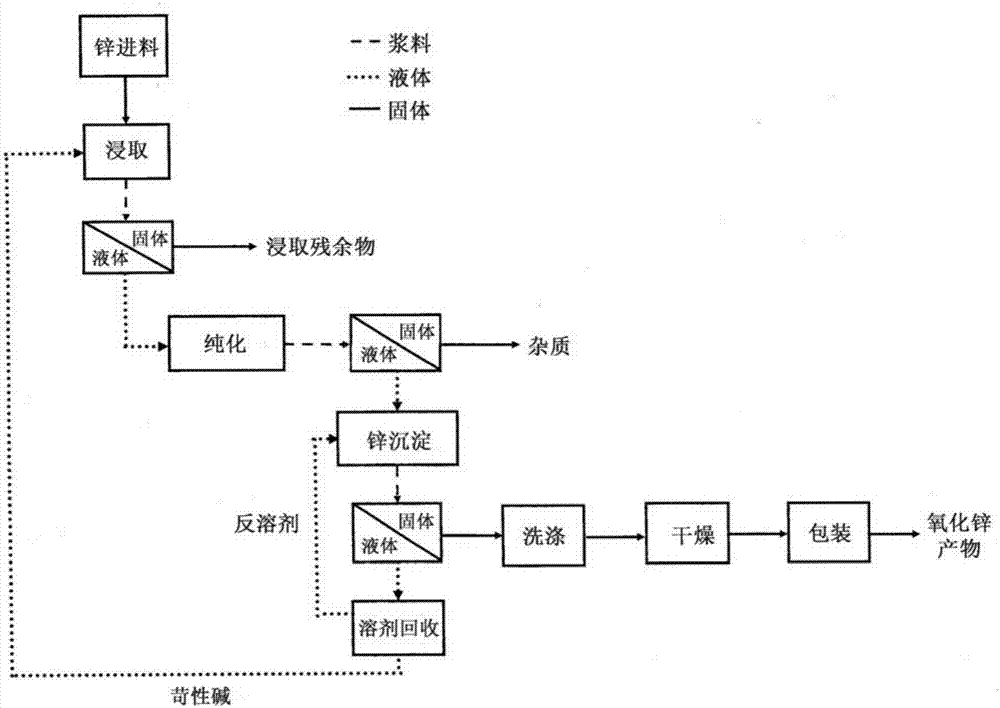
本申請是中國國家申請號為201180073364.7(pct申請號為pct/us2011/056852)、申請日為2011年10月19日、發明名稱為“用于純化氧化鋅的方法”的發明專利申請的分案申請。
背景技術:
:濕法冶金是將貴重的金屬物質從其他較低價值的材料中分離的方法。所述方法涉及將貴重的金屬物質溶解到水溶液中,然后將其與不可溶殘余物分離。為了提高離子的溶解速率和增加溶液中金屬離子的負載,通常的做法是使用酸性或堿性溶液。特別有用的堿性溶液的實例是氫氧化鈉在水中的混合物。也可以使用其他堿性材料,但氫氧化鈉相對較低的成本通常使得它成為最經濟的選擇。負載有溶解的金屬的水溶液稱為“母液”。可以通過一種或多種方式從母液中回收溶解的金屬,其包括:電解、中和和不混溶溶劑萃取。用濕法冶金方法來回收貴重金屬已經有幾十年。下文的討論和實例都是基于從混合原料材料回收氧化鋅。堿性可溶的氧化鋅是從非堿性可溶的材料中分離的。非可溶的材料包括(但不限于)金屬和金屬氧化物,例如鐵、氧化鐵、鎳、鈷、貴金屬和非金屬氧化物諸如二氧化硅。在關于從含有鋅的原料混合物中回收鋅的文獻中,有若干種方法。這些方法通常包括三個一般步驟:1.通常在升高的溫度,將含有鋅的原料與稀釋的堿接觸,以選擇性地溶解鋅2.通過過濾、離心或其他方式,從堿性溶液中分離浸取殘余物3.通過電解提取、中和或其他方式,從堿性溶液(母液)回收鋅。在這一方法中最困難的步驟通常是從母液分離中浸取殘余物。母液中懸浮的細粒子很難徹底去除。相對高的母液粘度和表面張力使得通過過濾或離心去除這些細粒子極其緩慢。但是,如果所述粒子沒有基本上完全從母液隔離,那么之后它們會在下一步驟中污染富鋅產物,導致整個純化方法無效。j.frenay等人的題為“通過cebedeau方法從電煉鋼塵中回收鉛和鋅(recoveryofleadandzincfromelectricsteelmakingdustbythecebedeauprocess)”的文章總結了將鋅從堿性不可溶物質分離的商業和中試規模的嘗試。高度濃縮的堿性溶液的高粘度通常將商業操作限制在大約25–30重量百分比堿的最大濃度。濕法冶金加工的成本在很大程度上依賴于母液中溶解的金屬物質的負載或濃度。當負載增加時,必須被加工以產生給定量產物的液體的量減少,同時節約了設備和運營費用。較高濃度的堿允許溶液中堿可溶金屬的較高負載。然而,較高濃度的堿也產生顯著更粘稠的溶液。這較高的粘度阻礙了下游加工,包括將母液從浸取殘余物中分離。已開發了許多方法來利用濕法冶金從各種廢料中回收鋅,但很少在商業上是成功的。在很大程度上,這歸因于從母液中回收溶解的金屬物質的高成本。典型的金屬回收策略包括:●電解,其中流動的電流將金屬離子還原為金屬并將金屬原子鍍在電極上。●將液體中和到接近中性的ph值,以沉淀各種金屬的鹽、氫氧化物或氧化物。●用不混溶的溶劑萃取金屬離子或絡合物。所有這些金屬回收的方法都是相對昂貴的。●電解需要大量的電流以將金屬從較高價態還原為金屬。此外,如果金屬氧化物是所期望的最終產物,那么堿金屬必須經受氧化加工以產生氧化物形式。