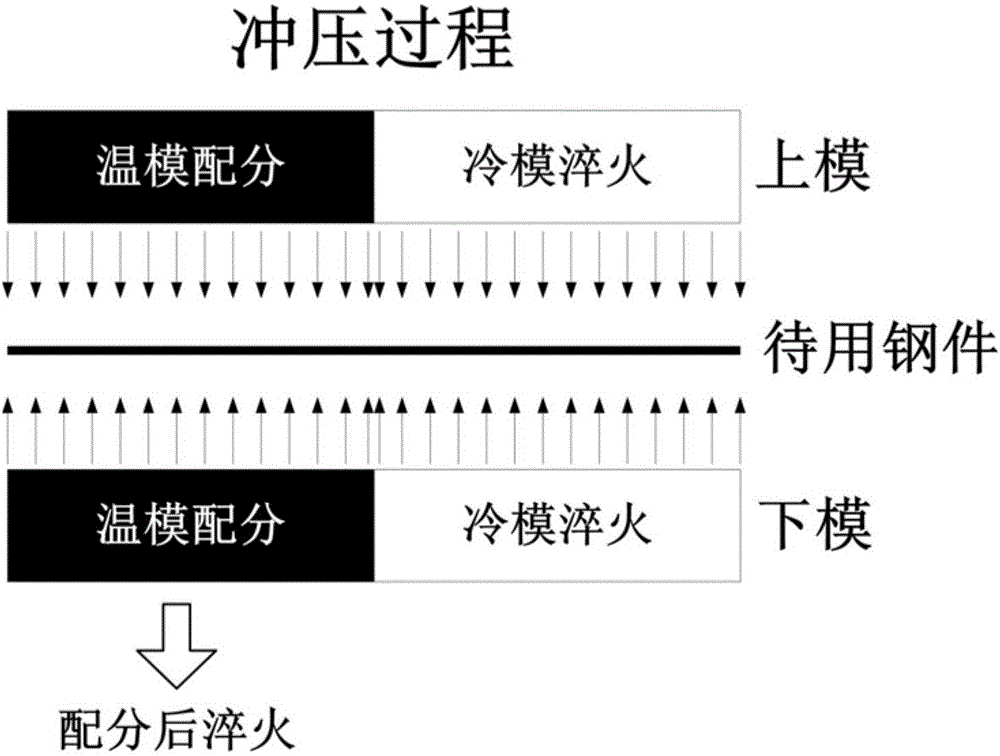
本發(fā)明屬于Q&P鋼件成形
技術(shù)領(lǐng)域:
,具體涉及一種通過二步法Q&P鋼將配分工藝和溫熱成形工藝同步進行的控制技術(shù),從而實現(xiàn)不同區(qū)域力學性能梯度分布的高強度Q&P鋼件制備方法。
背景技術(shù):
:為了實現(xiàn)汽車輕量化和安全性的技術(shù)目標,在車用鋼板方面,采用超高強度鋼板已成為汽車制造商、鋼鐵企業(yè)和各大科研院所共同努力的方向,相繼開發(fā)出第一代、第二代及第三代汽車鋼。Q&P鋼作為先進的第三代汽車鋼的一種,是2003年,研究者們在無碳化物貝氏體鋼的研究基礎(chǔ)上提出馬氏體鋼淬火+(碳)配分的熱處理工藝制得的,即將鋼由奧氏體化溫度淬火到Ms~Mf之間的某一溫度,再在此溫度或高于此溫度保溫,使碳從馬氏體向未轉(zhuǎn)變的奧氏體中擴散并使之穩(wěn)定化,最后二次淬火到室溫,得到由馬氏體和殘余奧氏體組成的,具有高強度和較好塑韌性的組織。那么,在該熱處理工藝中,當一次淬火溫度等于配分溫度時,稱為一步法Q&P工藝;當配分溫度高于一次淬火溫度時,稱為兩步法Q&P工藝。當前,關(guān)于Q&P鋼的制造方法已經(jīng)研究得很多,比如徐方毅等人《TRIP800鋼和熱成形鋼的Q&P工藝研究》指出將22MnB5鋼板材進行Q&P工藝處理,提出了一步和二步法的Q&P工藝,并未涉及熱成形,其中,二步法Q&P工藝中組織發(fā)生了明顯的回火轉(zhuǎn)變;常穎等人提出對于22MnB5鋼來說,沖壓成形時的載荷作用對22MnB5鋼馬氏體起始溫度Ms點的影響很敏感,當板材被加熱到高于Ms點溫度以上成形時,由于存在載荷作用,將會誘發(fā)奧氏體向馬氏體相變而提高Ms點,導(dǎo)致此條件下成形很難精確控制其馬氏體起始溫度和終止溫度,從而影響目標性能的獲得,其最佳成形溫度在700℃左右;馬寧等人提出根據(jù)CCT曲線,22MnB5需要不低于30℃/s的冷卻速率才能保證充分的馬氏體相變,獲得殘余奧氏體含量不超過5%的馬氏體組織結(jié)構(gòu),因此,就硼鋼來說,二步法配分過程中進行成形很難避免其他雜相的形成;對于22MnB5鋼的Q&P工藝與熱成形工藝結(jié)合時,大多控制在Ms點以下溫度,比如中國專利公開號為:CN103394573A《一種基于Q&P一步法的熱沖壓成形工藝》中所描述的技術(shù),是將板料在一步法Ms溫度以下進行熱沖壓,因為沖壓溫度較低,使得板料成形流動性差,摩擦系數(shù)大,造成模具損耗嚴重,也并未實現(xiàn)性能梯度分布的特征;段亞楠等人在《一種高強塑積熱沖壓成形用鋼的研究與開發(fā)》中所描述的技術(shù),是將特定成分的板料通過調(diào)節(jié)其各相變點等溫度值,經(jīng)過奧氏體化的板料在降溫過程中成形,然后繼續(xù)降溫到Ms點以下發(fā)生動態(tài)碳配分,該技術(shù)中經(jīng)各種工藝條件下的鋼板性能差距很小,接近一致;王存宇等人提出Q&P工藝的奧氏體化保溫后,降溫過程中對鋼板進行熱成形,然后再在加熱爐中進行后續(xù)的配分處理,此加載除了對Ms點,繼而對配分過程的溫度控制有影響之外,因配分過程中沒有模具的約束,使得成形件得不到精確的形狀控制,同時鋼件也無法實現(xiàn)性能梯度分布。