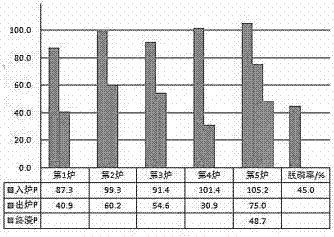
本發明屬于轉爐煉鋼新技術及其應用領域,提供了一種充分利用氣化脫磷渣循環冶煉提高轉爐渣利用率、降低冶煉成本的轉爐氣化脫磷渣循環脫磷煉鋼的方法。
背景技術:
:中國鋼鐵工業近20年來發展迅速,對國民經濟快速增長發揮了重要作用,但在節省資源、能源和減少爐渣等固體廢棄物排放等方面,目前面臨著巨大的壓力和挑戰。以占中國產鋼量90%以上氧氣轉爐煉鋼為例,每年生產約6.2億t粗鋼,要產生6000萬t以上爐渣,消耗3000萬t以上石灰和700萬t以上輕燒白云石,而用于生產煉鋼石灰和輕燒白云石的石灰石與生白云石礦產均為重要的不可再生資源。目前應用或正在探索中轉爐渣的綜合利用或減少排放的方法有很多種,大致分為兩類,一種是在爐渣從轉爐排放為固體物以后再加以處理和利用,比較成熟的是回收金屬鐵,以后用于燒結礦添加劑、合成渣原料、磷肥或轉爐渣水泥,即所謂“末端治理”,但是有效利用價值較低;另一種是爐渣在熔融狀態,乃至在轉爐內就加以循環利用,即所謂“源頭治理”,這種方法是目前轉爐渣的發展方向,符合無廢或少廢冶金的生態工業發展方向,比較成熟的有轉爐濺渣護爐留渣操作等冶煉工藝。20世紀后期,深沖鋼和高級別管線鋼等鋼種對磷含量要求苛刻,傳統的單渣法煉鋼脫磷率低,脫磷效果較差。90年代中期,日本各大鋼廠進行了轉爐鐵水脫磷的試驗研究,并在取得成功后迅速推廣,解決了超低磷鋼的生產難題。雙聯法是采用兩座轉爐聯合作業,一座轉爐脫磷,另一座轉爐接受來自脫磷爐的低磷鐵水脫碳,典型的雙聯法工藝流程為:高爐鐵水→鐵水預脫硫→轉爐脫磷→轉爐脫碳→二次精煉→連鑄。日本各鋼鐵廠轉爐雙聯法主要工藝技術參數對比,如表1所示。日本轉爐采用雙聯法脫磷煉鋼工藝的主要有jfe福山制鐵所的ld-nrp法、住友金屬的srp法、神戶制鋼的h爐法、新日鐵的ld-orp法,我國寶鋼、鞍鋼、首鋼京唐公司等也都選用了雙聯法煉鋼工藝。表1日本鋼鐵廠轉爐雙聯法主要技術工藝參數轉爐雙聯法脫磷在大批量生產純凈鋼時,轉爐容量大,有充分的反應空間,反應動力學條件優越,鐵水中磷可脫到0.010%以下,為少渣冶煉創造了條件;轉爐雙聯法為生產超低磷鋼、管線鋼及優質寬厚板鑄坯提供了有利的條件;雙聯法成本相對較低,轉爐脫碳渣用于另一座轉爐脫磷的雙聯法,生產1t鐵水的鋼鐵料消耗比傳統方法減少25kg,石灰消耗減少40%。但轉爐雙聯法煉鋼基建成本較高,需合理調度兩座轉爐設備,爐渣及鋼水互相反倒,操作較復雜。新日鐵室蘭制鐵所(兩座270tld-ob轉爐)和大分制鐵所(3座370t復吹轉爐)受設備和產品的限制,采用了murc技術,在同一轉爐進行鐵水脫磷預處理和脫碳吹煉,類似傳統煉鋼的雙渣法。murc工藝操作中將轉爐冶煉分為兩個階段,在第1階段主要進行脫硅、脫磷,結束后倒出部分爐渣,然后進行第2階段吹煉,吹煉結束后出鋼但將爐渣保持在爐內,下一爐在爐內留渣情況下裝入廢鋼、鐵水,然后進行第1和第2階段吹煉,并以此循環往復。室蘭制鐵所和大分制鐵所全部采用murc工藝,前期脫磷渣一般倒出50%,脫碳渣直接留在爐內用于下一爐脫磷吹煉,murc工藝冶煉周期約33~35min。2001年ogawa等報道了新日鐵開發的murc轉爐煉鋼新工藝及其在8t轉爐的試驗情況。近年來,新日鐵陸續報道了mucr工藝相關情況,新日鐵公司的大分、八幡、室蘭、君津等鋼廠采用了該工藝,產鋼占新日鐵總產鋼量55%左右,轉爐煉鋼石灰消耗減少40%以上。