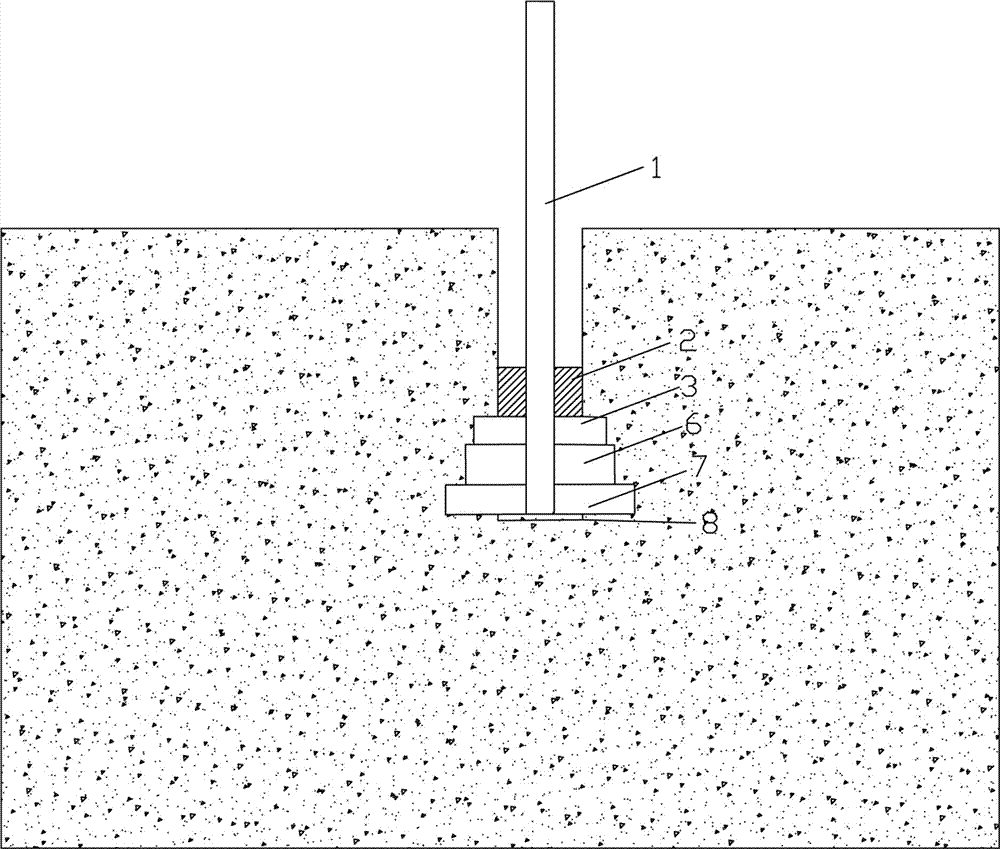
本發明涉及土層錨固領域,尤其是一種土層錨固中大幅提高抗拔力的裝置及方法。
背景技術:
:土層錨固技術起源于20個世紀,1969年在墨西哥召開的第七屆國際土力學和基礎工程會議上,曾把土層錨桿技術作為單獨的討論議題。七十年代以后,在召開的多次地區性國際會議上,均有涉及有關錨桿技術的經驗與研究介紹。當前錨桿技術的試驗和理論研究仍在不斷發展之中。八十年代以來,瑞典、德國、美國、英國、日本等國家分別研制了多種不同類型的錨桿施工工具和灌漿工藝,各國還各自制定了錨桿設計和施工的技術規程。錨桿技術在經濟建設中正起著越來越重要的作用。土層錨桿在交通、水利、建筑、電力、市政、采礦等領域有著廣泛的應用。在邊坡治理工程中,錨桿支護是一種最為常見的加固方式,錨桿錨固技術以其顯著的技術經濟效益,獲得了廣泛的應用。據不完全統計,僅2005年國內外各類巖石錨桿已達600余種,使用量就已達2.5億根之多。提高錨桿抗拔力在錨桿錨固工程中具有極高的經濟效益。現有試驗研究成果指出,錨桿錨固體在受到圍壓下,其極限抗拔力會有較大程度的增加。因此,創造并利用錨桿鉆孔周圍巖體側向壓力,對提高錨桿抗拔力具有重要意義。目前,在施工方法上我國還是以水泥注漿的錨桿為主,在水泥注漿的錨桿中,國內錨固工程一般采用425標號的普通硅酸鹽水泥漿液,其凝結時間長,早期強度低,養護時間長,造成了施工周期過長的問題,亟待一種新的施工工藝改變這一現狀。技術實現要素:本發明所要解決的技術問題是提供一種土層錨固中大幅提高抗拔力的裝置及方法,可以解決常規錨桿在支護過程中錨桿與錨固體發生滑動的問題,大幅提高錨桿抗拔力及支護效果,且結構簡單,材料易得,易操作,大幅節約試驗成本及周期。為解決上述技術問題,本發明所采用的技術方案是:一種土層錨固中大幅提高抗拔力的裝置,包括置于錨洞內的底部帶有剛性圓盤的錨桿,剛性圓盤放置于錨洞底部,剛性圓盤上的錨洞內部空間由下至上分別澆筑有第一膨脹性水泥層、第二膨脹性水泥層、第三膨脹性水泥層…第n膨脹性水泥層,n≥2,第一膨脹性水泥層、第二膨脹性水泥層、第三膨脹性水泥層…第n膨脹性水泥層所用膨脹性水泥漿內的膨脹劑摻量xn依次減少,n=n膨脹劑摻量xn=膨脹劑質量/(膨脹劑質量+水泥質量)×100%,第一膨脹性水泥層所用膨脹性水泥漿內的膨脹劑摻量x1≤35%,第n膨脹性水泥層所用膨脹性水泥漿內膨脹劑摻量xn>0%,第n膨脹性水泥層頂端澆筑有水泥層,水泥層頂端距離錨洞洞口的距離為10-20cm。優選地,各層膨脹性水泥層之間,第n膨脹性水泥層與水泥層之間設置有分隔板。優選地,第一膨脹性水泥層、第二膨脹性水泥層、第三膨脹性水泥層…第n膨脹性水泥層的高度為20-30厘米。優選地,n=3,第一膨脹性水泥層、第二膨脹性水泥層、第三膨脹性水泥層所用膨脹性水泥漿內的膨脹劑摻量xn按5%的量依次遞減。