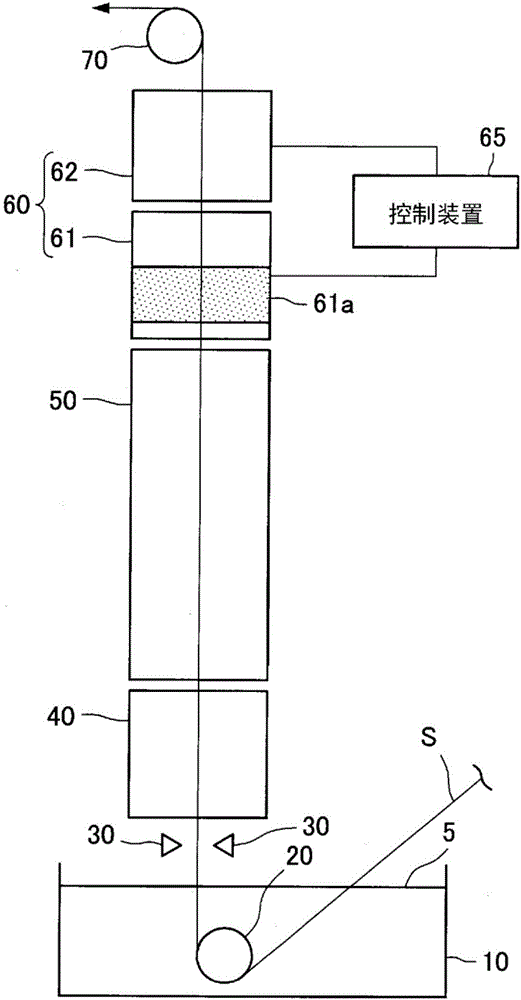
本發明涉及熱鍍鋅的合金化爐中的鋼帶的冷卻方法和冷卻設備。
背景技術:
:在鋼帶的熱鍍鋅處理工序中,鋼帶在通過脫脂、清洗等預處理槽之后,通過退火爐、放入有熔融鋅的鋅鍋,被鉛垂地提起。在合金化爐中對被提起來的鋼帶進行合金化處理。對于合金化爐而言,在鋼帶的提起方向上,自上游側起配置有加熱區域、冷卻區域。即,合金化爐的冷卻區域配置于加熱區域的鉛垂上方。因此,對于冷卻區域中的鋼帶的冷卻而言,為了不給配置于冷卻區域的鉛垂下方的設備帶來滴水等影響而使用氣體冷卻、噴霧冷卻。尤其是,為了提高生產能力,應用冷卻能力較高的噴霧冷卻(氣水冷卻)的做法很有效果。但是,若使用噴霧冷卻,則在為了對鋼帶進行強冷卻而以大水量進行噴霧的情況下,會在鋼帶的寬度方向上產生溫度不均。該溫度不均導致產生皺疤、合金卷曲(日文:合金巻き)等品質不良。針對這樣的問題,例如,在專利文獻1中,公開了一種合金化爐輸出側氣水冷卻方法,在該氣水冷卻方法中,通過調整鋼帶的冷卻模式來抑制過冷所導致的寬度方向上的溫度偏差。在專利文獻1中,以改變冷卻區域的前段與后段之間的冷卻比而對后段進行緩冷的方式來冷卻鋼帶,以抑制滴水所導致的冷卻偏差并使其成為折斷極限溫度不均以下。另外,在專利文獻2中,公開了一種合金化處理過程的冷卻方法,在該冷卻方法中,通過根據冷卻負荷而相應地分開使用氣體冷卻和氣水冷卻,從而避免過渡沸騰并抑制寬度方向上的溫度偏差。并且,在專利文獻3中,公開了一種密集地配置鋼帶的寬度方向中央部的噴嘴并設置用于遮擋噴嘴的閘門的技術。另外,在下述專利文獻4中,公開了如下一種技術:為了使冷卻區域的輸出側溫度為240℃以下以防止在氣水冷卻設備的輸出側產生頸縮、鋼板的彎曲,根據預定的關系式對張力值和溫度不均進行控制。另外,在下述專利文獻5中,公開了如下一種技術:為了使鍍層中的Fe濃度量為適當的量,針對每個區域分開使用氣水冷卻和利用氣體進行的冷卻,以使得不進入會產生冷卻偏差的過渡沸騰區域。現有技術文獻專利文獻專利文獻1:日本特開2006-111945號公報專利文獻2:日本特開平11-43758號公報專利文獻3:日本特公平7-65153號公報專利文獻4:日本特開平9-268358號公報專利文獻5:日本特開2000-256818號公報技術實現要素:發明要解決的問題但是,在上述專利文獻1所記載的冷卻方法中,由于是利用對前段進行高負荷冷卻并對后段進行緩慢冷卻的冷卻模式來消除溫度不均的方法,因此,在兼顧冷卻區域的冷卻能力確保和溫度不均的消除這兩方面時存在極限。另外,在上述專利文獻2所記載的冷卻方法中,分開使用了氣體冷卻和氣水冷卻,但是可明確的是,在該情況下也是,在氣體冷卻時冷卻區域的冷卻能力降低。即,不管在上述專利文獻1和專利文獻2中的哪一種方法中,對于消除高速通板條件下的溫度不均而言效果都受到限制,其結果,不能以高速進行通板,從而生產率降低。另外,在使用上述專利文獻3所公開的技術的情況下,閘門會妨礙霧沫的流動或引起滴水,因此無法應用。另外,密集地配置于中央部的噴嘴會使中央部的水流量密度在驟冷點附近增加,使驟冷點溫度上升而導致寬度方向上的冷卻不均。并且,上述專利文獻4所公開的技術是以鋼板的張力值為基礎對能夠容許的溫度不均進行設定的技術,但由于無法極端地改變鋼板的張力值,因此無法應用于實際的操作。另外,即使使用上述專利文獻5所公開的技術,也難以完全抑制因滴水的影響而產生冷卻不均。因此,本發明是鑒于上述問題而做出的,本發明的目的在于,提供能夠在合金化爐的冷卻區域中對鋼帶進行噴霧冷卻并能夠兼顧生產率和品質的、新的且改良了的鋼帶的冷卻方法和冷卻設備。用于解決問題的方案為了解決上述問題,根據本發明的某一觀點,提供一種鋼帶的冷卻方法,在該冷卻方法中,利用合金化爐的冷卻設備中的噴霧冷卻來冷卻鋼帶,該合金化爐用于對被熱鍍鋅了的鋼帶進行合金化處理。在該冷卻方法中,利用被設在冷卻設備的通板方向上游側的冷卻調整設備,以對通過該冷卻設備的鋼帶噴射的霧沫噴射量成為鋼帶的寬度方向上的邊緣部的霧沫噴射量小于中心部的霧沫噴射量的方式對通過冷卻設備的鋼帶噴射霧沫,利用至少設于冷卻設備的通板方向下游側的霧沫抽吸設備來對向鋼帶噴射出的霧沫的至少一部分進行抽吸,以如下通板速度來冷卻所述鋼帶,在該通板速度下,在自鋼帶的冷卻開始直到冷卻結束為止的期間,鋼帶的溫度在膜態沸騰溫度范圍內,且在所述冷卻設備的總冷卻長度中的至少自通板方向上游側起的該總冷卻長度的2/3以上的范圍內,鋼帶的寬度方向上的邊緣部的溫度為中心部的溫度以上。也可以是,相對于冷卻調整設備的設備長度L(m),鋼帶的速度被設定為利用下述式(a)算出的上限速度Vmax(m/s)以下,Vmax=(L×(Tin-β’)^m×(Tin-γ’))/(α’×th)...