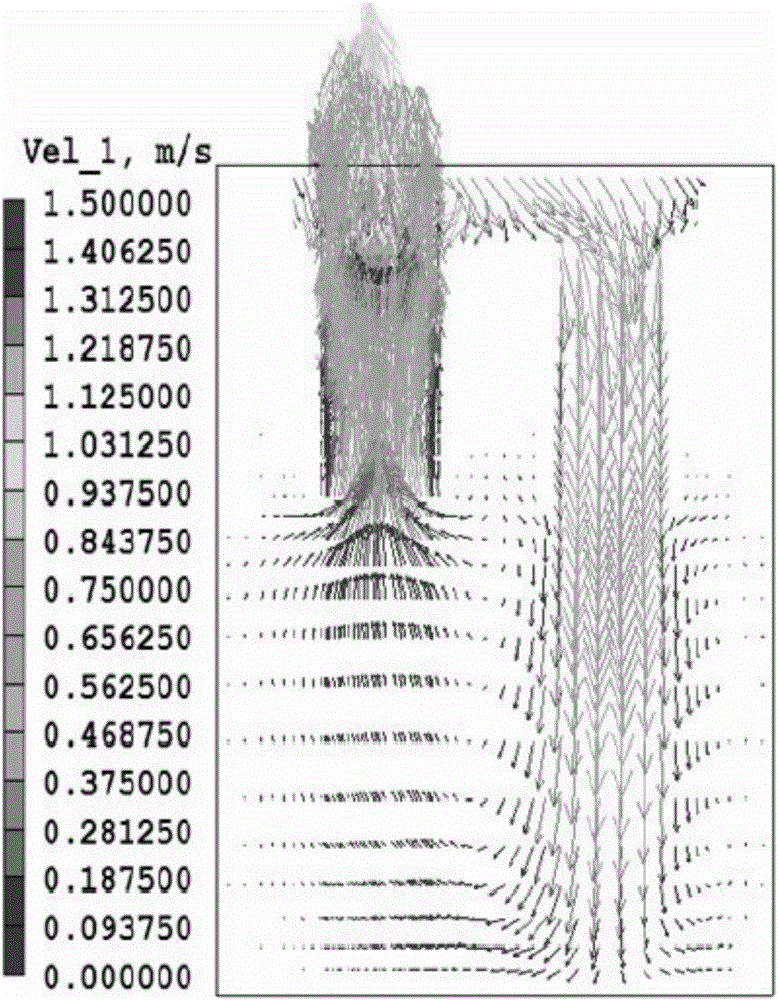
本實用新型屬于冶金行業中用于爐外精煉的真空脫氣裝置,具體涉及一種適用于小鋼包循環處理的RH真空槽導流式整體浸漬管。
背景技術:鋼水真空循環脫氣(RH)技術是一種鋼水二次精煉工藝,是生產高質量品種鋼必備的爐外精煉手段。RH真空精煉設備最初用于鋼水脫氣,其冶金原理是依靠壓差將鋼水提升至真空室,并通過吹氬氣使鋼水循環流動,利用真空環境達到脫氣(N2、H2、O2)的目的,其優點是反應速度快、真空度高、冶金效果好。隨處理容量的增大,循環流量對噴吹氣體流量、噴吹口深度和真空槽真空度的依賴性相應減弱,而浸漬管內徑的作用加大。盡管眾多的研究表明加大浸漬管內徑是提高鋼液循環流量的有效方法,但由于受到鋼水包的限制,特別是中小噸位的RH處理裝置,分體式浸漬管的內徑已經無可增加。申請號201310074271.7的實用新型專利“RH真空精煉裝置的一體式浸漬管”減少了鋼液攪拌的死區,對80t級以上鋼包的循環流量提升了15%~65%,但對于40t~60t級鋼包RH精煉處理仍無能為力。RH的鋼液循環流量直接影響其冶金效能。部分研究結果(如下公式)表明,在一定范圍內,循環流量Q1與驅動氣體吹入深度H的平方根成正比。Q1=0.0038kDM1.5H0.5Q1=K(HQbD2)0.5而氣泡行程過短會產生吹透現象,不利于循環流動。上升管內氣體引入位置降低時會使氣泡行程加大,較大的氣泡行程有利于氣泡的膨脹做功,由于對鋼液的作用時間加長,充分地發揮氣體的驅動作用,進而増大循環流量。所以應通過増加氣泡行程的方法來提高RH真空精煉裝置的循環流量。單嘴真空槽理論上可以對各種規格的鋼包進行真空處理,并且具有最大的氣泡行程。但是無論是申請號201020626765.3等所代表的鋼包底吹攪拌還是申請號201310498891.3、201510409388.5等所代表的浸漬管全周向吹氣攪拌以及申請號201310129031.2、201310323725.X等所代表的鋼包底吹+浸漬管單邊吹氣攪拌,均無法避免真空槽內上升鋼液與下降鋼液互相混沖,降低攪拌效率。申請號201520214416.3、201420179382.4的實用新型專利,單嘴真空槽結構在浸漬管內設置有擋墻,但攪拌氣從鋼包底部吹入仍然無法避免上述現象。并且,單嘴真空槽對鋼包鋼液的攪拌強度理論上比雙浸漬管的真空槽強大越4倍,但實際上帶入真空室的有效處理鋼液量并不比雙浸漬管真空槽大,實際處理效果并不如意,所以沒有被廣大鋼廠所選用。圖1、圖2所示的鋼液流場仿真說明了上述情況。通過對圖1中單嘴浸漬管RH與圖2中雙浸漬管RH流場形態的對比,單嘴浸漬管RH下降流股的流速較低,鋼包內角部區域是鋼液流速較低的地方,難于提高死區流速,并且單嘴浸漬管RH下降流股的擴張幅度明顯大于雙浸漬管RH下降流股的擴張幅度,占據了流場內大部分空間,對鋼包底部的沖擊攪拌作用較小,去雜效果差。理論和實踐均指出,鋼包底吹出的攪拌氣呈基本一致的放散角度上升,其散布面積與氣泡上升的距離的平方成正比。因此對具有較長上升距離和較小橫斷面積的小鋼包,單嘴底吹的效果尤其差。專利號為201220713193.1的實用新型專利,單嘴真空精煉裝置結構在浸漬管內設置有擋墻,并將吹氣口設置于浸漬管底部,有效避免了真空槽內上升鋼液與下降鋼液互相混沖,具有較高的攪拌效率。但是該結構所能產生氣泡行程較短,影響了冶金效果。
