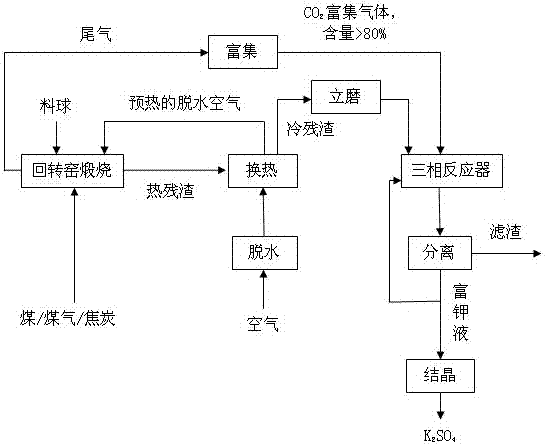
一種利用鉀長石-硫酸鈣礦化CO2聯產硫酸鉀的方法技術領域本發明涉及一種利用礦物礦化CO2達到固定CO2目的的方法,尤其涉及一種利用鉀長石-硫酸鈣礦化CO2聯產硫酸鉀的方法。
背景技術:目前,化石燃料的消耗逐年增加,導致CO2的排放量隨之增加。全球CO2排放量從2006年的280億t,增加到2010年的302億t(IEA,2012)。預計到2100年,溫室氣體的排放將導致海平面上升38cm,全球平均氣溫上升1.9℃(B.Meltetal.,CambrideUniv,2005)。CO2的減排問題已經達成全球共識。作為末端減排手段,對大規模二氧化碳的捕捉、封存(CCS),主要包括地質封存、海洋封存和礦化封存三種方式。地質封存和海洋封存可能引發泄漏、地質災害、地下水污染等次生災害。礦化相比前兩種方式,能將CO2轉化為穩定的碳酸鹽,長期固定下來,安全性更高(謝和平等,科學通報,2012),但是這種方法目前存在的最大問題就是經濟上不可行。鉀肥是農業生成必須的基礎肥料,每年世界鉀肥產量為3500萬噸左右,中國2012年表觀消費量為700萬噸,鉀肥需求量占世界總需求量20%。但目前鉀肥主要以水溶性鉀礦資源生產,對于中國這樣水溶性鉀資源短缺的國家,開辟非水溶性資源勢在必行。中國水溶性鉀資源只有青海湖、柴達木碰地等少數鹽湖鉀資源,水溶性鉀資源僅占世界1%(馬鴻文,地學前緣,2010)。中國非水溶性富鉀礦石儲量巨大,已探明可經濟開采的鉀長石總量約為97億t,如果將其加以開采利用,能夠滿足我國100年的鉀肥需求。世界范圍內鉀長石資源量也巨大,可以作為巨大的鉀資源儲備。美國和日本先后進行了鉀長石分解制鉀肥的研究,后因成本上不能與水溶性鉀資源生產鉀肥工藝競爭,均未取得大規模的工業化。鑒于鉀資源特征,中國從上個世紀60、70年代就開始研究鉀長石的利用,對鉀長石的研究主要是以高溫法生產復合肥料,主要產品是鉀鈣肥、鉀鎂磷鉀肥、硅鎂鉀肥(汪碧容等,廣東農業科學,2011)。鉀鈣肥的生產方法主要是將鉀長石、石灰石和煤按一定比例經破碎、粉磨、成球,經1200℃焙燒后磨成細粉,制得鉀鈣肥,有效K2O含量約為5%;鈣鎂磷鉀肥的生產方法主要是將鈣鎂磷肥工藝中的硅石原料用鉀長石全部或者部分替代制得,有效K2O含量約為4%;硅鎂鉀肥生產方式主要是將鉀長石、白云石和煤按一定比例配料,高溫熔融,在經水淬,干燥制得,K2O含量約為3%-8%(申軍,化工礦物與加工,2000)。這些過程生產的鉀肥含鉀率低,能耗高。中國在70、80年代開發了窯灰鉀肥同時聯產水泥。此法是將鉀長石摻入到水泥配料中一起高溫焙燒,煅燒溫度為1350℃,部分鉀揮發進入窯灰,將窯灰用干法或者濕法收集起來制得窯灰鉀肥(馬鴻文,礦產綜合利用,1998)。高溫法普遍存在能耗高,CO2排放量大,產品有效鉀含量低等問題。針對上述問題,科學家后期主要研究了用低溫分解鉀長石。