(a)其中,Tin(℃)是冷卻設備的入口處的鋼帶的中心部的溫度,th(m)是鋼帶的厚度,α’、β’、γ’、m是常數,是根據熱鍍鋅設備而設定的。常數也可以分別為,α’=1870000、β’=330、γ’=45、m=0.6。另外,為了解決上述問題,根據本發明的另一觀點,提供一種冷卻設備,其是利用合金化爐的噴霧冷卻來進行冷卻的冷卻設備,該合金化爐用于對被熱鍍鋅了的鋼帶進行合金化處理。該冷卻設備包括:冷卻調整設備,其設于冷卻設備的通板方向上游側,能夠對向通過該冷卻設備的鋼帶噴射的霧沫噴射量在鋼帶的寬度方向上進行調整;以及霧沫抽吸設備,其至少設于冷卻設備的通板方向下游側,用于對向鋼帶噴射出的霧沫的至少一部分進行抽吸,冷卻調整設備對向通過該冷卻設備的鋼帶噴射的霧沫噴射量進行調整,使得鋼帶的寬度方向上的邊緣部的霧沫噴射量小于中心部的霧沫噴射量,該冷卻調整設備具有如下那樣的鋼帶的通板方向上的設備長度,使得在自鋼帶的冷卻開始直到冷卻結束為止的期間,使鋼帶的溫度在膜態沸騰溫度范圍內,且在冷卻設備的總冷卻長度中的至少自通板方向上游側起的該總冷卻長度的2/3以上的范圍內,使鋼帶的寬度方向上的邊緣部的溫度為中心部的溫度以上。也可以是,冷卻調整設備以使該冷卻調整設備在鋼帶的通板方向上的設備長度L(m)滿足下述式(b)的方式設置,L≥(α×V×th)/((Tin-β)^m)×(Tin-γ))...(b)其中,Tin(℃)是冷卻設備的入口處的鋼帶的中心部的溫度,V(m/s)是鋼帶的速度,th(m)是鋼帶的厚度,α、β、γ、m是常數,是根據熱鍍鋅設備而設定的。常數也可以分別為,α=1700000、β=330、γ=45、m=0.6。另外,也可以是,冷卻調整設備在通板方向上包括多個集管,該集管由沿著寬度方向配置的多個噴嘴形成,各集管以在鋼帶的寬度方向邊緣部不對鋼帶噴射霧沫的方式構成。也可以是,冷卻調整設備的各所述集管以在鋼帶的寬度方向中心部對鋼帶噴射霧沫的噴嘴的數量自通板方向上游朝向下游去增加的方式的構成。發明的效果如以上說明那樣,采用本發明,能夠提供能在合金化爐的冷卻區域中對鋼帶進行噴霧冷卻并兼顧生產率和品質的鋼帶的冷卻方法和冷卻設備。附圖說明圖1是表示設有本發明的實施方式的冷卻設備的熱鍍鋅設備的概略結構的概略說明圖。圖2是表示正通過冷卻區域的鋼帶的寬度方向和長度方向上的板溫分布的說明圖。圖3是表示利用該實施方式的合金化爐的冷卻區域進行板溫控制的概略的說明圖。圖4是表示冷卻水量與驟冷溫度之間的關系和冷卻水量與鋼帶的中心部的溫度之間的關系的圖表。圖5是表示冷卻水量與寬度方向上的溫度分布的改善效果之間的關系的圖表。圖6是表示本實施方式的冷卻區域60的一結構例的說明圖。圖7是表示具有該實施方式的冷卻調整設備的冷卻區域前段部的一結構例的說明圖。圖8是表示氣水集管的一結構例的說明圖。圖9是對冷卻調整設備由一級氣水集管構成時的冷卻調整設備的設備長度進行說明的說明圖。圖10是作為比較例6而表示自冷卻區域的最終段側設有冷卻調整設備的情況下的、正通過冷卻區域的鋼帶的寬度方向和長度方向上的板溫分布的說明圖。具體實施方式下面,參照附圖來詳細說明本發明的優選實施方式。此外,在本說明書和附圖中,對于實質上具有相同功能結構的構成要件,通過標注相同的附圖標記而省略重復說明。<1.熱鍍鋅設備的概要>首先,參照圖1說明設有本發明的實施方式的冷卻設備的熱鍍鋅設備的概略結構。圖1是表示設有本實施方式的冷卻設備的熱鍍鋅設備的概略結構的概略說明圖。作為利用本實施方式的熱鍍鋅設備進行處理的鋼種,存在例如極低碳鋼、高張力鋼板等。通常,對厚度0.4mm~3.2mm、寬度600mm~1900mm的鋼材進行處理。如圖1所示,熱鍍鋅設備包括放入有用于對鋼帶S的表面進行鍍層處理的熔融鋅5的鋅鍋10、用于對附著于鋼帶S的鍍層的量進行調整的一對氣體噴嘴30、以及由加熱區域40、保熱區域50和冷卻區域60組成的合金化爐。此外,雖然本實施方式的熱鍍鋅設備包括保熱區域50,但本發明并不限定于該例子,也能夠應用不包括保熱區域50的熱鍍鋅設備。在熱鍍鋅設備中,使鋼帶S進入放入有熔融鋅5的鋅鍋10,利用被浸漬于熔融鋅5的沉沒輥20將鋼帶S鉛垂地提起。對于被提起來的鋼帶S,利用自氣體噴嘴30噴射的擦拭氣體(日文:ワイピングガス)將附著于鋼帶S的表面的鍍層的量調整為預定量。之后,一邊將鋼帶S進一步鉛垂地提起,一邊利用合金化爐對鋼帶S進行合金化處理。在合金化爐中,首先,利用加熱區域40加熱至鋼帶S的板溫達到大致均勻,之后利用保熱區域50確保合金化時間而產生合金層。之后,利用冷卻區域60對鋼帶S進行冷卻,并利用上輥(日文:トップロール)70將鋼帶S向接下來的工序輸送。