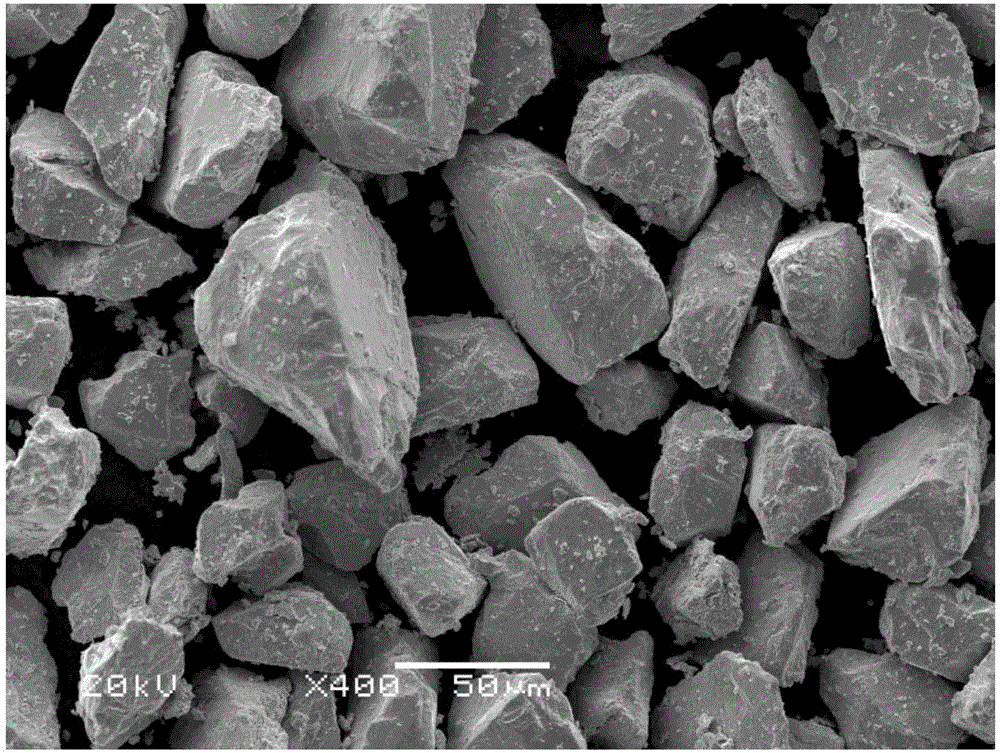
本發明涉及金屬
技術領域:
,尤其涉及一種金屬粉末及其制備方法和應用。
背景技術:
:激光增材制造,也被稱為激光3D打印技術,是一種通過層層堆積的方式將數字化模型直接制造出實體零件的一種技術。激光增材制造技術的基本思想是采用了數學中的積分思想,即任何三維實體均可由無窮多個二維平面疊加而成。首先對要加工的實體零件進行CAD建模,并切片分層二維平面,激光熔化同步送進的粉末或選擇性燒結預置的粉末形成二維熔覆層,并逐步順序堆積成三維實體零件。激光增材制造與傳統的制造技術相比,具有如下特點1)節約材料,無需或需少量后續加工,實現“凈成形”或“近凈成形”;2)無需大型鍛壓設備和模具、專用夾具;3)可以制造形狀復雜、難加工材料;4)個性化設計,柔性化生產;5)縮短了從設計到制造的時間,降低制造成本和風險;6)可以用于零件的修復。該技術是一種全新的短周期、低成本的制造技術,在航空、航天和生物醫學等領域具有重要的應用前景。目前隨著送粉式激光增材制造在鈦合金應用上越來越成熟,各大增才制造公司開始關注送粉式激光增材制造在高溫難熔金屬領域的應用研究。送粉式激光增材制造技術對金屬粉末的要求是粒度均勻分散,最好呈球形。因而近年來對于3D打印用球形粉末的制備方法研究越來越多。申請號CN201310470047.X和CN201410693232.X的中國專利均公開了一種制備3D打印用金屬粉末的方法。這些方法的共同特點是將金屬或合金粉末先熔融,而后將熔融液采用霧化法得到所需的球形或類球形金屬粉末。其缺點是只能制備熔點在2000℃以下的金屬或合金,無法制備熔點在2000℃以上的金屬,例如鉭、鈮、鎢等。申請號CN201510044848.9的中國專利公開了一種制備3D打印用超細球形金屬粉末的方法及裝置。其特點是將熔融的金屬液滴滴落到高速旋轉的圓盤上,通過離心力使金屬液滴粉碎,從而得到超細球形金屬粉末。因而此發明也需要將金屬或合金粉末先熔融,因此無法制備高熔點的金屬,例如鉭、鈮、鎢等。等離子粉體處理技術設備投資大、技術要求高,尤其對于鉭、鈮、鎢等高熔點金屬,工藝更復雜、粉末加工成本更高,難以大規模生產。現有技術提供的方法均需要將金屬或合金粉末先熔融,因此無法制備高熔點的金屬,例如鉭、鈮、鎢等。因而對于高溫難熔金屬,如鉭、鈮、鎢、鉬等得到球形粉末,難度很大,成本很高,無法得到廣泛應用。因此,現有技術急需一種能夠獲得高溫難容金屬粉末用于3D打印的技術。技術實現要素:有鑒于此,本發明的目的在于提供一種金屬粉末及其制備方法和應用,本發明提供的方法制備得到的金屬粉末適于作為3D打印粉末應用。本發明提供了一種金屬粉末的的制備方法,包括以下步驟:1)將金屬原料氫化破碎后進行分級處理,得到金屬顆粒;2)將金屬顆粒進行脫氫處理,得到脫氫后金屬顆粒;3)將所述脫氫后金屬顆粒進行球磨處理,得到金屬粉體;4)將所述金屬粉體進行脫氧處理,得到金屬粉末。優選的,所述金屬原料的成分為鉭或鉭合金、鈮或鈮合金。