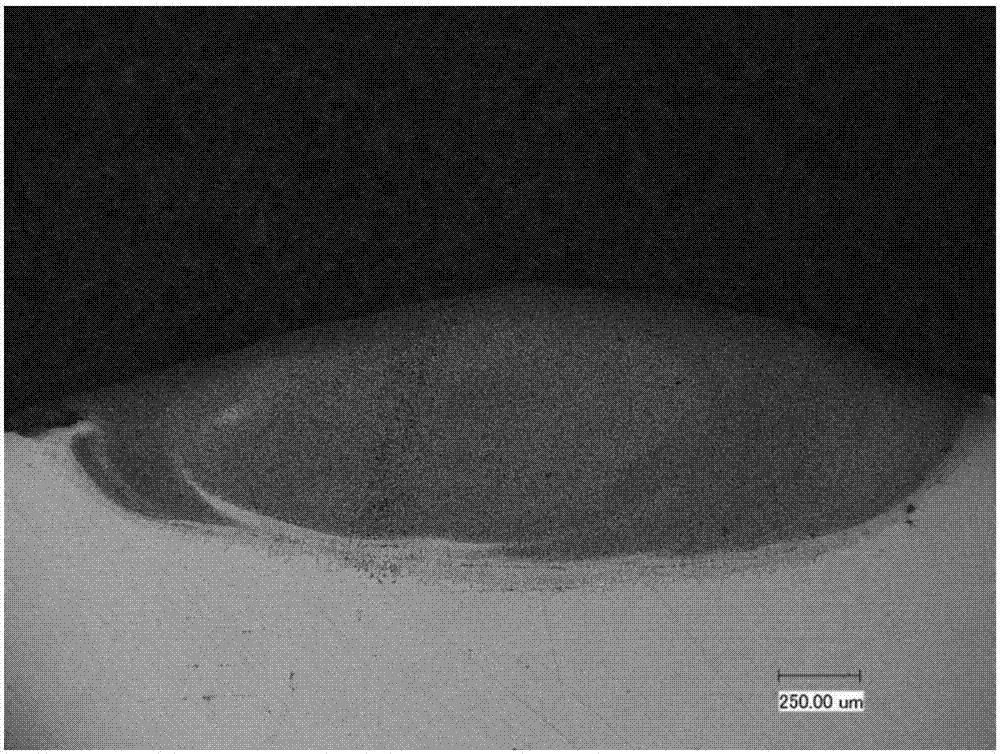
本發(fā)明涉及基體表面的激光應(yīng)用領(lǐng)域,尤其涉及一種用于不銹鋼表面鋁基合金涂層及其制備方法。
背景技術(shù):
:自304不銹鋼可以被大量生產(chǎn)以來,304不銹鋼已經(jīng)大量廣泛使用與汽車配件、醫(yī)療器具和船舶部件等方面。304不銹鋼材具有良好的耐熱耐腐蝕性,良好的機械性能,但是其硬度偏低,耐磨損性能較差,在在某些特殊材料的使用中,不銹鋼材料表面總會出現(xiàn)凹坑、剝落等現(xiàn)象,嚴(yán)重影響材料的使用壽命,甚至?xí)斐删薮蟮慕?jīng)濟(jì)損失。對304不銹鋼表面進(jìn)行改性處理是目前比較理想的處理方法,尤其是激光熔覆技術(shù),可以明顯提高基體表面的硬度及磨損性能。在目前的激光熔覆合金粉末研究中,最主要的合金粉末主要有鎳基合金粉末,鐵基合金粉末以及鈷基合金粉等。而對于鋁基合金粉末的研究主要集中在鋁合金板與鎂合金板,中國知識產(chǎn)局公開了104250812鋁合金表面的激光熔覆工藝,它的化學(xué)組成為60%-70%al,15%-25%ti,6%-8%fe,6%-12%b,上述成分配比為質(zhì)量百分比。熔覆涂層生成了tib強化相,提高了基體的硬度與耐磨性能。其中鋁粉的作用只是為了保證合金粉末與基體的熱膨脹系數(shù)近似,使涂層與基體有良好的冶金結(jié)合性,但是合金粉末中能夠生成金屬間化和物元素含量較少,因此生成的金屬間化和物強化相分布少,對基體的性能改善效果較差,可以考慮在保證熔覆層與基體形成良好冶金結(jié)合的同時生成較多的金屬間化和物強化相,對于改善集體的各種性能有著巨大的效果。目前對于不銹鋼基體采用鋁基合金粉末的研究較少,中國知識產(chǎn)局公開了104141084激光熔覆用高熵合金粉末,采用等摩爾的fe,ni,cr,al,si和mn(0-1的摩爾比)在42crmo鋼上進(jìn)行激光熔覆,獲得較良好的涂層,平均硬度值最高達(dá)到519.5hv,同時耐磨性較基體提高了3倍左右,但是該發(fā)明只是針對不銹鋼基體的硬度與耐磨損性能,對其他如耐腐蝕性能和抗高溫氧化性能等其它沒有明顯改善。技術(shù)實現(xiàn)要素:為了克服現(xiàn)有的技術(shù)不足,本發(fā)明為了提高熔覆層中生成的強化相的分布率,從而提高熔覆層的特征性能。在304不銹鋼板上激光熔覆al-si-ti-ni的合金粉末,在熔覆涂層中形成feal、alti3、feni、tisi2金屬間化合物,且分布均勻,提高基體的硬度與摩擦磨損性能,同時改善基體表面抗高溫氧化性能與抗硫化性能。對于燃?xì)鉁u輪發(fā)動機熱部件表面與其它高溫環(huán)境下的設(shè)備表面和硫化環(huán)境下的設(shè)備表面修復(fù)有著巨大的應(yīng)用價值。為了實現(xiàn)上述目的,本發(fā)明采取的技術(shù)方案為:用于不銹鋼表面鋁基合金涂層的制備方法,包括如下步驟:(1)對不銹鋼基材表面進(jìn)行處理;可以為噴砂預(yù)粗化預(yù)處理后采用酒精清理干凈。可以將不銹鋼用al2o3噴砂處理,然后用酒精或其他清洗劑清除殘留在變面的雜質(zhì)與油污。