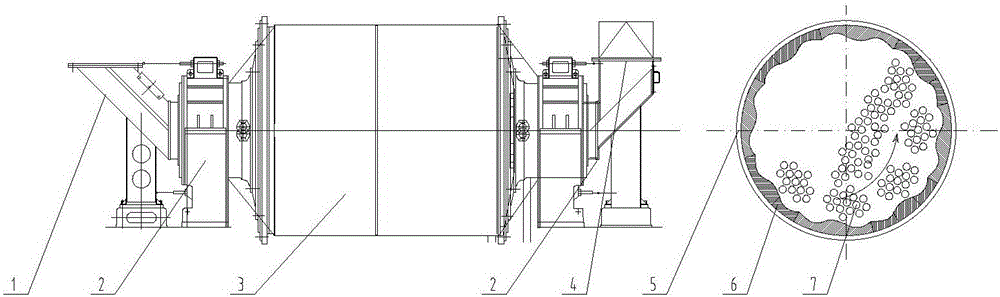
本發明屬于焦粉、煤粉燃燒發電
技術領域:
,尤其涉及一種高溫半焦磨制的系統和方法。
背景技術:
:我國煤炭資源豐富,原煤除了部分用于煉焦、轉化加工外,絕大部分用于直接燃燒。煤直接燃燒,導致煤炭中富含的油氣資源還沒有得到充分的提煉利用,而且直接燃燒熱效率低,對環境破壞嚴重。煤的熱解是將煤在惰性氣氛下加熱,制取半焦、煤氣和焦油等產品,得到的這些產品,又可以梯級利用,對油氣資源充分提取的同時,又提高了煤炭尤其是褐煤和長焰煤的綜合利用效率。現有技術公開了一種電廠半焦制粉噴吹工藝如圖1,其工藝流程為:熱解爐1產生的高溫半焦進入冷焦機2降溫,半焦溫度降低到80℃左右,然后通過提升機3進入冷焦倉,煤儲存在原煤倉6內,冷焦和原煤分別通過調速給焦機5和調速給煤機7按照一定比例進入磨煤機,在磨煤機8內磨成合格煤粉(焦粉)后通過鼓風機送入粉煤鍋爐燃燒,粉煤鍋爐生產的蒸汽送到汽輪機發電。現有技術還公開了一種球磨機,該設備主要結構工藝如圖2,具體磨制流程如下:物料從進料口1進入球磨機內部,球磨機在兩端軸承2支撐的條件下旋轉,球磨機筒體5內部安裝襯板6,同時裝有鋼球7,鋼球和物料混合,在筒體和襯板的帶動下旋轉,通過鋼球之間的摩擦和鋼球與襯板之間的摩擦磨制物料,物料磨制成粉后被風從出口帶出進入下一道工序。此外,現有技術也公開了一種中速磨,該設備主要結構如圖3,具體磨制流程如下:原煤通過進料口2進入磨機,襯板4在電機減速機系統5的帶動下旋轉,同時帶動磨輥3旋轉,原料在磨輥3和襯板4之間磨制,合格后被風機從出口1吹出進入下道工序。上述現有技術有如下缺點:(1)高溫半焦需要冷卻后再進入磨煤機磨制,原來的表熱沒有得到利用;(2)高溫半焦在冷卻過程中需要消耗大量的冷卻水,提高了半焦的生產成本;(3)系統需要設置冷焦機,增加了系統的復雜性和投資;(4)磨機結構特點限制了物料溫度;(5)由于筒體結構特點,物料溫度不能太高,一般限制在400℃以下,如果高出以上范圍,會造成球磨機本體和軸承溫度升高,會影響筒體的強度和軸承的安全運行;(6)磨機內部鋼球和襯板的接觸面積據定了磨機的生產效率,接觸面積收到了球磨機直徑和長度的限制,如果增加產能,就需要增加球磨機的長度和直徑,會大幅度增加磨機的生產成本。技術實現要素:為了解決上述問題,本發明開發一種新的設備和工藝,主要是為了解決高溫半焦高溫狀態下的磨制問題,高溫半焦通過高溫磨制成高溫焦粉,通過氣力輸送本直接送入鍋爐內燃燒,以實現高溫半焦的直接制粉輸送利用的目的。為實現上述目的,本發明提出了一種高溫半焦磨制系統,包括熱解爐、高溫調速給料機、原煤倉、給煤機和磨粉機;其中,所述高溫調速給料機設置在所述磨粉機和所述熱解爐之間,用于調節高溫物料進入所述磨粉機的速度;所述給煤機設置在所述磨粉機和所述原煤倉之間,用于將原煤送入所述磨粉機;所述磨粉機包括軸承和筒體,其中,所述軸承設置在筒體兩側,用于支撐所述筒體旋轉;所述筒體包括進料口、出料口和外殼,所述進料口和所述出料口分別位于所述筒體的兩端,所述外殼位于筒體表層;所述外殼內部設置有水冷腔,所述外殼還包括冷卻水進口和冷卻水出口,所述水冷腔用于使冷卻水在其內部循環。進一步地,所述系統還包括:高溫收塵器、高壓輸送泵、煤粉鍋爐;其中,所述磨粉機與所述高溫收塵器、所述高壓輸送泵、所述煤粉鍋爐順序相連,所述高溫收塵器用于對來自所述磨粉機的煤粉和焦粉進行收塵,所述高壓輸送泵用于通過氮氣將收塵后的煤粉和焦粉送入所述煤粉鍋爐進行燃燒。