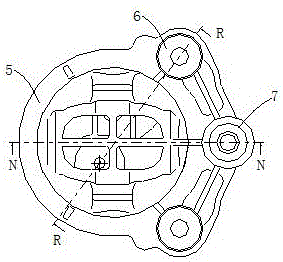
本發明屬于鑄造
技術領域:
,涉及一種汽車后橋主要配件的鑄造,具體涉及一種主減速器殼體的鑄造方法。
背景技術:
:減速器殼體裝配于汽車后橋,其結構復雜,對機械性能有較高的要求,是重要的汽車零部件,一般通過球墨鑄鐵鑄造成型。傳統的主減速器殼體鑄造方法是潮模砂型內納入覆膜砂芯,由潮模砂形成鑄件外殼,覆膜砂芯形成鑄件內腔。但這種鑄造方法有幾個明顯的缺點:1、對潮模砂混制質量要求高,容易產生砂孔、氣孔等鑄造缺陷;2、尺寸精度較低;3、該主減速器殼體多處壁厚突變較大,潮模砂型剛度較低,不利于消除縮孔縮松缺陷;4、鑄件外殼表面粗糙。由于傳統的主減速器殼體鑄造方法存在上述種種缺點,因此,主減速器殼體的鑄造方法有必要進一步改進。技術實現要素:本發明的目的是為了解決現有技術中減速器殼體在鑄造時所存在的缺陷,提供一種主減速器殼體的鑄造方法。為了實現上述目的,本發明技術思路為開發出一種新的主減速器殼體鑄造方法和工藝,采用新型覆膜砂殼型埋鋼丸生產方法,通過先進的模具工藝設計,最終生產出合格的主減速器殼體鑄件產品。本發明采用的技術方案是:一種主減速器殼體的鑄造方法,包括覆膜砂芯成型工藝、熔煉球鐵工藝和澆鑄工藝,覆膜砂芯成型工藝包括覆膜砂制芯、覆膜砂型裝配和砂型填埋鋼丸;熔煉球鐵工藝包括電爐熔煉、鐵水出爐和處理;澆鑄工藝步驟如下:(1)澆鑄;將澆鑄溫度范圍控制在1350--1430℃;單件澆鑄時間10±2s,球化包澆鑄時間控制在8min以內,型腔內部的氣體壓力小于達到侵入鐵水的壓力臨界值;(2)出箱;采用全自動出箱機構,設備自動翻箱后,鑄件、鋼丸、覆膜砂型自動分離;(3)去除澆冒口;其中冒口設計至少比鑄件高50mm,冒口頸根部做出斷口槽,去除澆冒口后鑄件不帶肉;(4)一次拋丸;采用懸掛式拋丸機,一次拋丸的懸掛方式為主減速器殼體的兩側垂直向下,鑄件內腔朝拋丸方向,拋丸時間20--25min;(5)打磨;用砂輪將鑄件的澆口、飛邊去除;(6)二次拋丸;二次拋丸;采用懸掛式拋丸機,二次拋丸懸掛方式為掛桿穿過主減速器殼體鑄件內部隔板上小孔,鑄件外殼朝拋丸方向,拋丸時間10--15min;二次拋丸后檢驗合格得鑄件產品。進一步,澆鑄過程中,鐵水倒入直澆道,通過陶瓷過濾片,將鐵水中的渣及其它雜質過濾掉,干凈鐵水平穩地向兩側橫澆道流動,然后經過冒口窩,最終流入鑄件型腔當中,隨著鐵水流入,鑄件型腔內的氣體透過覆膜砂型排出型腔外,排到型腔外的氣體透過鋼丸堆,進入到大氣中被吸塵罩吸入凈化;由于鋼丸堆和覆膜砂型的透氣性好,且覆膜砂型內部設有排氣通道,型腔內部的氣體不足以達到侵入鐵水的壓力臨界值,從而達到避免氣孔缺陷的目的。進一步,出箱后,覆膜砂型集中輸入到廢砂斗供回收利用,鋼丸經過冷卻系統進入鋼丸斗循環使用,鑄件通過震動落砂板集中進入到去除澆冒口區。