本實施方式的合金化爐的冷卻區域60包括設于鋼帶S的通板方向上游側(即鉛垂下方側(鋅鍋10側))的冷卻區域前段部61和相對于冷卻區域前段部61設于鋼帶S的通板方向下游側(即鉛垂上方側)的冷卻區域后段部62。在冷卻區域前段部61和冷卻區域后段部62中分別配置有多級氣水集管(圖8、圖9的附圖標記63)。在各氣水集管上設有多個以霧沫狀噴射冷卻水的氣水噴射嘴(圖9的附圖標記64)。自氣水噴射嘴噴射出的霧沫被吹送到鋼帶S的表面。向各氣水集管供給的冷卻水量受控制裝置65控制。另外,在冷卻區域60至少設有一對以與鋼帶S的寬度方向上的邊緣部相對的方式配置的霧沫抽吸設備(圖6的附圖標記67)。霧沫抽吸設備至少設于冷卻區域60的通板方向下游側,用于抽吸向鋼帶S噴射出的霧沫的至少一部分。<2.噴霧冷卻的機理>以往,為了提高生產能力,使用冷卻能力較高的噴霧冷卻,但在噴霧冷卻中,當為了對鋼帶S進行強冷卻而以大水量進行噴霧時,在鋼帶S的寬度方向上產生溫度不均,從而成為引起品質不良的原因。在圖2中表示正通過冷卻區域60的鋼帶S的寬度方向和長度方向上的板溫分布。在圖2的長度方向上的溫度分布中,示出了應用本申請之前的中心部的溫度Cb和邊緣部的溫度Eb以及應用本申請之后的中心部的溫度Ca和邊緣部的溫度Ea。另外,在圖2的寬度方向上的溫度分布中,示出了長度方向上的位置A、B、C處的、應用本申請之前的溫度分布和應用本申請之后的溫度分布。位置A是利用冷卻區域60冷卻鋼帶S的冷卻開始位置,位置B是冷卻區域前段部61與冷卻區域后段部62之間的位置,位置C是利用冷卻區域60冷卻鋼帶S的冷卻結束位置。在此,將鋼帶S的寬度方向上的中央部分作為中心部,將鋼帶S的寬度方向兩端側作為邊緣部。對于邊緣部而言,將自鋼帶S的寬度方向端部起到距離為100mm的交界位置為止的范圍作為邊緣部。在應用本申請之前,對于鋼帶S的長度方向上的溫度而言,如圖2所示,邊緣部的溫度Eb低于中心部的溫度Cb。隨著自冷卻區域前段部61向冷卻區域后段部62移動,鋼帶S的中心部的溫度和邊緣部的溫度均逐漸降低,且中心部的溫度和邊緣部的溫度的溫度差逐漸變大。即,當觀察寬度方向上的溫度分布時,隨著輸送鋼帶S,與中心部的溫度相比,邊緣部的溫度變低,在冷卻區域60輸出側即位置C,溫度分布成為向上凸起的形狀。作為在寬度方向上產生溫度分布的原因之一,可列舉出在冷卻區域內部朝向板端部方向去的氣體流動。在來自配置于板寬度方向中央附近的噴嘴的氣體朝向排氣口去時,產生經由冷卻區域60的寬度方向端部的流動,該氣體流動使附著在鋼帶S的表面上的霧沫朝向鋼帶S的兩端流動,因此鋼帶S的邊緣部的板溫降低。對于鋼帶S的溫度較高的部分而言,鋼帶表面的鍍層附著于上輥70而成為品質不良的原因,另一方面,對于鋼帶S的溫度較低的部分而言,溫度低于水的膜態沸騰區域與過渡沸騰區域之間的交界溫度即驟冷溫度而成為局部的過冷卻,從而產生皺疤。因此,需要最終使鋼帶S的寬度方向上的溫度分布均勻。在本實施方式中,為了提高生產能力,作為冷卻區域60中的冷卻方法,也采用噴霧冷卻。為了通過采用噴霧冷卻來提高生產能力并且不產生品質不良,本申請發明人進行了認真研究的結果,完成了能夠抑制鋼帶S的邊緣部的過冷卻且最終使鋼帶S的寬度方向上的溫度分布均勻并避免冷卻不穩定的冷卻設備。即,在本實施方式的合金化爐的冷卻區域60中,為了將鋼帶S穩定地冷卻,在冷卻區域60中,維持使附著于鋼帶S的霧沫進行膜態沸騰的板溫。隨著液體在沸騰狀態下溫度升高,液體的形態從核態沸騰變化至過渡沸騰,進而變化至膜態沸騰。通常,在合金化爐的冷卻區域60的輸入側,鋼帶S的溫度處于水進行膜態沸騰的溫度區域。之后,當隨著鋼帶S的溫度的降低而在鋼帶S的表面上局部地產生水自膜態沸騰變成過渡沸騰的區域時,成為不穩定的冷卻,在鋼帶S上產生溫度不均。因此,在本實施方式中,在冷卻區域60中,以維持使附著于鋼帶S的霧沫進行膜態沸騰的板溫的方式進行冷卻。并且,為了抑制鋼帶S的邊緣部的過冷卻,在通板方向上游側,對向鋼帶S噴射的霧沫噴射量進行調整,使得鋼帶S的寬度方向上的邊緣部的霧沫噴射量少于鋼帶S的寬度方向上的中心部的霧沫噴射量。若在鋼帶S的整個寬度方向上以相同的霧沫噴射量來冷卻鋼帶S,則如所述那樣鋼帶S的邊緣部的溫度大大降低,邊緣部與中心部之間的溫度偏差變大。因此,在通板方向上游側,對向鋼帶S噴射的霧沫進行調整而抑制鋼帶S的邊緣部的冷卻,且排除鋼帶S的邊緣部的過量的霧沫而防止通板過程中的鋼帶S的邊緣部的板溫降低。由此,防止邊緣部的過冷卻,如圖2所示,在利用冷卻區域60開始冷卻直到冷卻結束為止的期間,鋼帶S的溫度在膜態沸騰溫度范圍內且鋼帶S的邊緣部的溫度為中心部的溫度以上。當觀察鋼帶S的寬度方向上的溫度分布時,例如位置B處的狀態那樣,成為鋼帶S的寬度方向邊緣部的溫度比鋼帶S的寬度方向中心部的溫度高的溫度曲線。