優選的,所述步驟3)進行球磨處理后,還包括:將球磨處理后的產物進行酸洗,得到金屬粉體。優選的,所述步驟2)中脫氫處理的溫度為800~950℃。優選的,所述步驟2)中脫氫后金屬顆粒的氫含量≤300ppm。優選的,所述步驟3)中球磨處理的方法為振磨、攪拌球磨或滾動球磨。優選的,所述步驟4)中脫氧處理的方法為:將所述金屬粉體在低溫下脫氧然后在高溫下保溫;所述低溫為650~850℃;所述高溫為1050~1250℃。本發明提供了一種上述技術方案所述的方法制備得到的金屬粉末。優選的,所述金屬粉末的平均粒徑D10>25μm,D90<150μm,氧含量≤500ppm。本發明提供了一種金屬制品,以上述技術方案所述的金屬粉末為原料進行3D打印制備得到。與現有技術相比,本發明采用氫化破碎的方法得到金屬粉末,尤其是在脫氫處理后采用球磨的方法制備金屬粉末,這種方法制備得到的金屬粉末粒度分布較窄,顆粒棱角平滑,具有良好的鋪展性和流動性,作為3D打印原料能夠避免制備得到的產品出現空心、氣泡的缺陷,提高產品的質量。附圖說明為了更清楚地說明本發明實施例或現有技術中的技術方案,下面將對實施例或現有技術描述中所需要使用的附圖作簡單地介紹,顯而易見地,下面描述中的附圖僅僅是本發明的實施例,對于本領域普通技術人員來講,在不付出創造性勞動的前提下,還可以根據提供的附圖獲得其他的附圖。圖1為本發明實施例1制備得到的鉭粉末的粒度分布圖;圖2為本發明實施例1制備得到的鉭粉末的400倍的SEM照片。具體實施方式下面將結合本發明實施例中的附圖,對本發明實施例中的技術方案進行清楚、完整地描述,顯然,所描述的實施例僅僅是本發明一部分實施例,而不是全部的實施例。基于本發明中的實施例,本領域普通技術人員在沒有做出創造性勞動前提下所獲得的所有其他實施例,都屬于本發明保護的范圍。本發明提供了一種金屬粉末的的制備方法,包括以下步驟:1)將金屬原料氫化破碎后進行分級處理,得到金屬顆粒;2)將金屬顆粒進行脫氫處理,得到脫氫后金屬顆粒;3)將所述脫氫后金屬顆粒進行球磨處理,得到金屬粉體;4)將所述金屬粉體進行脫氧處理,得到金屬粉末。本發明對所述步驟1)中的金屬原料沒有特殊的限制,可以為金屬錠或金屬條。在本發明中,所述金屬錠或金屬條可以是以各種工藝生產的金屬粉為原料,通過高溫燒結除雜或電子轟擊除雜得到的金屬錠或金屬條,也可由市場購買獲得。本發明對所述金屬原料的形狀沒有特殊的限制,如可以為餅狀、圓柱狀、棒狀等形狀的金屬錠。在本發明中,所述金屬原料的純度優選達到99.9%以上。在本發明中,所述金屬原料優選為鉭或鉭合金、鈮或鈮合金,更優選為鉭或鉭合金。本發明對所述步驟1)中的氫化破碎的具體方法沒有特殊的限制,采用本領域技術人員熟知的氫化破碎的方法將上述金屬原料進行破碎即可。本發明對所述分級處理的方法沒有特殊的限制,可以采用本領域技術人員熟知的氣流分級、水力分級或過篩分級均可,優選采用過篩分級的方法。本發明通過分級處理能夠使得到的金屬顆粒粒度集中。在本發明中,所述金屬顆粒的粒度優選為80~200目、100~325目或200~500目。