例如中國專利(ZL95104123.1)公開了一種低溫分解鉀長石的方法,將鉀長石與無機酸和氟化物在常壓低溫下反應,產物加工生產出硫酸鉀銨、鋁系列和硅系列產品。鉀長石分解率為93%,硫酸鉀銨純度只有約20%。低溫分解鉀長石雖然不需要高溫,但對設備的耐腐蝕性要求高,且硫酸鉀產純度不高,若要得到高純度的硫酸鉀產品必須進一步分離提純,能耗和設備投入均會大大增加。馬鴻文等研究了熱水法提取鉀肥(馬鴻文,現代地質,2005)但水熱法需要高溫高壓,設備成本高。以上提取鉀肥的過程都集中在鉀的水溶性轉化,就單純提取鉀來看,很難同現有的水溶性鉀鹽資源生產鉀肥競爭。我國是磷肥生產大國,每年磷肥產量為2000萬噸左右。磷肥行業副產磷石膏主要來源于濕法磷酸工藝,每生產1tP2O5約排放4.5~5t磷石膏,我國磷石膏的年排放量為20Mt,主要以堆存為主(鄭蘇云等,化工生產與技術,2003)。磷石膏的排放不僅占用大量土地還污染了環境。目前,磷石膏的利用主要集中在三個方面:一是作為硫鈣資源生產化工產品;二是建筑原材料;三是改良土壤(李飛,副產品綜合利用,2012)。磷石膏作為硫鈣資源主要是用于生產硫酸等化工產品,例如硫酸生產過程是將磷石膏與還原劑在高溫下進行反應,得到二氧化硫氣體,進一步制得硫酸等產品。該方法普遍存在的問題是分解溫度需要在1200℃以上,產生大量的CO2氣體(中國專利CN10400009,CN1161943A,CN1724338A,CN1884048A)。由于生產成本較高,這一工藝并沒有被普遍推廣。磷石膏作為建筑材料,主要研究其制備水泥緩凝劑、免燒磚等產品。磷石膏緩凝劑一般的生產方法是將堿性鈣質中和磷石膏中的游離磷酸及氟離子后,改性后磷石膏一部分脫水制得半水硫酸鈣,煅燒后的磷石膏和未煅燒磷石膏混合,造粒,陳化后即為緩凝劑。但是這種方法在脫水過程中需要較高的能耗,且容易帶來二次污染。后來李進等人(CN201110183609.3)通過利用半水磷石膏部分陳化為二水磷石膏后,加入堿性激化劑及水,造粒風干后即得產品。雖然由磷石膏生產的水泥緩凝劑質量符合國家相關標準,但是和天然石膏、脫硫石膏生產水泥緩凝劑相比(包括政策優惠),磷石膏沒有優勢,很難推廣。以鐘本和為代表的制備免燒磚技術(中國專利ZL02113258.5)將磷石膏和其它原料包括激活復合劑、非激活復合劑、水、促進劑,通過初步混合、消化反應、主混合、壓制成型、蒸汽養護、靜置晾干等工序后制得了生產強度高、容重低的磷石膏免燒磚。此法在技術上、能耗上具有一定的可行性,但是磷石膏用于建筑材料的安全性、可靠性還需要有待考證。磷石膏改良土壤是通過磷石膏富含的鈣離子交換鹽堿土壤中的鈉離子調節土壤酸堿度,利用磷石膏中的磷、硫、鎂等有效元素,改良鹽堿土壤的理化性能,使農作物增收。高原等(CN201210522182.X)以磷石膏為主要原料,添加腐殖酸、硫酸亞鐵、尿素和硫酸鋅,通過造粒干燥等步驟制得的改良劑,能夠耕層土壤pH降低,土壤水溶性Na+和交換性Na+含量降低,土壤堿化度降低,土壤容重減輕,土壤入滲性能提高,肥料利用率提高,土地生產力提高。