20世紀50~70年代,中國一些轉爐鋼廠在鐵水硅、磷質量分數高時,為了降低石灰消耗,減少吹煉過程噴濺,改善脫磷效果,曾采用出鋼后留渣或“留渣+雙渣”煉鋼工藝。隨著高爐生產水平的日益提高(鐵水硅質量分數降低),高磷鐵礦石用量減少(鐵水磷質量分數降低),以及顧忌留渣造成鐵水噴濺安全隱患,留渣煉鋼工藝沒有更大規模推廣采用。近年來國內許多鋼廠開始采用轉爐留渣煉鋼工藝,王新華等的發明專利201610012514.4“一種減少渣量的轉爐煉鋼方法”和201110340294.9“一種冶煉低磷鋼的轉爐冶煉工藝方法”,其關鍵技術是脫磷階段通過采用低堿度(w(cao)/w(sio2):1.3~1.5)和低mgo質量分數(≤7.5%)渣系,形成流動性良好和適度泡沫化爐渣,解決了“留渣+雙渣”煉鋼工藝快速足量倒渣和渣中金屬鐵質量分數高這兩大難題。針對轉爐底吹攪拌弱的問題,在脫磷階段采用低槍位和高強度供氧方法,利用頂吹氧氣流加強金屬熔池攪拌以促進脫磷,脫磷階段結束時[p]平均降低至0.029%左右,脫碳階段終點[p]降低至0.0096%左右,滿足了絕大多數鋼種對磷質量分數控制要求。經工業試驗形成了sgrs工藝方法,首鋼在其遷鋼公司5座210t復吹轉爐和首秦公司3座100t復吹轉爐大規模采用此法,取得了煉鋼石灰消耗減少47%以上,輕燒白云石消耗減少55%以上,渣量降低30%以上的效果。崔陽等的發明專利200910088141.2提出了“一種在濺渣護爐條件下頂底復吹轉爐鐵水脫磷的方法”,專利通過濺渣護爐操作有效利用前一爐次的爐渣和保護爐襯,同時提高脫磷效率。這些專利方法所基于的雙渣法都需要在冶煉中期之前快速倒渣,提槍中斷吹氧操作,與常規工藝相比,由于增加了爐渣固化和脫磷結束倒渣的時間,采用雙渣+留渣工藝后轉爐單爐生產周期比常規冶煉延長約4min,并且為了降低爐渣氧化性并固化爐渣,其濺渣護爐工藝中加入多種調質造渣料,如石灰、生白云石、輕燒白云石、鎂碳球等。李建新等的發明專利200910077085.2提出了“一種使用脫磷劑的轉爐冶煉工藝”,其技術方案指出利用前期低溫和高氧化亞鐵等良好的動力學條件,并使用含少量cacl2的cao基脫磷劑進行脫磷,后期重新造渣,脫碳渣做為下爐的脫磷渣使用。最近,趙東偉等的發明專利201610166145.8提出了“一種轉爐高效脫磷的冶煉方法”,專利指出濺渣護爐后倒出殘余爐渣,在轉爐吹煉開始前,向爐內加入預熔渣,成分為cao:70~85%,sio2:15~30%,進行轉爐吹煉操作。這些專利均優化了濺渣護爐后的爐渣,但存在的問題是未能充分對轉爐渣進行改質并深入利用,磷富集問題限制了大量轉爐渣在鋼鐵廠內部的循環利用。20世紀70年代末,日本的伊藤公久研究了ca2sio4-ca3(po4)2和cao-sio2-fe2o3液相渣間磷的平衡分配比,結果表明轉爐渣中的磷絕大部分富集在初晶相ca2sio4-ca3(po4)2中,以固溶體形態存在,很難去除。morita等學者采用微波碳熱還原對cao-sio2-feto系合成渣、鐵水脫磷預處理渣和含cr的轉爐不銹爐渣中fe、p、cr的回收進行了基礎研究,驗證了該方法脫磷的可行性并提出了進一步回收還原產物中p的方法。采用微波加熱碳熱還原轉爐爐渣進行氣化脫磷,是將爐渣中磷元素脫除的一條有效途徑。