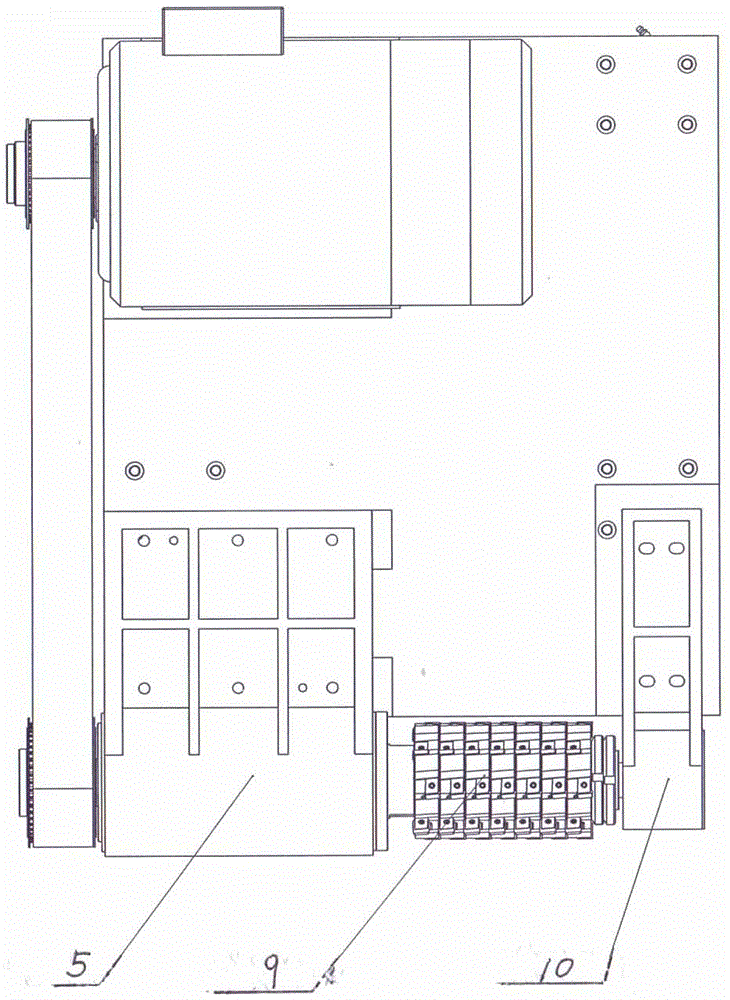
本發明涉及一種葉片根部數控滾銑機床。
背景技術:
:能源和環保是當今世界共同關注的重大課題。風力發電則是當今可再生綠色能源之一,是我國繼火電、水電之后的第三大發電來源,2015年我國風電全年裝機容量達到2900萬千瓦,創造了一個歷史新高,2015年我國風電上網電量已超過全年社會用電的3%。風電與其他可再生能源相比,在度電成本、環境影響、能量儲備、發展空間等方面均有比較強的競爭優勢。我國自2005年以來開始規模化發展風電產業,僅用十年時間反超了歐美等國三十多年的發展歷程。目前在全球十大風電制造企業中,中國軍團已占據了半壁江山,并且在全球市場占有率逐年提升。在可預計的年代,風電將成為具備良好發展前景的新型產業(見下表)序號國家地區風電目前占全社會用電量未來規劃風電占全社會用電比例1美國4%2030年風電占美國電力供應量30%2中國3%2050年風電占中國電力供應量20%3歐盟8%2030年風電占歐盟電力供應量35%但是在風電產業蓬勃發展過程中,風電設備制造中依然存在環境污染的缺陷,尤其是葉片制造過程中普遍存在勞動強度高,工效低,粉塵污染嚴重,占用場地面積大等突出問題。這些問題在國外也未得到很好的解決。所以,目前風力發電設備中的葉片制造部分正在轉移到中國來,如果我們不能處理好這些工藝問題,勢必在我國造成新的污染,對我國的工人造成極大的人身傷害,對環境造成巨大污染。目前,在國內對葉片根部的加工工序中采用兩種方法。其一,人工手持打磨機,將已在模具上成型的葉片端部打磨成形。這種工藝方法,將導致每支葉片至少有五公斤的玻璃鋼粉塵在車間空氣中飛揚,不僅當工序操作工人深受其害,周圍其他工序工人也同樣受污染之害。打磨的工作強度很大,一般情況下,兩個工人用三個小時至五個小時打磨一支葉片,而且加工曲線不規范。其二,國內也出現過一種機械代替人工打磨的方法,但由于未脫離切割片打磨的基本思路,雖然替代了小部分人工打磨工作量,但沒有從根本上解決問題,有的甚至粉塵飛揚的情況更嚴重,而且機械切割方法只能加工直線,仍然有約60%以上的工作量必須由人工打磨來完成。技術實現要素:本發明的目的在于提供一種結構合理,精整后的半葉片結合面符合設計模型要求、現場無粉塵飛揚的葉片根部數控滾銑機床。本發明的技術解決方案是:一種葉片根部數控滾銑機床,其特征是:包括機床底板部件,在機床底板部件上設置左、右兩個工作機構;每個工作機構包括在直線導軌上縱向移動的縱向滑移部件,在縱向滑移部件上設置橫向滑移部件,在橫向滑移部件上設置垂向滑移部件,垂向滑移部件上裝主軸,主軸上裝一把滾銑刀;所述滾銑刀的刀片呈螺旋狀分布于刀體表面;左、右兩個工作機構的二個主軸對稱配置,左、右兩個工作機構的滾銑刀方向對稱,分別為左旋、右旋;在滾銑刀上部配有集塵罩,集塵罩經吸塵管與吸塵器相通。