在汽車零部件的使用過程中,為了簡化焊裝等連接工藝,以及提高零部件的服役性能、整體性能等,研究者們提出了研制性能梯度分布的鋼件結(jié)構(gòu);中國專利公開號為:CN105463307A《一種具有梯度組織的Q&P鋼及其制備方法》中所描述的技術(shù),是通過增加滲碳工藝來實現(xiàn)組織梯度的特征,但工藝時間過長,不適于大規(guī)模批量生產(chǎn);高強鋼梯度性能的實現(xiàn)當前大多集中于熱成形的淬火工藝,或通過差厚板工藝,比如中國專利公開號為:CN104668326A《一種高強度鋼材零部件性能梯度化分布的熱沖壓方法》中所描述的技術(shù),是將熱沖壓鋼板奧氏體化加熱后迅速冷卻,再加熱至奧氏體化區(qū)域,進行沖壓,該技術(shù)存在二次加熱奧氏體化的情況,不利于生產(chǎn)效率的提高,而且二次奧氏體化不利于晶粒細化的組織獲得,也不符合Q&P的工藝特點;或通過在淬火過程中利用模具的選擇性冷卻工藝,將完全奧氏體化的組織結(jié)構(gòu)分解成馬氏體、珠光體、貝氏體等不同組織,來實現(xiàn)性能上的差別,屬于全模冷工藝。綜上,關(guān)于二步法Q&P工藝過程中如何通過設(shè)計新工藝而實現(xiàn)性能梯度,經(jīng)查新,尚未出現(xiàn)相關(guān)報道。技術(shù)實現(xiàn)要素:根據(jù)上述提出的技術(shù)問題,而提供一種性能梯度分布的高強度Q&P鋼件制備方法。本發(fā)明主要利用將加熱至奧氏體化溫度的板料保溫后降溫到Ms~Mf溫度之間并保溫,然后再將板料升溫到高于Ms點的配分溫度,利用具有恒溫區(qū)和冷卻區(qū)的模具對板料進行沖壓成形后,冷卻區(qū)直接淬火;恒溫區(qū)配分后脫模,再通過冷卻介質(zhì)對待用鋼件進行淬火,淬火過程中,不穩(wěn)定的奧氏體發(fā)生相變,穩(wěn)定的奧氏體殘留在鋼件中,最終獲得力學性能梯度分布的高強度Q&P鋼件。本發(fā)明采用的技術(shù)手段如下:一種性能梯度分布的高強度Q&P鋼件制備方法,其特征在于,包括如下步驟:S1、將低碳合金鋼制成待用鋼件,該低碳合金鋼的化學成分重量百分比為:C:0.1~0.51%;Si:0~2.0%;Mn:0~6.0%;Cr:0~1.1%;Ni:0~3.0%;V:0~0.2%;Mo:0~0.7%;Nb:0~0.05%;P≤0.015%;S≤0.005%;N≤0.006%;O≤30ppm;余量為Fe以及不可避免的雜質(zhì);S2、將待用鋼件加熱至完全奧氏體化,保溫3~5分鐘,將完全奧氏體化的待用鋼件以預(yù)設(shè)的冷卻速率降溫至Ms-Mf溫度之間,保溫0-30s;S3、再次加熱待用鋼件至Ms點以上的配分溫度,利用具有恒溫區(qū)和冷卻區(qū)的模具對待用鋼件完成沖壓成形,其中,冷卻區(qū)在沖壓過程中對待用鋼件直接淬火,恒溫區(qū)對待用鋼件恒溫沖壓并配分,然后脫模,通過冷卻介質(zhì)對待用鋼件淬火至室溫,最終得到力學性能梯度分布的高強度Q&P鋼件。