●母液的中和需要大量試劑。中和方法有效地破壞了液體以便進一步提取,并產生了必須處理的廢鹽流。●使用不混溶的溶劑(例如摻雜有機胺的煤油)的提取通常需要大量過量的萃取溶劑以及昂貴的后加工以從所述不混溶的溶劑中回收金屬。lemaire的美國專利第4,005,061號公開了使用可混溶的溶劑從廢棄電池的鋅/空氣電解質除去鋅的方法。在'061專利中引用的單一材料的特征為“廢物”,然而,這一化學系統,實際上,是包含氫氧化鉀和鋅酸鉀以及幾個百分比的碳酸鉀和痕量雜質的廢料。所描述的系統涉及具有鋅負極的電化學蓄電池,并且因此,與作為本申請主題的冶金廢物和副產物材料不同并且遠不如其復雜。電解質是廢棄的,僅僅因為金屬鋅粉末已被空氣氧化為鋅酸鉀。它沒有與其他材料混合且僅發生一個簡單的化學反應。另一方面,冶金廢料和副產物,廢棄催化劑等,通常是包含若干顯著濃度的不同化學元素的絡合混合物,并且它們通常還含有若干不同的陰離子。在這些材料中的復雜性需要額外的加工步驟以將所需化合物與雜質和不需要的化合物分離。此外,沒有所描述的方法在其他類型的系統,尤其是更復雜的系統,或者在其它的兩性化合物的回收中有用的指征或建議。含有兩性金屬的不同化合物的溶解度可以顯著變化。例如,硫酸鉛僅溶于熱的濃縮的氫氧化鈉溶液,而硫酸鋅即使在室溫下也易溶于25%的naoh。鹵化物的溶解度在室溫下顯著下降到約35%苛性堿(caustic)以上。技術實現要素:本申請涉及從金屬、金屬氧化物和其他材料的混合物中回收鋅和氧化鋅的方法。根據某些實施例,所述方法包括:1.將鋅溶解到堿性溶液中,其通常具有足以溶解鋅但仍然抑制或防止鹵素、鹽和其他不需要物質的溶解的濃度。2.從未溶解的材料分離含有溶解的鋅的堿性溶液。3.純化堿性溶液以除去可溶于堿性溶液中的不需要的非鋅材料。4.用可溶性反溶劑,例如甲醇,沉淀鋅。5.通過分離技術,例如蒸餾或結晶,以回收適于在所述方法中循環使用的堿性溶液和反溶劑,來再生堿性溶液和反溶劑。這一方法的主要優點是反溶劑降低了氧化鋅在堿性溶液中的溶解度,而不破壞堿。它不會如酸一樣將其化學毀壞。這使得可以很容易地再生堿性溶液和反溶劑兩者,以在所述方法中循環使用。這一方法的另一個優點是稀釋事件中用水將具有鋅的溶液過飽和的能力是必要的以使固體能夠從母液中分離。如本文所公開的濕法冶金方法可以提高母液流中鋅的負載,從而提高了濕法冶金方法的容量,同時避免大的粘度增加,以使得下游的操作可以繼續暢通進行。通過首先將鋅或氧化鋅與濃縮堿性溶液接觸(如果鋅是金屬的,那么必須也加入氧化劑以氧化鋅),然后用水稀釋溶液來達到所期望的粘度,可在相對低粘度的堿性溶液中獲得非常高濃度的鋅。根據某些方面,所獲得的金屬負載量是通過簡單將金屬或金屬氧化物與稀釋的堿接觸的金屬負載量的大約3至5倍。人們以為通過將水添加到濃縮的堿性溶液并降低堿的濃度,所述系統將成為所溶解的金屬離子過飽和的并會產生沉淀。申請人已經證實,相當意外地,所期望的金屬離子保留在溶液中并且在隨后的加工過程中不沉淀。附圖說明圖1是在naoh在水中不同濃度下,實驗性測定的氧化鋅在堿性溶液中的溶解度的圖表。