一種采用上述裝置形成多層擴頭大幅提高抗拔力的方法,該方法包括以下步驟:步驟1:鉆孔:在支護邊坡上進行鉆孔形成錨洞;步驟2:制作底部帶有剛性圓盤的錨桿;步驟3:配制不同膨脹劑摻量xn的膨脹性水泥漿,n=1、2、3…n,x1、x2、x3…xn依次減小,x1≤35%、xn>0%;步驟4:植桿及澆筑:將底部帶有剛性圓盤的錨桿垂直放入錨洞,保證錨桿處于錨洞正中位置,利用注漿設備向錨洞內注入膨脹劑摻量為x1的膨脹性水泥漿形成第一膨脹性水泥層,注漿完成后放置分隔板,再在分隔板上澆筑膨脹劑摻量為x2的膨脹性水泥漿形成第二膨脹性水泥層,注漿完成后放置分隔板,以此類推,完成膨脹劑摻量為xn的第n膨脹性水泥層的澆筑;步驟5:在第n膨脹性水泥層的頂端澆筑水泥漿形成水泥層;第一膨脹性水泥層、第二膨脹性水泥層、第三膨脹性水泥層…第n膨脹性水泥層體積膨脹,形成錨固體多層分層擴頭,大幅提高錨桿的抗拔力。本發明的另一種形式為:一種土層錨固中大幅提高抗拔力的裝置,包括置于錨洞內的底部帶有剛性圓盤的錨桿,剛性圓盤放置于錨洞底部,剛性圓盤上的錨洞內部空間由下至上分別澆筑有第一膨脹性水泥層、第二膨脹性水泥層…第n膨脹性水泥層,n≥2,第一膨脹性水泥層、第二膨脹性水泥層…第n膨脹性水泥層所用膨脹性水泥漿內的膨脹劑摻量xn依次減少,n=n膨脹劑摻量xn=膨脹劑質量/(膨脹劑質量+水泥質量)×100%,第一膨脹性水泥層所用膨脹性水泥漿內的膨脹劑摻量x1≤35%,第n膨脹性水泥層所用膨脹性水泥漿內膨脹劑摻量xn>0%,每兩層膨脹性水泥層之間澆筑有水泥層,第n膨脹性水泥層頂端澆筑有頂部水泥層,頂部水泥層頂端距離錨洞洞口的距離為10-20cm。優選地,各膨脹性水泥層與各水泥層之間設置有分隔板。優選地,n=2,第一膨脹性水泥層和第二膨脹性水泥層所用膨脹性水泥漿內的膨脹劑摻量xn按10%的量依次遞減。一種采用上述裝置形成多層擴頭大幅提高抗拔力的方法,該方法包括以下步驟:步驟1:鉆孔:在支護邊坡上進行鉆孔形成錨洞;步驟2:底部帶有剛性圓盤的錨桿;步驟3:配制不同膨脹劑摻量xn的膨脹性水泥漿,n=1、2…n,x1、x2…xn依次減小,x1≤35%、xn>0%;步驟4:植桿及澆筑:將底部帶有剛性圓盤的錨桿垂直放入錨洞,保證錨桿處于錨洞正中位置,利用注漿設備向錨洞內注入膨脹劑摻量為x1的膨脹性水泥漿形成第一膨脹性水泥層,注漿完成后放置分隔板,再在分隔板上澆筑水泥層,在水泥層上澆筑膨脹劑摻量為x2的膨脹性水泥漿形成第二膨脹性水泥層,注漿完成后放置分隔板,再澆筑水泥層,以此類推,完成第n膨脹性水泥層及兩層膨脹性水泥層之間水泥層的澆筑;步驟5:在第n膨脹性水泥層的頂端澆筑水泥漿形成頂部水泥層;第一膨脹性水泥層、第二膨脹性水泥層…第n膨脹性水泥層體積膨脹,形成錨固體多層分層擴頭,大幅提高錨桿的抗拔力。