主軸的懸伸端與可調支承掛腳連接;所述可調支承掛腳為可旋轉支承座形式。刀體為整體式或分體式,刀體內圓上有一對稱平鍵槽,刀體通過平鍵槽中的鍵與主軸連接。機床底板部件的中間部分呈可拆卸的剖分形式。縱向滑移部件由伺服電機經滾珠絲杠驅動,在縱向滑移部件上設有一組橫向滾動直線導軌,橫向滑移部件的橫向滑板在橫向滾動直線導軌上移動;橫向滑移部件由伺服電機經橫向滾珠絲杠驅動橫向滑移部件的橫向滑板作橫向進給運動;橫向滑板之前端裝有一組垂向直線導軌,為垂向滑移部件導向,垂向伺服電機以滾珠絲杠驅動垂向滑板作垂向進給運動。滾銑刀具的直徑Ф120-Ф150mm、寬度為140mm-180mm,左、右兩個工作機構的滾銑刀分別呈左、右螺旋狀,升角為25°。在滾銑刀附近設有傳感器,測量刀具至模具邊緣的距離,當距離小于等于1.5mm時,機床電氣系統報警并停機,以保護模具不受損害。機床使用雙通道六軸控制器,并配以PLC控制程序同步加工兩側不同形狀的曲面,在工作中自動控制各項輔助功能;當加工結束時,機床各部件根據PLC程序自動進入安全起吊位置。在機床底板部件兩側設有穩定支撐并固定主機、且保證與用戶模具間有確定關系的輔助支撐系統;所述輔助支撐系統有兩部分,一部分用于在固定模具一側,機床底板部件兩側各有三個安裝座,用于連接至與模具相連的支撐座上,六個支承柱與地面固定,上部與模具定位,只需機器從上往下靠住就可;另一部分則用于可翻轉模具一側,可隨模具翻轉,六個支承柱各分成兩截,一截固定在模具上,可隨模具翻轉,另一截固定于地面;當模具回復原狀時,兩截支撐自動準確貼合,并依靠模具本身的重力,使兩者穩定結合;只須將本機器吊裝到上支撐結合面,即可穩定工作。翻轉模具外側之三個支撐還具有底腳外側翻轉90°的能力,以便在模具翻轉時預先避讓,不與模具干涉。在機床底板部件下方有兩個固定的定位V形塊,用以確定本機與用戶模具間的關系。本發明葉片根端的全部精整加工由機械自動完成,精整后的半葉片結合面完全符合設計模型的要求。在加工過程中,95%以上的粉塵被自動收集處理,現場無粉塵飛揚。機器在模具上的安裝必須快捷、可靠、安全,所有的安裝支架既要剛性好,又能充分滿足大型模具工作的特點。附圖說明下面結合附圖和實施例對本發明作進一步說明。圖1是本發明一個實施例的結構示意圖。圖2是機床的主軸系統結構示意圖。圖3是滾銑刀具的結構示意圖。具體實施方式一種葉片根部數控滾銑機床,包括機床底板部件1,在機床底板部件上設置左、右兩個工作機構;每個工作機構包括在直線導軌上縱向移動的縱向滑移部件2,在縱向滑移部件上設置橫向滑移部件3,在橫向滑移部件上設置垂向滑移部件4,垂向滑移部件上裝主軸5,主軸上裝一把滾銑刀9;所述滾銑刀的刀片呈螺旋狀分布于刀體表面;左、右兩個工作機構的二個主軸對稱配置,左、右兩個工作機構的滾銑刀方向對稱,分別為左旋、右旋;在滾銑刀上部配有集塵罩,集塵罩經吸塵管與吸塵器6相通。