技術實現要素:鑒于上述不足,本實用新型的目的在于提供一種適用于小鋼包循環處理的RH真空槽導流式整體浸漬管,該整體式浸漬管能夠在不改變現有RH真空精煉裝置的尺寸的條件下充分利用氣泡的附壁效應,增大循環流量,并延長浸漬管的使用壽命,提高RH真空精煉裝置的效能。為實現上述目的及其他相關目的,本實用新型技術方案如下:一種RH真空槽導流式整體浸漬管,所述浸漬管包括管體以及位于管體內的導流板,所述導流板將管體分隔成上升通道和下降通道,所述導流板向下伸出所述管體下端,所述導流板位于上升通道一面的伸出部上設有多個提升氣噴口,形成上升通道的管體下部的進鋼口一周還另設有多個提升氣噴口。采用上述結構,通過導流板分隔浸漬管管體,使真空槽內上升鋼液與下降鋼液的通道隔離,避免鋼液混沖消弱攪拌效果。在導流板伸出管體下端的部分設置有多個提升氣噴口,提升氣噴口對應于上升通道,在上升通道所對應的管體下部也設置多個提升氣噴口;并且利用鋼液中氣泡的附壁效應降低提升氣噴口位置到浸漬管管體以下,延長鋼液驅動氣上升形成,能夠在保持RH真空精煉裝置的主體尺寸適應小型鋼包的條件下,增大上升鋼液截面積與下降鋼液的截面積,使更多的鋼液進入真空精煉有效區,并使下降鋼液能夠沖擊到鋼包底部,同時浸漬管管體插入鋼液深度較淺,減少浸漬管管體與鋼包壁之間的鋼液攪拌死區,實現優于單嘴浸漬管真空槽的冶金效能。進一步地,所述導流板與管體連接為一體。進一步地,所述浸漬管內部為金屬骨架,金屬骨架外部包裹隔熱耐火襯,所述耐火襯通過錨固釘固定在金屬骨架上,防止隔熱耐火襯脫落。其中導流板和管體的金屬骨架連接為一體,導流板和管體的隔熱耐火襯也連接成整體。進一步地,所述導流板位于上升通道的一面沿上下方向設置有多層提升氣噴口,至少其中一層與管體下部的提升氣噴口相對應,最下層的提升氣噴口位于導流板的伸出部上。導流板上的提升氣噴口至少有一層與管體下部的提升氣噴口相對應,可使上升通道內產生向上的吸力作用,達到快速提升鋼液的目的。本實用新型同時提供一種真空精煉裝置,包括所述的RH真空槽導流式整體浸漬管。進一步地,還包括真空槽、熱彎管和水冷頂槍,所述真空槽下端為管狀敞口結構,真空槽下端與浸漬管的頂部固定。真空槽下端形成無底的敞口結構,使得進入真空槽的鋼水厚一些,參與真空反應的鋼水多。進一步地,所述浸漬管通過金屬骨架與真空槽底部法蘭焊接固定,或所述浸漬管的頂部設有用于與真空槽底部焊接固定的法蘭板。進一步地,所述真空槽上部與熱彎管密封連接,所述熱彎管上安裝有頂槍密封通道,水冷頂槍從密封通道伸入真空槽上部。