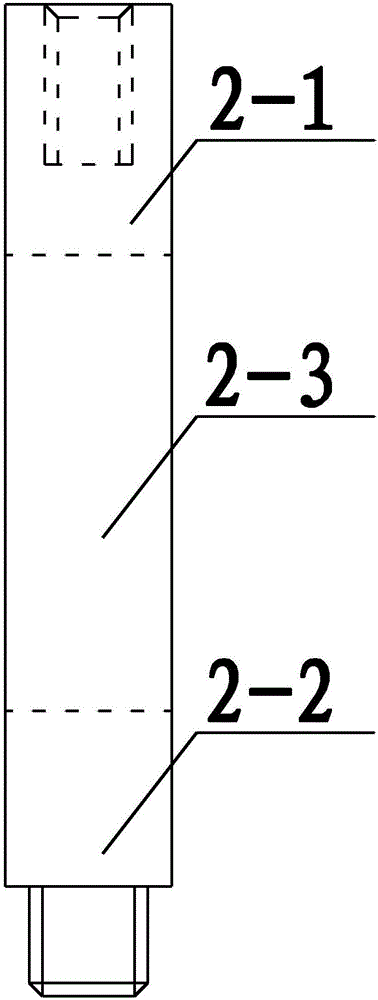
本發明屬于有色金屬冶煉
技術領域:
,具體涉及一種鋁熔體凈化用分段式炭陶復合材料轉子及其制備方法。
背景技術:
:采用旋轉轉子噴吹惰性氣體來除去鋁液中的氫氣和氧化夾雜物是當今世界上一項先進的鋁液凈化技術,該項技術自20世紀70年代在國外問世以來,實現了熔鑄生產在線連續凈化和自動化,其先進合理的凈化工藝給生產廠家帶來了巨大的技術和經濟效益。在這些在線凈化系統中,利用轉子將介質氣體如高純氬氣(或氮氣)輸送到鋁液的底部,并進行攪拌,基于高能擴散和化學驅動原理,通過氣泡將鋁液中的氫氧雜質帶出,達到脫氣除雜的效果。目前,轉子主要采用石墨材料,這是由于石墨材料具有高溫強度高、導電傳熱性好、抗熱震性、耐腐蝕和具有自潤滑性的特點,是一種較好的鋁液凈化轉子材料。但是石墨材料本身存在兩個較為嚴重的缺陷:一是石墨屬于脆性材料,強度和韌性較差;二是石墨材料在空氣中超過450℃開始氧化,較差的力學性能和弱的抗氧化性能導致石墨轉子使用壽命較低,因此如何提高石墨轉子的使用壽命一直是鋁精煉行業使用者和轉子制造廠家重要的研究課題之一。一般地,高壽命石墨轉子應從兩個途徑進行開發,一是提高石墨材質,二是針對局部損耗較大的部位,進行特殊處理,如涂料保護法,套筒保護法等。但是石墨材料本身固有的缺陷無法從根本上解決。技術實現要素:本發明所要解決的技術問題在于針對上述現有技術的不足,提供一種鋁熔體凈化用分段式炭陶復合材料轉子。該轉子相對于現有石墨轉子,在腐蝕氧化區域,利用C/C-SiC復合材料代替原有的涂層或者陶瓷套管,利用SiC材料優異的抗氧化性能和抗腐蝕性能,從根本上解決了石墨轉子材料本身固有的缺陷。為解決上述技術問題,本發明采用的技術方案是:一種鋁熔體凈化用分段式炭陶復合材料轉子,其特征在于,包括石墨段和復合段,所述石墨段和復合段之間為螺紋連接;所述復合段包括C/C復合材料上段和C/C復合材料下段,以及位于C/C復合材料上段和C/C復合材料下段之間的C/C-SiC復合材料段,所述C/C復合材料上段、C/C-SiC復合材料段和C/C復合材料下段為一體式結構。上述的一種鋁熔體凈化用分段式炭陶復合材料轉子,其特征在于,所述石墨段的數量為一個,所述石墨段位于復合段上方。上述的一種鋁熔體凈化用分段式炭陶復合材料轉子,其特征在于,所述石墨段的數量為兩個,所述復合段位于兩個石墨段之間。上述的一種鋁熔體凈化用分段式炭陶復合材料轉子,其特征在于,所述石墨段上設置有外螺紋,復合段上設置有與所述外螺紋相配合的內螺紋。另外,本發明還提供了一種制備上述分段式炭陶復合材料轉子的方法,其特征在于,包括以下步驟:步驟一、將密度為0.20g/cm3~0.50g/cm3的炭纖維預制體增密,得到密度為1.20g/cm3~1.40g/cm3的C/C復合材料;步驟二、將步驟一中所述C/C復合材料機械加工成直徑為50mm~200mm,高度為300mm~500mm的C/C復合材料桿;步驟三、將石墨工裝套裝于步驟二中所述C/C復合材料桿上且位于C/C-SiC復合材料段的部位,所述石墨工裝包括石墨套筒和位于石墨套筒下方的石墨擋圈,所述石墨擋圈的內壁與C/C復合材料桿的外壁緊密配合,石墨套筒的內壁與C/C復合材料桿的外壁之間形成空隙,向所述空隙中填充硅粉,形成組合件;步驟四、將步驟三中所述組合件置于加熱爐中進行反應熔滲處理,或將多個步驟三中所述組合件疊放或并列置于加熱爐中進行反應熔滲處理,出爐后拆除石墨工裝,在套裝石墨工裝的部位形成密度為1.50g/cm3~2.10g/cm3的C/C-SiC復合材料,得到復合段;步驟五、將石墨段和步驟四中所述復合段通過螺紋連接,得到分段式炭陶復合材料轉子。上述的方法,其特征在于,步驟三中所述空隙的厚度為2mm~6mm。上述的方法,其特征在于,步驟三中所述硅粉的質量純度不小于99.99%,硅粉的粒徑不大于2mm。