圖2是根據本發明的一個實施例說明回收氧化鋅的方法的流程圖。具體實施方式在相關部分中,引用的所有文件都以引用方式并入本文;任何文件的引用均不應當被解釋為承認它相對于本發明是現有技術。描述下面的方法用于從混合原料材料的中收氧化鋅。如果其它金屬和金屬氧化物與鋅分離則價值將大大增加,本領域技術人員中也可以將這些技術應用于從其它金屬和金屬氧化物,包括鎳、鈷、錳和銅中,分離氧化鋅。所描述的方法也可用于在鋅的生產過程中取代常規的鋅純化。將含有鋅的原料材料與堿性溶液例如氫氧化鈉溶液混合。如果鋅是金屬的,那么必須也加入合適的氧化劑,例如空氣,以將鋅氧化為zn+2。溶解的金屬的較高負載通常是通過較高濃度的堿實現。根據本發明有用的堿是無機堿,其在水中高度可溶(至少25%重量計)并產生oh的增加,而陽離子不與鋅形成絡合物。可使用的堿的具體實例包括但不限于,堿金屬堿,例如氫氧化鈉,氫氧化鋰和氫氧化鉀。圖1是說明在naoh在水中不同濃度下,氧化鋅在堿性溶液中的溶解度的圖表。氧化鋅與氫氧化鈉溶液的反應可寫作:zno+2naoh+h2o→na2zn(oh)4在摩爾基礎上,兩個鈉陽離子與每個二價鋅酸鹽陰離子相關。因此,較高濃度的鋅可以溶解在較高濃度的堿中。這極大地提高了溶劑萃取方法的效率并得到明顯較高的鋅負載。在圖1中所示的溶解度數據清楚地表明,可以通過使用較高濃度的堿性溶液來獲得氧化鋅負載的增加。通過將堿性溶液的濃度由25%增加至50%獲得大約六倍的增加。根據某些實施例,使用濃縮的氫氧化鈉,其中所述溶液可含有超過30%重量%的naoh,在本發明的某些方面超過40%重量%的naoh,并且在其它實施例中超過50%重量%的naoh。不幸的是,具有50重量%的堿和超過200g溶解的氧化鋅每升堿性溶液的溶液是非常粘稠的-即使是在接近-沸點溫度。從這樣的溶液除去懸浮細粒子是非常困難的。雖然在某些情況下,從含有大于200g/l的鋅的50%的naoh溶液絮凝和沉降固體是可能的。在根據本發明的某些方面中,高濃度的絡合鋅離子可以通過以下特定路徑或步驟順序在相對稀釋的堿性溶液中獲得。然而,并非本發明的所有方面都需要特定的步驟順序。在圖2中提供的流程圖說明了根據本發明的一個實施例的回收氧化鋅的方法。通常情況下,固液平衡與路徑無關。“最終狀態”是很重要的,并且實現這一目標狀態的途徑是無關緊要的。出乎意料地,申請人已經發現特定的路徑使得人們可以產生遠高于預期的鋅負載。所述方法利用了三種現象:1.濃縮的堿性溶液比稀釋的堿性溶液溶解更多的鋅。2.當水被加入到鋅離子的濃縮溶液中,稀釋堿性時,鋅不容易沉淀。3.稀釋的堿性溶液比濃縮的堿性溶液具有明顯更低的粘度并且更容易處理和加工。因此,通過在高堿性濃度用鋅加載堿性溶液,然后用水稀釋所述溶液以降低堿性濃度,可以產生同時具有高的鋅負載和相對低粘度的溶液。相對低的粘度允許容易(facile)的下游加工,包括固-液分離(沉積、離心、過濾等)。在約600g氧化鋅每升堿性溶液中,將50重量%的naoh的堿性溶液用鋅飽和。所述溶液可用水稀釋至35重量%naoh的當量堿性濃度。按照這一路徑產生的最終溶液包含約420g氧化鋅每升堿性溶液。