本實用新型的有益效果是:1)本實用新型的RH真空槽導流式整體浸漬管與現有的浸漬管相比,循環流量在不增加提升氣流量的情況下得到明顯提高;2)由于上升鋼液截面積與下降鋼液的截面積增加,允許提升氣流量能夠有效增加,并進一步加大循環流量;3)本實用新型的RH真空槽導流式整體浸漬管通過加大上升鋼液截面積與下降鋼液的截面積,使得由于工作過程中沾渣導致的鋼液截面積減小造成的維修及最終報廢的周期延長,因此本實用新型的RH真空槽導流式整體浸漬管比普通浸漬管使用壽命長;4)本實用新型的RH真空槽導流式整體浸漬管消除了現有分體式浸漬管的上升管與下降管之間鋼液流動的死區,提高了鋼液混合的效率;5)本實用新型的RH真空槽導流式整體浸漬管通過增大上升鋼液截面積后,上升管出口處鋼液的最大速度降低,有利于減小鋼液飛濺高度,降低真空槽內以及熱彎管內的冷鋼附著量;6)對于同樣的鋼液循環流量要求,本實用新型的RH真空槽導流式整體浸漬管可以比現有的分體式浸漬管減小提升氣流量,并進一步減少真空泵抽氣量;7)本實用新型的RH真空槽導流式整體浸漬管比現有的分體式浸漬管更節能,能夠有效減少RH真空精煉裝置的運行費用。附圖說明圖1為單嘴浸漬管真空槽鋼液流場仿真示意圖;圖2為分體式浸漬管真空槽鋼液流場仿真示意圖;圖3為本實用新型RH真空槽導流式整體浸漬管與真空槽連接結構的剖面示意圖;圖4為本實用新型導流式整體浸漬管真空精煉裝置剖面示意圖。零件標號說明1管體2導流板3鋼骨架4耐火襯5提升氣噴口6法蘭7真空槽8熱彎管9水冷頂槍10提升氣噴口11鋼包12提升氣噴口13上升通道14下降通道具體實施方式以下通過特定的具體實例說明本實用新型的實施方式,本領域技術人員可由本說明書所揭露的內容輕易地了解本實用新型的其他優點與功效。本實用新型還可以通過另外不同的具體實施方式加以實施或應用,本說明書中的各項細節也可以基于不同觀點與應用,在沒有背離本實用新型的精神下進行各種修飾或改變。實施例1如圖3所示,為本實用新型RH真空槽導流式整體浸漬管結構示意圖。本實施例的RH真空精煉裝置的導流式整體浸漬管,包括管體1和導流板2,導流板2位于管體1中間并向下伸出管體1下端面,導流板2前后側與管體1連接,將管體1左右分隔為上升通道13和下降通道14,管體1和導流板2均包括鋼骨架3和耐火襯4,管體1和導流板2的鋼骨架3焊接連接為一整體,耐火襯4包覆在鋼骨架3外為一整體。其中導流板2具有朝向上升通道13的第一面和朝向下降通道14的第二面,該導流板2伸出管體2下端的部分設有多個提升氣噴口5,提升氣噴口5位于導流板2第一面,與導流板2第一面相對的管體1下部設置有多個提升氣噴口10,提升氣噴口5和提升氣噴口10均與上升通道連通。本例中采用鋼材骨架,其他實施例中可采用類似的金屬骨架。進一步地,導流板2上可沿上下方向設置多層提升氣噴口,最下方的一層提升氣噴口位于導流板2的伸出部上。至少其中一層提升氣噴口12與管體1下部的提升氣噴口10相對應,當然,在管體1下部也可以沿上下方向設置多層提升氣噴口。本實用新型同時提供一種真空精煉裝置,包括上述的RH真空槽導流式整體浸漬管,還包括真空槽7,真空槽7下端為管狀敞口結構,浸漬管通過鋼骨架焊接在真空槽7底部外殼法蘭6上,所述真空槽7上部密封連接有熱彎管8,所述熱彎管8上安裝有頂槍密封通道,水冷頂槍9從密封通道伸入真空槽7上部。