煉工藝,包括以下步驟:(1)對廢舊鉛酸蓄電池進行破碎,收集鉛膏和鉛柵待用,其中廢舊鉛酸電池中鉛含量鉛膏占30%左右,鉛柵占34%左右;(2)將鉛膏放入加熱設備中,在真空環境下,加熱溫度控制在100℃-110℃,鉛膏厚度1cm~2cm,加熱時間不超過60分鐘,完成后立即進行預脫硫處理;通過加熱處理,能夠提高鉛膏的脫硫效果,脫硫后的鉛膏與水的溶解速度快,便于水洗。(3)將預脫硫后的鉛膏進行水洗后干燥,然后和鉛柵一起投入低溫熔煉爐,控制熔煉溫度在400℃-500℃;(4)將熔煉得到的鉛液送入澆鑄系統,經澆鑄得到鉛錠,再進行精煉可得到精鉛。上述步驟(3)中水洗后的水送入凈化系統進行凈化后回用。上述低溫熔煉爐包括:基座以及設置于基座上的熔煉爐、鋁液暫存爐以及澆鑄系統,所述熔煉爐并排設置有2組,所述鋁液暫存爐位于2組熔煉爐中間,所述的2組熔煉爐分別通過鋁液流通管路與鋁液暫存爐相通,所述鋁液暫存爐與澆鑄系統相連;廢鋁通過投料系統將廢鋁塊投入熔煉爐中,采用天燃氣對熔煉爐進行加溫,使溫度達到400-500℃,熔化后的鋁液流入鋁液暫存爐,再通過鋁液暫存爐將鋁液送入到澆鑄系統進行澆鑄成型。所述熔煉爐包括一爐體,所述爐體垂直設置于基座內,所述爐體上端設置有能夠蓋合爐體的端蓋,在端蓋上設置有投料口,所述爐體內設置有攪拌桿,所述攪拌桿上端伸出端蓋連接至減速器的動力輸出端,所述減速器的動力輸入端通過皮帶連接至電機。所述攪拌桿上設置有攪拌葉片,用于對爐體內的鋁液進行攪拌,加速熔化。所述攪拌葉片由攪拌桿底部向上設置有2層,每層設置2片攪拌葉片,其中一片攪拌葉片傾斜設置,另一片垂直設置。所述攪拌葉片包括上部攪拌基葉,在攪拌過程中將熔液向下壓,在上部攪拌基葉底部連接有下層攪拌葉,所述下層攪拌葉與上部攪拌基葉相垂直,該種設計可以提高攪拌效率。所述澆鑄系統包括澆鑄機以及設置在澆鑄機一側的輸送鏈,在所述輸送鏈上設置有鉛錠成型模。本發明的有益效果是:本發明工藝方法簡單,易于實施,采用低溫熔煉,能耗低,效率高,產品質量穩定,提高了資源的利用率。附圖說明圖1為本發明低溫熔煉爐結構示意圖;圖2為本發明熔煉爐結構圖;圖3為本發明攪拌葉片結構圖;圖4為本發明凈化系統結構圖。具體實施方式為了使本發明實現的技術手段、創作特征、達成目的與功效易于明白了解,下面結合具體實施例,進一步闡述本發明。實施例1:一種再生鉛低溫連續熔煉工藝,包括以下步驟:(1)對廢舊鉛酸蓄電池進行破碎,收集鉛膏和鉛柵待用,其中廢舊鉛酸電池中鉛含量鉛膏占30%左右,鉛柵占34%左右;(2)將鉛膏放入加熱設備中,在真空環境下,加熱溫度控制在100℃-110℃,鉛膏厚度1cm~2cm,加熱時間不超過60分鐘,完成后立即進行預脫硫處理;通過加熱處理,能夠提高鉛膏的脫硫效果,脫硫后的鉛膏與水的溶解速度快,便于水洗。(3)將預脫硫后的鉛膏進行水洗后干燥,然后和鉛柵一起投入低溫熔煉爐,控制熔煉溫度在400℃-500℃;(4)將熔煉得到的鉛液送入澆鑄系統,經澆鑄得到鉛錠,再進行精煉可得到精鉛。實施例2一種再生鉛低溫連續熔煉工藝,包括以下步驟:(1)對廢舊鉛酸蓄電池進行破碎,收集鉛膏和鉛柵待用,其中廢舊鉛酸電池中鉛含量鉛膏占30%左右,鉛柵占34%左右;(2)將鉛膏放入加熱設備中,在真空環境下,加熱溫度控制在100℃-110℃,鉛膏厚度1cm~2cm,加熱時間不超過60分鐘,完成后立即進行預脫硫處理;通過加熱處理,能夠提高鉛膏的脫硫效果,脫硫后的鉛膏與水的溶解速度快,便于水洗。(3)將預脫硫后的鉛膏進行水洗后干燥,然后和鉛柵一起投入低溫熔煉爐,控制熔煉溫度在400℃-500℃;(4)將熔煉得到的鉛液送入澆鑄系統,經澆鑄得到鉛錠,再進行精煉可得到精鉛。如圖1、圖2所示,低溫熔煉爐包括:基座1以及設置于基座1上的熔煉爐2、鋁液暫存爐3以及澆鑄成型系統4,熔煉爐2并排設置有2組,鋁液暫存爐3位于2組熔煉爐2中間,2組熔煉爐2分別通過鋁液流通管路與鋁液暫存爐3相通,鋁液暫存爐3與澆鑄成型系統4相連;熔煉爐2包括一爐體201,爐體201垂直設置于基座1內,爐體201上端設置有能夠蓋合爐體201的端蓋202,在端蓋202上設置有投料口203,爐體201內設置有攪拌桿204,攪拌桿204上端伸出端蓋202連接至減速器206的動力輸出端,減速器206的動力輸入端通過皮帶連接至電機207。