關于經濟有效地去除轉爐爐渣中磷的方法,尤其是利用濺渣護爐過程中爐內氣化脫除熔渣中磷的方法有很多報道,王書桓等的發明專利200610012514.4發明了一種“轉爐濺渣護爐過程中氣化脫除熔渣中磷的方法”,在濺渣護爐前,向熔池中加入適量脫磷劑,在濺渣過程中,高壓氮氣通過氧槍后產生巨大沖擊力,將爐內熔渣擊碎成顆粒飛濺起來掛于爐襯,此過程為固(焦炭)-氣(氮氣)-液(熔渣)之間的反應、以及熔渣內部的化學反應提供了良好的動力學條件,使熔渣中的磷得以通過化學反應進入氣相脫除,氣化脫磷劑分碳質脫磷劑和硅質脫磷劑兩種,碳質更具有工業應用現實意義,經多年實驗室基礎實驗和鋼鐵企業工業試驗,氣化脫磷率達到40%水平,留渣率80%以上,噸爐渣量平均為50~70kg/t,取得了良好的效果。王虎的發明專利201510561089.3發明了“一種用轉爐煤氣濺渣護爐作業的方法”,該工藝采用轉爐煤氣代替氮氣進行轉爐濺渣護爐作業,實現濺渣護爐作業時快速高效氣化脫磷,降低煉鋼成本。這些專利方法均能有效氣化脫磷,但仍停留在轉爐渣的處理上,未提出用于下爐冶煉的作用及影響,沒有形成高效循環煉鋼工藝。本發明基于濺渣護爐的氣化脫磷渣,提出了一種轉爐氣化脫磷渣循環脫磷煉鋼的方法,是一種所謂的“半雙渣法”煉鋼工藝,與新日鐵murc工藝、首鋼“留渣+雙渣”工藝等相比,其特點是發揮氣化脫磷渣在冶煉前期脫磷、轉爐冶煉末期利用拉碳倒渣、熱態熔渣爐內循環利用,提高了前期低溫脫磷效率,減少了石灰造渣劑用量,循環高效利用轉爐渣,降低了噸爐渣量,減少了鐵損。技術實現要素:本發明的目的在于提供一種轉爐氣化脫磷渣循環脫磷煉鋼的方法,該方法克服了傳統工藝諸多缺陷,適用于現有鋼鐵廠工藝技術的改進。實現上述目的采用以下技術方案:一種轉爐氣化脫磷渣循環脫磷煉鋼的方法,其特征在于,所述方法分為濺渣護爐氣化脫磷、兌鐵加料、吹氧造渣冶煉、拉碳倒渣和終點控制并出鋼五個階段,具體方法是:第一階段濺渣護爐氣化脫磷:轉爐出鋼結束后,根據爐渣基本狀態,向轉爐內熱態熔渣中添加脫磷劑,在濺渣護爐過程中通過氣化的方式脫除渣中的磷,保留濺渣后的氣化脫磷渣;第二階段兌鐵加料:傾斜轉爐兌入廢鋼和鐵水,利用氣化脫磷渣的富裕熱量提高轉爐廢鋼比,之后轉爐降槍吹氧,加入頭批造渣料,冶煉前期采用較低槍位,造渣原料中增加轉爐石灰石用量;第三階段吹氧造渣冶煉:轉爐冶煉前期低溫高效脫除鋼水中磷,冶煉中后期繼續吹氧造渣深脫磷;第四階段拉碳倒渣:終點拉碳時倒出部分高磷渣;第五階段終點控制并出鋼:終點鋼水成分和鋼水溫度合適后出鋼,同時判斷出鋼時爐渣基本狀態,進入下一個周期的轉爐冶煉操作;如此循環多爐次形成轉爐氣化脫磷渣循環脫磷煉鋼工藝;終點爐渣參數是,堿度控制為2.0~3.0,氧化性控制為feo含量15~25%,溫度為1660~1680℃。進一步,所述第二階段按照傾斜轉爐內的物料重量往傾斜轉爐兌入廢鋼的重量比值為10~35%。所述造渣原料中石灰石用量的重量比為20~40%。所述冶煉前期較低槍位,是指比不采用氣化脫磷渣的操作槍位低0.1~0.3m。所述終點拉碳次數為1~3次,第1次倒出總渣量的1/5~2/5,第2次、第3次盡量少倒渣。按照所述的第五個階段循環5~12爐次。第五個階段循環爐次為:小型轉爐為5~8爐次或更多,中大型轉爐為10~12爐次或更多。與傳統工藝相比,本發明具有以下優點:(1)加大濺渣前留渣比例,濺渣后不排渣,充分循環利用留渣熱量和爐渣高堿度優勢,提高冶煉前期低溫脫磷效果,提高轉爐冶煉效率。(2)可利用留渣及濺渣層熱量,增加廢鋼比,提高廢鋼使用量,以石灰石替代部分石灰煉鋼,降低石灰消耗;(3)爐渣鐵損減少,金屬收得率提高;(4)減少轉爐渣向爐外排放,節能減排促進環境保護。