其他實施例中,浸漬管的頂部可設置用于與真空槽7底部焊接固定的法蘭板,通過法蘭板與真空槽7底部連接。如圖4所示,為本實施例真空精煉裝置剖面示意圖。真空槽7上部密封連接有熱彎管8,熱彎管8的頂部插入水冷頂槍9,真空槽7的導流式整體浸漬管插入鋼包11內的鋼液中,當熱彎管8的出口向外抽氣時,真空槽7內部形成低氣壓,鋼液在大氣壓的作用下通過浸漬管的管口進入真空室,這時各提升氣噴口吹入的氣體混入鋼液導致該部分鋼液的密度降低,從而使之源源不斷上升,并在真空槽7內溢出氣體后重新下降到鋼包11,形成連續的鋼液循環。進入真空槽7的鋼液發生冶金反應,實現脫氣、脫碳、混勻成分與溫度等冶金功能。本實用新型能夠在保持RH真空精煉裝置的主體尺寸不變的條件下,增大上升通道與下降通道的截面積,并取得了如下效果:1)本實施例導流式整體浸漬管與現有的分體式浸漬管相比,循環流量在不增加提升氣流量的情況下得到明顯提高;2)由于上升通道與下降通道的截面積增加,允許提升氣流量能夠有效增加,并進一步加大循環流量;3)由于上升通道與下降通道的截面積增大,使得由于工作過程中沾渣導致的鋼液流通截面減小造成的維修及最終報廢的周期延長,因此本實施例的RH真空精煉裝置的導流式整體浸漬管比分體式浸漬管使用壽命得以延長;4)本實施例的RH真空精煉裝置的導流式整體浸漬管消除了現有分體式浸漬管的上升管1與下降管2之間鋼液流動的死區,提高了鋼液混合的效率;5)本實施例的RH真空精煉裝置的導流式整體浸漬管通過增大鋼液流通截面,上升通道出口處鋼液的最大速度降低,有利于減小鋼液飛濺高度,降低真空槽7內以及熱彎管內的冷鋼附著量;6)對于同樣的鋼液循環流量要求,本實施例的RH真空精煉裝置的導流式整體浸漬管可以比現有的分體式浸漬管減小提升氣流量,并進一步減少真空泵抽氣量;7)本實施例的RH真空精煉裝置的導流式整體浸漬管比現有的分體式浸漬管更節能,能夠有效減少RH真空精煉裝置的運行費用。下面對采用本實施例導流式整體浸漬管的某60tRH真空精煉裝置的具體實施方式作詳細說明。60t鋼包內緣直徑約2060mm。為避免與鋼包耐材相碰比留足測溫取樣液面,導流式整體浸漬管外徑最大為1700mm。浸漬管耐材厚度設為350mm,則上升通道截面積為0.16m2,下降通道截面積0.14m2。該通道截面積已經超過100t分體浸漬管RH所能獲得的最大鋼液流通截面積。因此設計導流式整體浸漬管管體高度1000mm,導流板高度為1300mm,導流板提升氣噴口設上下兩排,相距200mm,位于下方的一排距導流板底部300mm,管體對應處設1排提升氣噴口,距底部200mm。導流式整體浸漬管工作時浸入鋼液300mm~400mm。數值仿真結果表明鋼液循環流量最大可達92t/min。上述實施例僅例示性說明本實用新型的原理及其功效,而非用于限制本實用新型。任何熟悉此技術的人士皆可在不違背本實用新型的精神及范疇下,對上述實施例進行修飾或改變。因此,舉凡所屬技術領域中具有通常知識者在未脫離本實用新型所揭示的精神與技術思想下所完成的一切等效修飾或改變,仍應由本實用新型的權利要求所涵蓋。