此法和天然石膏、脫硫石膏改良土壤相比,最大的問題仍然是沒有經濟優勢,推廣難。針對上述問題,本發明耦合CO2碳酸化和鉀長石提鉀兩個工藝步驟,形成了一種同時處理CO2、工業固廢并加工鉀長石生產鉀肥的新方法。通過同時處理鉀長石、CO2和磷石膏等工業固廢,生產高濃度鉀肥,從而得到很好的固廢處理收益和很好的經濟價值。如果從生產過程的成本中扣去磷石膏等工業固廢處理的環境收益、CO2減排的碳稅收益,從經濟上來講是可行的。
技術實現要素:本發明充分利用CO2碳酸化特征,并耦合熱分解鉀長石制取水溶性硫酸鉀工藝,目的在于克服傳統鉀長石制取鉀肥工藝中的CO2排放和產品純化成本高的不足之處,以解決了我國貧鉀問題和碳排放問題。本發明的技術方案:將預處理后的鉀長石粉末,與硫酸鈣均勻混合后成型,通過高溫反應活化后,采用CO2礦化煅燒渣,分離并獲得含碳酸鈣的礦化渣和水溶性的硫酸鉀肥料。本發明所述的利用鉀長石-硫酸鈣礦化CO2聯產硫酸鉀的方法,工藝步驟如下:(1)將鉀長石原料進行破碎、粉磨、過篩,與硫酸鈣均勻混合,并采用壓片或團粒的方法成型;(2)型料送入反應溫度900~1300℃的高溫反應爐煅燒10~600min;(3)焙燒產物冷卻至室溫后,粉碎過篩,按固液質量比1:1~1:100在加壓反應器內攪拌條件下與CO2進行礦化反應,CO2氣體壓力在1~30MPa,反應溫度為25~300℃,礦化反應時間10~600min;(4)礦化后的液固混合物經過過濾分離,濾液經過蒸發、結晶后可制得硫酸鉀,濾渣即為包含CaCO3的硅鋁酸鹽,可作為水泥材料。本發明所述方法中原料,鉀長石為天然開采鉀長石礦,通常全鉀含量在8~12wt%(以K2O計),破碎后,可以通過棒磨或立磨等常規方法粉磨至粒徑≤0.42mm。本發明所述方法中原料,硫酸鈣為含硫酸鈣的工業固廢,如磷石膏、脫硫石膏等的干燥粉體。本發明所述方法中原料,CO2可以是生產過程中捕捉分離的純CO2氣體,也可以是其他生產過程如合成氨、煤氣化后副產純CO2氣體,含量>80%。本發明所述方法,型料成型手段可以采取圓盤造粒、滾筒造粒、壓片機壓片等常規方法實現。本發明所述方法,型料的高溫煅燒活化可以在立窯或旋轉窯等反應器中進行,煅燒爐由煤、煤氣、天然氣或者電加熱。附圖說明圖1是本發明所述一種利用鉀長石-硫酸鈣礦化CO2聯產硫酸鉀的方法的一種工藝流程框圖。圖2是本發明所述方法具體實施方式的一種工藝流程框圖。圖3是本發明所述方法具體實施方式的一種工藝流程框圖。圖4是本發明所述方法具體實施方式的一種工藝流程框圖。有益效果:(1)由于直接添加硫酸鈣和鉀長石反應,制得的硫酸鉀產品純度高≥85%,且提鉀率≥80%;(2)本發明和其它高溫分解鉀長石傳統工藝相比,每消耗一份鉀長石,能減排CO2達6%以上;(3)本發明和已報道的利用鉀長石、氯化鈣礦化CO2聯產鉀肥的方法相比(謝和平等,科學通報,2012),由于本發明體系中不含有氯離子,對設備沒有腐蝕,并可以將提鉀礦化合為一步進行,節約能耗。