攪拌桿207上設置有攪拌葉片208,用于對爐體201內的鋁液進行攪拌,加速熔化。澆鑄成型系統4包括澆鑄機401以及設置在澆鑄機401一側的輸送鏈402,在輸送鏈402上設置有鉛錠成型模403。廢鋁通過投料系統將廢鋁塊投入熔煉爐2中,采用天燃氣對熔煉爐2進行加溫,使溫度達到400-500℃,熔化后的鋁液流入鋁液暫存爐3,再通過鋁液暫存爐3將鋁液送入到澆鑄成型系統4進行澆鑄成型。如圖3所示,攪拌葉片208由攪拌桿207底部向上設置有2層,每層設置2片攪拌葉片208,其中一片攪拌葉片208傾斜設置,另一片垂直設置。攪拌葉片208包括上部攪拌基葉209,在攪拌過程中將熔液向下壓,在上部攪拌基葉209底部連接有下層攪拌葉210,下層攪拌葉210與上部攪拌基葉209相垂直,該種設計可以提高攪拌效率。實施例3一種再生鉛低溫連續熔煉工藝,包括以下步驟:(1)對廢舊鉛酸蓄電池進行破碎,收集鉛膏和鉛柵待用,其中廢舊鉛酸電池中鉛含量鉛膏占30%左右,鉛柵占34%左右;(2)將鉛膏放入加熱設備中,在真空環境下,加熱溫度控制在100℃-110℃,鉛膏厚度1cm~2cm,加熱時間不超過60分鐘,完成后立即進行預脫硫處理;通過加熱處理,能夠提高鉛膏的脫硫效果,脫硫后的鉛膏與水的溶解速度快,便于水洗。(3)將預脫硫后的鉛膏進行水洗后干燥,然后和鉛柵一起投入低溫熔煉爐,控制熔煉溫度在400℃-500℃;(4)將熔煉得到的鉛液送入澆鑄系統,經澆鑄得到鉛錠,再進行精煉可得到精鉛。如圖4所示,上述步驟(3)中水洗后的水送入凈化系統進行凈化后回用,所述凈化系統包括設置在濕地、水塘或低洼地中的凈化池1a,用于集中含鉛廢水,凈化池1a內壁設置有硬化層2a,該硬化層2a的作用是防止中水滲入地下,在硬化層2a的外圍設置有過濾層3a,對中水進行過濾,在過濾層3a外圍設置有土壤凈化層4a,利用土壤再一次對中水進行自然凈化,經土壤凈化后的中水即可達標再返回生產企業循環使用。過濾層3a和土壤凈化層4a均設置在硬化層2a表面,在過濾凈化的同時防止水體向下滲透污染地下水源。過濾層3a是由具有過濾功能的過濾材料組成,過濾材料為活性炭,活性炭具有極強的吸附功能,也可以吸附水中的重金屬成分,并定期清理更換過濾材料,提高過濾效果。土壤凈化層4a采用經過人工加工后的合成土壤,利用土壤的自然凈化功能對污水進行凈化,定期對土壤進行處理,將土壤中過濾掉的重金屬提取處理,然后重新利用。土壤過濾層外4a圍設置有防滲層5a,防止中水向周圍漫延滲透。凈化方法如下:(1)將含鉛廢水通過管道引入到凈化池中,在凈化池中進行集中;(2)隨著凈化池中水位的升高,上層水流向過濾層,經過濾層中的過濾材料過濾掉一部分重金屬鉛元素;(3)經過濾層過濾后水體再緩慢滲入到土壤過濾層,利用土壤的自然凈化功能,將水體中的重金屬鉛元素吸附掉;(4)經土壤過濾層出來的水,鉛含量<0.05mg/l,再返回生產企業循環使用。上述合成土壤是由以下重量份數的組分制成:三合土120-150份,細沙20-30份,尿素3-5份,ph調節劑1-50份,蛋殼粉15-20份,竹粉20-25份,煅燒高嶺土40-60份,水30-50份。該合成土壤對于含鉛中水中的鉛離子吸附量達到800~900mg/g,遠優于常規的鉛元素吸附劑。實施例的測試結果測試項目實施例1實施例2實施例3凈化后水體含鉛量0.05mg/l0.072mg/l0.046mg/l吸附率99.8%99.4%99.6%以上顯示和描述了本發明的基本原理和主要特征和本發明的優點。本行業的技術人員應該了解,本發明不受上述實施例的限制,上述實施例和說明書中描述的只是說明本發明的原理,在不脫離本發明精神和范圍的前提下,本發明還會有各種變化和改進,這些變化和改進都落入要求保護的本發明范圍內。本發明要求保護范圍由所附的權利要求書及其等效物界定。當前第1頁12