附圖說明圖1為轉爐氣化脫磷渣循環脫磷煉鋼工藝圖;圖2為氣化脫磷量及脫磷率圖3終點鋼水成分圖4終渣成分及加碳量圖5氣化脫磷量及脫磷率圖6終點鋼水成分圖7終渣成分及加碳量圖8氣化脫磷量及脫磷率圖9終點鋼水成分圖10終渣成分及加碳量圖11氣化脫磷量及脫磷率圖12終點鋼水成分圖13終渣成分及加碳量圖14氣化脫磷量及脫磷率圖15終點鋼水成分圖16終渣成分及加碳量圖17氣化脫磷率總體統計圖圖中標記:轉爐1、氧槍2、氮氣3、鐵水4、鐵水包5、廢鋼6、氧氣7、爐渣8、鋼水9、渣罐10、鋼包11。具體實施方式下面結合附圖對本發明做進一步的描述。圖1為轉爐氣化脫磷渣循環脫磷煉鋼工藝的五個階段。第一階段是濺渣護爐氣化脫磷,第二階段是兌鐵加料,第三階段是吹氧造渣冶煉,第四階段是拉碳倒渣,第五階段是終點控制并出鋼。具體工藝為:裝有氮氣3和氧槍2的轉爐1出鋼結束后,根據爐渣基本狀態,向轉爐1內熱態熔渣中添加合適的脫磷劑,在濺渣護爐過程中通過氣化的方式脫除渣中的磷,保留濺渣后的氣化脫磷渣;傾斜轉爐1兌入廢鋼6和鐵水包5內的鐵水4,利用氣化脫磷渣的富裕熱量提高轉爐廢鋼比,之后轉爐降槍吹氧氣7,加入頭批造渣料,氣化脫磷渣堿度高、流動性好,冶煉前期可采用較低槍位,造渣原料中可增加轉爐石灰石用量;轉爐冶煉前期低溫高效脫除鋼水9中磷,冶煉中后期繼續吹氧造渣深脫磷,終點拉碳時倒出部分高磷渣,當終點鋼水成分和鋼水9溫度合適后出鋼至鋼包11,同時判斷出鋼時鋼包10中爐渣9的基本狀態,進入下一個周期的轉爐冶煉操作;如此循環一定爐次,形成了轉爐氣化脫磷渣循環脫磷煉鋼工藝。按照上述的五個階段,采用轉爐氣化脫磷渣循環脫磷煉鋼方法的具體實施例:在某廠65t轉爐出鋼結束后,根據爐渣基本狀態,在溫度1660~1680℃狀態下,第一階段向轉爐內熱態熔渣中添加脫磷劑,在濺渣護爐過程中通過氣化的方式脫除渣中的磷,保留濺渣后的氣化脫磷渣;第二階段按照傾斜轉爐內的物料重量往傾斜轉爐兌入廢鋼和鐵水,成分如表1所示,第三階段轉爐降槍吹氧,加入頭批造渣料,各種造渣料成分如表2所示,氣化脫磷渣堿度高、流動性好,冶煉前期采用1.65~1.75m的低槍位,造渣原料中石灰石用量為1100~1500kg;第四階段轉爐冶煉前期低溫高效脫除鋼水中磷,冶煉中后期繼續吹氧造渣深脫磷,終點一次拉碳至碳含量0.08%,第一次倒出占總渣量1/5的高磷渣,如果有渣進行第2次、第3次倒渣,盡量少倒渣。第五階段當終點鋼水成分合格和鋼水溫度為1660℃~1680℃時出鋼,出鋼時爐渣基本狀態為堿度2.0,氧化性為feo含量18%,溫度1680℃,之后進入下一個周期的轉傾斜轉爐兌入廢鋼爐冶煉操作,如此循環6爐次。采用氣化脫磷渣循環脫磷煉鋼工藝后,冶煉低合金系列鋼磷含量合格率達到100%,石灰消耗降低1.5kg/t,生產成本噸鋼降低3~5元。表1廢鋼和鐵水成分鐵水質量/kg廢鋼質量/kg廢鋼p含量/%鐵水s含量/%鐵水si含量/%鐵水p含量/%7250058300.030.0250.470.113表2造渣料成分(干基%)名稱caomgosio2spfeofe2o3mnoh2oco2k2ona2oal2o3石灰石47.885.022.710.050.006542.86石灰74.057.793.90.0530.00915.56輕燒36.9626.10.850.0150.005633.7除塵灰9.322.132.280.2060.13739.3539.650.710.73.951.690.1鐵皮球0.2550.580.160.0850.7636.9150.361.581.40.113.8721.67礦石0.010.011.960.0480.0280.6195.470.121.13具體操作實施例實施例1按照上述原料情況實施轉爐氣化脫磷渣循環脫磷煉鋼,循環的爐數為5爐,試驗結果如圖2~圖4所示。