進一步,覆膜砂芯成型工藝制備的主減速器殼體的覆膜砂芯,包括相互配合的第一砂芯,第二砂芯、第三砂芯、第四砂芯以及第五砂芯,其特征在于,在第五砂芯上連接有冒口砂芯和直澆道砂芯,第一砂芯上設有徑向凸緣,第三砂芯上設有與徑向凸緣吻合的凹槽,第二砂芯設置在第一砂芯和第三砂芯之間并緊密接觸,第四砂芯安置在第三砂芯上方,第四砂芯上設有定位塊,第五砂芯設有與定位塊對應的定位槽,第一砂芯、第三砂芯、第四砂芯以及第五砂芯上均設有相互吻合并貫通的連通槽。進一步,所述第一砂芯和第五砂芯上均設有凹孔,凹孔與所述直澆道砂芯連通。進一步,所述各砂芯均帶有加強筋;優選,第五砂芯就屬于平板狀類砂芯,為了防止其變形,首先在設計層面上,在砂芯上設置多道加強筋,其次在第五砂芯剛從殼型機中取出處于熱狀態時,將其與第一砂芯先裝配好,將第五砂芯容易產生變形的周圍一圈利用第一砂芯的裝配臺階支撐固定住,待第五砂芯冷卻后再取出疊放好,能有效防止第五砂芯變形。進一步,將覆膜砂型放入生產線鐵框內,向鐵框內加入鋼丸,振動臺將鋼丸震動緊實后,將鐵框自動推到待澆鑄區。進一步,覆膜砂芯成型工藝還包括MAGMA模擬,是對鐵水充型和凝固收縮做一個模擬分析;為調整澆冒口尺寸或改變鑄件入水口位置提供模擬數據。進一步,采用內包式砂芯裝配結構,第一砂芯由徑向凸緣11這一小塊砂芯作為定位和支撐結構,將第三砂芯與徑向凸緣11吻合的凹槽31固定住;由于裝配處中空,有利于砂芯排氣。進一步,熔煉球鐵工藝包括以下步驟:(1)在熔煉爐中分若干次加入爐料,爐料包括球鐵屑、回爐料和廢鋼,先在爐底中加入一次爐料,待爐子底下開始化出鐵水后,開始加入增碳劑;每次加入增碳劑后,用爐料壓住,爐料的加入次數比增碳劑加入次數多一次;其中,回爐料要預留10±2%;(2)分若干次全部加完爐料后,熔煉爐中爐料全部熔化時,開始升溫至鐵水溫度達1550±5℃,保溫3±0.5分鐘,保溫時攪拌均勻,待所有增碳劑完全熔化完后,加入除渣劑,渣全部集中在一起后,將渣用打渣棍挑出爐子外面;(3)爐前取樣化驗,爐前化驗各大元素達到要求之后,加入步驟(1)預留的回爐料,升溫到1620±5℃,進行球化處理,球化是采用堤壩式球化包,球化劑的加入量為1.5±0.1%,放在鐵水對沖的另一側,在球化劑上壓1±0.1%的球鐵屑和0.5±0.2%的硅鐵孕育劑;(4)二次孕育處理;在大包轉小包時候,進行二次孕育;孕育方法是用0.5mm規格的硅鋇粉,通過孕育漏斗,每一小包鐵水加入孕育劑量為0.2±0.05%;(5)澆鑄產品材質:所得球鐵的球化級別為2~3級,硬度在155HB-165HB之間;基于球鐵的質量百分比計,珠光體含量5%±0.5%,S含量<0.02%,鐵素體含量>85%,不含游離滲碳體,以上百分比為質量百分比。進一步,步驟(1)中,廢鋼所占的比例≥65%,增碳劑的比例為2.5%±0.2%;回爐料和球鐵屑按照1:1的比例搭配使用。進一步,所述廢鋼包括邊角料廢鋼;回爐料包括澆冒口。進一步,增碳劑為低硫增碳劑,選用煅后焦,其內的固定C含量≥98.5%,S含量≤0.05%。進一步,增碳劑的粒度為5±0.5mm粒度。進一步,步驟(3)中,球化處理前的原鐵水的C含量為4.0%±1%,Si含量1.2%±0.2%。進一步,熔煉爐采用中頻感應爐熔煉。