具體實施方式實施實例1本實施例中,礦化CO2聯產硫酸鉀的方法如下:(1)物料團球。鉀長石礦化學組成(質量分數)為:K2O11.48%,Na2O0.08%,Al2O315.94%,SiO266.88%,CaO0.95%,Fe2O32.56%。將上述鉀長石用立磨機粉磨至粒徑≤0.075mm后與硫酸鈣按質量比1:2均勻混合,采用常規圓盤造球法方法造球,造球時加入混合粉料重量1.5%的粘土以及混合粉料重量10%的水作為粘結劑,球團粒徑為10mm。將料球置于烘箱中在120℃下進行干燥至恒重。(2)將料球從回轉窯尾部連續送入回轉窯,輸送速度為1~1.5t/h,采用煤、煤氣或焦炭等加熱方式將回轉窯加熱,將脫水空氣預熱至550℃后通入回轉窯,使其溫度保持在1200℃。料球在主反應段被加熱至反應溫度1200℃,料球在主反應段停留時間至少為2h,反應生成的尾氣和新進回轉窯的料球進行熱交換,溫度降至400-600℃從回轉窯窯尾引出。高溫熱殘渣從回轉窯窯頭輸出,進入冷卻機,脫水空氣作為冷卻介質與高溫熱殘渣進行熱交換。熱交換后的殘溫度降至≤100℃后排出。(3)將冷卻機中排出的熟料用立磨機粉磨至粒徑≤0.15mm,按1:3添加工藝水調成料漿,輸送至三相反應器中,將尾氣中捕集分離后的CO2氣體(純度>80%)連續通入三相反應器中,在充分攪拌,反應溫度為150℃,反應時間為1h的條件下進行礦化反應后分離,得到含碳酸鈣礦渣和水溶性硫酸鉀肥料。該實施方式示意圖如圖2所示。該過程提鉀率可達到~80%,礦化率可達到~2%。實施實例2(1)、(2)操作同實施例1。(3)將冷卻機中排出的熟料用立磨機粉磨至粒徑≤0.15mm,按1:3添加工藝水調成料漿,輸送至三相反應器中,將尾氣中捕集分離后的CO2氣體(純度>80%)間歇通入三相反應器中,初始壓力為4MPa,在充分攪拌,反應溫度為100℃),反應時間為2h的條件下進行礦化反應后分離,得到含碳酸鈣礦渣和水溶性硫酸鉀肥料。該實施方式示意圖如圖3所示。該過程提鉀率可達到~80%,礦化率可達到~7%。實施實例3(1)物料壓片。鉀長石礦原料、粉磨、配料操作同實施例1相同,采用高速壓片機壓片的方法壓片,成型壓力6MPa,直徑為13mm,平均厚度為5mm。(2)將無煙煤采取同(1)的壓片方式成型后和生料片均勻很合,無煙煤的量為總質量的~15%。(3)將混合片從立窯頂部連續送入立窯,輸送速率為1.3~1.9t/h,將脫水空氣預熱至550℃后,從立窯部底連續輸入立窯,無煙煤片均勻分布在立窯內,在脫水空氣中燃燒產生的高溫氣體與混合片逆向運行進行熱交換,生料片在主反應段被加熱至反應溫度1200℃,生料片在主反應段停留時間至少為2h,反應生成的尾氣和新進立窯的混合片進行熱交換,溫度降至400-600℃從立窯頂部煙囪引出。高溫熱殘渣從立窯底部輸出,進入冷卻機,脫水空氣作為冷卻介質與高溫熱殘渣進行熱交換。熱交換后的殘溫度降至≤100℃后排出。(4)操作同實施例2步驟(3)。該實施方式示意圖如圖4所示。該過程提鉀率能達到~80%,礦化率能達到~5%。