(2)將鋁基合金粉末混粉:將鋁基合金粉末進(jìn)行混粉得到混合好的合金粉末;所述合金粉末的成分重量百分比為:30-70%al,10-30%si,10-30%ti,10%ni;根據(jù)這四種粉末的比例不同,在熔覆過程中所形成的產(chǎn)物不同,當(dāng)ti/al≥3時,易形成alti3金屬間化合物,當(dāng)al/ti=1時,易形成alti金屬間化合物,當(dāng)al/ti≥3,易形成al3ti金屬間化合物。因此在熔覆涂層中,只要比例合適,可以形成較多的金屬間化合物強化相,明顯提高熔覆層的硬度和耐磨性能。優(yōu)選的所述合金粉末的成分重量百分比為:40%-50%al,20%-30%si,10%-30%ti,10%ni,使用本發(fā)明的合金粉末在不銹鋼合金基體進(jìn)行激光熔覆會與基體中的鐵等元素發(fā)生反應(yīng),可以生成較多的強化相,能明顯改善基體的各項性能。采用10%的ni,含量與不銹鋼基體的ni含量百分比相似,既可以使合金粉末的熱膨脹系數(shù)與基體更相近,提高熔覆層的成型性能,同時提高ni含量可以提高其耐腐蝕性。因為本發(fā)明使用的粉末都為純粉,因此需要將其進(jìn)行混粉,時期成分均勻,在熔覆涂層中獲得均勻的成分分布。(3)預(yù)制涂層:將粘結(jié)劑與步驟(2)中的混合好的合金粉末混合調(diào)和成糊狀或膏狀,預(yù)置在步驟(1)中進(jìn)行過表面處理的不銹鋼表面形成合金涂層,所述合金涂層的厚度為0.8-1.0mm;優(yōu)選的,粘結(jié)劑與合金粉末的配比為3-7ml:9-14g。如果粘結(jié)劑量過低,這樣不利于粉末均勻鋪展在基體表面,如果粘結(jié)劑量過高,配成的混合物流動性強,鋪展在基體表面的粉末均勻性差,因此要控制好比例,既能使混合物能鋪展在基體表面,又能使它的均勻性由保障。(4)合金涂層烘干:將步驟(3)中合金涂層在80℃-100℃烘干形成預(yù)置層;(5)激光熔覆:將步驟(4)所得預(yù)置層在保護(hù)氣氛下進(jìn)行激光熔覆,使所述的預(yù)置層與不銹鋼基材實現(xiàn)冶金結(jié)合,即得到用于不銹鋼表面鋁基合金涂層。其中,述步驟(2)中的合金粉末為250-350目的,各組分純度均大于95%。其中,所述步驟(2)中的混粉方式為真空環(huán)境下間歇式混粉,每混粉30分鐘,暫停10分鐘,再進(jìn)行混粉。可以采用行星式球磨機,采用間歇式混粉,轉(zhuǎn)速250r/min,使用真空球磨罐抽真空,球料比為5:1,混粉時間共計2h。其中,所述步驟(3)中的粘結(jié)劑為二丙酮醇和醋酸纖維素反應(yīng)而成的。其中,所述步驟(5)中保護(hù)氣氛為氮氣、氬氣、氦氣中的一種或幾種,保護(hù)氣氣壓是4mpa。其中,所述步驟(5)中激光熔覆中用的激光器采用光纖激光器。該激光器工作模式為多模,連續(xù)輸出。本發(fā)明的激光熔覆工藝采用中高度的激光功率、較快的激光掃描速度,對基體表面進(jìn)行激光快速熔覆,在基體表面形成的熔池較小并且熱影響區(qū)較少,在基體表面上獲得良好的激光熔覆涂層的同時,減少熱影響區(qū)對基體的影響。其中,所述步驟(5)中的激光光斑直徑為3mm,離焦量35mm。其中,所述步驟(5)中的激光功率分別為1400-1600w,掃描速度分別為550-650mm/min。上述制備方法制備的用于不銹鋼表面鋁基合金涂層。