然后,隨著鋼帶S的輸送,如圖2的鋼帶S的長度方向上的分布所示,邊緣部的溫度Ea與中心部的溫度Ca之間的溫度偏差變小,最終能夠使冷卻區域60的輸出側的鋼帶S的寬度方向上的溫度分布大致均勻。即,在利用冷卻區域60開始冷卻直到冷卻結束為止的期間,使鋼帶S的溫度在膜態沸騰溫度范圍內且使鋼帶S的邊緣部的溫度為中心部的溫度以上,由此避免鋼帶S的邊緣部的不穩定的過渡沸騰狀態,防止鋼帶S的品質不良。此外,并非需要在利用冷卻區域60開始冷卻直到冷卻結束為止的整個范圍內使鋼帶S的邊緣部的溫度均為中心部的溫度以上。只要在冷卻區域60的通板方向上的總冷卻長度中的至少自通板方向上游側起的該總冷卻長度的2/3以上的范圍內使鋼帶S的邊緣部的溫度為中心部的溫度以上即可。只要在該范圍內使鋼帶S的邊緣部的溫度為中心部的溫度以上,就能夠將鋼帶S的品質保持在容許范圍內。如圖2所示最終溫度差為零是理想的,在現實中,在產生皺疤的溫度上限與產生合金卷曲的溫度下限之間存在富余,該富余溫度通常為40℃左右。因而,只要在自通板方向上游側起的總冷卻長度的2/3以上的范圍內使鋼帶S的邊緣部的溫度為中心部的溫度以上,就能夠將最終溫度偏差保持在能夠避免皺疤和合金卷曲的溫度范圍內。此外,本見解是根據在實際生產線中對鋼帶S的溫度偏差的產生量進行了調查的結果而研究出的。此時,在總冷卻長度的冷卻中間位置處,鋼帶S的邊緣部的溫度期望比中心部的溫度高20℃以上。即,通過在總冷卻長度的冷卻中間位置處如圖2的位置B那樣成為鋼帶S的寬度方向邊緣部的溫度高于鋼帶S的寬度方向中心部的溫度的溫度曲線,能夠最終使冷卻區域60的輸出側的鋼帶S的寬度方向上的溫度分布大致均勻。<3.利用冷卻區域的冷卻設備進行的鋼帶冷卻>(3-1.鋼帶的冷卻方法)在圖3中表示利用本實施方式的合金化爐的冷卻區域60進行板溫控制的概略。如圖3所示,鋼帶S通過冷卻區域60而被冷卻到目標終點溫度。通常,在熱鍍鋅處理中,鋼帶S在合金化爐的冷卻區域60的輸入側的溫度為大約450℃~600℃,終點溫度為300℃~400℃左右。另外,圖3所示的驟冷溫度Tq是水的膜態沸騰區域與過渡沸騰區域之間的交界溫度。比驟冷溫度Tq高的溫度范圍是水在鋼帶S的表面上發生膜態沸騰的膜態沸騰溫度范圍。驟冷溫度Tq因冷卻條件而變化,當以大水量對鋼帶S進行強冷卻時,驟冷溫度Tq存在上升的傾向。如圖3所示,終點溫度與驟冷溫度Tq之間的溫度差小于冷卻區域60的輸入側的板溫與驟冷溫度Tq之間的溫度差。因而,當在冷卻區域后段部62對鋼帶S進行強冷卻時,驟冷溫度Tq上升,終點溫度與驟冷溫度Tq之間的溫度差變得更小。這樣一來,霧沫在冷卻區域后段部62發生過渡沸騰的可能性變高,有可能使鋼帶S產生溫度不均。在本實施方式的冷卻區域60中,在冷卻區域60的通板方向上游側以大水量積極地冷卻鋼帶S,并使板溫始終不會成為驟冷溫度Tq以下。具體而言,在冷卻區域前段部61的通板方向上游側設有冷卻調整設備61a,該冷卻調整設備61a用于對向通過冷卻區域60的鋼帶S噴射的霧沫的噴射量在鋼帶S的寬度方向上進行調整。冷卻調整設備61a進行調整,使得對鋼帶S的寬度方向上的中心部積極地進行冷卻并抑制邊緣部的冷卻。通過設置冷卻調整設備61a,從而使鋼帶S的溫度不會成為水自膜態沸騰變成過渡沸騰的驟冷溫度以下,且不使鋼帶S的寬度方向上的溫度分布變得劇烈。將冷卻調整設備61a設于冷卻區域前段部61的通板方向上游側的理由在于,如所述那樣,與將冷卻調整設備61a設于冷卻區域60的通板方向下游側相比,在鋼帶S的溫度控制幅度上具有富余。由于鋼帶S的目標終點溫度處于水的驟冷溫度附近,因此,為了使鋼帶S的溫度不會成為驟冷溫度以下,要求控制裝置65具有較高的控制精度。因此,期望的是,在冷卻區域前段部61的通板方向上游側設置冷卻調整設備61a,以大水量來積極地冷卻鋼帶S。另外,在本實施方式的冷卻區域60中,為了使驟冷點的位置變化的影響最小化而設有霧沫抽吸設備67,其對向鋼帶S噴射出的霧沫的至少一部分連同存在于冷卻區域60內的空氣一起進行抽吸。由此,能夠對導致滴水的剩余的霧沫進行抽吸,從而能夠防止剩余的霧沫作為滴水而掛在鋼帶S上。該霧沫抽吸設備67優選至少設于冷卻區域60中的與鋼帶S的邊緣部相對的部分的附近。通過將霧沫抽吸設備67設于該位置,能夠更有效地對在邊緣部會導致滴水的剩余的霧沫進行抽吸。另外,該霧沫抽吸設備67優選至少設于冷卻區域60的通板方向下游側。在鋼帶S的溫度處于更低的狀態的通板方向上的下游側,因滴水而產生驟冷點位置的變化、沸騰狀態自膜態沸騰狀態向過渡沸騰狀態轉變的可能性較高。因而,通過將霧沫抽吸設備67重點地設于冷卻區域60的通板方向下游側,能夠更有效地抑制滴水所引起的溫度偏差。此外,對于設于冷卻區域60的霧沫抽吸設備67的個數,并沒有特別限定,只要根據冷卻區域60的大小、應當自冷卻區域60抽吸的霧沫的量等適當設定即可。