進一步地,所述系統還包括:廢氣鼓風機、助燃風機;其中,所述高溫收塵器還包括鍋爐廢氣出口;所述廢氣鼓風機位于所述鍋爐廢氣出口和所述筒體的所述進料口之間,利用來自所述高溫收塵器的鍋爐廢氣,所述廢氣鼓風機把所述磨粉機的合格粉料吹入所述高溫收塵器;所述煤粉鍋爐包括助燃風入口;所述助燃風機包括助燃風出口,所述助燃風出口和所述助燃風入口相連;所述助燃風機產生助燃風,進入所述粉煤鍋爐后和所述煤粉和焦粉一起燃燒。進一步地,所述磨粉機還包括旋轉接頭,所述旋轉接頭位于所述冷卻水進口處,所述水冷腔通過所述旋轉接頭和外部冷卻水管連接。具體地,所述軸承內部為空心軸,所述水冷腔通至所述空心軸。進一步地,所述筒體還包括襯板,所述襯板設置在所述外殼內側,所述襯板為耐高溫不銹鋼。進一步地,所述筒體還包括保溫層,所述保溫層設在所述外殼和所述襯板之間,所述保溫層的材質為石棉保溫板。進一步地,所述筒體還包括螺旋板,所述螺旋板通過螺旋板支撐和緊固件固定在所述襯板上。所述螺旋板弧度半徑為0.1~0.2D。弧度為120°。本發明還提供一種用利用上述系統進行半焦磨制的方法,其特征在于,將所述熱解爐生產的高溫半焦和所述原煤倉內的所述原煤,分別通過所述高溫調速給料機和所述給煤機給入所述磨粉機,所述磨粉機在兩端軸承支撐的條件下旋轉磨制,磨制結束后,將產生的所述煤粉和焦粉從所述出料口排出;加料前將冷卻水從所述冷卻水進口輸至所述水冷腔,在所述水冷腔內循環,從所述冷卻水出口排出。進一步地,所述方法還包括:利用來自所述高溫收塵器的鍋爐廢氣,將所述磨粉機磨制后得到的合格粉料吹入所述高溫收塵器;所述合格粉料經過所述高溫收塵器收塵后,再利用氮氣將所述高壓輸送泵內的所述煤粉和焦粉送入所述粉煤鍋爐;將所述助燃風機產生的助燃風輸至所述粉煤鍋爐和所述煤粉和焦粉一起燃燒,然后將產生的蒸汽輸至汽輪機發電。具體地,將給入所述磨粉機的所述熱解爐生產的高溫半焦和所述原煤倉內的原煤的比例控制為1:0.5-2。作為優選的實施方案,通過所述高溫調速給料機和所述給煤機,調節所述熱解爐生產的高溫半焦和所述原煤倉內的原煤進入所述磨粉機的速度,將所述熱解爐生產的高溫半焦和所述原煤倉內的原煤混合后的溫度控制在450-750℃。具體地,通過調節所述水冷腔的所述冷卻水流量,將所述外殼溫度控制在200℃以下。采用本發明的系統和方法,取得了以下效果:(1)解決里高溫半焦和高溫物料的磨制問題;可以對1000℃以下的高溫物料直接磨制并進入下一道工序,簡化了高溫物料的生產流程;(2)高溫半焦直接磨制使用,減少了中間環節;(3)充分利用了高溫半焦的表熱,減少了能源浪費;(4)工藝更加簡化,取消了冷焦機;(5)本發明大幅提高了磨機的磨制效率,可以在同等磨制體積和同樣能耗的前提下大幅度提高產量。本發明的附加方面和優點將在下面的描述中部分給出,部分將從下面的描述中變得明顯,或通過本發明的實踐了解到。附圖說明圖1是本發明的電廠半焦制粉噴吹工藝工藝流程圖;圖1中,1-熱解爐;2-冷焦機;3-提升機;4-冷焦倉;5-調速給焦機;6-原煤倉;7-調速給煤機;8-磨粉機;9-鼓風機;10-粉煤鍋爐;圖2是本發明的球磨機結構原理圖;圖2中,1-進料口;2-軸承;3-筒體;4-出料口;5-外殼;6-襯板;7-鋼球;圖3是本發明的中速磨結構原理圖;圖3中,1-出料口;2-進料口;3-磨輥;4-襯板;5-電機減速機;圖4是本發明的高溫半焦直接磨制工藝流程;圖4中,1-熱解爐;2-高溫調速給料機;3-廢氣鼓風機;4-原