進一步,在熔煉爐中分10±2次等量加入爐料。本發明的有益效果為:1、采用覆膜砂殼型埋鋼丸的生產方法,相比傳統主減速器殼體鑄造方法具有生產過程更容易控制,高尺寸精度,高表面光潔度的優勢。2、將容易因排氣不暢導致鑄件產生氣孔缺陷的第一至第五砂芯內部設計貫通,保證排氣通暢,從砂芯排氣工藝上避免鑄件氣孔缺陷的產生。3、為降低砂芯高度、減少覆膜砂用量,采用內包式砂芯裝配結構,既減小了砂芯充填難度、有利于砂芯排氣,更降低了生產成本。4、為保證鑄件良好的組織致密性,通過運用magma鑄造模擬軟件多次模擬對比,不斷優化改進澆注系統,確保鑄件無縮孔縮松,最終定型工藝。5、為解決砂芯變形問題,在各砂芯易變形部位設計加強筋,并專門針對平板狀第五砂芯增加變形矯正工序,最大限度地防止砂芯變形。6、熔煉球鐵工藝中,創造性地在生產過程中通過對細節的處理和對爐料的掌控,在爐料使用廢鋼含量大于2/3,用增碳劑所增加碳含量,大于總含碳量一半的情況下,把加入增碳劑的次數從三次提高到十次,并且每次加入后都在上面壓上廢鋼回爐料等重量較重的原材料。在出鐵水前在爐子里面高溫保溫3分鐘,使得原鐵水的含碳量有著顯著的提升。原鐵水的含碳量提高了,相對應的球化后鐵水的含碳量也就會提升,顯著提高了增碳劑的吸收率。提高了產品質量,降低了生產成本。同時,在砂芯防錯定位、模具射砂排氣等工藝措施及其他細節方面做了大量工作。第一砂芯上設有徑向凸緣,第三砂芯上設有與徑向凸緣吻合的凹槽,第二砂芯設置在第一砂芯和第三砂芯之間并緊密接觸,第四砂芯安置在第三砂芯上方,第四砂芯上設有定位塊,第五砂芯設有與定位塊對應的定位槽,各個砂芯裝配后牢固、穩定,而且第一砂芯、第三砂芯、第四砂芯以及第五砂芯上均設有相互吻合并貫通的連通槽,保證排氣通暢,從砂芯排氣工藝上避免鑄件氣孔缺陷的產生,砂孔、氣孔缺陷廢品率控制在1%以內,無縮孔縮松缺陷,鑄件尺寸穩定性好,表面光潔度高,相比傳統主減速器殼體鑄造方法具有成品率更高,生產過程更容易控制,產品競爭力更強的優勢。因此,本發明容易穩定控制砂孔和氣孔缺陷,減小縮孔傾向,達到高尺寸精度,高表面光潔度。附圖說明圖1工藝流程圖;圖2為本發明覆膜砂的示意圖;圖3為圖2中沿R-R線的截面示意圖;圖4為圖2中沿N-N線的截面示意圖;圖5為本發明的裝配示意圖;圖6為本發明的砂型填埋鋼丸填埋示意圖;圖7為本發明MAGMA模擬圖;圖8是本發明實施例1球鐵產品具有代表性的兩塊本體切塊腐蝕后的金相照片;圖9是本發明對比例2球鐵產品具有代表性的兩塊本體切塊腐蝕后的金相照片。具體實施方式下面結以具體實施例對本發明做進一步的說明。實施例1:覆膜砂制芯是鑄造方法中重要的一環,制芯設備采用全自動雙頭殼型機,制芯步驟如下。1、將各砂芯模具分別安裝到殼型機上,檢查設備完好,打開模具加熱開關;2、模具溫度到達設定溫度后,檢查氣壓表讀數正常,開始制芯;3、按下殼型機啟動按鈕,設備自動完成一組制芯工序:上下模合模——兩側射砂頭壓緊模具——壓縮空氣將兩側砂斗里的覆膜砂射入模具——覆膜砂在高溫模具內固化——固化結束自動開模——頂桿將砂芯頂出;4、將砂芯取出,開始下一組制芯工序。