本發(fā)明的有益之處在于:本發(fā)明提供的涂層在提高不銹鋼基體表面硬度與摩擦磨損性能的同時,改善基體表面抗高溫氧化性能與抗硫化性能。本發(fā)明提供的制備方法工藝成本較低,易于生產(chǎn)。附圖說明圖1為實施例1-9中所用帶防氧化裝置的圓形坩堝。其中,1.保護(hù)氣、2.進(jìn)氣口、3.坩堝、4.進(jìn)氣口。圖2為實施例6的合金涂層的宏觀形貌圖。圖3實施例6的合金涂層微觀組織形貌的涂層頂部。圖4實施例6的合金涂層微觀組織形貌的涂層中部。圖5實施例6的合金涂層微觀組織形貌的涂層底部。圖6為實施例6的xrd分析圖。具體實施方式下面結(jié)合實施例,對本發(fā)明作進(jìn)一步說明:以下實施例所用的材料參數(shù)如下:al(99.5%,300目),si(99.5%,300目),ti(99.5%,300目),ni(99.5%,200目)粘結(jié)劑:二丙酮醇和醋酸纖維素反應(yīng)而成的醋酸纖維。(每200ml二丙酮醇混合8.5g乙酸纖維素,水浴加熱溫度到90℃進(jìn)行反應(yīng),直到溶液中的乙酸纖維素反應(yīng)完全為止。)實施例1:(1)將304不銹鋼用al2o3噴砂處理,然后用酒精或其他清洗劑清除殘留在變面的雜質(zhì)與油污。(2)將鋁基合金粉末混粉:將鋁基合金粉末用可變速率行星式高能球磨機混粉,每混粉30分鐘,暫停10分鐘,再進(jìn)行混粉,轉(zhuǎn)速250r/min,使用真空球磨罐抽真空,球料比為5:1,混粉時間共計2h。鋁基合金粉末各成分重量比為al:si:ti:ni=7:1:1:1,(3)預(yù)制涂層:將粘結(jié)劑與合金粉末按配比3-7ml:9-14g混合,然后預(yù)置在步驟(1)中進(jìn)行過表面處理的不銹鋼表面形成合金涂層,所述合金涂層的厚度為0.9mm;(4)合金涂層烘干:將步驟(3)中合金涂層放入80℃的烘箱4小時后取出,形成預(yù)置層。(5)激光熔覆:將有預(yù)置層的不銹鋼放入自制的圓形坩堝中(如圖1),坩堝槽兩邊通入保護(hù)氣(ar),保護(hù)氣氣壓是4mpa,激光熔覆,激光采用連續(xù)式光纖激光器,激光器的輸出功率為1500w掃描線速度為600mm/min,激光器離焦量為35mm,激光器的光斑直徑為3mm。實施例2:本實施例與實施例1基本相同,只有鋁基合金粉末各成分重量比為al:si:ti:ni=6:1:2:1,與實施例1不同,同時其他實驗條件不變。實施例3:本實施例與實施例1基本相同,只有鋁基合金粉末各成分重量比為al:si:ti:ni=5:1:3:1,與實施例1不同,同時其他實驗條件不變。實施例4:本實施例與實施例1基本相同,只有鋁基合金粉末各成分重量比為al:si:ti:ni=6:2:1:1,與實施例1不同,同時其他實驗條件不變。實施例5:本實施例與實施例1基本相同,只有鋁基合金粉末各成分重量比為al:si:ti:ni=5:2:2:1,與實施例1不同,同時其他實驗條件不變。實施例6:本實施例與實施例1基本相同,只有鋁基合金粉末各成分重量比為al:si:ti:ni=4:2:3:1,與實施例1不同,同時其他實驗條件不變。實施例7:本實施例與實施例1基本相同,只有鋁基合金粉末各成分重量比為al:si:ti:ni=5:3:1:1,與實施例1不同,同時其他實驗條件不變。實施例8:本實施例與實施例1基本相同,只有鋁基合金粉末各成分重量比為al:si:ti:ni=4:3:2:1,與實施例1不同,同時其他實驗條件不變。