在本發明中,可通過篩目進行分級處理,將氫化破碎后的金屬原料過80目篩,而后再將80目篩下面的金屬顆粒過200目篩,取200目篩上面的金屬顆粒即可得到80~200目的金屬顆粒。與現有技術相比,采用氣旋式破碎分級機將破碎與分級同時進行制備金屬粉末,很難得到球形或近球形的金屬粉末,而且工藝過程中沒有脫氫后球磨的步驟,最終得到的金屬粉顆粒棱角尖銳,從而造成顆粒間相互搭橋,不利于3D打印使用。而本發明先將金屬原料進行氫化破碎然后再進行分級處理并在脫氫后進行球磨能夠得到圓整度相對較高、棱角平滑的金屬粉末。本發明對的步驟2)中脫氫處理的具體方法沒有特殊的限制,采用本領域技術人員熟知的脫氫處理的技術方案將金屬顆粒進行加熱即可。在本發明中,所述脫氫處理優選在惰性氣體的保護下進行。在本發明中,所述脫氫處理的溫度優選為800~950℃,更優選為820~880℃,最優選為820℃、850℃或880℃。在本發明中,所述脫氫處理的時間優選為3~5小時,更優選為3.5~4.5小時,最優選為4小時。在本發明中,所述脫氫處理能夠使金屬顆粒中的氫含量盡可能的低,同時又不能使超細金屬顆粒粘連在大顆粒的表面,從而保證金屬顆粒的分散性。在本發明中,所述金屬顆粒越細則應采用越低的脫氫溫度。在本發明中,優選將加熱保溫后的金屬顆粒進行降溫、出爐、過篩,得到脫氫后的金屬顆粒。在本發明中,所述脫氫后的金屬顆粒的氫含量優選≤300ppm。在本發明中,如果脫氫后的金屬顆粒的氫含量過高,雖然也能實現本發明的目的,但由于脫氫后的金屬顆粒還有一定的氫脆性,因而在球磨破碎過程中易產生更多細粉,同時不利于對金屬顆粒邊緣的鈍化,因而脫氫后的金屬顆粒的氫含量越低越好。在本發明中,所述步驟3)中球磨處理的方法優選為振磨、攪拌球磨或滾動球磨,更優選為攪拌球磨,最優選為濕式攪拌球磨。在本發明中,所述濕式攪拌球磨的球磨介質沒有特別的限制,優選為不銹鋼球。在本發明中,對于不銹鋼球大小的選擇,隨著金屬顆粒平均粒徑D50的變小,不銹鋼球的直徑也相應的變小,直徑小的研磨介質在研磨腔中的充填量大,增加了研磨介質的沖擊作用和摩擦作用,同時增大了研磨介質的接觸面積,研磨面積增大,有助于對金屬顆粒棱角的打磨。在本發明中,所述不銹鋼球的直徑優選為1~5mm,更優選2~4mm,能實現較好的研磨效果。在本發明中,所述濕式攪拌球磨的分散介質優選為水或有機溶劑。在本發明中,所述有機溶劑優選為酒精。在本發明中,在球磨過程中為防止金屬顆粒團聚,優選在分散介質中添加表面活性劑作為助磨劑,表面活性劑可以附著于金屬顆粒表面,形成一層保護層,使金屬顆粒在球磨的同時實現表面鈍化,可以有效抑制金屬顆粒團聚。本發明對所述助磨劑的種類沒有特殊的限制,優選為異丙醇。在本發明中,所述助磨劑的用量優選為脫氫后金屬顆粒質量的1~4%,更優選為2~3%。在本發明中,所述濕式攪拌球磨的攪拌速度優選為70~90轉/分,更優選為75~85轉/分,最優選為80轉/分,速度過慢,對金屬顆粒棱角起不到打磨的作用,速度過快,由于金屬顆粒硬度較高,會造成不銹鋼球的嚴重磨損,使大量的金屬雜質混入物料中,導致得到金屬粉末中雜質含量偏高。