結果表明,爐渣的氣化脫磷率為45.0%。試驗過程中,低拉碳時終點碳在0.110%以下,平均為0.076%;終點平均溫度1671℃;終點feo含量大于17.1%,平均為21.5%;堿度平均為2.67;四爐試驗加碳粉,平均加入量為2袋。采用低拉碳高氧化性操作,試驗終渣條件較好,氣化脫磷率較高。實施例2按照上述原料情況實施轉爐氣化脫磷渣循環脫磷煉鋼,循環的爐數為5爐,試驗結果如圖5~圖7所示。結果表明,本次循環氣化脫磷率為30.9%。試驗過程中,拉碳時終點碳在0.160%以下,平均為0.105%;終點平均溫度1656℃;終點feo含量大于17.7%,平均為18.9%;堿度平均為2.58;三爐試驗加碳粉,平均加入量為2.3袋(第一次加了5袋)。試驗終渣條件明顯不如第一個循環好,feo含量在20以下,碳粉加入量很少,導致氣化脫磷率相對較低。實施例3按照上述原料情況實施轉爐氣化脫磷渣循環脫磷煉鋼,爐數為6爐,試驗結果如圖8~圖10所示。結果表明,本次循環氣化脫磷率為27.5%。試驗過程中,拉碳時終點碳在0.083%以下,平均為0.053%;終點平均溫度1656℃;終點feo含量大于15.3%,平均為22.7%;堿度平均為2.45;三爐試驗加碳粉,平均加入量為2.4袋。采用低拉碳、高氧化性操作,試驗終渣條件較好,氣化脫磷率相對較高。實施例4按照上述原料情況實施轉爐氣化脫磷渣循環脫磷煉鋼,循環的爐數為5爐,試驗結果如圖11~圖13所示。結果表明,本次循環氣化脫磷率為47.9%。試驗過程中,拉碳時終點碳在0.011%以下,平均為0.06%;終點平均溫度1662℃;終點feo含量大于17.0%,平均為20.2%;堿度平均為2.44;三爐試驗加碳粉,平均加入量為1.7袋。采用低拉碳、高氧化性操作,試驗終渣條件較好,氣化脫磷率相對較高。實施例5按照上述原料情況實施轉爐氣化脫磷渣循環脫磷煉鋼,循環的爐數為6爐,試驗結果如圖14~圖16所示。結果表明,本次循環氣化脫磷率為37.3%。試驗過程中,拉碳時終點碳在0.08%以上,平均為0.11%;終點平均溫度1663℃;終點feo含量大于12.8%,平均為15.0%;堿度平均為2.41;五爐試驗加碳粉,平均加入量為2.0袋。拉碳適中,但終渣氧化性較低,試驗終渣條件一般,氣化脫磷率相對較高。總之,轉爐氣化脫磷渣循環脫磷煉鋼實施例的脫磷率總體統計圖如圖17所示,可見氣化脫磷率為27.5%~47.9%,統計平均值為38%,爐渣脫磷效果很好,使得冶煉過程渣量小、熱損低、鐵損少,顯著降低了冶煉成本。轉爐氣化脫磷渣循環脫磷煉鋼實施例表明,在操作水平和參數條件控制較好時氣化脫磷率完全可達到40%的水平,主要包括:多爐次氣化脫磷循環冶煉終點碳平均控制在0.010%以下,終點平均溫度1660℃,終點feo含量平均大于20%,堿度平均為2.45,碳粉平均加入量為2~3袋;同時配合良好的濺渣護爐過程及穩定的冶煉操作技術水平。操作實施例中所述的所加碳粉的重量,每袋碳粉重17kg。雖然,上文中已經用一般性說明及具體實施方案對本發明作了詳盡的描述,但在本發明基礎上,可以對之作一些修改或改進,這對本領域技術人員而言是顯而易見的。因此,在不偏離本發明精神的基礎上所做的這些修改或改進,均屬于本發明要求保護的范圍。當前第1頁12