實施例9:本實施例與實施例1基本相同,只有鋁基合金粉末各成分重量比為al:si:ti:ni=3:3:3:1,與實施例1不同,同時其他實驗條件不變。經(jīng)試驗分析發(fā)現(xiàn),實施例5-7的成分比例(40%-50%al,20%-30%si,10%-30%ti,10%ni)得到的熔覆涂層無明顯裂紋,硬度值高,其中實施例6(40%al-20%si-30%ti-10%ni)達(dá)到的效果最好。對比例1鐵基激光熔覆粉末及熔覆層制備方法:(1)將不銹鋼噴砂處理,然后用酒精或其他清洗劑清除殘留在變面的雜質(zhì)與油污。(2)將鐵基合金粉末混粉:將鐵基合金粉末用研缽中機械研磨機混粉,優(yōu)選組分含量為c為0.5-0.8%,cr為21-22%,ni為10-11%,al為10-10.5%,mo為5-5.5%,ceo2為1-1.2%,其余為fe。(3)在上述鐵基激光熔覆粉末中,選用各個組分均為純度大于等于99%的粉末,粒徑為100-500目,優(yōu)選200-300目,即鐵粉、鉻粉、鎳粉、鋁粉、鉬粉、石墨粉、二氧化鈰。(4)預(yù)制涂層:將粘結(jié)劑與合金粉末按質(zhì)量百分比92-95%合金粉末與5-8%乙醇混合,然后預(yù)置在步驟(1)中進(jìn)行過表面處理的不銹鋼表面形成合金涂層,所述合金涂層的厚度為1-2mm;(5)激光熔覆:激光功率為1520-1650w,掃描線速度為150-220mm/min,激光器離焦量為0,激光器的光斑直徑為0.8-1mm。對比例2激光熔覆用高熵合金粉末及熔覆層制備方法和用途:(1)將不銹鋼噴砂處理,然后用酒精或其他清洗劑清除殘留在變面的雜質(zhì)與油污。(2)將高熵合金粉末粉末混粉:將高熵合金粉末用研缽中機械研磨機混粉,組分含量為激光熔覆用高熵合金粉末,由fe、ni、cr、al、si和mn元素粉末組成,即合金粉末組成表示為fenicralsimnx,x為mn的摩爾比且其取值范圍為0-1,具體來說,所述fe、ni、cr、al、si之間為等摩爾比,調(diào)整金屬mn的用量,以使其使用摩爾量與si(或者其余四種元素)的摩爾比為0-1,優(yōu)選0.3-1,更加優(yōu)選0.5-0.7。(3)在上述鐵基激光熔覆粉末中,選用各個組分均為純度大于等于99%的粉末,粒徑為100-500目,優(yōu)選200-300目。(4)預(yù)制涂層:將粘結(jié)劑與合金粉末按質(zhì)量百分比92-95%合金粉末與5-8%乙醇混合,然后預(yù)置在步驟(1)中進(jìn)行過表面處理的不銹鋼表面形成合金涂層,所述合金涂層的厚度為1-2mm;(5)激光熔覆:激光功率為1520-1650w,掃描線速度為150-220mm/min,激光器離焦量為0,激光器的光斑直徑為0.8-1mm。下面是對實施例1-9激光熔覆al-si-ti-ni涂層及對比例1、2進(jìn)行組織結(jié)構(gòu)分析與性能測試。1、組織與結(jié)構(gòu)分析表1宏觀形貌分析由圖2所示實施例6的熔覆涂層與基體形成冶金結(jié)合。由圖3-5為實施例6的合金涂層微觀組織形貌的涂層頂部、涂層中部、涂層底部。涂層組織結(jié)構(gòu)較為均勻,無明顯氣孔和裂紋。