利用霧沫抽吸設備67抽吸剩余霧沫的抽吸量受控制裝置65控制。控制裝置65通過對冷卻調整設備61a和霧沫抽吸設備67這兩者進行控制,能夠更高效地對鋼帶S的冷卻狀態實施管理。在此,當被霧沫抽吸設備67抽吸的霧沫的量過少時,會產生殘留的剩余霧沫所引起的滴水,當被抽吸的霧沫的量過多時,不能對鋼帶S充分地進行冷卻。因此,優選的是,在控制裝置65的控制下使霧沫抽吸設備67所抽吸的霧沫的量在能夠防止產生滴水且能夠對鋼帶S充分地進行冷卻的、預定的范圍內。能夠通過公知的方法對利用霧沫抽吸設備67所抽吸的、排出空氣和霧沫的量進行控制,例如,能夠利用在霧沫抽吸設備67的霧沫吸入口附近設置的壓力計(圖6的附圖標記69)的值來進行控制。即,只要利用設于霧沫抽吸口附近的壓力計對霧沫抽吸口附近的鋼帶S的中心部的壓力值進行測量并以使測得的壓力值成為負壓的方式對設于霧沫抽吸設備67的排氣風機的風門開度進行調整即可。另外,為了利用冷卻調整設備61a在通板方向上的有限的設備長度對寬度方向上的溫度分布進行調整,需要以大水量來使用冷卻調整設備61a。另一方面,在膜態沸騰區域中使用冷卻調整設備61a時,為了避免驟冷溫度Tq的上升,期望以小水量來使用冷卻調整設備61a。這樣,在僅設置冷卻調整設備61a的情況下,用于實現寬度方向上的溫度分布的調整的條件和用于實現膜態沸騰區域中的穩定冷卻的條件成為相反的要件而不容易兼顧。不必要地延長冷卻調整設備61a的設備長度的做法導致如下問題:設備變得復雜而設置成本變高這樣的問題、在不需要調整寬度方向上的溫度分布的對象材料的情況下反而使邊緣部的溫度變高這樣的問題。因此,本申請發明人對用于實現抑制寬度方向上的溫度分布和維持膜態沸騰條件的設備進行了研究,結果發現,只要使冷卻調整設備61a的設備長度L(m)滿足以下的式(1)即可。L≥(α×V×th)/((Tin-β)^m)×(Tin-γ))...(1)其中,將冷卻區域60的入口處的鋼帶S的中心部的溫度設為Tin(℃),將鋼帶S的速度設為V(m/s),將鋼帶的厚度設為th(m)。另外,α、β、γ、m是常數,是根據熱鍍鋅設備而設定的。本申請發明人在各種操作條件下對與冷卻調整設備61a的水量相對應的寬度方向上的溫度分布調整能力和冷卻穩定性進行了調查。結果發現,在能夠維持膜態沸騰區域的條件之中,存在使寬度方向上的溫度分布變為最平緩的水量。另外,發現了,該水量與冷卻區域60的入口處的鋼帶S的溫度、鋼帶S的速度、鋼帶S的厚度、以及冷卻調整設備61a的設備長度L有關。因此,利用該關系導出了上述式(1),上述式(1)用于對為了獲得寬度方向上的溫度分布調整效果而所需的冷卻調整設備61a的設備長度L進行限定。式(1)是如以下那樣導出的。首先,如上述那樣,當以大水量對鋼帶S進行強冷卻時,驟冷溫度Tq存在上升的傾向。該關系能夠通過使用模擬實際設備的試驗設備來評價鋼帶的冷卻特性而得到。例如圖4所示,驟冷溫度Tq利用下述式(1-1)那樣的冷卻水量Q的一次函數來表示。在式(1-1)中,a、b是常數。Tq=aQ+b...(1-1)另外,如圖4所示,在將冷卻調整設備61a的中心部(寬度方向上的中心)處的鋼帶S的輸入側的溫度Tin、鋼帶S的厚度th、鋼帶S的速度V以及冷卻調整設備61a的設備長度L設為恒定時,如圖4所示,對于冷卻水量Q和鋼帶S的中心部的溫度T,存在冷卻水量Q越大則鋼帶S的中心部的溫度T越低那樣的關系。在此,利用冷卻調整設備61a來改善鋼帶S的中心部與邊緣部之間的溫度差的改善效果ΔT同鋼帶S的中心部的輸入側的溫度Tin與冷卻調整設備61a內的任意的通板方向位置的溫度T1之差存在正比關系。即,寬度方向上的溫度分布的改善效果ΔT利用下述式(1-2)來表示。在式(1-2)中,α是常數。ΔT=α(Tin-T1)...(1-2)另一方面,為了使鋼帶S的溫度不會冷卻到小于驟冷溫度Tq,能夠利用冷卻調整設備61a進行調整的、寬度方向上的溫度分布存在上限。即,如圖5所示,在自點PA起到表示成為驟冷溫度Tq的位置的點PB之間,冷卻水量Q越增加,寬度方向上的溫度分布的改善效果ΔT越高。但是,當鋼帶S的溫度T小于驟冷溫度Tq時,鋼帶S成為局部地過冷卻的狀態,如圖5所示,自點PB朝向點PC去,寬度方向上的溫度分布的改善效果ΔT急劇地降低。因而,能夠利用冷卻調整設備61a進行調整的、寬度方向上的溫度分布成為鋼帶S的溫度為驟冷溫度Tq以上的膜態沸騰溫度范圍(點PA~點PB的范圍)。因此,當將驟冷溫度Tq下的寬度方向上的溫度分布的改善效果設為ΔTmax時,根據式(1-2),能夠利用下述式(1-3)來表示。ΔTmax=α(Tin-Tq)...(1-3)并且,根據需要進行調整的溫度分布偏差,決定冷卻調整設備61a的設備長度L。