通過比較,最初將氧化鋅溶解在35重量%naoh的堿性溶液中,僅約220g氧化鋅溶解于每升堿性溶液。稀釋至35%naoh降低了溶液的粘度并且改進了固體殘余物從母液中分離,而沒有顯著增加雜質例如鹵化物鹽的溶解度。根據本發明的一個實施例,可以得到的鋅負載比通過簡單地用25重量%堿的苛性堿性溶液開始的可能的鋅負載高大約3倍。可以通過使用具有超過50重量%堿的苛性堿性溶液來實現甚至更大的最終鋅負載量。堿和鋅的最大濃度僅受加工考慮因素例如過高粘度的限制。并沒有將濃縮的溶液稀釋到只有25重量%的堿性濃度的具體要求。取決于下游加工設備的要求,必須僅加入足夠降低粘度至所需水平的水。從實用的角度看,溶液通常稀釋至約15–30重量%的堿性濃度的濃度。在其他情況下,可以將溶液稀釋至約30-35%的堿性濃度的濃度。如果有待將鹵素與鋅分離,這一更高的堿性溶液,例如,可以是特別有用的。當然,該特定范圍之外的濃度也在本發明的范圍之內。如本文所公開的,可將水加至濃縮的鋅酸鈉溶液,提供稀釋并產生粘度的降低而不沉淀任何負載鋅的顆粒。鋅離子以遠遠高于由圖1中提供的溶解度曲線預測的濃度保持在溶液中。這使得懸浮粒子可以更容易地從母液分離,同時保持溶液中的高鋅負載。在某些方面,可以實現進一步的加工而無需稀釋母液。根據其他實施例,可以通過加入多達初始naoh溶液重量的30%的量的水來稀釋母液,以提供低粘度的溶液,其有利于進一步固液分離。母液可以用足夠的水稀釋以將漿料的粘度減少至少10%,并且根據本發明的某些方面至少50%以及在其它方面至少75%。在濕法冶金廠的設計中,高鋅負載是重要的。通常,隨著溶液溫度的升高和攪拌強度的增強,這兩者有利于物質從固體轉變為液體,溶解速率也增加。鋅負載越高,回收給定量的鋅所需的循環堿比率(circulatingbasicrate)越少。循環堿比率的降低對資本和運營成本兩者都具有重大影響。可通過任何數量的可獲得的技術將母液(含有溶解的鋅的堿性溶液)從剩余材料分離,包括沉降、離心分離和過濾。盡管母液已稀釋,但是所得到的金屬負載量仍高于如果溶液之前沒有在所述方法的提取步驟期間被如此高度濃縮時可以獲得的金屬負載。總之,所述溶液是超飽和的。通過生成這樣的超飽和溶液,可以通過將回收每單位金屬所必須加工的母液的量最小化來提高加工效率。為了減少必須被處理材料的量,母液可以在已去除雜質之后被重構至初始濃度或接近初始濃度的堿濃度。如本文所用,術語“重構”意指增加母液的堿濃度至接近初始浸取液的堿濃度的水平。根據某些實施例中,母液被重構以獲得大于約25%的堿濃度。根據特定實施例,堿濃度被重構至大于約30%,大于約35%,更特別地大于約40%以及在某些實施例中約50%至大于50%的堿性。通過重構母液至較高的堿濃度,必須被加工的溶液的量減少,并且沉淀氧化鋅所需的反溶劑的量也減少了。可以根據常規方法例如蒸發來實現重構溶液,以得到更加濃縮的溶液。應當指出的是,可在由已知技術例如沉淀、電解或膠結的反溶劑沉淀之前,將某些溶解的材料例如銅、鉛、氧化鋁、二氧化硅、一些鹵素和鈣從鋅酸鈉溶液中去除。這導致隨后產生極純氧化鋅產物。確切的純化步驟將取決于雜質的組合和組合物的具體性質。