本發明提供的一種土層錨固中大幅提高抗拔力的裝置及方法,有益效果如下:1、首次將大幅提高錨桿錨固段漿體中膨脹劑摻量應用于土層錨固技術中,打破了膨脹劑主要應用于靜態爆破和微膨脹混凝土的工程常規,建立大摻量膨脹劑高強預壓錨固理論技術體系。2、在錨洞中注入不同膨脹劑摻量的膨脹水泥漿,通過膨脹性水泥漿擴頭效應,形成錨固體多層分層擴頭,在土體中錨桿抗拔力最大增幅可達480%,大幅降低錨桿接觸水與空氣的概率,提高錨桿的耐久性,從而大幅提高錨桿抗拔力和使用壽命周期。3、不同膨脹劑摻量的膨脹水泥漿可以在錨洞中形成多層擴頭,與其它類錨固技術相比:①節約機械錨固頭費用;②實現土中自動擴頭,節約購置擴頭設備成本(約65萬元);③跳過擴頭工序,縮減錨固支護一半工期。4、在錨桿底部設置剛性圓盤,將拉力型錨桿轉換為壓力型錨桿,從而大幅提高錨桿抗拔力和使用壽命周期。5、可以大幅節約施工成本,縮短施工工期,加快施工進度,提高安全儲備,具有較廣闊的工程運用前景。本發明能解決常規錨桿錨固力不足的問題,通過利用膨脹水泥漿自動擴頭效應,運用新工藝改拉力型錨桿未壓力型錨桿,在最小成本下將錨固力達到最大化,能解決常規錨桿在支護過程中錨桿與錨固體發生滑動的問題,大幅提高錨桿抗拔力及支護效果,且該方法結構簡單,材料易得,易操作,大幅節約試驗成本及周期,廣泛適用于鐵路、公路、隧道、水利工程、采煤礦井坑道及國防、基坑工程、等支護工程中。附圖說明下面結合附圖和實施例對本發明作進一步說明:圖1為本發明實施例一裝置的結構示意圖;圖2為本發明實施例二形成多層擴頭的示意圖;圖3為本發明實施例三膨脹劑摻量為10%的膨脹水泥漿壓力值;圖4為本發明實施例三膨脹劑摻量為15%的膨脹水泥漿壓力值;圖5為本發明實施例三膨脹劑摻量為20%的膨脹水泥漿壓力值;圖6為本發明實施例四裝置的結構示意圖;圖7為本發明實施例五形成多層擴頭的示意圖。具體實施方式實施例一如圖1所示,一種土層錨固中大幅提高抗拔力的裝置,包括置于錨洞5內的底部帶有剛性圓盤8(優選為鐵圓盤)的錨桿1,剛性圓盤8放置于錨洞5底部,剛性圓盤8上的錨洞5內部空間由下至上分別澆筑有第一膨脹性水泥層7、第二膨脹性水泥層6、第三膨脹性水泥層3,第一膨脹性水泥層7所用膨脹性水泥漿內的膨脹劑摻量x1=20%;第二膨脹性水泥層6所用膨脹性水泥漿內的膨脹劑摻量x2=15%;第三膨脹性水泥層6所用膨脹性水泥漿內的膨脹劑摻量x3=10%;膨脹劑摻量xn=膨脹劑質量/(膨脹劑質量+水泥質量)×100%,第三膨脹性水泥層6頂端澆筑有水泥層2,水泥層2頂端距離錨洞5洞口的距離為10-20cm。各層膨脹性水泥層之間,第三膨脹性水泥層6與水泥層2之間設置有分隔板4,分隔板4優選為中心開孔的圓形塑料薄板,中心孔徑應等于錨桿1直徑,外徑小于或等于錨固孔洞孔徑。其目的在于防止注漿時不同含量膨脹水泥漿混漿,避免影響膨脹效果,減小對拉拔力的影響。