在本發明中,所述濕式攪拌球磨的時間優選為1~4小時,即可實現對脫氫后金屬顆粒棱角的打磨,更優選為1.5~3.5小時,最優選為2~3小時。在本發明中,球磨時間過短,對金屬顆粒棱角起不到打磨的作用,時間過長,由于金屬顆粒硬度較高,采用不銹鋼球研磨會造成不銹鋼球的嚴重磨損,使大量的金屬雜質混入物料中,導致得到金屬粉末中雜質含量偏高。與現有技術相比,在氫化破碎或者脫氫之前進行球磨制備金屬粉末,由于金屬粉末的氫脆性依然存在,因而只能將金屬粉末再次磨細,而起不到對金屬粉末的打磨和整形作用,從而一方面造成粉末利用率的下降,成本增加,另一方面容易在3D打印的過程中造成顆粒間搭橋,導致產品內部有空心、氣泡等現象產生,由此造成產品性能下降,不能滿足3D打印用粉的要求。本發明在脫氫之后進行球磨處理,通過球磨使氫化破碎后金屬顆粒棱角尖銳突起的部分盡量磨平,但是由于金屬原料脫氫后韌性加強而脆性減弱,從而不易將金屬顆粒再次磨碎,保證了制備得到的金屬粉末的粒度;同時經過球磨處理后能夠使制備得到的金屬粉末棱角平滑,在3D打印過程中不會造成顆粒間的相互搭橋,利于3D打印使用。在本發明中,所述球磨處理后優選將得到的產物進行酸洗去除其中的金屬雜質,得到金屬粉體。在本發明中,所述酸洗的酸優選為HNO3和HF的混合酸。在本發明中,所述酸洗后優選進行水力分級、烘干和過篩,得到金屬粉體,所述水力分級用于去除球磨時產生的少量超細粉。在本發明中,所述步驟4)中脫氧處理的方法優選為:將所述金屬粉體在低溫下脫氧然后在高溫保溫。本發明采用低溫脫氧達到脫氧目的的同時保證金屬粉體不燒結不長大;在高溫下保溫是在將鎂蒸汽排完后,在保證金屬粉體不發生團聚的前提下,提高溫度保溫,盡可能除去脫氧后殘余的金屬鎂、球磨酸洗帶入的H、F等雜質。在本發明中,所述低溫的溫度優選為650~850℃,更優選為700~800℃,最優選為750℃。本發明對所述低溫下脫氧的方法沒有特殊的限制,采用本領域技術人員熟知的低溫脫氧的技術方案即可。在本發明中,所述低溫下脫氧的方法優選為:將金屬粉體和鎂粉混合后加熱保溫,然后在真空條件下保溫。在本發明中,所述加熱保溫優選在惰性氣體的保護下進行。在本發明中,所述加熱保溫的溫度優選為650~850℃,更優選為700~800℃,最優選為750℃。在本發明中,所述加熱保溫的時間優選為2~4小時,更優選為2.5~3.5小時,最優選為3小時。在本發明中,所述真空條件下保溫的時間優選為2~4小時,更優選為2.5~3.5小時,最優選為3小時。在本發明中,所述鎂粉的用量為金屬粉體質量的0.2~2%,更優選為0.5~1.5%,更優選為0.8~1.2%,最優選為1%。在本發明中,所述高溫的溫度優選為1050~1250℃,更優選為1100~1200℃,最優選為1150℃。在本發明中,所述高溫下保溫的時間優選為1~3小時,更優選為1.5~2.5小時,最優選為2小時。在本發明中,所述高溫下保溫優選在真空條件下進行。本發明通過在高溫下保溫盡可能除去脫氧后殘余的金屬鎂、球磨酸洗帶入的H、F等雜質。在本發明中,所述真空條件優選為10~1Pa。