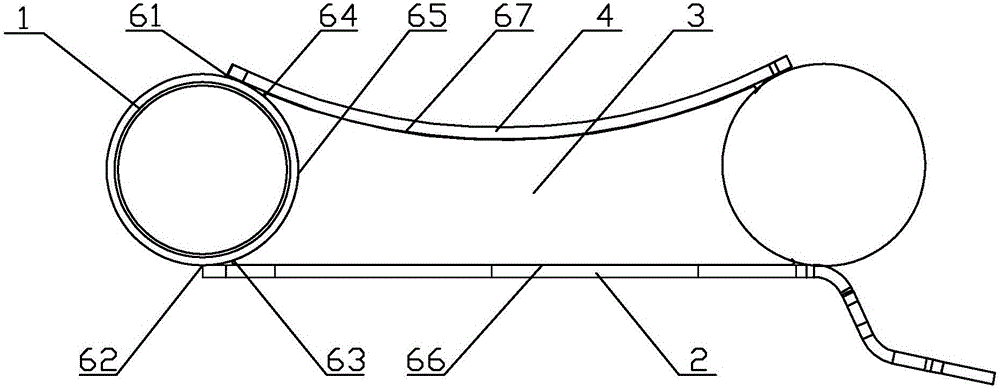
本發(fā)明涉及一種車(chē)軸附件結(jié)構(gòu)及其焊接方法,具體涉及半掛車(chē)車(chē)軸縱臂及其焊接方法。
背景技術(shù):
:所述車(chē)軸縱臂為半掛車(chē)車(chē)軸的附件,產(chǎn)品主要結(jié)構(gòu)由主軸、縱臂組件、減震座、錨式板座、制動(dòng)底板、固定座、凸輪軸支架、氣室座組件等組成。其中,主軸經(jīng)過(guò)成型、熱處理、粗車(chē)、淬火、精車(chē)、精磨等多道工序加工后才能制成,并與上述零部件組裝焊接而成。半掛車(chē)帶縱臂梁車(chē)軸由主軸中心劃分形成左右對(duì)稱式的分布,而經(jīng)過(guò)精加工后的主軸,特別是縱臂再焊接,主要問(wèn)題就是焊后易產(chǎn)生焊接變形,如果不能有效地控制焊接變形,產(chǎn)品將無(wú)法滿足圖紙技術(shù)的要求,產(chǎn)品甚至?xí)a(chǎn)生報(bào)廢的可能。因此,合理有效地控制焊接變形是此產(chǎn)品是否滿足圖紙技術(shù)的要求的一種重要工作與措施。目前,通用的焊接順序編排技術(shù)與方法,只適用于廣義的范疇。而不同的焊接結(jié)構(gòu)形式都有著其特殊的焊縫布局,車(chē)軸縱臂焊接結(jié)構(gòu)構(gòu)造是由襯套管、帶曲面的下翼梁、中心網(wǎng)塊和上翼梁組成,襯套管與下翼梁、中心網(wǎng)塊及上翼梁構(gòu)件結(jié)合處,焊縫交叉重疊形成焊接應(yīng)力集中區(qū)域,而下翼梁、中心網(wǎng)塊和上翼梁按其設(shè)計(jì)結(jié)構(gòu)形式自然形成一種帶曲面的“工字梁”結(jié)構(gòu)。使此類結(jié)構(gòu)極易造成由于焊接順序不當(dāng)、焊接輸入不當(dāng)和焊接時(shí)焊接方向錯(cuò)誤等原因,造成焊接結(jié)構(gòu)整體扭曲變形,結(jié)果無(wú)法保證結(jié)構(gòu)尺寸符合圖紙技術(shù)要求。此外,申請(qǐng)?zhí)枮椋篊N201110460702.4的對(duì)比文件公開(kāi)了“一種車(chē)架縱梁的焊接方法”,此方法是針對(duì)車(chē)架縱梁,屬于轎車(chē)的結(jié)構(gòu),是鋁合金材料結(jié)構(gòu),與本申請(qǐng)具有實(shí)質(zhì)性的差異。技術(shù)實(shí)現(xiàn)要素:為了克服現(xiàn)有技術(shù)的上述不足,本發(fā)明的目的在于提供一種車(chē)軸縱臂焊接順序編排方法,該方法能夠充分避免焊接應(yīng)力集中以及熱應(yīng)力引起的變形,保證焊接的形變量最小。本發(fā)明實(shí)現(xiàn)上述目的的技術(shù)方案為:一種車(chē)軸縱臂結(jié)構(gòu),所述車(chē)軸縱臂結(jié)構(gòu)包括襯套管,一端焊接在所述襯套管上的上翼梁和下翼梁,以及焊接在所述上翼梁和所述下翼梁中間的中心網(wǎng)塊;所述中心網(wǎng)塊一端面焊接在所述襯套管上。所述下翼梁為曲面結(jié)構(gòu),所述上翼梁為直面結(jié)構(gòu);所述上翼梁、所述下翼梁以及所述中心網(wǎng)塊構(gòu)成曲面工字結(jié)構(gòu)。所述中心網(wǎng)塊與主軸拼接并焊接成型。一種車(chē)軸縱臂結(jié)構(gòu)焊接方法,其焊接步驟為:步驟一,在所述襯套管和所述下翼梁搭接處外側(cè)焊接第一焊縫;步驟二,在所述襯套管和所述上翼梁搭接處外側(cè)焊接第二焊縫;步驟三,在所述襯套管和所述上翼梁形成的夾角處焊接第三焊縫;步驟四,在所述襯套管和所述下翼梁形成的夾角處焊接第四焊縫;步驟五,在所述襯套管和所述中心網(wǎng)塊的拼接處焊接第五焊縫;步驟六,在所述中心網(wǎng)塊與所述上翼梁的拼接處焊接第六焊縫;步驟七,在所述中心網(wǎng)塊與所述下翼梁的拼接處焊接第七焊縫。