第一膨脹性水泥層7、第二膨脹性水泥層6、第三膨脹性水泥層3的高度為20-30厘米。實施例二一種采用實施例一所述的裝置形成多層擴頭大幅提高抗拔力的方法,該方法包括以下步驟:步驟1:選取一塊穩定的支護邊坡,將表面的雜物清除并挖出表面的軟土層;步驟2:鉆孔:在支護邊坡上進行鉆孔形成錨洞5,錨洞的高度為1.5米,直徑為6厘米;步驟3:制作底部帶有剛性圓盤8的錨桿1,錨桿1長度為1.8米,外徑為22毫米;步驟4:配制不同膨脹劑摻量xn的膨脹性水泥漿,n=1、2、3…n,x1=20%,x2=15%,x3=10%;配制方法如下:配制膨脹劑含量為10%,15%,20%的膨脹性水泥漿和不含膨脹劑的水泥漿,即取普通硅酸鹽水泥1800g、1700g、1600g,共三組。再取膨脹劑200g、300g、400g,再稱出三組溫水(50攝氏度左右),每組700g,并將組號依次標記為1、2、3,將所稱取的水泥、膨脹劑倒入攪拌桶攪拌均平后再加入水進行攪拌,配制成不同膨脹劑含量如下的膨脹劑的膨脹水泥漿三組:10%、15%、20%。另外再取2000g普通硅酸鹽水泥和700g溫水配制不含膨脹劑的水泥漿。步驟5:植桿及澆筑:將底部帶有剛性圓盤8的錨桿1垂直放入錨洞5,保證錨桿1處于錨洞5正中位置,利用注漿設備向錨洞5內注入膨脹劑摻量為x1的膨脹性水泥漿形成第一膨脹性水泥層7,注漿完成后放置分隔板4,再在分隔板4上澆筑膨脹劑摻量為x2的膨脹性水泥漿形成第二膨脹性水泥層6,注漿完成后放置分隔板4,以此類推,完成膨脹劑摻量為x3的第三膨脹性水泥層6的澆筑;步驟6:在第三膨脹性水泥層6的頂端澆筑水泥漿形成水泥層2;第一膨脹性水泥層7、第二膨脹性水泥層6、第三膨脹性水泥層3體積膨脹,形成錨固體多層分層擴頭,如圖2所示,實現大幅提高錨桿的抗拔力。實施例三對實施例二安裝的裝置進行壓力測試和抗拔力拉拔試驗,在將錨桿1放入錨洞之前在錨桿1上粘貼應變片:根據錨固段長度l等間距(10厘米)粘貼應變片,用錫焊將應變片引線與導線焊接,涂上704密封膠水,并用絕緣膠布包扎后,最后進行應變片電阻測量(一般為120歐姆),以檢測應變片的粘貼效果,將應變片及連接導線用絕緣膠帶固定在錨桿桿體上,以便隨錨桿1一同放入錨洞5內。待所有漿體注漿完成之后利用壓力采集系統,對安裝好的裝置進行壓力測試,即從膨脹水泥漿初凝開始,測試膨脹壓力的變化情況。灌漿完成后的4小時內不間斷測量,待漿體終凝過后,每隔12小時測試一次,直到其膨脹力不變為止;孔洞內不同深度膨脹劑摻量為10%、15%、20%的膨脹水泥漿壓力值如圖3、4和5所示。