煤倉;5-給煤機;6-磨粉機;圖5是本發明的磨粉機結構原理圖;圖5中,6-磨粉機;61-進料口;62-冷卻水進口;63-旋轉接頭;64-冷卻水出口;65-軸承;66-筒體;67-水冷腔;68-保溫層;69-螺旋板;610-鋼球;圖6是本發明的螺旋板安裝定位圖;圖6中,68-保溫層;69-螺旋板;611-外殼;612-襯板;613-螺旋板支撐;614-緊固件;圖7是本發明的高溫焦粉進入鍋爐流程圖;圖7中,3-廢氣鼓風機;6-磨粉機;7-助燃風機;8-高溫收塵器;9-高壓輸送泵;10-氮氣;11-煤粉鍋爐。具體實施方式以下結合附圖和實施例,對本發明的具體實施方式進行更加詳細的說明,以便能夠更好地理解本發明的方案及其各個方面的優點。然而,以下描述的具體實施方式和實施例僅是說明的目的,而不是對本發明的限制。本發明提出了一種高溫半焦磨制系統,如圖4,包括熱解爐1、高溫調速給料機2、原煤倉4、給煤機5和磨粉機6;其中,所述高溫調速給料機2設置在所述磨粉機6和所述熱解爐1之間,用于調節高溫物料進入所述磨粉機6的速度;所述給煤機5設置在所述磨粉機6和所述原煤倉4之間,用于將原煤送入所述磨粉機6。所述磨粉機6結構原理如圖5,包括軸承65和筒體66,其中,所述軸承65設置在筒體66兩側,用于支撐所述筒體66旋轉;所述筒體66包括進料口61、出料口和外殼611,所述進料口61和所述出料口分別位于所述筒體66的兩端,所述外殼611位于筒體66表層。所述外殼611內部設置有水冷腔67,所述外殼611還包括冷卻水進口62和冷卻水出口64,所述水冷腔67用于使冷卻水在其內部循環。原來的鋼外殼改成了帶水冷腔的外殼611,水冷腔67分為8個部分,冷卻水在水冷腔內循環,防止高溫物料造成外殼611溫度大幅度升高,一般把外殼611溫度控制在200℃以下。進一步地,如圖7,所述系統還包括:高溫收塵器8、高壓輸送泵9、煤粉鍋爐11;其中,所述磨粉機6與所述高溫收塵器8、所述高壓輸送泵9、所述煤粉鍋爐11順序相連,所述高溫收塵器8用于對來自所述磨粉機6的煤粉和焦粉進行收塵,所述高壓輸送泵9用于通過氮氣10將收塵后的煤粉和焦粉送入所述煤粉鍋爐11進行燃燒。進一步地,所述系統還包括:廢氣鼓風機3、助燃風機7;其中,所述高溫收塵器8還包括鍋爐廢氣出口;所述廢氣鼓風機3位于所述鍋爐廢氣出口和所述筒體66的所述進料口61之間,利用來自所述高溫收塵器8的鍋爐廢氣,所述廢氣鼓風機3把所述磨粉機6的合格粉料吹入所述高溫收塵器8;所述煤粉鍋爐11包括助燃風入口;所述助燃風機7包括助燃風出口,所述助燃風出口和所述助燃風入口相連;所述助燃風機7產生助燃風,進入所述煤粉鍋爐11后和所述煤粉和焦粉一起燃燒。進一步地,如圖5及圖6,所述磨粉機6還包括旋轉接頭63,所述旋轉接頭63位于所述冷卻水進口62處,旋轉的筒體66所述水冷腔67通過所述旋轉接頭63和外部冷卻水管連接,保證在設備旋轉過程中正常的冷卻效果。具體地,所述軸承65內部為空心軸,所述水冷腔67通至所述空心軸。這樣磨機軸承內部的空心軸的溫度也得到了保證,防止高溫物料影響磨機空心軸外部軸承溫度。進一步地,所述筒體66還包括襯板612,所述襯板612設置在所述外殼611內側,所述襯板612為耐高溫不銹鋼。進一步地,所述筒體66還包括保溫層68,所述保溫層68設在所述外殼611和所述襯板612之間,所述保溫層68的材質為石棉保溫板,一方面減少高溫物料的熱量流失,另一方面,減少高溫物料和外殼之間的熱量傳導。