進一步地,所述步驟S2中的預(yù)設(shè)冷卻速率不低于5℃/s。進一步地,所述步驟S2中的降溫至Ms-Mf溫度之間的一次淬火溫度及保溫時間的設(shè)置以控制一次馬氏體含量不超過30%為界。進一步地,所述步驟S3中,冷卻區(qū)在沖壓過程中對待用鋼件進行淬火,獲得馬氏體微觀結(jié)構(gòu);恒溫區(qū)在沖壓過程中對待用鋼件進行配分處理,保溫、保壓5~300s,再脫模,通過冷卻介質(zhì)對鋼件淬火到室溫,冷卻過程中有一部分奧氏體發(fā)生相變,最終獲得奧氏體含量不少于10%的亞穩(wěn)奧氏體和馬氏體的復(fù)合微觀結(jié)構(gòu)。進一步地,所述步驟S3中模具的冷卻區(qū)為具有水道或其他冷卻介質(zhì)的冷卻模具;所述模具的恒溫區(qū)可通過加熱元件或其他熱源維持恒溫的模具;所述模具的恒溫區(qū)脫模后可通過壓縮氣體或空冷等方式進行冷卻。較現(xiàn)有技術(shù)相比,本發(fā)明具有以下優(yōu)點:1、Q&P工藝中加熱方式不需要開發(fā)特殊的加熱爐裝置,工業(yè)化容易實現(xiàn)。2、本發(fā)明雖然增加了分區(qū)模具的成本,但工業(yè)化生產(chǎn)效率高,不影響目前的生產(chǎn)流程。3、本發(fā)明在高于Ms溫度的配分過程沖壓,利于鋼板的流動性,減小摩擦系數(shù),延長模具使用壽命,提高成形性。4、本發(fā)明加工的零部件,實現(xiàn)了高強度Q&P鋼件不同區(qū)域的力學性能梯度化,使得汽車在保證安全性的前提下提高局部區(qū)域的吸能效果,從而提高成形件整體的碰撞安全性。附圖說明為了更清楚地說明本發(fā)明實施例或現(xiàn)有技術(shù)中的技術(shù)方案,下面將對實施例或現(xiàn)有技術(shù)描述中所需要使用的附圖作一簡單地介紹,顯而易見地,下面描述中的附圖是本發(fā)明的一些實施例,對于本領(lǐng)域普通技術(shù)人員來講,在不付出創(chuàng)造性勞動性的前提下,還可以根據(jù)這些附圖獲得其他的附圖。圖1為本發(fā)明的制備方法流程示意圖。圖2為本發(fā)明的沖壓過程示意圖。圖3為本發(fā)明的一種具體實施方式,即具有性能梯度分布的Q&P工藝中高強鋼U型件示意圖及各區(qū)域?qū)?yīng)的力學性能,其中,A是經(jīng)恒溫沖壓/配分再淬火的部位;B是直接沖壓淬火的部位。具體實施方式為使本發(fā)明實施例的目的、技術(shù)方案和優(yōu)點更加清楚,下面將結(jié)合本發(fā)明實施例中的附圖,對本發(fā)明實施例中的技術(shù)方案進行清楚、完整地描述,顯然,所描述的實施例是本發(fā)明一部分實施例,而不是全部的實施例。