使用氧化鈣或其他堿金屬氧化物的沉淀和與金屬鋅的膠結是特別有用的方法,其可與許多常見的材料一起使用。在使組合物經歷膠結和/或沉淀之前過濾浸取液并不總是必須的。可以通過加入可溶性反溶劑從母液中沉淀氧化鋅。反溶劑可溶于母液并有效地促使溶解的鋅從母液中沉淀。可溶性反溶劑降低鋅在堿性溶液中的溶解度,導致所溶解的物質沉淀-通常為金屬氧化物、氫氧化物,或氧化物和氫氧化物的混合物。可溶性反溶劑分子通常具有非極性烴部分和含有雜原子例如氧、氮或硫的極性部分。使反溶劑可溶于母液是極性官能團(polarfunctionality)。在本發明中有用的反溶劑的具體實施例包括但不限于,甲醇、乙醇、丙醇等。甲醇是特別有用的并以相對低的量產生溶解物質的沉淀。可溶性反溶劑降低了母液中溶解物質的溶解度,使它們沉淀。然而,可溶性反溶劑不會永久中和或破壞溶液的堿性組分。更確切地說,它形成了可以很容易分離以再生堿性溶液和反溶劑兩者的新的溶液。沉淀步驟最好在遠低于反溶劑的沸點的溫度下進行,以避免反溶劑的過度蒸發。最適宜的溫度和壓力是反溶劑物理性質的函數。沉淀的金屬的量(為溶液中總金屬的百分比)通常隨反溶劑的量的增加而增加。需要的反溶劑的量根據具體的加工條件和所使用的反溶劑而變化。典型地,約1至5個體積反溶劑每1個體積母液將引起母液中超過約90%的金屬氧化物的沉淀。可溶性反溶劑與母液的實際比例是溶液中鋅濃度,溶液中堿濃度以及所述方法中所期望的回收率的函數。沉淀在加入反溶劑時立即開始并且在幾分鐘內完成。最初形成的氧化鋅粒子的尺寸為<2μm。如果在將氧化鋅從液體中分離前允許混合漿料,那么粒子的尺寸將增加。這提供了生產具有不同粒度和比表面積的氧化鋅產物的方法。粒徑和比表面積在氧化鋅的某些用途中是重要。通常,堿性溶液中鋅的初始濃度越高以及苛性堿的濃度越高,則對于給定用量的反溶劑來說回收的鋅的百分比越大。簡單的蒸餾通常從廢母液(spentpregnantliquor)回收具有低至中等沸點的反溶劑,再生反溶劑和堿性溶液兩者。也可以使用重結晶和其它常規方法來再生堿性溶液和反溶劑。堿性溶液和反溶劑兩者之后都可以在所述方法中循環使用,以處理下一批原料材料。這種再生方案遠遠沒有包括通過與酸反應(形成廢鹽溶液)破壞堿性溶液并且之后購買新鮮堿處理下一批原料材料的那些方案昂貴。結晶和膜分離是可以在這個步驟中使用的再生方法的實施例。如可以由本領域的普通技術人員來確定的,也可以使用其它再生方法。本發明的某些方面通過以下的非限制性實施例更詳細地說明。回收氧化鋅的具體實施例用于演示所述方法的原料是來自黃銅鑄塊制造商的集塵灰(baghousedust)。如下文所詳細描述的,將其加工以回收非常純的氧化鋅。原料,在行業中稱為“黃銅煙”,是在黃銅合金的生產過程中形成的。它含有約65重量%的鋅,伴隨少量的鉛、銅和其他材料。用icp(電感耦合等離子體)分析原料材料來確定各種金屬物質的濃度。原料的分析可在表1中找到。