上述的方法,其特征在于,步驟四中所述反應熔滲處理的溫度為1550℃~1750℃,保溫時間為6h~10h。本發明與現有技術相比具有以下優點:1、本發明相對于現有石墨轉子,在腐蝕氧化區域,利用C/C-SiC復合材料代替原有的涂層或者陶瓷套管,利用SiC材料優異的抗氧化性能和抗腐蝕性能,從根本上解決了石墨轉子材料本身固有的缺陷。2、本發明相對傳統反應熔滲工藝,采用石墨工裝,通過仿形結構設計,將硅粉置于石墨套筒內壁和炭/炭復合材料部件外壁之間,在炭/炭復合材料部件外表面形成一層10mm~25mm厚度的碳化硅陶瓷基體,所獲得的C/C-SiC復合材料部件不需要進行機械加工,大幅度降低了陶瓷材料的加工成本。3、本發明通過將多個組合件疊放后同時進行反應熔滲,大幅度提高了生產效率,降低了生產成本。4、采用本發明的方法制備的分段式炭陶復合材料轉子相對于傳統石墨轉子,使用壽命提高3~5倍,可達到2個月以上。下面結合附圖和實施例,對本發明的技術方案做進一步的詳細說明。附圖說明圖1為本發明分段式炭陶復合材料轉子的第一種具體實施方式的結構示意圖。圖2為本發明復合段的第一種具體實施方式的結構示意圖。圖3為本發明組合件的第一種具體實施方式的結構示意圖。圖4為本發明分段式炭陶復合材料轉子的第二種具體實施方式的結構示意圖。圖5為本發明復合段的第二種具體實施方式的結構示意圖。圖6為本發明組合件的第二種具體實施方式的結構示意圖。附圖標記說明:1—石墨段;2—復合段;2-1—C/C復合材料上段;2-2—C/C復合材料下段;2-3—C/C-SiC復合材料段;3—石墨套筒;4—石墨擋圈;5—硅粉;6—C/C復合材料桿。具體實施方式實施例1如圖1和圖2所示,本實施例的鋁熔體凈化用分段式炭陶復合材料轉子,包括石墨段1和復合段2,所述石墨段1和復合段2之間為螺紋連接;所述復合段2包括C/C復合材料上段2-1和C/C復合材料下段2-2,以及位于C/C復合材料上段2-1和C/C復合材料下段2-2之間的C/C-SiC復合材料段2-3,所述C/C復合材料上段2-1、C/C-SiC復合材料段2-3和C/C復合材料下段2-2為一體式結構。本實施例中,所述石墨段1的數量為一個,所述石墨段1位于復合段2上方。本實施例中,所述石墨段1上設置有外螺紋,復合段2上設置有與所述外螺紋相配合的內螺紋。本實施例的分段式炭陶復合材料轉子的制備方法包括以下步驟:步驟一、根據所要制備炭陶復合材料轉子的形狀和性能要求,采用常規方法利用炭纖維、炭布和網胎制成密度為0.20g/cm3的炭纖維預制體,然后將所述炭纖維預制體增密,得到密度為1.20g/cm3的C/C復合材料;步驟二、將步驟一中所述C/C復合材料機械加工成直徑為50mm,高度為300mm的C/C復合材料桿6;步驟三、將石墨工裝套裝于步驟二中所述C/C復合材料桿6上且位于C/C-SiC復合材料段2-3的部位,所述石墨工裝包括石墨套筒3和位于石墨套筒3下方的石墨擋圈4,所述石墨擋圈4的內壁與C/C復合材料桿6的外壁緊密配合,石墨套筒3的內壁與C/C復合材料桿6的外壁之間形成厚度為2mm的空隙,向所述空隙中填充硅粉5,形成組合件(如圖3所示);所述硅粉的質量純度不小于99.99%,硅粉的粒徑為1mm;步驟四、將2~4個步驟三中所述組合件疊放置于加熱爐中進行反應熔滲處理,出爐后拆除石墨工裝,在套裝石墨工裝的部位形成密度為1.50g/cm3的C/C-SiC復合材料,得到復合段2,并在復合段2上機加工內螺紋;所述反應熔滲處理的溫度為1550℃,保溫時間為6h;步驟五、將設置有外螺紋的石墨段1和步驟四中所述復合段2通過螺紋連接,得到分段式炭陶復合材料轉子。