進一步地,所述筒體66還包括螺旋板69,一方面增加了鋼球610和襯板612的接觸面積,提高了磨制效率,另一方面,在磨機的旋轉過程中,螺旋板69有利于把鋼球610提高到更高的高度,增加了鋼球610下落的沖擊力,也有利于提高磨制效率。另一方面,也有利于推進物料的有序前進。螺旋板69結構和安裝見圖6,其結構特點如下:(1)設定磨粉機6公稱直徑為D,螺旋板69弧度半徑為0.1~0.2D,螺旋板69弧度為120°;(2)螺旋板69通過螺旋板支撐613和固定螺栓、固定螺母或其他緊固件614固定在筒體上,優選地,內部設置8條螺旋板均勻布置,每個螺旋板利用兩排螺栓固定;(3)襯板612采用耐高溫不銹鋼,優選地,規格為310S不銹鋼,根據目前的內高溫不銹鋼的耐溫條件,耐溫按照1200℃設計;(4)由于襯板612的改進,可以增加磨制面積1倍以上,同時保證了鋼球610的提升高度,通過以上手段使單位體積的磨機在不增加能耗的前提下產能大幅度提高。本發明還提供一種半焦磨制的方法,其特征在于,將所述熱解爐1生產的高溫半焦和所述原煤倉4內的所述原煤,分別通過所述高溫調速給料機2和所述給煤機5給入所述磨粉機6,所述磨粉機6在兩端軸承5支撐的條件下旋轉磨制,磨制結束后,將產生的所述煤粉和焦粉從所述出料口排出;加料前將冷卻水從所述冷卻水進口62輸至所述水冷腔67,在所述水冷腔67內循環,從所述冷卻水出口64排出。進一步地,所述方法還包括:利用來自所述高溫收塵器8的鍋爐廢氣,將所述磨粉機6磨制后得到的合格粉料吹入所述高溫收塵器8;所述合格粉料經過所述高溫收塵器8收塵后,再利用氮氣10將所述高壓輸送泵9內的所述煤粉和焦粉送入所述煤粉鍋爐11;將所述助燃風機7產生的助燃風輸至所述煤粉鍋爐11和所述煤粉和焦粉一起燃燒,然后將產生的蒸汽輸至汽輪機發電。具體地,將給入所述磨粉機6的所述熱解爐1生產的高溫半焦和所述原煤倉4內的原煤的比例控制為1:0.5-2。作為優選的實施方案,通過所述高溫調速給料機2和所述給煤機5,調節所述熱解爐1生產的高溫半焦和所述原煤倉4內的原煤進入所述磨粉機6的速度,將所述熱解爐1生產的高溫半焦和所述原煤倉4內的原煤混合后的溫度控制在450-750℃。具體地,通過調節所述水冷腔67的所述冷卻水流量,將所述外殼611溫度控制在200℃以下。根據圖6,本發明的高溫半焦直接磨制的具體工藝流程如下:熱解爐1生產的高溫半焦(700-900℃)通過高溫調速給料機2按照一定速度進入高溫高效磨粉機6,原煤倉4內部的原煤通過調速給煤機按照一定的速度進入磨粉機6,半焦和原煤按照一定的比例混合。原煤和半焦在高溫高效磨粉機內部混合磨制,同時原煤利用高溫半焦的熱量升溫烘干。原煤半焦磨制成合格的煤粉(焦粉)后通過廢氣鼓風機3吹出的鍋爐廢氣,送到煤粉鍋爐11燃燒發電。根據圖7,磨制完的混合粉在廢氣鼓風機3的帶動下進入煤粉鍋爐11燃燒的具體工藝流程如下:廢氣鼓風機3利用鍋爐廢氣把磨粉機6內的合格粉料吹入高溫收塵器,焦粉(煤粉)通過收塵后進入高壓輸送泵9,廢氣通過收塵器后排出,80%回到廢氣鼓風機3繼續使用,高壓輸送泵9內的煤粉通過少量氮氣10送入煤粉鍋爐11,助燃風機7產生的助燃風和煤粉一起進入煤粉鍋爐11燃燒,產生的蒸汽進入汽輪機發電。廢氣鼓風量10萬Nm3/h。其中8萬Nm3/h為循環使用,剩余排放。煤粉按照100t/h左右進入鍋爐,其中輸送氮氣量為3000Nm3/h,助燃風量為80萬Nm3/h,由于氮氣和助燃風相比非常微小,對煤粉(焦粉)燃燒基本沒有影響。