制芯參數需根據砂芯形狀、重量而定,以第一砂芯為例,通過調試,最終將制芯參數定為:模具溫度230±10℃、射砂氣壓0.4—0.6Mpa、射砂時間4s、固化時間110s。在此參數下,制出的砂芯緊實,顏色正常,砂芯內部燒結情況良好。如圖2至圖5所示,主減速器殼體的覆膜砂芯,包括相互配合的第一砂芯1,第二砂芯2、第三砂芯3、第四砂芯4以及第五砂芯5,在第五砂芯5上連接有冒口砂芯6和直澆道砂芯7,第一砂芯1上設有徑向凸緣11,第三砂芯3上設有與徑向凸緣11吻合的凹槽31,第二砂芯2設置在第一砂芯1和第三砂芯3之間并緊密接觸,第四砂芯4安置在第三砂芯3上方,第四砂芯4上設有定位塊41,第五砂芯5設有與定位塊41對應的定位槽51,第一砂芯1、第三砂芯3、第四砂芯4以及第五砂芯5上均設有相互吻合并貫通的連通槽8,第一砂芯1和第五砂芯2上均設有凹孔9,凹孔9與直澆道砂芯7連通,各砂芯均帶有加強筋。該覆膜砂芯的第一砂芯1上設有徑向凸緣11,第三砂芯3上設有與徑向凸緣11吻合的凹槽31,第二砂芯2設置在第一砂芯1和第三砂芯3之間并緊密接觸,第四砂芯4安置在第三砂芯3上方,第四砂芯4上設有定位塊41,第五砂芯5設有與定位塊41對應的定位槽51,各個砂芯裝配后牢固、穩定,而且第一砂芯1、第三砂芯3、第四砂芯4以及第五砂芯5上均設有相互吻合并貫通的連通槽8,保證排氣通暢,從砂芯排氣工藝上避免鑄件氣孔缺陷的產生,砂孔、氣孔缺陷廢品率控制在1%以內,無縮孔縮松缺陷,鑄件尺寸穩定性好,表面光潔度高,相比傳統主減速器殼體鑄造方法具有成品率更高,生產過程更容易控制,產品競爭力更強的優勢。如圖6將覆膜砂型10放入生產線鐵框20內,生產線鋼丸斗向鐵框內加入大約500kg鋼丸30,振動臺將鋼丸震動緊實后鐵框自動推到待澆鑄區。如圖7,覆膜砂芯成型工藝還包括MAGMA模擬,MAGMA模擬主要是對鐵水充型和凝固收縮做一個模擬分析。例如鐵水充型模擬,通過模擬結果中的鐵水流動路徑及狀態,判斷鑄件澆鑄過程中是否有產生卷氣、紊流等風險,若有,則需要針對模擬結果調整澆冒口尺寸或改變鑄件入水口位置,調整好后再次進行模擬,如此循環往復,直至得到滿意的模擬結果,最終將工藝定型。如圖1所示,覆膜砂制芯、覆膜砂型裝配如上述所述的技術內容。熔煉球鐵工藝涉及電爐熔煉、鐵水出爐及球化處理:熔煉設備是中頻感應爐,每爐的滿負荷容量為1800KG。原料包括廢鋼、回爐料和增碳劑,以原料的質量百分比計,廢鋼所占的比例>65%。廢鋼為本廠邊角料廢鋼,回爐料為本廠的回爐料。選用合理大小的增碳劑粒度,能保證增碳劑的最大吸收率。根據本廠中頻感應爐的大小,選用5mm直徑粒度的高品質低硫增碳劑。以質量百分比計,增碳劑內的固定C含量>98.5%,S含量<0.05%,增碳劑的加入總量為45KG;選用優質穩定的增碳劑,是保證增碳劑使用穩定的前提。