實施例2如圖4和圖5所示,本實施例的鋁熔體凈化用分段式炭陶復合材料轉子,包括石墨段1和復合段2,所述石墨段1和復合段2之間為螺紋連接;所述復合段2包括C/C復合材料上段2-1和C/C復合材料下段2-2,以及位于C/C復合材料上段2-1和C/C復合材料下段2-2之間的C/C-SiC復合材料段2-3,所述C/C復合材料上段2-1、C/C-SiC復合材料段2-3和C/C復合材料下段2-2為一體式結構。本實施例中,所述石墨段1的數量為兩個,所述復合段2位于兩個石墨段1之間。本實施例中,所述石墨段1上設置有外螺紋,復合段2上設置有與所述外螺紋相配合的內螺紋。本實施例的分段式炭陶復合材料轉子的制備方法包括以下步驟:步驟一、根據所要制備炭陶復合材料轉子的形狀和性能要求,采用常規方法利用炭纖維、炭布和網胎制成密度為0.40g/cm3的炭纖維預制體,然后將所述炭纖維預制體增密,得到密度為1.30g/cm3的C/C復合材料;步驟二、將步驟一中所述C/C復合材料機械加工成直徑為100mm,高度為400mm的C/C復合材料桿6;步驟三、將石墨工裝套裝于步驟二中所述C/C復合材料桿6上且位于C/C-SiC復合材料段2-3的部位,所述石墨工裝包括石墨套筒3和位于石墨套筒3下方的石墨擋圈4,所述石墨擋圈4的內壁與C/C復合材料桿6的外壁緊密配合,石墨套筒3的內壁與C/C復合材料桿6的外壁之間形成厚度為4mm的空隙,向所述空隙中填充硅粉5,形成組合件(如圖6所示);所述硅粉的質量純度不小于99.99%,硅粉的粒徑為2mm;步驟四、將2~4個步驟三中所述組合件并列置于加熱爐中進行反應熔滲處理,出爐后拆除石墨工裝,在套裝石墨工裝的部位形成密度為1.85g/cm3的C/C-SiC復合材料,得到復合段2,并在復合段2上機加工內螺紋;所述反應熔滲處理的溫度為1600℃,保溫時間為8h;步驟五、將兩個設置有外螺紋的石墨段1和步驟四中所述復合段2通過螺紋連接,得到分段式炭陶復合材料轉子。實施例3如圖4和圖5所示,本實施例的鋁熔體凈化用分段式炭陶復合材料轉子的結構與實施例2相同。本實施例的分段式炭陶復合材料轉子的制備方法包括以下步驟:步驟一、根據所要制備炭陶復合材料轉子的形狀和性能要求,采用常規方法利用炭纖維、炭布和網胎制成密度為0.50g/cm3的炭纖維預制體,然后將所述炭纖維預制體增密,得到密度為1.40g/cm3的C/C復合材料;步驟二、將步驟一中所述C/C復合材料機械加工成直徑為200mm,高度為500mm的C/C復合材料桿6;步驟三、將石墨工裝套裝于步驟二中所述C/C復合材料桿6上且位于C/C-SiC復合材料段2-3的部位,所述石墨工裝包括石墨套筒3和位于石墨套筒3下方的石墨擋圈4,所述石墨擋圈4的內壁與C/C復合材料桿6的外壁緊密配合,石墨套筒3的內壁與C/C復合材料桿6的外壁之間形成厚度為6mm的空隙,向所述空隙中填充硅粉5,形成組合件(如圖6所示);所述硅粉的質量純度不小于99.99%,硅粉的粒徑為1.5mm;步驟四、將步驟三中所述組合件置于加熱爐中進行反應熔滲處理,出爐后拆除石墨工裝,在套裝石墨工裝的部位形成密度為2.10g/cm3的C/C-SiC復合材料,得到復合段2,并在復合段2上機加工內螺紋;所述反應熔滲處理的溫度為1750℃,保溫時間為10h;步驟五、將設置有外螺紋的石墨段1和步驟四中所述復合段2通過螺紋連接,得到分段式炭陶復合材料轉子。對本發明的分段式炭陶復合材料轉子的使用壽命與石墨轉子的使用壽命進行比較,結果見下表:表1不同材料鋁熔體凈化處理用轉子使用壽命對比材料使用壽命(天)石墨轉子20實施例1制備的分段式炭陶復合材料轉子60實施例2制備的分段式炭陶復合材料轉子80實施例3制備的分段式炭陶復合材料轉子100從表1中可以看出,本發明的分段式炭陶復合材料轉子在使用過程中,其使用壽命比石墨轉子明顯延長。以上所述,僅是本發明的較佳實施例,并非對本發明做任何限制,凡是根據發明技術實質對以上實施例所作的任何簡單修改、變更以及等效結構變化,均仍屬于本發明技術方案的保護范圍內。當前第1頁1 2 3