本發明采用上述低溫脫氧和高溫保溫的方式,既避免了傳統工藝在液態和汽態鎂存在下,溫度過高脫氧而帶來的金屬粉體燒結粘連,又進一步除去脫氧后殘余的金屬鎂、以及球磨酸洗帶入的H、F等雜質,使氣體雜質含量得到了很好的控制。本發明提供的脫氧方法在保證產品脫氧效果的同時,縮短了工藝周期。本發明優選將脫氧處理后得到的產物進行降溫、鈍化、出爐、過篩,得到金屬粉末。本發明提供了一種上述技術方案所述的方法制備得到的金屬粉末。對于高熔點3D打印金屬粉末來說,顆粒D90過大會造成3D打印過程中金屬粉不易融化,從而造成過程打印不連續;但是金屬粉末粒度過細容易在3D打印的過程中造成搭橋,從而造成產品內部有空心、氣泡等現象產生,由此造成產品性能下降。在本發明中,所述金屬粉末的平均粒徑優選D10>25μm,D90<150μm,更優選D10>30μm,D90<120μm。對于增材制造(3D打印)用粉來說,氧含量越低越好,過高的氧含量會造成制造的金屬器材中存在氧化物而形成缺陷。在本發明中,所述金屬粉末的氧含量優選≤500ppm。本發明提供了一種金屬制品,以上述技術方案所述的金屬粉末為原料進行3D打印制備得到。本發明提供了一種上述技術方案所述的金屬粉末作為3D打印原料的應用。本發明提供的方法制備得到的金屬粉末粒度分布較窄,顆粒棱角平滑,具有良好的鋪展性和流動性,尤其適用于作為3D打印原料,制備得到的金屬制品質量較高,不會出現空心、氣泡等缺陷。與現有技術相比,本發明提供的金屬粉末的制備方法設備投資小;生產成本低;工作效率高;工藝路線短。本發明以下實施例所用到的原料均為市售商品。實施例1選用鉭含量達到99.995%以上的鉭錠,將鉭錠進行氫化破碎。將鉭錠氫化后所得的鉭屑,先過100目篩,而后再將100目篩下面的鉭粉過325目篩,取325目篩上面的鉭粉,從而得到100~325目之間的鉭顆粒10kg,而后將該鉭顆粒裝入反應彈內,在抽空條件下加熱,在900℃保溫約120分鐘,然后進行降溫、出爐、過100篩得到脫氫的鉭粉9.96kg,分析其氫含量見表1,表1為本發明實施例制備得到脫氫的鉭粉中的氫含量。將上述得到脫氫的鉭粉裝入攪拌球磨機,加入40kg直徑為φ4mm的鋼珠,而后加入10L酒精,再加入鉭粉重量1.2%的異丙醇。調整轉速為80轉/分鐘,球磨2小時,而后將球磨后鉭粉用HNO3和HF的混合酸(HNO3、HF和水的體積比是4:1:20)酸洗去除金屬雜質,烘干過篩,得到球磨酸洗后的鉭粉9.59kg。而后通過水力分級進一步去除超細粉,分級后的物料進行烘干過篩,得到鉭粉9.31kg。然后將上述鉭粉與以鉭粉重量計的1.2%的鎂粉混合,然后在惰性氣體保護的情況下加熱到780℃保溫2小時,然后再抽真空,在10~1Pa真空條件下再保溫約2小時,然后在抽真空條件下再升溫至1200℃保溫2小時,最后降溫、鈍化、出爐,用硝酸洗滌去掉多余的鎂及氧化鎂,然后用去離子水洗到中性,烘干過篩得到鉭粉末9.21kg。對本發明實施例1制備得到的鉭粉按照GB/T15076《鉭鈮化學分析方法》進行成分測量,檢測結果如表2所示,表2為本發明實施例制備得到的鉭粉末性能測試結果。