所述第六焊縫和/或所述第七焊縫采用分段退焊法焊接完成。所述分段退焊為分兩段或兩段以上退焊。所述任一步驟完成之后,待溫度冷卻至80℃再進(jìn)行下一步驟。所述步驟三采用分段跳焊法及交叉對(duì)稱的焊接順序,所述步驟四采用分段跳焊法及交叉對(duì)稱的焊接順序。焊接電流為160A~400A,焊接電壓為18V~40V,氣體流量為15L/min~25L/min。優(yōu)選地,焊接電流為170A~200A,焊接電壓為18V~25V,氣體流量為20L/min~25L/min。本發(fā)明與現(xiàn)有技術(shù)相比具有以下的有益效果:本發(fā)明的車(chē)軸縱臂有曲面和直面的結(jié)構(gòu),經(jīng)過(guò)高精度的焊接,能承受較大的載荷和較高的應(yīng)力。焊接順序的合理編排與應(yīng)用,可以有效地糾正車(chē)軸縱臂結(jié)構(gòu)焊接變形。焊接的時(shí)候由于受應(yīng)力作用焊件會(huì)變形,改變焊接順序和方向,可以使應(yīng)力相互抵消。該方法使焊縫能較自由地收縮,以最大限度地減少焊接應(yīng)力,使內(nèi)應(yīng)力合理分布。選擇合適的焊接參數(shù):如焊接電流,電弧電壓,焊接速度及氣體流量等,都可以極大程度地達(dá)到消除或減少焊接變形的目的。附圖說(shuō)明圖1是本發(fā)明的結(jié)構(gòu)側(cè)視示意圖;圖2是本發(fā)明的結(jié)構(gòu)仰視示意圖;圖3是左縱臂的立體結(jié)構(gòu)示意圖;圖4是右縱臂的立體結(jié)構(gòu)示意圖;圖5是本發(fā)明的產(chǎn)品結(jié)構(gòu)示意圖;圖6是本發(fā)明的局部立體結(jié)構(gòu)示意圖。具體實(shí)施方式下面結(jié)合附圖和具體實(shí)施例對(duì)本發(fā)明作進(jìn)一步的詳細(xì)說(shuō)明。實(shí)施例1,參照?qǐng)D3至圖5,一種車(chē)軸縱臂結(jié)構(gòu),所述車(chē)軸縱臂為半掛車(chē)車(chē)軸的附件結(jié)構(gòu),該結(jié)構(gòu)要求加工精度高、形變量小、尺寸精度高等特點(diǎn),需要特別的焊接方法和順序,才能保證符合設(shè)計(jì)要求。所述車(chē)軸縱臂結(jié)構(gòu)包括襯套管1,一端焊接在所述襯套管1上的上翼梁2和下翼梁4,以及焊接在所述上翼梁2和所述下翼梁4中間的中心網(wǎng)塊3;所述中心網(wǎng)塊3一端面焊接在所述襯套管1上;所述中心網(wǎng)塊3與主軸5拼接并焊接成型。所述下翼梁4為曲面結(jié)構(gòu),所述上翼梁2為直面結(jié)構(gòu);所述上翼梁2、所述下翼梁4以及所述中心網(wǎng)塊3構(gòu)成曲面工字結(jié)構(gòu)。本車(chē)軸縱臂為鋼材結(jié)構(gòu),且能承受較大載荷。參照?qǐng)D1,一種車(chē)軸縱臂結(jié)構(gòu)的焊接步驟為:步驟一,在所述襯套管1和所述下翼梁4搭接處外側(cè)焊接第一焊縫61;步驟二,在所述襯套管1和所述上翼梁2搭接處外側(cè)焊接第二焊縫62;步驟三,在所述襯套管1和所述上翼梁2形成的夾角處焊接第三焊縫63;步驟四,在所述襯套管1和所述下翼梁4形成的夾角處焊接第四焊縫64;步驟五,在所述襯套管1和所述中心網(wǎng)塊3的拼接處焊接第五焊縫65;步驟六,在所述中心網(wǎng)塊3與所述上翼梁2的拼接處焊接第六焊縫66;步驟七,在所述中心網(wǎng)塊3與所述下翼梁4的拼接處焊接第七焊縫67。