下面參考具體實施例,對本發明進行描述,需要說明的是,實施例僅僅是描述性的,而不以任何方式限制本發明。實施例1本實施例提出了一種高溫半焦磨制系統和磨制方法,褐煤通過干燥后進入熱解爐,生成半焦,半焦和動力煤按照一定比例進入磨煤機磨制干燥,磨成煤粉后進入煤粉鍋爐燃燒產生蒸汽去汽輪機發電。褐煤的技術數據如表1:表1:褐煤的技術數據:褐煤的下煤量設計為120t/h,通過給料機進入干燥機,通過干燥后褐煤的水分Mt≤10%,然后進入熱解爐熱解。褐煤熱解后產生半焦,產量為65t/h,半焦出口溫度700℃,半焦參數如下:表2:高溫半焦參數高溫半焦和原煤倉內的原煤按照2:1的比例進入磨煤機,原煤倉內的原煤參數如下:表3原煤倉原煤煤基礎數據進入磨煤機后,兩種物料再和助燃風混合,混合后溫度為550℃左右,磨制完的混合粉在鼓風機的帶動下進入煤粉鍋爐燃燒,混合粉產量為95t/h。表4磨機出口混合粉參數溫度粒度(-200目)揮發分Vad產量(t/h)煙氣量量(Nm3/h)550℃≥75%10.595100000實施例2本實施例與上述實施例1所用系統一樣,但工藝條件不同,如下所述。褐煤的技術數據如表1:表1:褐煤的技術數據:褐煤的下煤量設計為110t/h,通過給料機進入干燥機,通過干燥后褐煤的水分Mt≤10%,然后進入熱解爐熱解。褐煤熱解后產生半焦,產量為60t/h,半焦出口溫度900℃,半焦參數如下:表2:高溫半焦參數高溫半焦和原煤倉內的原煤按照1:1的比例進入磨煤機,原煤倉內的原煤參數如下:表3原煤倉原煤煤基礎數據進入磨煤機后,兩種物料再和助燃風混合,混合后溫度為750℃左右,磨制完的混合粉在鼓風機的帶動下進入煤粉鍋爐燃燒,混合粉產量為120t/h。表4磨機出口混合粉參數溫度粒度(-200目)揮發分Vad產量(t/h)煙氣量量(Nm3/h)750℃≥75%10.5120100000實施例3本實施例與上述實施例1所用系統一樣,但工藝條件不同,如下所述。褐煤的技術數據如表1:表1:褐煤的技術數據:褐煤的下煤量設計為100t/h,通過給料機進入干燥機,通過干燥后褐煤的水分Mt≤10%,然后進入熱解爐熱解。褐煤熱解后產生半焦,產量為60t/h,半焦出口溫度700℃,半焦參數如下:表2:高溫半焦參數高溫半焦和原煤倉內的原煤按照1:2的比例進入磨煤機,原煤倉內的原煤參數如下:表3原煤倉原煤煤基礎數據進入磨煤機后,兩種物料再和助燃風混合,混合后溫度為450℃左右,磨制完的混合粉在鼓風機的帶動下進入煤粉鍋爐燃燒,混合粉產量為180t/h。表4磨機出口混合粉參數溫度粒度(-200目)揮發分Vad產量(t/h)煙氣量量(Nm3/h)450℃≥75%10.7180100000實施例4本實施例與上述實施例1所用系統一樣,但工藝條件不同,如下所述。褐煤的技術數據如表1:表1:褐煤的技術數據:褐煤的下煤量設計為110t/h,通過給料機進入干燥機,通過干燥后褐煤的水分Mt≤10%,然后進入熱解爐熱解。褐煤熱解后產生半焦,產量為65t/h,半焦出口溫度800℃,半焦參數如下:表2:高溫半焦參數高溫半焦和原煤倉內的原煤按照1:1.2的比例進入磨煤機,原煤倉內的原煤參數如下:表3原煤倉原煤煤基礎數據進入磨煤機后,兩種物料再和助燃風混合,混合后溫度為650℃左右,磨制完的混合粉在鼓風機的帶動下進入煤粉鍋爐燃燒,混合粉產量為140t/h。表4磨機出口混合粉參數溫度粒度(-200目)揮發分Vad產量(t/h)煙氣量量(Nm3/h)650℃≥75%10.3140100000當前第1頁1 2 3