表1zno進料樣品材料結果/單位b0.34%cd0.18%cu0.62%k0.41%na2.14%pb10.75%si0.15%sn0.69%zn65.3%其他mg、al、cr、mn、fe、bi0.01-0.1%ti、ni、as、mo、ag、sb、w0.001-0.01%尋找但未檢測到的元素be、ca、co、ge、in、nb、sr、v、zr步驟1:溶解將兩百克原料材料與含有重量計50%氫氧化鈉的650克堿性溶液混合。將原料和堿性溶液的混合物加熱至100℃約一小時并持續攪拌。原料材料的大部分溶解到堿性溶液中。計算出的鋅負載超過250克鋅每升溶液。一小時后,將溶液冷卻至約50℃,并且另外加入325克水,減少有效堿性強度至33%堿的當量。沒有觀察到沉淀。方法中這一點上的鋅負載是過量的167克每升。需要注意的是33%的堿性溶液中鋅的溶解度為僅約145克每升,如上所述使所述溶液超飽和。步驟2:固液分離通過在室溫下經玻璃纖維過濾器過濾,采用了真空以提高過濾速度,將母液從廢料中分離。大約10克的精細黑色殘余物保留在過濾器上之后使用膠結作用從母液中去除不需要的錫、鎘、鉛和銅。將漿料加熱至80℃持續30分鐘伴隨恒定攪拌,并且之后將約15克細粉狀金屬鋅混合至母液中。鋅粉與溶液中的鉛和銅離子反應。30分鐘后,通過真空過濾將固體從母液中分離。為了確保純度,重復上文的膠結程序。第二次膠結的過程中注意到鋅粉末的微小外觀變化,表明電位序在鋅以下的所有金屬已經與金屬鋅反應并從母液中去除。步驟3:用反溶劑沉淀氧化鋅將母液如之前一樣過濾,冷卻至室溫,并用四倍體積的甲醇在環境溫度和壓力下進行處理。將甲醇加入母液之后立即形成白色沉淀。通過真空過濾從廢堿性溶液和反溶劑的混合物中回收沉淀的固體。將濾液先用甲醇洗滌以除去苛性堿,并且之后用熱水反復洗滌以除去任何殘留的堿性溶液或反溶劑,并且之后在100℃下干燥。回收到約150克干的,亮白色粉末。用icp(電感耦合等離子體)來分析產物沉淀物以確定各種金屬物質的濃度。樣品僅是部分洗滌的。通常,使用樣品的完整洗滌和純化的大規模操作將提供更高純度和更少雜質的樣品。雜質可以被減少到小于10ppm。氧化鋅產物的結果示于表2中。表2zno產物樣品材料結果/單位ca0.23%na0.31%si0.28%zn79.1%其他mg、cr、sn0.01-0.1%b、al、mn、fe、ni、cu、as、sr、sb、pb0.001-0.01%尋找但未檢測到的元素ag、be、bi、cd、co、ge、in、mo、nb、ti、v、w、zr步驟4:堿性溶劑和反溶劑再生之后通過蒸餾再生反溶劑和廢堿的混合物。蒸餾中的一個階段產生了大約90%的甲醇純度。甲醇和水的這一溶液已被證明是一種可接受的反溶劑。如果需要,可通過在多級蒸餾塔中精餾來實現甲醇的進一步純化。蒸餾“底部”或重的液體產物是含有約35重量%氫氧化鈉的堿性溶液。進一步加熱會導致額外的水蒸發,并且氫氧化鈉的濃度可以很容易地提高至50%(或更多)以便用于浸取后續批次的原始材料。增加凈金屬負載使得資本設備和運營成本得到節約。回收相同量金屬需要較少溶液,從而導致更小的罐、泵、過濾器等。另外,需要較少的熱能,因而降低了運營成本。通過不顯著增加母液的粘度,能夠繼續利用浸取方法下游的同一設備而無阻礙轉移物質。這使得在整個濕法冶金廠中的生產率顯著增加。當前第1頁12