廢鋼熔煉球鐵的步驟如下:(1)在中頻感應爐熔煉中分11次等量加入爐料,爐料包括球鐵屑、回爐料和廢鋼,其中廢鋼所占的比例≥65%,增碳劑的比例為2.5%±0.2%;回爐料和球鐵屑按照1:1的比例搭配使用,所述廢鋼包括邊角料廢鋼,回爐料包括澆冒口;先在爐底中加入一次爐料,待爐子底下開始化出鐵水后,開始加入增碳劑,增碳劑為低硫增碳劑,選用煅后焦,以質量百分比計,其內的固定C含量≥98.5%,S含量≤0.05%,增碳劑的粒度為5mm粒度;每次加入增碳劑后,用爐料壓住,增碳劑分10次等量加入;其中,回爐料要預留10%±2%;增碳劑的加入時間要盡量長;每次用鐵鍬加入增碳劑后,用鐵屑、澆冒口和廢鋼壓住,防止增碳劑上浮以影響吸收率。(2)分11次全部加完爐料后,鐵水燒到中頻感應爐容量的九成滿時,即熔煉爐中爐料全部熔化時,開始升溫至鐵水溫度達1550℃,保溫3分鐘,保溫時攪拌均勻,待所有增碳劑完全熔化完后,加入除渣劑,渣全部集中在一起后,將渣用打渣棍挑出爐子外面;保溫時用打渣棍充分攪拌均勻,使得爐內增碳劑能夠充分的融化分解,達到最大的吸收率;攪拌均勻后,除去鐵水上面的渣。(3)爐前取樣化驗,爐前化驗各大元素達到要求之后,其中,鐵水的C含量為4.0%±0.1%,Si含量1.2%±0.2%;加入步驟(1)預留的回爐料,升溫到出爐溫度后出鐵水球化處理;即升溫到1620℃,進行球化處理,球化是采用堤壩式球化包,球化劑的加入量為1.5%,放在鐵水對沖的另一側,在球化劑上壓1%的球鐵屑和0.5%的硅鐵孕育劑;(4)二次孕育處理;在大包轉小包時候,進行二次孕育;孕育方法是用0.5mm規格的硅鋇粉,通過孕育漏斗,每一小包鐵水加入孕育劑量為0.2%;防止因球化劑的加入使得球鐵的過冷傾向增大,從而減少碳化物的析出,促進析出大量細小而圓整的石墨球。(5)澆鑄;所得球鐵的球化級別為2~3級,硬度在155HB-165HB之間;基于球鐵的質量百分比計,珠光體含量5%±0.5%,S含量<0.02%,鐵素體含量>85%,不含游離滲碳體,以上百分比為質量百分比。本發明自身對比例:也是采用中頻感應爐為熔煉設備,每爐的滿負荷容量為1800KG。由于產品含硫量有嚴格的要求,增碳劑加入量一般比較大,一爐鐵水增碳劑的加入量為45KG。因此,增碳劑選用高品質的低硫增碳劑,即固定碳含量98.5%>,含硫量0.05%<的高品質煅后焦;選用的是3mm直徑的粒度。由于加入量較大,采取分次數加入的方法,平均分成三份,分三次加入。一份加在爐底,上面蓋上球鐵屑,澆冒口,再加廢鋼。等爐子融化出1/3鐵水再把第二份加入,依次加入球鐵屑,澆冒口,廢鋼。鐵水融化出半爐再把剩下的1/3增碳劑加入。爐料加9成以后,先不急著打渣,在溫度達到1500℃左右用打渣棍充分攪拌均勻,再除渣,除渣后爐前取樣化驗,化驗無誤后,再把剩下的爐料加入,升溫到指定溫度,出水球化處理。經過爐前光譜分析檢測,增碳劑的吸收率只有85—90%之間。