縱向移動的縱向滑移部件2、橫向滑移部件3、垂向滑移部件4組成了本機床三個切削進給運動,可令刀具作空間曲線、曲面運動,并驅使兩個主軸頭同時作空間切削運動。圖中還有控制系統7、工件11、磨具12。主軸的懸伸端與可調支承掛腳10連接;所述可調支承掛腳為可旋轉支承座形式,有效提高了刀具系統的切削剛性。刀具外形尺寸在Ф90-Ф150間根據需要設計。機夾可重磨式硬質合金刀片成螺旋狀分布于刀體表面。左右兩把刀分別為左旋與右旋。刀體內圓上有一對稱平鍵槽,刀體通過平鍵槽中的鍵(及另外的螺母)與主軸連接。刀體可制成整體式,也可成分體式。分體式的優點在于制作工藝簡單,整體開螺旋槽和內孔對稱鍵槽,然后精整刀片裝夾面。機床底板部件的中間部分呈可拆卸的剖分形式,并用機械方法強力連接。縱向滑移部件由伺服電機經滾珠絲杠驅動,在縱向滑移部件上設有一組橫向滾動直線導軌,橫向滑移部件的橫向滑板在橫向滾動直線導軌上移動;橫向滑移部件由伺服電機經橫向滾珠絲杠驅動橫向滑移部件的橫向滑板作橫向進給運動;橫向滑板之前端裝有一組垂向直線導軌,為垂向滑移部件導向,垂向伺服電機以滾珠絲杠驅動垂向滑板作垂向進給運動。滾銑刀具的直徑Ф120-Ф150mm、寬度為140mm-180mm,左、右兩個工作機構的滾銑刀分別呈左、右螺旋狀,升角約為25°。滾銑刀具的刀片13通過壓刀塊14裝在刀體15上,并通過壓釘16固定。在滾銑刀附近設有傳感器,測量刀具至模具邊緣的距離,當距離小于等于1.5mm時,機床電氣系統報警并停機,以保護模具不受損害。機床使用雙通道六軸控制器,并配以PLC控制程序同步加工兩側不同形狀的曲面,在工作中自動控制各項輔助功能;當加工結束時,機床各部件根據PLC程序自動進入安全起吊位置。在機床底板部件兩側設有穩定支撐并固定主機、且保證與用戶模具間有確定關系的輔助支撐系統;所述輔助支撐系統有兩部分,一部分用于在固定模具一側,機床底板部件兩側各有三個安裝座8,用于連接至與模具相連的支撐座上,六個支承柱與地面固定,上部與模具定位,只需機器從上往下靠住就可;另一部分則用于可翻轉模具一側,可隨模具翻轉,六個支承柱各分成兩截,一截固定在模具上,可隨模具翻轉,另一截固定于地面;當模具回復原狀時,兩截支撐自動準確貼合,并依靠模具本身的重力,使兩者穩定結合;只須將本機器吊裝到上支撐結合面,即可穩定工作。翻轉模具外側之三個支撐還具有底腳外側翻轉90°的能力,以便在模具翻轉時預先避讓,不與模具干涉。在機床底板部件下方有兩個固定的定位V形塊,用以確定本機與用戶模具間的關系。當前第1頁1 2 3