養護30天后,采用拉拔儀、靜態應變采集儀、百分表等技術手段,進行逐級加載拉拔試驗,測得錨桿拉拔過程中的抗拔力、應變、位移等參數;錨洞孔洞內不同深度膨脹劑摻量為10%、15%、20%的膨脹水泥漿以及不含膨脹劑的水泥漿的最大抗拔力如表1所示:表1不同膨脹劑含量下壓應力最大值與穩定值膨脹劑含量(單孔錨桿)最大抗拔力kn最大膨脹壓應力mpa穩定后膨脹壓應力mpa0127——10%2235.485.4715%2398.288.2620%1683.822.68由圖3-5及表1的數據可知,未加膨脹劑的錨桿與添加不同含量膨脹劑的錨桿最大抗力相差近一倍,且隨著膨脹劑含量的增加錨桿抗拔力呈現遞增趨勢,故本發明所述的一種土層錨固中大幅提高抗拔力的裝置及方法,不僅提高錨桿的抗拔力,減小了錨桿錨固性能失效的風險,還具有較廣闊的工程運用前景實施例四如圖6所示,一種土層錨固中大幅提高抗拔力的裝置,包括置于錨洞7內的底部帶有剛性圓盤6的錨桿1,剛性圓盤6放置于錨洞7底部,剛性圓盤6上的錨洞7內部空間由下至上分別澆筑有第一膨脹性水泥層5、第二膨脹性水泥層3,第一膨脹性水泥層5所用膨脹性水泥漿內的膨脹劑摻量x1=20%、第二膨脹性水泥層3所用膨脹性水泥漿內的膨脹劑摻量x2=10%;膨脹劑摻量xn=膨脹劑質量/(膨脹劑質量+水泥質量)×100%,第一膨脹性水泥層5和第二膨脹性水泥層3之間澆筑有不含膨脹劑的水泥層4,第二膨脹性水泥層3頂端澆筑有頂部水泥層2,頂部水泥層2頂端距離錨洞5洞口的距離為10-20cm。各膨脹性水泥層與各水泥層之間設置有分隔板8。實施例五一種采用實施例四所述的裝置形成多層擴頭大幅提高抗拔力的方法,該方法包括以下步驟:步驟1:選取一塊穩定的支護邊坡,將表面的雜物清除并挖出表面的軟土層;步驟2:鉆孔:在支護邊坡上進行鉆孔形成錨洞5,錨洞的高度為1.5米,直徑為6厘米;步驟3:制作底部帶有剛性圓盤8的錨桿1,錨桿1長度為1.8米,外徑為22毫米;步驟4:配制不同膨脹劑摻量xn的膨脹性水泥漿,n=1、2、3…n,x1=20%,x2=10%;步驟5:植桿及澆筑:將底部帶有剛性圓盤6的錨桿1垂直放入錨洞7,保證錨桿1處于錨洞7正中位置,利用注漿設備向錨洞7內注入膨脹劑摻量為x1的膨脹性水泥漿形成第一膨脹性水泥層5,注漿完成后放置分隔板8,再在分隔板8上澆筑水泥層,在水泥層上澆筑膨脹劑摻量為x2的膨脹性水泥漿形成第二膨脹性水泥層6,注漿完成后放置分隔板8;步驟6:在第二膨脹性水泥層6的頂端澆筑不含膨脹劑的水泥漿形成頂部水泥層2;第一膨脹性水泥層5、第二膨脹性水泥層3體積膨脹,形成錨固體多層分層擴頭,如圖7所示,實現大幅提高錨桿的抗拔力。上述各實施例中所用水泥均為普通硅酸鹽水泥。上述的實施例僅為本發明的優選技術方案,而不應視為對于本發明的限制。本申請中的實施例及實施例中的特征在不沖突的情況下,可以相互任意組合。本發明的保護范圍,應以權利要求記載的技術方案,包括權利要求記載的技術方案中技術特征的等同替換方案等,為保護范圍。即在此范圍內的等同替換改進,也在本發明的保護范圍之內。當前第1頁12