對比分析:一、實施例原鐵水的光譜分析結果如表1所示:表1CSiMnPS第一組4.021.180.1910.0110.016第二組4.031.180.1880.0120.015第三組4.011.210.1890.0110.014第四組4.041.180.1920.0130.016實施例球化處理后的光譜分析結果如表2所示:表2CSiMnPSMgCe第一組3.842.610.1920.0120.0120.0440.023第二組3.832.620.1890.0090.0140.0410.022第三組3.852.630.1930.010.0150.0430.026第四組3.852.580.1910.0110.0130.0450.024二、對比例原鐵水的光譜分析結果如表3所示:表3對比例球化處理后的光譜分析結果如表4所示:表4表1提高吸收率后原鐵水碳含量,表3吸收率提高之前原鐵水碳含量;對比表1表3能發現,在爐料使用廢鋼含量大于2/3,用增碳劑所增加碳含量,大于總含碳量一半的情況下,把加入增碳劑的次數從三次提高到十次,并且每次加入后都在上面壓上廢鋼回爐料等重量較重的原材料。在出鐵水前在爐子里面高溫保溫3分鐘,使得原鐵水的含碳量有著顯著的提升。原鐵水的含碳量提高了,相對應的球化后鐵水的含碳量也就會提升,表2表4能清楚的看到。表2所示的爐前光譜分析檢測結果,增碳劑的吸收率達到95%以上。如圖8所示球鐵的金相照片,球化級別2-3級,硬度在155HB-165HB之間;經檢測,基于球鐵的質量百分比計,珠光體含量在5%左右,S含量<0.02%,鐵素體含量>85%,不含游離滲碳體。同時原鐵水白口及反白口傾向較小;生產的球鐵中石墨球尺寸小,圓整度高,鐵素體含量多,球鐵的韌性提高。表4所示的爐前光譜分析檢測結果,增碳劑的吸收率只有85—90%之間。如圖9所示球化級別2-3級,珠光體含量20%左右,硬度在170HB-180HB之間,不符合客戶對于硬度的要求,影響其加工性能。具體澆鑄鑄造方法為:(1)澆鑄;本實施例涉及的主減速器殼體,經過多次澆鑄試驗,發現澆鑄溫度低于1350℃時,鑄件出現冷隔的概率較高,澆鑄溫度高于1430℃時,鑄件容易產生粘砂問題,最終將澆鑄溫度范圍定在1350--1430℃。單件澆鑄時間10±2s,球化包澆鑄時間控制在8min以內。澆鑄過程中,鐵水倒入直澆道,通過陶瓷過濾片,將鐵水中的渣及其它雜質過濾掉,干凈鐵水平穩地向兩側橫澆道流動,然后經過冒口窩,最終流入鑄件型腔當中,隨著鐵水流入,鑄件型腔內的氣體透過覆膜砂型排出型腔外,排到型腔外的氣體透過鋼丸堆,進入到大氣中被吸塵罩吸入凈化。由于鋼丸堆和覆膜砂型的透氣性好,且覆膜砂型內部設有排氣通道,型腔內部的氣體不足以達到侵入鐵水的壓力臨界值,從而達到避免氣孔缺陷的目的。(2)出箱;采用全自動出箱機構,設備自動翻箱后,鑄件、鋼丸、覆膜砂型自動分離,覆膜砂型集中輸入到廢砂斗供回收利用,鋼丸經過冷卻系統進入鋼丸斗循環使用,鑄件通過震動落砂板集中進入到去除澆冒口區。(3)去除澆冒口;采用鐵錘敲擊冒口的方式去除澆冒口,冒口設計比鑄件高50mm,方便敲擊,冒口頸根部做出斷口槽,鐵錘敲擊時澆冒口容易分離并能避免鑄件帶肉。(4)一次拋丸;本主減速器殼體內腔形狀復雜,且有油道,鑄件要求不能留有殘砂,一般拋丸工序是:粗拋--精拋--內腔拋丸。