在此,如下述式(1-4)那樣,上述的能夠調整的溫度分布的改善效果的上限ΔTmax也能夠利用鋼帶S的輸入側的中心部的溫度Tin、鋼帶S的厚度th和鋼帶S的速度V、以及冷卻調整設備61a的設備長度L來表示。ΔTmax=(α·2·h·L·(Tave-Tw))/(ρ·Cp·V·th)...(1-4)其中,Tave是平均板溫,其利用例如鋼帶S的輸入側的中心部的溫度Tin與驟冷溫度Tq之間的平均值來表示。另外,Tw是冷卻水溫,ρ是鋼材密度,Cp是鋼材比熱。當對該式(1-4)的關系、上述式(1-1)、式(1-3)、以及表示冷卻水量Q(l/m2·min)與熱傳遞系數h(W/m2·℃)之間的關系的式(1-5)進行整理時,能夠得到上述式(1)。在式(1-5)中,k是常數。h=kQm...(1-5)此外,此時,上述式(1)的常數α、β、γ如下。α=20280×am/k...(1-7)β=33+b...(1-8)γ=45...(1-9)常數α、β、γ能夠利用使用模擬實際設備的試驗設備來對鋼帶的冷卻特性進行評價而得到的結果來設定,能夠設為,例如α=1700000、β=330、γ=45、m=0.6。此外,冷卻區域60的入口處的鋼帶S的溫度T、鋼帶S的速度V、鋼帶S的厚度th是由鋼種、生產量、預訂尺寸決定的值,因此,利用式(1)算出的L的值不會成為固定的值。因而,冷卻調整設備61a的設備長度L是例如以代表性的操作條件為前提而決定的。另外,在冷卻調整設備61a的設備長度L為恒定時,根據上述式(1)的關系,也可以是,以自下述式(2)算出的鋼帶S的上限速度Vmax以下的速度來生產鋼帶S。α’、β’、γ’、m是常數,是根據熱鍍鋅設備而設定的。能夠設為,例如α’=1700000、β’=330、γ’=45、m=0.6。鋼帶S的速度V因通板對象不同而變化,這些常數是考慮過渡狀態而設定的。Vmax=(L×(Tin-β’)^m×(Tin-γ’))/(α’×th)...(2)這樣,在不能改變冷卻調整設備61a的設備長度L的情況下,通過根據鋼種、生產量、預訂尺寸來改變鋼帶S的上限速度Vmax并以上限速度Vmax以下的速度V來生產鋼帶S,也能夠避免冷卻不均所引起的品質不良并能夠獲得較高的生產率。能夠使用例如向導系統將鋼帶S的速度V通知給操作者,進行更改。另外,對于鋼帶S的寬度方向上的溫度分布,期望沒有溫度分布,但只要保持在預定的溫度范圍內,就不會對品質產生較大的影響。例如,預定的溫度范圍為30℃左右。此外,對于冷卻區域60的輸出側的終點溫度,如上述那樣終點溫度為300℃~400℃左右,當終點溫度高于該范圍時,鋼帶S的表面的鍍層有可能卷繞在上輥70上。因而,進行控制,使得冷卻區域60的輸出側的鋼帶S的寬度方向上的溫度中的最高溫度不高于300℃~400℃。[3-2.冷卻調整設備的結構例]根據圖6~圖9來說明冷卻調整設備61a的一結構。圖6是表示本實施方式的冷卻區域60的一結構例的說明圖。圖7是表示具有本實施方式的冷卻調整設備61a的冷卻區域前段部61的一結構例的說明圖。圖8是表示氣水集管63的一結構例的說明圖。圖9是對冷卻調整設備61a由一級氣水集管63構成時的冷卻調整設備61a的設備長度進行說明的說明圖。本實施方式的冷卻區域60是通過將圖8所示那樣的、沿著鋼帶S的寬度方向排列有多個氣水噴射嘴64的氣水集管63在長度方向上配置多個而構成的。在冷卻區域前段部61和冷卻區域后段部62中,氣水集管63分別設有多級(例如大約30級)。圖7所示那樣的冷卻區域60隔著鋼帶S的通板方向對稱地配置。由此,自表面和背面冷卻鋼帶S。來自氣水噴射嘴64的霧沫噴射量(即,氣水集管63的水量)能夠通過圖8所示的閥66a、66b的開閉來進行調節。能夠利用控制裝置65針對每級來調整閥66a、66b的開閉。冷卻調整設備61a能夠通過如下方式構成:例如利用罩將排列于各氣水集管63的氣水噴射嘴64中的、靠鋼帶S的寬度方向上的邊緣部側的氣水噴射嘴64堵塞而使該邊緣部側的氣水噴射嘴64不噴射霧沫。在圖7的例子中,位于冷卻區域前段部61的通板方向上游側的第1級~第n級的氣水集管63的邊緣部被罩堵塞而形成了未噴射區域63b。因而,在鋼帶S通過冷卻調整設備61a的期間,鋼帶S的與噴射區域63a相對應的中心部被積極地冷卻,而鋼帶S的兩邊緣部的冷卻受到抑制。此外,構成冷卻調整設備61a的氣水集管63的數量n根據利用上述式(1)設定的冷卻調整設備61a的設備長度L或預先設定的冷卻調整設備61a的恒定的設備長度L來進行設定。具體而言,冷卻調整設備61a的設備長度L利用下述式(3)來表示。在此,在冷卻調整設備61a由一級氣水集管63構成時(即,n=1時),如圖9所示,將自氣水噴射嘴64向鋼帶S的表面以相對于垂直的方向呈上下45°的角度θ噴射霧沫的范圍作為冷卻調整設備61a的設備長度L。數學式1在此,p表示在通板方向上相鄰的氣水集管63的間距,d表示鋼帶S與氣水集管63之間的距離。