采用馬爾文儀器的Mastersizer2000測得本發明實施例1制備得到的鉭粉末的粒度分布,測試結果如圖1所示,圖1為本發明實施例1制備得到的鉭粉末的粒度分布圖。采用JSM-5610LV高低分辨率掃描電鏡儀器對本發明實施例1制備得到的鉭粉末進行SEM檢測,檢測結果如圖2所示,圖2為本發明實施例1制備得到的碳粉末的400倍的SEM照片。實施例2選用由鉭含量達到99.95%以上的鉭錠,將鉭錠進行氫化破碎。將鉭錠氫化后所得的鉭屑先過200目篩,而后再將200目篩下面的鉭粉過500目篩,取500目篩上面的鉭粉,從而得到200~500目之間的鉭顆粒10kg,而后將該鉭顆粒通過水力分級進一步去除超細粉,分級后的物料進行烘干過篩,得到鉭粉9.46kg。而后將該鉭粉裝入反應彈內,在抽空條件下加熱,在850℃保溫約120分鐘,然后進行降溫、鈍化、出爐、過200篩得到脫氫的鉭粉9.38kg,分析其氫含量見表1。將上述得到脫氫的鉭粉裝入攪拌球磨機,加入40kg直徑為φ3mm的鋼珠,而后加入10L酒精,再加入鉭粉重量1.3%的異丙醇。調整轉速為80轉/分鐘,球磨2.5小時,而后將球磨后鉭粉用HNO3和HF的混合酸(HNO3、HF和水的體積比是4:1:20)酸洗去除金屬雜質,烘干過篩,得到球磨酸洗后的鉭粉9.08kg。而后再將該鉭粉通過水力分級進一步去除超細粉,分級后的物料進行烘干過篩,得到鉭粉8.96kg。然后將鉭粉與以鉭粉重量計的1.3%的鎂粉混合,然后在惰性氣體保護的情況下加熱到750℃,保溫2小時,然后再抽真空,在10-1Pa真空條件下再保溫約2小時,然后在抽真空條件下再升溫至1100℃保溫2小時,最后降溫、鈍化、出爐,用硝酸洗滌去掉多余的鎂及氧化鎂,然后用去離子水洗到中性,將鉭粉烘干過篩得到鉭粉末8.85kg。按照實施例1所述的方法對本發明實施例2制備得到的鉭粉末進行性能測試,檢測結果如表2所示。表1本發明實施例制備得到脫氫的鉭粉中的氫含量氫含量實施例1實施例2H(ppm)140210表2本發明實施例制備得到的鉭粉末性能測試結果由表2可知,采用本發明提供的方法制備得到的金屬粉末的粒度分布范圍集中,同時具有低的O含量。由以上實施例可知,本發明提供了一種金屬粉末的的制備方法,包括以下步驟:1)將金屬原料氫化破碎后進行分級處理,得到金屬顆粒;2)將金屬顆粒進行脫氫處理,得到脫氫后金屬顆粒;3)將所述脫氫后金屬顆粒進行球磨處理,得到金屬粉體;4)將所述金屬粉體進行脫氧處理,得到金屬粉末。與現有技術相比,本發明采用氫化破碎的方法得到金屬粉末,尤其是在脫氫處理后采用球磨的方法制備金屬粉末,這種方法制備得到的金屬粉末粒度分布較窄,顆粒棱角平滑,具有良好的鋪展性和流動性,作為3D打印原料能夠避免制備得到的產品出現空心、氣泡的缺陷,提高產品的質量。以上實施例的說明只是用于幫助理解本發明的方法及其核心思想。應當指出,對于本
技術領域:
的普通技術人員來說,在不脫離本發明原理的前提下,還可以對本發明進行若干改進和修飾,這些改進和修飾也落入本發明權利要求的保護范圍內。當前第1頁1 2 3