基于本發(fā)明中的實施例,本領(lǐng)域普通技術(shù)人員在沒有做出創(chuàng)造性勞動前提下所獲得的所有其他實施例,都屬于本發(fā)明保護的范圍。一種性能梯度分布的高強度Q&P鋼件制備方法,包括如下步驟(如圖1所示):S1、將低碳合金鋼制成待用鋼件,該低碳合金鋼的化學成分重量百分比為:C:0.1~0.51%;Si:0~2.0%;Mn:0~6.0%;Cr:0~1.1%;Ni:0~3.0%;V:0~0.2%;Mo:0~0.7%;Nb:0~0.05%;P≤0.015%;S≤0.005%;N≤0.006%;O≤30ppm;余量為Fe以及不可避免的雜質(zhì);S2、將待用鋼件加熱至完全奧氏體化,保溫3~5分鐘,將完全奧氏體化的待用鋼件以不低于5℃/s的冷卻速率降溫至Ms-Mf溫度之間,保溫0-30s,其溫度選取和保溫時間以控制一次馬氏體含量不超過30%為佳;S3、再次加熱待用鋼件至Ms點以上的配分溫度,利用具有恒溫區(qū)和冷卻區(qū)的模具對待用鋼件完成沖壓成形,如圖2所示其中,冷卻區(qū)在沖壓過程中對待用鋼件直接淬火;恒溫區(qū)對待用鋼件恒溫沖壓并配分,然后脫模,通過冷卻介質(zhì)對待用鋼件淬火至室溫,最終得到力學性能梯度分布的高強度Q&P鋼件。所述模具的冷卻區(qū)為具有水道或其他冷卻介質(zhì)的冷卻模具;所述模具的恒溫區(qū)可通過加熱元件或其他熱源維持恒溫的模具;所述模具的恒溫區(qū)脫模后可通過壓縮氣體或空冷等方式進行冷卻。實施例選取適于二步法Q&P工藝的合金鋼,待用鋼件其成分為:C為0.2%;Si為1.0%;Mn為5.0%;P和S控制在0.005%以下,其余是Fe。將待用鋼件加熱到850℃,保溫5分鐘,至待用鋼件獲得完全、均勻的奧氏體化組織。然后以10℃/s的冷卻速率降溫到Ms~Mf溫度之間,選取290℃,保溫2s,此時,形成的馬氏體含量不超過30%;然后待用鋼件升溫到500℃。利用具有分區(qū)的模具對板料進行沖壓成鋼件,一部分待用鋼件在冷卻模具中沖壓成形并淬火(B區(qū));一部分待用鋼件在500℃恒溫區(qū)完成沖壓并配分過程,保溫、保壓30s后脫模,利用空冷方式淬火至室溫(A區(qū))。如圖3所示,解剖鋼件,對比不同區(qū)域鋼件的力學性能如表1:表1U型件具有性能梯度分布的力學性能力學性能/分區(qū)A區(qū)B區(qū)抗拉強度/MPa8651430延伸率/%178從表中可以看出,A區(qū)(通過恒溫沖壓/配分再淬火)和B區(qū)(沖壓后直接淬火)獲得了明顯的性能梯度,包括抗拉強度和延伸率都具有明顯差異。最后應(yīng)說明的是:以上各實施例僅用以說明本發(fā)明的技術(shù)方案,而非對其限制;盡管參照前述各實施例對本發(fā)明進行了詳細的說明,本領(lǐng)域的普通技術(shù)人員應(yīng)當理解:其依然可以對前述各實施例所記載的技術(shù)方案進行修改,或者對其中部分或者全部技術(shù)特征進行等同替換;而這些修改或者替換,并不使相應(yīng)技術(shù)方案的本質(zhì)脫離本發(fā)明各實施例技術(shù)方案的范圍。當前第1頁1 2 3