為減少工序、減低成本,通過多次拋丸試驗,將拋丸工序簡化為:一次拋丸、二次拋丸。采用懸掛式拋丸機,一次拋丸的懸掛方式為主減速器殼體的兩側垂直向下,鑄件內腔朝拋丸方向,拋丸時間20--25min。(5)打磨;用砂輪機、手磨機將鑄件的澆口、飛邊去除。相比傳統主減速器殼體鑄造方法,由于本覆膜砂型裝配間隙小,所以飛邊的打磨工作量小。(6)二次拋丸;采用懸掛式拋丸機,二次拋丸懸掛方式為掛桿穿過主減速器殼體鑄件內部隔板上的Φ45小孔,鑄件外殼朝拋丸方向,拋丸時間10--15min。(7)檢驗;嚴格按照《產品出廠檢驗報告單》內容,檢驗標準見表5。表5產品出廠檢驗標準本實施例中:各砂芯均帶有加強筋。覆膜砂芯熱狀態時強度相對較低,此時容易產生變形,尤其是平板狀類砂芯,第五砂芯就屬于這一類砂芯,為了防止其變形,首先在設計層面上,在砂芯上設置多道加強筋,其次在第五砂芯剛從殼型機中取出處于熱狀態時,將其與第一砂芯先裝配好,該操作目的在于將第五砂芯容易產生變形的周圍一圈利用第一砂芯的裝配臺階支撐固定住,待第五砂芯冷卻后再取出疊放好,能有效防止第五砂芯變形。第一至第五砂芯內部設計貫通,保證排氣通暢,從砂芯排氣工藝上避免鑄件氣孔缺陷的產生;如何穩定控制砂孔和氣孔缺陷,減小縮孔傾向,達到高尺寸精度,高表面光潔度。覆膜砂強度比潮模砂強度高很多,基本不會因為觸碰和震動產生掉砂問題,從而在根源上避免了鑄件砂孔缺陷;潮模砂氣孔缺陷不容易穩定控制是因為潮模砂內的水分含量時時有波動,而覆膜砂型只要監控好每批次覆膜砂原材料的發氣量,相對更容易控制,所以更容易穩定控制鑄件氣孔缺陷;鋼丸導熱系數比潮模砂導熱系數大,鑄件凝固速度更快,有利于澆冒口補縮,所以該生產方法比潮模砂生產方法的鑄件縮孔傾向更小;由于覆膜砂芯強度高,砂芯裝配穩固、裝配間隙小,故能夠達到高尺寸精度;覆膜砂芯表面比潮模砂更為緊實光滑,相應的,由覆膜砂芯形成的鑄件表面也具有更高的表面光潔度。采用覆膜砂型內包式砂芯裝配結構及技術,既降低了砂芯充填難度、有利于砂芯排氣。傳統覆膜砂芯納入潮模砂生產方式受限于潮模砂的強度不高,只能使用外插式裝配結構,而覆膜砂芯強度高,第一砂芯由徑向凸緣11這一小塊砂芯作為定位和支撐結構,將第三砂芯與徑向凸緣11吻合的凹槽31固定住。這種內包式砂芯裝配結構不需要做出芯頭,所以砂芯高度更小,既減少了覆膜砂用量,降低了砂芯充填難度,還由于裝配處中空,有利于砂芯排氣。本實施例,鑄造方法相比傳統鑄造方法更具靈活性,傳統方法潮模砂造好型后,幾天內必須澆鑄完。而覆膜砂型只要存放得當,可存放3個月甚至更長,這對車間生產安排十分有利,生產受設備故障等因素的影響相對較小。以上顯示和描述了本發明的基本原理、主要特征和本發明的優點。本行業的技術人員應該了解,本發明不受上述實施例的限制,上述實施例和說明書中描述的只是本發明的原理,在不脫離本發明精神和范圍的前提下本發明還會有各種變化和改進,這些變化和改進都落入要求保護的本發明的范圍內。本發明要求的保護范圍由所附的權利要求書及其等同物界定。當前第1頁1 2 3