能夠根據上述式(3)來決定構成冷卻調整設備61a的氣水集管63的數量n、設置位置。例如圖7所示,也可以是,在通板方向上游側利用罩將冷卻調整設備61a的、與鋼帶S的兩邊緣部對應的氣水噴射嘴64較多地堵塞而增大未噴射區域63b,并隨著朝向下游側去而自中心部側減少被罩堵塞的氣水噴射嘴64的數量而使未噴射區域63b變小。即,使利用氣水集管63的氣水噴射嘴64向鋼帶S的表面噴射霧沫的噴射區域63a自通板方向上游朝向下游去增大。例如,在鋼帶S的厚度為0.6mm、冷卻區域60的入口的鋼帶溫度為500℃時所需的冷卻調整設備61a的設備長度L如以下的表1那樣進行設定。鋼帶S的速度V越大,需要越長的冷卻調整設備61a。表1鋼帶的速度(m/分鐘)冷卻調整設備的所需長度(m)1200.211500.261800.312500.433000.51由此,能在冷卻開始時有效地抑制鋼帶S的邊緣部的過冷卻并在之后逐漸擴大鋼帶S的冷卻范圍而全面地進行冷卻。尤其是,通過在冷卻開始階段集中地冷卻鋼帶S的中心部并停止邊緣部的冷卻,如圖2所示,在通過冷卻區域60的過程中,能夠使鋼帶S的邊緣部的溫度為中心部的溫度以上。因而,在冷卻區域60中的冷卻結束時,鋼帶S的寬度方向上的溫度分布不會變得劇烈,能夠大致均勻地進行冷卻。對于冷卻區域60中的、比冷卻調整設備61a靠通板方向下游側的氣水集管63、即冷卻區域前段部61的第n+1級之后的氣水集管63和冷卻區域后段部62的所有的氣水集管63而言,自所有的氣水噴射嘴64噴射霧沫。此外,如圖6所示,并不是必須從冷卻區域60的通板方向最上游的第1根氣水集管63起設置冷卻調整設備61a,但為了享受本發明的效果,期望盡量在上游側、可能的話自第1根起設置冷卻調整設備61a。另外,如圖6和圖7所示,霧沫抽吸設備67以與鋼帶S的邊緣部相對的方式設于冷卻區域前段部61的下游側和冷卻區域后段部62的下游側。根據利用壓力計69測得的壓力值,利用該霧沫抽吸設備67,以使中心部的壓力值成為負壓的方式對自氣水集管63噴射出的霧沫抽吸預定量。由此,在冷卻區域前段部61的內部存在能夠在防止產生滴水的同時對鋼帶充分地進行冷卻的霧沫,能夠防止因滴水而產生冷卻不均。圖6和圖7所示的冷卻調整設備61a的結構是一個例子,本實施方式的冷卻區域60的冷卻調整設備61a的結構并不限定于該例子。也可以是,例如,在圖6和圖7中,起初就不設置被罩65堵塞的氣水噴射嘴64,使邊緣部的冷卻停止?;蛘咭部梢允牵皇惯吘壊康睦鋮s完全停止,以比中心部的水量低的水量對邊緣部進行噴霧。另外,圖6和圖7的冷卻調整設備61a以自通板方向上游朝向下游去鋼帶S的中心部的冷卻范圍增大的方式構成,但利用冷卻調整設備61a對中心部進行冷卻的冷卻范圍也可以為恒定。以上,說明了本實施方式的熱鍍鋅處理設備中的合金化爐的冷卻區域60。本實施方式的合金化爐的冷卻區域60在冷卻區域前段部61的通板方向上游側包括用于在鋼帶S的寬度方向上對向通過冷卻區域60的鋼帶S噴射的霧沫的噴射量進行調整的冷卻調整設備61a。在冷卻調整設備61a中,積極地冷卻鋼帶S的中心部,另一方面,停止邊緣部的冷卻或以低水量對邊緣部進行噴射。另外,至少在冷卻區域60中的與鋼帶S的邊緣部相對的部分的附近設有一對霧沫抽吸設備67。此時,通過將冷卻調整設備61a的設備長度L設定為能夠在防止出現鋼帶S的寬度方向上的溫度偏差變大而產生溫度不均的情況的同時、以鋼帶S的板溫不會變為驟冷溫度Tq以下的方式進行冷卻的長度,能夠穩定地冷卻鋼帶S。在本實施方式的合金化爐的冷卻區域60中,能夠利用噴霧冷卻來穩定地冷卻鋼帶,因此,能夠使鋼帶高速地通過并對鋼帶進行處理,從而能夠提高生產率。另外,通過將霧沫抽吸設備67設于上述位置,能夠對可能在邊緣部成為滴水的原因的剩余的霧沫更有效地進行抽吸。實施例作為實施例,在熱鍍鋅處理設備的合金化爐的冷卻區域中,使冷卻調整設備的使用集管數變化而改變冷卻調整設備的設備長度L,對冷卻了熱鍍鋅鋼帶時的、冷卻后的鋼帶的寬度方向上的溫度分布和產品的外觀品位進行了調查。冷卻區域的結構與圖6相同,包括36級氣水集管。其中,第1級~第9級的氣水集管構成冷卻調整設備。在本例子中,冷卻調整設備的邊緣部的水量為零,僅對中心部進行了霧沫噴射。將結果表示在表2中。此外,在表2中,對于冷卻區域中間位置處的溫度差而言,示出了在冷卻區域前段部61與冷卻區域后段部62之間的位置處的、自邊緣部的溫度減去中心部的溫度而得到的值。冷卻區域輸出側處的溫度差也示出了自邊緣部的溫度減去中心部的溫度而得到的值。邊緣部的溫度為距鋼帶的寬度方向端部的距離為100mm的位置處的表面溫度,中心部的溫度為鋼帶的寬度方向中心位置處的表面溫度。