由圖6所示實施例6的xrd分析圖,分析發(fā)現(xiàn)涂層主要存在feal、alti3、feni、tisi2相,能有效提高集體的硬度與摩擦磨損性能,同時改善基體的抗高溫氧化性能與抗硫化性能。2.顯微硬度測試實施例1-9及對比例1、2的硬度分析如表2:表2實施例1-9硬度值比較由上表可以看出實施例中實施例6的最高硬度值與平均硬度值達(dá)到最高。3.高溫抗氧化性能測試為了使抗高溫氧化性能測試不受基底材料的影響,氧化試驗涂層厚度約為0.6-0.8mm,用線切割方法將涂層與基底分離,氧化試驗前涂層試樣經(jīng)超聲波丙酮溶液清洗、烘干后用精度0.01mg電光分析天平稱重,將試件裝入灼燒恒重的氧化鋁坩堝中,在800℃條件下利用靜態(tài)增重法進(jìn)行氧化試驗,時間為80h。每10h稱重一次,得出其單位面積氧化增重量,對比試樣為無涂層的不銹鋼。實施例1-9及對比例1、2的高溫抗氧化性能測試分析如表3:表3800℃基體與熔覆涂層隨時間變化氧化增重量(mg/cm2)10h20h30h50h80h基體15.1219.2825.3337.5245.19實施例19.2112.2615.3718.6921.33實施例27.6410.1513.5815.3817.58實施例37.1510.0313.4415.0717.44實施例46.289.9912.3514.6516.35實施例55.368.5611.9813.8615.98實施例65.088.0110.2512.93.15.25實施例75.888.6810.6613.3515.66實施例86.359.6211.0913.7916.09實施例97.5510.0312.6214.0116.62對比例111.3613.8817.6919.7322.65對比例27.3810.1613.6316.0117.314.抗硫化性能測試為了使抗高溫氧化性能測試不受基底材料的影響,氧化試驗涂層厚度約為0.6-0.8mm,用線切割方法將涂層與基底分離,氧化試驗前涂層試樣經(jīng)超聲波丙酮溶液清洗、烘干后用精度0.01mg電光分析天平稱重。將樣品放入600℃,0.01mpas(g)+n2的馬弗爐中,同時開啟硫加熱套,對硫坩塥加熱,開始反應(yīng)計時。硫化結(jié)束時,取出樣品測定樣品的硫化增重量。實施例1-9及對比例1、2的抗硫化性能測試分析如表4:表4600℃0.01mpas(g)+n2基體與熔覆涂層隨時間變化增重量(mg/cm2)10h20h40h50h基體8.5310.1212.6814.79實施例15.386.217.428.13實施例25.426.167.538.19實施例35.315.947.167.88實施例45.325.867.087.59實施例55.015.366.416.94實施例64.585.015.736.21實施例75.125.796.136.81實施例85.395.756.357.19實施例95.866.356.997.54對比例18.038.759.9910.54對比例27.317.869.2310.06以上所述的實施例對本發(fā)明的技術(shù)方案和有益效果進(jìn)行了詳細(xì)說明,應(yīng)理解的是以上所述僅為本發(fā)明的具體實施例,并不用于限制本發(fā)明,凡在本發(fā)明的原則范圍內(nèi)所做的任何修改和改進(jìn)等,均應(yīng)包含在本發(fā)明的保護(hù)范圍之內(nèi)。當(dāng)前第1頁12