以上步驟中的第一焊縫61、第二焊縫62、第三焊縫63、第四焊縫64均為橫向焊縫,即焊縫方向與襯套管的軸心線平行;第五焊縫65、第六焊縫66、第七焊縫67均為縱向焊縫,即焊縫方向與襯套管的軸心線垂直。參照?qǐng)D1,按以上所述的焊接順序進(jìn)行焊接可有效地減少焊接變形。焊接完步驟一后,迅速將工件翻轉(zhuǎn)焊接步驟二。步驟三和步驟四的焊接,焊接參數(shù)要選下限值,由于有中心網(wǎng)塊的間隔,步驟三和步驟四均要采用對(duì)稱焊接的方法,焊接方向均采用由外至里,且步驟三焊接完成后,在焊接步驟四時(shí),要注意時(shí)間間隔的控制,適當(dāng)?shù)难娱L(zhǎng)冷卻時(shí)間,避免集中受熱而產(chǎn)生大的變形。步驟五的焊接,要求嚴(yán)格按照對(duì)稱的方式焊接,同時(shí)也要選擇焊接參數(shù)的下限值,避免工件過(guò)度受熱,而造成大的變形。所述任一步驟完成之后,待溫度冷卻至80℃再進(jìn)行下一步驟。每完成一個(gè)所述任一步驟,然后焊接另一側(cè)的對(duì)應(yīng)位置,再進(jìn)行下一步驟。所述步驟三采用分段跳焊法及交叉對(duì)稱的焊接順序,所述步驟四采用分段跳焊法及交叉對(duì)稱的焊接順序。焊接電流為160A~400A,焊接電壓為18V~40V,氣體流量為15L/min~25L/min。優(yōu)選地,焊接電流為170A~200A,焊接電壓為18V~25V,氣體流量為20L/min~25L/min,這樣能使得焊接變形量符合較小的值的要求。例如,可以采用焊接電流為185A,焊接電壓為20V,氣體流量為20L/min;參照?qǐng)D1至圖6,下翼梁4、中心網(wǎng)塊3和上翼梁2由結(jié)構(gòu)形成一個(gè)“工字梁”形焊接結(jié)構(gòu),下翼梁4為一曲面形的結(jié)構(gòu),而上翼梁2為一直面形結(jié)構(gòu),從熱漲冷縮原理上分析,直面局部受熱要比曲面局部受的拉應(yīng)力要大,因此,先焊接步驟六再焊接步驟七。步驟六和步驟七的焊接均要嚴(yán)格按照“工字梁”所排的焊接順序號(hào)進(jìn)行對(duì)稱焊接,否則將產(chǎn)生較大的扭曲變形,使結(jié)構(gòu)不能滿足設(shè)計(jì)技術(shù)要求。經(jīng)過(guò)按焊接排序工藝進(jìn)行焊接,半掛車(chē)軸縱臂的尺寸要求達(dá)到設(shè)計(jì)規(guī)定范圍值,見(jiàn)表1。序號(hào)實(shí)測(cè)值11.1021.0030.8540.8050.76表1焊后襯套管與主軸平行度檢測(cè)值實(shí)施例2,參照?qǐng)D2,所述第六焊縫66和/或第七焊縫67采用分段退焊法,分兩段或兩段以上退焊。步驟六和步驟七均采用從圖2的右向左分段焊接,例如分為兩段焊接第六焊縫66,先從右向左的焊接左半段,再?gòu)挠蚁蜃蟮暮附拥谄吆缚p67的左半段;然后從右向左焊接第六焊縫66的右半段,最后從右向左的焊接第七焊縫67的右半段。當(dāng)采用分兩段以上的分段焊接時(shí),也是采用相同的焊接順序和方法依次焊接。在焊接上采用逐步退焊法,以保證獲取小的焊接變形量。其余步驟和方法與實(shí)施例1相同。本發(fā)明的實(shí)施方式不限于此,按照本發(fā)明的上述內(nèi)容,利用本領(lǐng)域的普通技術(shù)知識(shí)和慣用手段,在不脫離本發(fā)明上述基本技術(shù)思想前提下,本發(fā)明還可以做出其它多種形式的修改、替換或變更,均落在本發(fā)明權(quán)利保護(hù)范圍之內(nèi)。當(dāng)前第1頁(yè)1 2 3