表2◎:無(良好),△:略有(劣),×:有(劣)比較例0是不使用作為冷卻調整設備的第1級~第9級的氣水集管的情況、即對鋼帶的整個寬度方向進行噴霧冷卻的情況。在比較例0中,也未使用霧沫抽吸設備。此時,與鋼帶的寬度方向上的中心部相比,邊緣部的板溫大大降低。鋼帶表面的鍍鋅附著于上輥,還產生了皺疤。比較例1是在比較例0的狀態的基礎上設置霧沫抽吸設備的情況。在該情況下,未產生皺疤,但看到鋼帶表面的鍍鋅附著于上輥。實施例1~實施例3是使用了作為冷卻調整設備的第1級~第9級的氣水集管的情況。實施例1~實施例3的冷卻調整設備的長度以滿足上述式(1)的方式被設定為比該長度的下限值長。在實施例1~實施例3的情況下,在利用冷卻調整設備來積極地冷卻鋼帶的寬度方向上的中心部之后,利用比冷卻調整設備靠下游側的氣水集管來對鋼帶的整個寬度方向進行噴霧冷卻,由此,與比較例0和比較例1相比,減輕了邊緣部溫度降低程度。既不會出現鋼帶表面的鍍鋅附著于上輥的情況,也不會產生皺疤。比較例2是使用了作為冷卻調整設備的第1級~第9級的氣水集管的情況,是雖然冷卻調整設備的長度滿足上述式(1)、但未設置霧沫抽吸設備的情況。在該情況下,與比較例0同樣地,與鋼帶的寬度方向上的中心部相比,邊緣部的板溫大大降低,鋼帶表面的鍍鋅附著在上輥,且還產生了皺疤。比較例3~比較例5是減少作為冷卻調整設備的第1級~第9級的氣水集管的使用根數的情況。在比較例3~比較例5中,冷卻調整設備的長度均不滿足上述式(1),冷卻調整設備的長度被設定為短于該長度的下限值。此外,對于比較例3,由于不滿足上述式(1)的關系,因此,鍍鋅少量地附著在上輥的鋼帶表面上。能想到其原因在于,在冷卻過程中,鋼帶的溫度未低于驟冷溫度,但由于冷卻區域中間位置處的鋼帶的寬度方向上的中心部的溫度為比邊緣部的溫度略高的程度,因此,在冷卻區域輸出側的溫度差變大。對于比較例4和比較例5,它們是如下那樣的情況:減少了冷卻調整設備的氣水集管的使用根數,其結果,為了抑制中心部與邊緣部之間的溫度差消除量變少所帶來的影響,增多向冷卻調整設備的各氣水集管供給的水量而想要減少冷卻區域輸出側的中心部與邊緣部之間的溫度差。在比較例4中,冷卻區域輸出側的中心部與邊緣部之間的溫度差變小,但由于在冷卻過程中鋼帶的溫度低于驟冷溫度,因此產生了皺疤。在比較例5中,即使增多向冷卻調整設備的各氣水集管供給的水量,也不能充分地減少中心部與邊緣部之間的溫度差。其結果,冷卻區域出口處的鋼帶的寬度方向上的中心部的溫度變高。另一方面,鋼帶的寬度方向上的邊緣部的溫度降低并低于驟冷溫度。其結果,在比較例5中,鋼帶表面的鍍鋅附著在上輥上,還產生了皺疤。比較例6是將冷卻調整設備設于冷卻區域的最終段側的情況。在比較例6中,冷卻調整設備的長度滿足上述式(1),還設置了霧沫抽吸設備。即,如圖10所示,在冷卻區域中,以與鋼帶S的寬度方向上的邊緣部相對的方式配置的一對霧沫抽吸設備67設于冷卻區域60的通板方向中間位置和輸出側,用于對向鋼帶S噴射出的霧沫的至少一部分進行抽吸。另外,自冷卻區域輸出側朝向通板方向上游側去構成了冷卻調整設備。冷卻調整設備通過利用罩將鋼帶S的寬度方向上的邊緣部側的氣水噴射嘴堵塞、使該邊緣部側的氣水噴射嘴不噴射霧沫而構成。此時,隨著自冷卻區域輸出側朝向通板方向上游側去,未噴射區域63c變小。在比較例6中,在冷卻區域前段部61,鋼帶S的寬度方向全部被冷卻,因此,在冷卻區域的中間位置,鋼帶的寬度方向上的邊緣部的溫度低于中心部的溫度。其結果,在冷卻區域后段部62,即使抑制了邊緣部的冷卻,也不能避免邊緣部的不穩定的過渡沸騰,鋼帶表面的鍍鋅附著于上輥,還產生了皺疤。由本實施例可知,在將冷卻調整設備設于冷卻設備的通板方向上游側時,通過滿足上述式(1),能夠減輕鋼帶的寬度方向上的邊緣部的溫度降低程度而抑制產生溫度不均,從而能夠制造沒有皺疤的良好的產品。另外,示出了還能夠消除鋼帶表面的鍍鋅附著于上輥的情況。以上,參照附圖詳細地說明了本發明的優選實施方式,但本發明并不限定于該例子。很明顯的,只要是具有本發明所屬的
技術領域:
中的通常的知識的人,就能夠在權利要求書中記載的技術思想的范疇內想到各種變更例或修改例,所述變更例或修改例當然也被認為屬于本發明的保護范圍。例如,在上述實施方式中,作為用于冷卻鋼帶的冷卻設備而使用了噴射霧沫的氣水噴嘴(雙組分噴嘴),但本發明并不限定于該例子。例如,也可以利用噴射水的單組分噴嘴來構成冷卻設備。此外,從水質管理的觀點考慮,與水質管理較困難的單組分噴嘴相比,優選使用雙組分噴嘴。附圖標記說明5、熔融鋅;10、鋅鍋;20、沉沒輥;30、氣體噴嘴;40、加熱區域;50、保熱區域;60、冷卻區域;61、冷卻區域前段部;62、冷卻區域后段部;63、氣水集管;63a、噴射區域;63b、未噴射區域;64、氣水噴射嘴;65、控制裝置;70、上輥;S、鋼帶。當前第1頁1 2 3